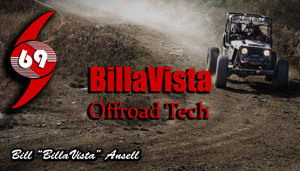 |
Axleshaft Tech
By Bill "BillaVista" Ansell
Photography: Bill Ansell
Copyright 2004 - Bill Ansell
(click any pic to enlarge)
|
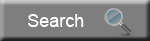 |
Introduction
Deceptively simple in appearance,
modern axle shaft technology is actually quite technical and complicated. I
certainly do not poses all the answers; neither, on the other hand, does any
other single person as far as I can tell. In this part of the BillaVista-60
article I will share with you everything I have learned about alloy axles, shaft
technology, and splines. Hopefully this will help to explain and illuminate
why I decided to build my axle using Superior Alloy Axle shafts, and allow you
to make your own product evaluations and purchasing decisions from an educated,
or at least informed, point of view. |
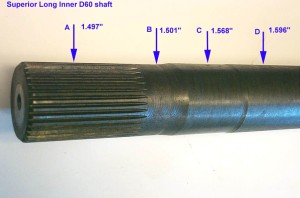 |
That said - there are no inarguable
absolute truths in the world of axle shaft technology. Major manufacturers
and many talented professional engineers often have serious disagreements on
the topic. One of the reasons for this, especially in our case (dealing with
4x4 front axles) is that, as a sport, rock crawling is still really in its infancy
- meaning there hasn't yet been time for the generations of investment in product
R&D that there has in more established motorsports - none of which use front
4x4 axle shafts! Also, as the rock crawling market is young and growing rapidly,
competition is fierce leaving companies and engineers even more tight lipped
than their drag racing colleagues.
My purpose is to try and establish
just what makes a great axle shaft, and what qualifies a product as "the
best". In order to do so, we must have some background knowledge
of axle shafts and their design. But where are we to gain this knowledge?
One could of course ask the manufacturers themselves, but we can be reasonably
certain they would assure us that theirs are the best! So, in addition
to asking the manufacturers it seems to me there are 3 main sources of information
to which we can turn:
- Established motorsports (mostly
rear axle technology)
- OEM's
- Basic engineering principles
Regarding the first source, consider
that the technology involved in front axle shaft design is different than for
rear axles; not nearly as much is known or proven in front axle technology as
in rear, and those that do know, aren't saying much. Keep in mind that when
discussing (or arguing :-) front axle technology, it is not possible to simply
refer to what is done with drag racing or other rear axles, as the technology
can be quite different - though there are similarities and basic principles
we can learn from.
Regarding the second source, the
OEMs (even if it is only the source from which we extrapolate) are also of limited
use to us in navigating the waters of front axle tech because of one simple
law, and that law is: "All design is a compromise" This fact, coupled
with the requirement for OEM's to generate profit for shareholders as their
single goal of overwhelming primacy means they design not the "best"
or "strongest' products they can, but those that are "adequate for
the job, in the shortest time possible, at the cheapest cost" Those
are the practical limitations of real-life engineering - they don't have the
luxury of designing "ultimate" products. To be sure, they know
a great deal about axles, and we can learn from them - but we must temper what
we learn with the knowledge that their goals are very different from ours.
Which leaves us with the final source
- basic engineering principles. Of course, because I am not a professional
engineer - I am limited in my ability to apply engineering principles - though
I think I can do it well enough to at least be an informed consumer. I
will share with you what I know of these principles and how I used them to determine
who had the best shafts for the BillaVista-60 - but keep in mind that I am not
a pro - just an average Joe.
In the end, the data I have gathered
over the last 3-4 years comes from many and varied sources - from:
- product information sheets and
catalogues of major axle manufacturers the likes of Strange Engineering, Mark
Williams, and Foot Axle and Forge (Superior Axle);
- from personal discussions with
engineers at Superior Axle, Moser Engineering, SAW, and more than one professional
race team;
- from industrial and scientific
texts ranging from "The Machinery's Handbook" to Carroll Smith's
excellent series of books; and
- from the industry experts and
professional engineers kind enough to share their knowledge online.
After all that, the only thing I
know for sure is that I don't know everything - not by a long, shot. But I have
learned quite a lot, certainly enough to be a well informed consumer.
In my front axle I want the strongest
axle shaft available. By strongest I mean able to handle the largest torsional
load - which is the technical way of saying I want my axle shafts to be able
to handle big tires, reasonable horsepower, and hard use in the rocks - steep
climbs, axle bouncing, alternately slipping and grabbing, tires wedges amongst
rocks - the works, serious abuse!
For all things load bearing, strength
comes in 3 kinds:
Strength of Material (including treatment
and process);
Strength of Size (bigger is stronger
- no surprise there); and
Strength of Shape (profile of the
shaft)
More specifically for axle shafts,
there are three components that go together to make a great front axle shaft.
They are:
- The material used to make the
shaft, and how it is heat treated / hardened (strength of material)
- Size and profile of the shaft
(strength of size and strength of shape)
- The splines - their size,
number, shape, and how they are formed. (strength of shape)
We will look at all 3 in turn.
Material and Treatment
Recall some basic facts from my Steel & Materials Strength Article:
- Steel is an awesome material for
load bearing structures, like axle shafts, because it is strong, stiff, and
elastic in nature.
- There are many types of steel
with wildly varying mechanical properties, from yield strength to percent
elongation.
- There are numerous ways to heat
treat steel to improve its mechanical properties, depending on our intended
use.
- Type of steel / alloy and heat
treatment must be carefully matched.
- Generally, the harder a steel
is, the stronger it is but also the less ductile.
All of these factors are important
in the manufacture, or in our case selection, of an axle shaft. Depending on
the desired properties of the shaft, different material and methods will be
used to make them.
Plain carbon steel shafts, like those
used by the OEMs and many aftermarket suppliers cannot be through hardened.
Examples of non-through hardenable steels used to make axle shafts include SAE
1055, 1541, etc. Similarly, true alloy steels used to make axle shafts (e.g.
4340, 300m, etc.) must be through hardened to reap the benefits of the alloy's
strength. As a result, all 4x4 front axle shafts fall into one of 2 broad
categories in terms of their material and treatment. They are either:
- Carbon steel / induction hardened;
or
- Alloy Steel / through hardened.
Heat
Treatment
So what are the different hardening
methods?
Induction hardening is done by placing the metal part inside or close to an "applicator"
coil of one or more turns, through which alternating current is passed. The
coil, formed to suit the general class of work to be heated, is usually made
of copper tubing through which water is passed to prevent overheating of the
coil itself. In most cases, the work piece is held either in a fixed position
or is rotated slowly within or close to the applicator coil. Where the length
of work is too great to permit heating in a fixed position, progressive heating
may be employed. Thus, a rod or tube of steel (e.g. an axle shaft) may be fed
through an applicator coil of one or more turns so that the heating zone travels
progressively along the entire length of the work piece.[1] In the case
of axle shafts, the shaft is passed through the coil, and the coil has to be
of a small enough diameter so that it is close enough to the shaft to do the
heating. Unfortunately the small diameter of the coil prevents the passage of
the yoke (or flange in a rear axle), which means induction hardened front axle
shafts do not have hardened yokes. This is, of course, a MAJOR weak point,
as it is very often the thin, soft yokes that are the weakest part of a front
shaft and therefore the first part to fail.
Induction hardening will be done
to a certain hardness level, and do a certain depth from the surface, called
the "case depth". Typically induction hardening penetrates to about
0.150-inch and the axle core remains relatively soft. Typically, the shaft surface
hardness is a very hard 55-58 Rockwell (almost brittle). There are some benefits
to induction hardening, even over through hardening. The exact physical
and chemical metallurgy is beyond the scope of this article, but basically the
induction hardening process leaves the shaft so hard at the surface, that there
is a residual compressive stress at the surface (using our Lego block analogy
from Part 1a, imagine the surface Lego blocks being pressed down on, making
them harder to bend apart). This residual compressive stress actually
improves fatigue resistance and prolongs fatigue life. Why? Because
most fatigue cracks initiate at imperfections at the surface of the shaft (scuffs,
nicks, burrs, rust, corrosion, grinding marks, etc) and grow from there. The
residual compressive stress makes crack tip advance under cyclic loading more
difficult.
Note also that other surface treatments
help to prevent crack propagation, from finish grinding and polishing to paint
or other coating application.
Through hardening,
though in reality very technical, is much easier to describe. Essentially
the entire part is placed in a large (but very special) oven-like machine and
then heated up, and held at a certain temperature. The part is then the
cooled at very specific and carefully controlled rate. The result is,
the entire part is hardened, including the yokes, AND the part is hardened THROUGH
it's entire thickness, hence the name - through hardening. Through hardening
produces a part with a much more even and uniform crystal lattice structure
(grain), and therefore with much improved mechanical properties - notably yield
and ultimate strengths. Take for example, 4340 Chrom-moly steel, In its
normalized state (having a hardness of Rockwell C 22) is has an approximate
Ultimate Tensile Strength (UTS) of 112, 000 psi. However, through hardened
to a hardness of Rockwell C 42 it has a UTS of approximately 181,000 psi! |
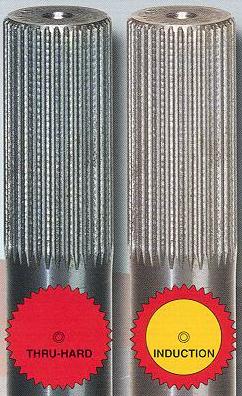 |
Picture graphically
illustrating difference between through hardening and induction hardening.
Pic from Strange Engineering
ad. |
Clearly, through hardening an axle
shaft makes it vastly stronger and therefore through hardening is a must for
any shaft to be considered for the title of "ultimate."
Of course, the ideal treatment would
be a combination of through hardening and induction hardening, to take advantage
of the best of both worlds. There is one manufacturer who does this, and
ONLY one in the 4x4 axle shaft aftermarket that does. The answer should
come as no surprise - Superior Axle and Gear!
Material
But what about the difference in
just the material itself? Compare 2 typical steels used to build axle
shafts, one representative of each group:
- SAE 1030 - low carbon steel, suitable
for induction hardening only - typical of Spicer / OEM type axles
- SAE 4340 - Chrom-moly alloy steel
suitable for through hardening - used by manufacturers such as Superior and
Mark Williams
UTS in psi
67,000 |
108,000 |
75,000 |
185,000 |
106,000 |
213,000 |
Notes:
- Annealed = the softened form,
softest condition.
- Normalized = the normal, plain,
neutral form. Normalization "erases" prior heat treatment.
- Quenched and Tempered = heat treated
/ hardened.
Regardless of the steel's condition
we can clearly see that the cr-mo steel has much greater tensile strength.
Recall from part 1 this is due to the addition of the alloying elements themselves
- the chromium and molybdenum.
Therefore, manufacturing axle shafts
from an alloy steel, though much more difficult, time consuming, and expensive,
gives us the double-advantage of greater strength because of the material itself
AND grater strength because of the through hardening possible.
So what does all this mean to the
shaft? It's NOT what most people think!
The little known FACT is, the material
and how it is heat treated have NOTHING to do with how much the axle will twist
under a given load. How much an axle will twist is determined by the torsional
modulus of elasticity of the axle, which as you will recall from part
1 is a constant for all steels. This means that all axles, of the same
size and profile (shape), under the same load will twist exactly the same amount.
If you were to take identical Spicer OEM (SAE 1055), Moser (1541M), Dutchman
(1541H), and Superior (4340) axles and chuck them in a torsional testing machine
and apply the same load, you would see them all twist exactly the same amount.
The difference is: depending on what steel or alloy they are made from, they
will behave differently when that load is released. Recall the stress/strain
diagrams and properties from Part 1a - The different steels and alloys have different
mechanical properties and therefore stress/strain curves. the "better"
alloy steels will have a much greater 'elastic range" and much greater
yield strengths, meaning they will spring back unharmed to original size and
shape where the lesser steels may not.
Lets' say, for the sake of argument
that we we put 120,000 psi load on the axle shaft (say, by wedging a tire and
tromping the gas) - Regardless of the axle material they will all twist the
same amount, however, the one made from 1030 carbon steel will have had its
Ultimate Strength exceeded, and so will break. The one made from 1541
may only have had its yield strength exceeded and so will not rupture but will
not return exactly to it's original shape - it will have twisted or taken a permanent
set. The alloy axle made from 4340 will have had neither its ultimate
strength nor its yield strength exceeded, and so will return to exact original
size and shape - in effect shrugging off the load an carrying on unharmed.
In short, the "better"
axles made from alloy steel and through hardened are "stronger" not
because they resist twisting more or twist less under load, but because they
are made from a material and process that allows them to handle the twisting
better, to survive it unscathed. That's what being built for the task
is all about, and THAT is what makes the best 4x4 shaft!
For those mathematically inclined,
the equation for how much a solid steel shaft will twist under load is:
alpha=[584(T)(l) ] / D^4 * G
Where:
alpha = the torsional deflection
in degrees (how much it twists)
T = Torsional or twisting moment in inch pounds (torque or load placed on the
axle)
l = length of the shaft in inches
D = diameter of shaft in inches
G= torsional modulus of elasticity (a constant for all steel shafts at 11,500,000
psi )
Note that in the equation, the diameter
of the shaft (D) is raised to the power of 4. This shows mathematically
why a larger shaft is "stronger" than a smaller one, because it twists
less (resists the load better or has a steeper stress/strain curve).
Note that this "stronger"
- strength of size - is quite different from the "stronger" attributable
to material and treatment.
Summary
Strength of size - larger shaft is
stronger because it resists the load better (twists less under load)
Strength of material - Shafts made
of better material and process (alloy shafts, through hardened) are stronger
because they can take much larger loads before yield and rupture. They
"shrug off" applied loads much better.
Both play a part in determining how
much load a shaft can take, and therefore when it will fail, and therefore how
suitable it is for our intended use. However, you begin to see how difficult
it is to just label something as "stronger". Ideally, for the
shaft to be ultimate we want it to be as large as possible, constructed of as
a high a grade of alloy steel as possible, through hardened, and if possible,
induction hardened for fatigue life as well.
(No prizes for guessing at this stage
the one and only one manufacturer of front axle shafts that fits this description!)
Here is a table of current axle manufacturers
listing information that is accurate, to the best of my knowledge, at the time
of this writing (Mar 2004):
Manufacturer |
Alloy |
Heat Treatment |
Notes |
Currie |
1541H |
Induction Hardened |
Pre-machined axle blanks then
splines cut after induction hardening |
Dutchman |
1541H |
Induction Hardened |
Pre-machined axle blanks then
splines cut after induction hardening |
Dynatrac |
1541H |
Induction Hardened |
Pre-machined axle blanks then
splines cut after induction hardening |
Mark Williams |
chromium-molybdenum-nickel alloy |
Through hardened (austempered) |
Rear axles only. |
Moser |
1541H |
Induction Hardened |
Pre-machined axle blanks then
splines cut after induction hardening |
Spicer |
1040, 1137, 1030, 1039 etc. |
Induction Hardened |
|
Strange |
Hy-Tuf alloy
(high silicone nickel-cr-mo) |
Through hardened RC 46-48 |
Not as good as 4340 but much
cheaper, very tough, don't like bending. Rear axles only. |
Strange |
1541M |
Induction Hardened RC 58-62 |
Rear axles only. |
Summers Brothers |
alloy steel |
through hardened |
Rear axles only. |
Superior |
4340 |
Through hardened to RC35 AND
Induction hardened to RC 52 |
|
Warn |
4340 |
Through hardened |
Hardened to Rockwell C 55,
(too high for 4340 making the yoke ears brittle.)
No Dana 60 apps. |
So, strength of size and strength
of material are important - what about strength of shape? that leads me to the
next section:
Profile
We already know why the profile,
or shape of the axle shaft is so important to its strength - we just may not
know that we know! When we combine what we already know with the concept
of "stress concentration" and the first law of thermodynamics, we
will truly understand the importance of axle shaft profile.
But first, we need to review a few
concepts:
The first
law of thermodynamics.
The
first law of thermodynamics states that energy can neither be created nor
destroyed, only converted from one form to another. In other words, energy
in = energy out. It has to go somewhere or be transferred into something
else - it can't just disappear. In other words:
E = MC^2
Trust me - it's important.
Concentration
of Stress.
When we apply a force or load to
a part we apply stress (stress is merely the force divided by the cross sectional
area). We can imagine the overall stress we put on a part to be made up
of innumerable separate forces which in turn we can visualize as being tiny
threads or straight lines running through the part. For example, if we
take a solid, constant diameter steel shaft and pull on opposite ends (place
it in tension) the stress in the shaft can be pictured as countless tiny lines
of stress running the length of the shaft from one end to the other. |
 |
These
lines are formally known as "stress trajectories"
Picture concept adapted from "High Performance Hardware"; Forbes Aird |
Now here's the thing about stress
trajectories - they have to flow, like water. They flow through and along
a material. They cannot flow through space or air. That means, if
a stress trajectory is happily flowing along and then suddenly meets space,
for example if there is a sharp corner, a notch, or a hole in the part, it gets
very unhappy. It cannot simply stop, or leap out into space - it has to
bunch up with other stress trajectories to go around the interruption.
This causes a concentration of stress. Picture it like water flowing along in
a stream - if there is suddenly a rock in the middle of the stream, the water
must bunch up and flow around it. In the stream, we would see this as
turbulent water or eddies in the stream around the rock. In our steel
part under load we cannot see the bunched up stress trajectories, but they are
there, and we sure as heck need to account for them. |
 |
Stress Trajectories bunching up as
they are forced to dodge around a notch, creating a stress concentration.
Picture from "High
Performance Hardware"; Forbes Aird |
You see, the thing about stress
bunching up, is that it is now concentrated - and that can and will cause failures.
For example, imagine our plain steel shaft has a cross sectional area of 1 square
inch. Suppose we placed a tensile force of 100 pounds on it. The
uniform stress in the shaft would be 100 psi, with all the stress trajectories
happily running along the length of the bar. Now suppose we cut a notch in the
shaft, or reduced its diameter - suddenly some of the stress trajectories would
have to bunch up to get around the interruption, causing a stress concentration.
Mathematically we have suddenly reduced the cross sectional area in that spot
to < 1 sq. in. so that the 100 lb force is divided by <1 sq. in.
so that the stress, in pounds PER square inch, goes up. The severity of
the stress concentration depends on how suddenly the area changes, and any change
in shape or area that causes the stress trajectories to focus into a smaller
area,(to bunch up), will produce a stress concentration - holes, notches, grooves,
cracks, radius changes, are all guilty. These areas of stress concentration
are known as "stress raisers". In our example, let's assume
the ultimate tensile strength of the shaft was 150 psi. When we pull on
the unmolested shaft with a force of 100 psi, the shaft is fine - it carries
the load without problem. However, once we add a stress raiser, we can
easily cause the stress to concentrate in that area to a level above the UTS
of 150psi, causing the shaft to rupture at that point EVEN THOUGH WE ARE ONLY
PULLING ON IT WITHH 100 PSI, LESS THAN THE UTS!! |
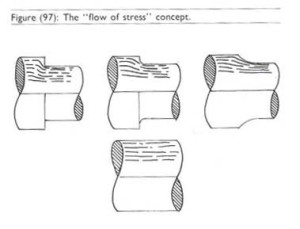 |
Stress trajectories at varying degrees
of concentration, causing stress raisers
Picture from "Engineer to Win" |
Of course, not all stress raisers
can be eliminated - we have to drill holes in things, things have to have corners
and shape changes, and in the case of front axle shafts there need to be shaft
diameter changes (section changes). The key is, to make changes in shape
as gentle and smooth as possible. Any time there is a section change,
no matter how small, there must be a fillet radius - and the radius must blend
smoothly into both adjacent surfaces. There can be no exceptions if we
expect the part to live.[2] |
 |
Picture illustrating the concept
of a fillet radius. Part on the right has it.
Picture from "Engineer to Win" |
|
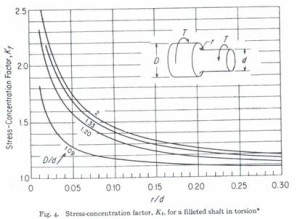 |
Graph illustrating the effect
of proper fillet radii on stress concentration
The fillet radius is labelled
"r" in the shaft diagram.
Note that as the radius of
the fillet (r) gets larger r/d (horizontal axis) gets larger, and the
stress concentration goes down. This effect is magnified the larger the
section change.
In other words the bigger
the difference between the small part and the large part of the shaft,
the more critical the fillet radius.
Picture from Machinery's Handbook |
Profile
What do we mean by a shafts profile?
As illustrated by the following 3
pics, when we speak of a shafts profile, we mean the various diameters along
its length, (its section changes) from the splined end to the yoke. |
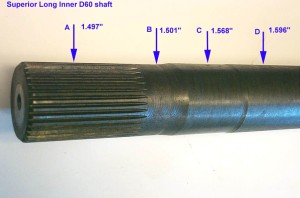 |
Superior Alloy shaft
- D60 long side inner. |
|
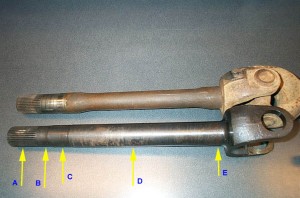 |
Spicer (top) and Superior Alloy
D60 short side inner shafts. |
|
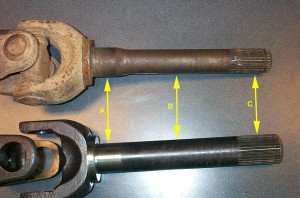 |
Spicer (top) and Superior alloy
D60 stub shafts. |
Summary
So to briefly recap:
- Energy transmitted into a shaft
has to go somewhere - it can't just disappear
- Stress likes to flow, and when
it bunches up, it concentrates - possibly to levels so much greater than the
input stress that the part breaks
- Axle shafts, by necessary design,
will have section changes - resulting in stress concentrations.
- Shaft diameter has huge effect
on torsional deflection of the shaft (How much a solid steel shaft will twist
under load is dependant on the diameter of the shaft raised to the power of
4.
What does all this have to do with
the "ultimate" shaft?
Well, ultimately, how "strong"
a shaft is, how much abuse it can stand, how much load it can carry is very
much affected by the shafts profile - specifically in the following areas:
- The Spline Stress Raiser
- The working diameter of the shaft
- The equalization of torque
Let's examine each in turn:
The Spline
Stress Raiser and Working Diameter
Every splined axle shaft has at least
one huge stress raiser by virtue of it's design. The point at which the
splines end is natural stress raiser. Why should this be so? Imagine a
wheel wedged between 2 rocks, but the throttle pressed and torque applied to
the axle shaft. The splined portion of the shaft, engaged in the carrier, is,
in a manner, held fast. Because the wheel is held steady, the shaft will
immediately twist. Because the force is input via the carrier, we can
instinctively imagine how the stress would concentrate where the splines end.
The concept would be similar to the following example: chuck a thin stick
of wood vertically in your vice, sticking up a couple of feet. Apply a
force to the top of it by pushing, and you already know where it will snap -
right where the jaws of the vice clamp it. Same deal with the splines.
Now, admittedly the torsional stress
an axle shaft experiences is significantly more complicated (being a combination
of tension, compression, and shear) than the simple tension or shear stress
examples we have been using to illustrate concepts - however, we can still use
these simple models to understand the concepts.
Here's what Carroll Smith has to
say, in his usually extremely blunt fashion, about splined shafts profile, particularly
in the area of the end of the splines. |
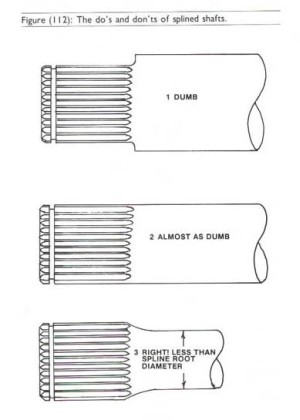 |
Splines MUST
be placed on a diameter that is greater then the operating diameter of the
part, or they must be eliminated from the design. Spline roots must
never be allowed to blend into the operating diameter.[3] |
So, in order to deal with the spline
stress raiser, the textbook way to build an axle shaft is to make the operating
diameter of the shaft smaller than the diameter of the splines. This not
only serves to reduce the stress raiser at the root of the splines, but, if
we re-examine the equation for torsional deflection, we can easily see how this
reduced diameter also allows the axle shaft to twist more. Recalling how
energy is converted, this twisting allows the shaft to convert the energy (mainly
into heat through internal friction) as opposed to just transferring it where
it would break U-joints, ring and pinions, driveshafts, transmission outputs,
etc. As we discussed under material - the key is then to build the shaft
from a high enough quality material to be able to handle this twisting comfortably
withing the elastic range.
This "reduction of shaft diameter
after the splines" is often commonly referred to (and often with a negative
connotation) as "neckdown". This proper neckdown IS NOT to be
confused with what the OEM's do (e.g. notorious D44 front axle neckdown).
That OEM Spicer neckdown is done either as a manufacturing convenience (to facilitate
quick, easy splining) or to introduce an intentional design weak point (so that
if the ring and pinion fails/seizes in 4wd the shaft breaks and the wheels remain
free and steerable as opposed to the front wheels locking up) - depending on
who you ask.
Note that there is a discrepancy
between this neckdown rule, and making the diameter of the shaft as large as
possible for maximum strength. Like all design - there is a trade off
and a compromise must be reached. With this in mind, consider that when
building a stock-replacement axle to fit into existing carriers, the manufacturer
is limited to an existing, exact spline size - they can't make it larger or
smaller - the splines have to fit the carrier. So, in order to obey the
neckdown rule, they would have to make the shaft, in the case of a D60, smaller
than 1.50". This may well cross the line of diminishing return.
In other words, when the final engineering analysis is done, it may turn out
that keeping the shaft operating diameter at 1.50" actually imparts greater
overall load carrying capacity/strength to the shaft than would obeying the
neckdown rule.
Add in the strength of the materials,
as well as the cost/complexity factor of manufacturing an axle with a neckdown
and we begin to get a clearer picture.
There are, in fact, no aftermarket
companies that I'm aware of making replacement shafts for Dana axles with this
particular profile feature, the proper neckdown - not even Superior. I
asked around amongst all my contacts and tried to find out why - nobody's talking.
I suspect that the added complexity and expense of this design, especially when
balanced against the wide design margin afforded by the high quality materials
(heat treated 4340) in use amongst the top companies, and the trad-off in strength
vs shaft diameter, when coupled with an analysis of the shafts required duties
(in a rock-crawler, as opposed to drag car etc.) that the decision is that it's
just not worth it.
I do know, however, that certain
axles built by Sandy Cone and other suppliers to the big $$ trophy trucks have
the textbook neckdown profile - it's just not common on front D60 4x4 shafts.
The concept
of equal torque.
There is one more important aspect
of axle shaft profile we should examine before moving on, and that is the concept
of equal torque.
Imagine climbing a steep, rocky climb.
You need to get your foot into it, and as result you're hopping and skidding
all over the place with the weight bouncing around and the tires alternately
spinning and then suddenly grabbing traction. This is a nightmare for
axle shaft survival - but a scenario we commonly encounter and expect our parts
to survive! In this scenario, or any other high-load situation, the axle
as an assembly has the greatest chance of survival if both shafts survive.
For both shafts to survive - the best scenario is for them to share the abuse
/ stress; to participate equally in sharing the load.
However, there's one big gotcha -
almost always one shaft is dramatically shorter than the other. In my
own GM Dana 60, the long side shaft is 35" long, or about 50% longer than
the 18" short side shaft. The problem with this becomes evident when
we recall once again our friend the angular deflection equation (math is soooo
cool :-)
alpha=[584(T)(l) ] / D^4 * G
Where:
alpha = the torsional deflection
in degrees (how much it twists)
T = Torsional or twisting moment in inch pounds (torque or load placed on the
axle)
l = length of the shaft in inches
D = diameter of shaft in inches
G= torsional modulus of elasticity (a constant for all steel shafts at 11,500,000
psi )
In my front axle in any given "all
wheels driving" situation, for each shaft G and T are equal, or about equal,
and l is quite different: meaning that if D is constant between the 2 shafts,
the longer shaft will twist more than the short. This will normally allow
the energy to be dissipated better in the longer, greater twisting shaft than
in the short shaft - this explains why quite often we see more broken short
side axles than long. The converse is also possible, depending on the
nature of the loading on the axle (magnitude, axle material, etc), the long
side axle may fail prematurely because it twists so much more than the short
side. Either way this explains why some rigs perpetually break one side
or the other.
Regardless, the optimum situation
is to have both shafts share the load and twist equally - thereby creating the
most reliable and predictable assembly. This concept is the concept of
equal torque. On last look at the equation, and we see that for either
shaft of any given axle we can't change l or G, and we have no real way to predict
or control T (except let up on the loud pedal - and what fun is that?) so the
only way to achieve equal torque loading of the shafts is to alter D between
the shafts. Note that D is raised to the fourth power so that small changes
in shaft diameter have relatively large effects on how much the shaft will twist.
A well made axle shaft will take
this into account. Again, it will come as no surprise that Superior do,
in a process they call their "exclusive (patent pending) Torque Equalizing
Diameter Profile"
OK, so if we understand material,
heat treatment, neckdown, operating diameter, and torque equalization, it's
time to consider the last factor in shaft design - splines.
Axle Spline Technology
The actual splined section of an
axle shaft has a dramatic effect on the overall strength of an axle shaft; from
their size, shape and angle to how they were made and how well they fit in the
carrier. |
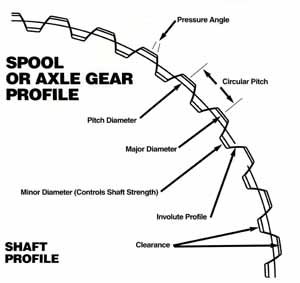 |
A splined shaft has a minor and major
diameter and is further classified by the shape of the splines, the pressure
angle, the number of teeth, and the diametrical pitch. |
Major and
Minor Diameter.
As illustrated in the diagram above,
the major diameter is the diameter of the splined section of the shaft measured
at the outside or tips of the teeth of the splines. The diameter of the shaft
at the bottom of the grooves between the teeth is the minor diameter of the
splines.
Shape |
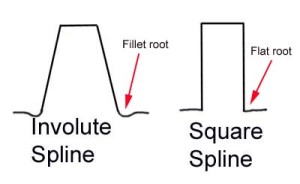 |
Splines are either "square"
or "involute" in shape. Involute splines have teeth with a profile
as shown in the above pic where the tip is narrower than the base. Involute
splines have 3 distinct advantages over square cut:
- Involute spline couplings
have greater torque-transmitting capacity than any other type
- Involute splines can be produced
using the same techniques and equipment as is used to cut gears; and
- Involute splines have a self-centering
action under load even when there is backlash between mating members[4]
- the faces of the splines are slightly
curved to provide optimum contact and even pressure distribution during engagement
|
Square cut splines are quite old-fashioned
and are rarely used anymore. However, I mention them because some aftermarket
axle shaft shorten-and-respline outfits cut splines using equipment that is
not able to reproduce the correct involute spline profile. This
is a disaster because, even if you can get the square cut splined shaft to engage
with the involute spline carrier, the contact points will be focused on a very
concentrated area, causing enormous stress concentrations - and we know all
about avoiding them, don't we!.
The only way to produce the correct
involute spline is to roll, hob, or cut them using a single point cutting
process with a correctly shaped cutter. Axles that have been made or resplined
using a flycutting procedure will NOT have proper involute splines.
In addition to the shape of the tooth,
splines also have either a fillet root or flat root. The root of the spline is
the area where the tooth originates from the shaft. As you can imagine,
the root would be an enormous concentration of shearing stress. Recall
from our discussion on the flow of stress that a fillet radius will help relieve
this concentration of stress, which must be balanced against the slightly smaller
minor diameter that results. Most of our axles are fillet root.
Pressure
angle
Not all involute
splines are the same shape - there are variation in exact "tooth shape"
possible. These differences in tooth shape are known as
the pressure angle of the spline. The pressure angle is the basic included
angle of the spline tooth (see diagram above). Common axle spline pressure
angles are 30° (60° included angle) and 45° (90° included angle). 45°
pressure angle splines offer a slight strength advantage because for a given
major diameter spline the teeth
of a 45° spline are shorter-allowing for a larger minor diameter size.
Dana and some GM axles are 30°, Ford, Toyota, some GM, and most racing axles are 45°. Some Rockwell and
older axles are 37.5° pressure angle.
The most important thing is to ensure
you MATCH the pressure angle of the shaft with the pressure angle of the carrier
being used. It is no good at all to try and cram a 45° pressure angle
aftermarket axle shaft into an OEM 30° pressure angle carrier - like forcing
a square cut spline in an involute carrier, the stress would be focused on far
too small an area creating uneven pressure points and unacceptable stress raisers
begging for failure. |
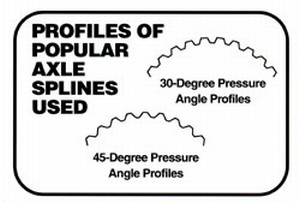 |
|
Diametrical
Pitch
Diametrical pitch
of splined shaft is a specification that relates the number of splines to the
size of the shaft. This spec is what allows us to refer to an axle as
just "35 spline" and be able to compare it to a "30 spline"
axle without having to also list the minor and major diameters of the shafts.
For example, almost anyone would instinctively tell you that a 35 spline
shaft was stronger than a 30 spline shaft. But what if the 35 spline shaft
had a minor diameter of 1 inch and the 30 spline shaft had a minor diameter
of 2 inches? I can tell you without doing the engineering math that the
30 spline 2' shaft would be stronger. To avoid this confusion, and indeed
to insure that the number of splines and the size of the shaft are standardized
so that the teeth are evenly spaced and parts can be made to fit together, we
have the concept of diametrical pitch. We
are familiar with the fact that there are a limited, set number of standard
threads-per-inch available that match certain bolt sizes (e.g. a 3/8" bolt
has either 16 (coarse) or 24 (fine) threads per inch) so that we may have a
reasonable chance of finding nuts and bolts that fit together - can you imagine
if the number of different threads per inch for any size bolt were unlimited?!!
In the same way, splined shafts must have a limited number of possible diameter
and # of teeth combinations. Instead of threads-per-inch, diametrical
pitch is used.
The pitch diameter
of a splined shaft is is the
mid-point between the major and minor diameters. The diametrical pitch is the
number of teeth per inch of pitch diameter, similar to the number of threads
per inch specified for bolt threads. Because the splines are all the same
size and shape, the distance between the centreline of adjacent splines (the
circular pitch) remains constant. Therefore as the pitch diameter of the shaft
increases, more teeth can "fit around" the pitch diameter, and therefore
the larger the shaft diameter the larger the number of splines for any given
diametrical pitch.
An actual diametrical pitch specification
will be a number specifying the number of teeth per inch of pitch diameter.
Industry standards state that most modern automotive axle shafts (All of the
28, 30, 31, 35, 40 spline axles that interest us) are 24-pitch. Therefore, if
the shaft had a 1-inch circular pitch diameter it would have exactly 24 splines
(or teeth). Using this standard diametrical pitch of 24-pitch a 35-spline axle
has a major diameter of 1,500 inches; a 40-spline 1.708 inches.
Note that if you know the diametrical
pitch of a splined shaft you can calculate its major diameter. This may
be counter-intuitive, as it may seem as if one would decide to use a 1.5"
diameter shaft, and then decide to cut splines into and settle on 35 splines.
This is not how it actually works, In reality, the pitch controls the
major diameter, as the following equation demonstrates. Using the equation
you can calculate the number of splines on any size shaft or conversely the
size of any shaft given the pitch and number of splines.
Major Diameter
Do=(N+1)/P
Where:
Do = major diameter of splined shaft
N = number of splines
P = diametrical pitch (24 for just about every axle we care about)
If you know any 2 of the 3 variables
you can simply rearrange the equation algebraically and compute the third/
For example:
Q: What is the major diameter of
a 35 spline shaft?
A: N=35, assume P=24, Do=(N+1)/p
= (35+1)/24 = 36/34 = 1.50"
Yipeeee! Fun with math again!
Q: - What is the major diameter
of a 30 spline Dana axle?
Bonus question - what is the diametrical
pitch of the fabled full-float GM 14 bolt axle shaft (and why the heck did they decide
to be different from the rest of the planet?)
30 |
45° |
Basis For Comparison: GM 12 Bolt |
1.2917 |
1.2083 |
0.0% |
0.0% |
|
|
|
|
|
|
|
28 |
30° |
Older Jeep/Dana |
1.1960 |
1.127 |
-7.9% |
-21.9% |
30 |
30° |
Dana 44 |
1.2793 |
1.1960 |
-1.0% |
-3.0% |
35 |
30° |
Dana 60 |
1.4876 |
1.4043 |
16.2% |
57.0% |
|
|
|
|
|
|
|
26 |
45° |
Late GM 10 bolt |
1.1250 |
1.0417 |
-13.8% |
-35.9% |
28 |
45° |
Early GM 10 bolt, Ford
9", & Ford 8.8" |
1.2083 |
1.1250 |
-6.9% |
-19.3% |
31 |
45° |
Ford 9" |
1.3333 |
1.2500 |
3.5% |
10.7% |
33 |
45° |
Ford 9" |
1.4167 |
1.3333 |
10.3% |
34.4% |
35 |
45° |
Mark Williams 35 Spline |
1.5000 |
1.4167 |
17.2% |
61.2% |
40 |
45° |
Mark Williams 9" &
40 spline Dana 60 |
1.7083 |
1.6250 |
34.5% |
143.2% |
Methods of
Forming
We have come to the
final factor to consider in axle spline technology and indeed in the whole process
of deciding which axle shaft is the best - and that is the topic of how the
splines are formed in the shaft.
There are basically 4 ways to spline
an axle shaft:
1. Rolling the spline: This
is a cold-working process. It is done by a huge and powerful hydraulic
powered machine that presses the splines into the shaft with anything from 2,500
psi - 7,000 psi, depending on the shaft. Recall from part 1 of the article
that this cold-working process produces a refined and more consistent grain
structure, resulting in a stronger part. The rolling machine has 2 plates
that are extremely hard dies with the appropriate spline shape to them.
The axle is rolled between these plates, one top and one bottom, and the splines
are thus cold formed into the shaft. This is the very best way possible to form
a spline as it is a cold working process, it removes no material from the shaft,
and finally because it is done prior to the axle shaft being heat treated (hardened).
Compared to a spline cut after hardening, a properly rolled spline will be up
to 30 or 35% stronger. There are VERY few companies capable of rolling
splines. The only two I know of are Dana/Spicer and Superior Axle and
Gear. The drawback (for a manufacturer) to rolling splines is that not
only is the equipment very expensive, but it is also time-consuming to set up,
so that it is only feasible to roll splines in axles in large batches.
This explains why so few aftermarket axles have rolled splines, and why virtually
no custom shafts will have rolled splines.
2. Hobbing: Hobbing splines is the
second-best way to from a splined shaft. Many very specialized, highly
custom race and drag axles have their splines hobbed. The spline hobber
is a machine that cuts all the splines at the same time. Hobbing produces a
true involute spline shape, and if done before the shaft is hardened, some would
argue there is very little strength difference between hobbed and rolled splines.
Practically speaking this is probably quite true, but rolling is still the very
best method.
You can tell a rolled spline from
a hobbed or cut spline quite easily by looking at how the root of the splines
terminates. |
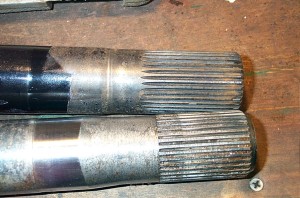 |
In this pic of
D60 inner shafts, the top shaft is a pre-production Superior D60 shaft
with hobbed splines, the lower is a Spicer inner shaft with rolled splines.
Note the very square ends of
the splines in the shaft with rolled splines, compared to the pointy ends
of the hobbed splines. |
|
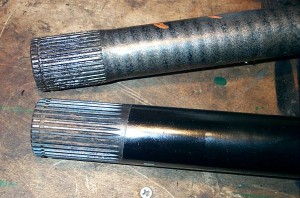 |
In this pic the top shaft is
a Spicer stock D60 stub shaft with rolled splines, the lower is a Superior
D60 shaft with hobbed splines. Again, note the different appearance. |
3. Spline shaping or cutting.
There are many variations and different pieces of equipment that can and are
used for cutting the splines. Using this method, the splines are cut one
at a time. In many cases (e.g. flycutting splines) the cutting process
does not produce a proper involute spline profile. Another problem with
cutting splines, particularly in re-splining operations, is that it is done
AFTER the shaft is hardened, and most often induction hardened too. However,
acceptable results can be obtained if the cutting is
a) done on a through hardened shaft
or; with an induction hardened shaft done either before hardening or only to
a depth that doesn't approach the hardened depth (this will depend on spline
size/pitch and case depth); and
b) done in such a manner as to produce the proper involute shape, pressure angle,
and preferably fillet root. Single point cutting on a mill can produce an involute
profile if the cutting tool is shaped correctly.
4. Spline grinding: splines are
ground into the shaft with a diamond or carbide tip grinding wheel. this
is another process where splines are formed one at a time. I know very
little else about this method and I don;t know if or who any 4x4 axle shaft
manufacturers use spline grinding.
Summary. Rolled splines are
best but rare, hobbed splines (done before hardening) are almost as good, and
cut splines have a number of issues and don't really qualify an axle shaft for
"ultimate" status.
Axle Failure Analysis
This is a huge and
very complicated topic in itself, and will be added at a later date. Failure
analysis is complicated at best, and when one considers the effect of fatigue
life, extremely difficult. For example, consider the calculation
of the polar moment of inertia:
The polar moment of inertia ,
J, of a cross-section with respect to a polar axis, that is, an axis at right
angles to the plane of the cross-section, is defined as the moment of inertia
of the cross-section with respect to the point of intersection of the axis and
the plane. The polar moment of inertia may be found by taking the sum
of the moments of inertia about two perpendicular axes lying in the plane of
the cross-section and passing through this point. Thus, for example, the
polar moment of inertia of a circular or a square area with respect to a polar
axis through the center of gravity is equal to two times the moment of inertia
with respect to an axis lying in the plane of the cross-section and passing
through the center of gravity.
The polar moment of inertia with respect to a polar axis through the center of
gravity is required for problems involving the torsional strength of shafts
since this axis is usually the axis about which twisting of the shaft takes
place.
The polar section modulus (also called section modulus of torsion), Zp, for
circular sections may be found by dividing the polar moment of inertia, J, by
the distance, c, from the center of gravity to the most remote fiber.
This method may be used to find the approximate value of the polar section modulus
of sections that are nearly round. The polar section modulus multiplied
by the allowable torsional shearing stress gives the allowable twisting moment
to which a shaft may be subjected.[5]
So there!
Formulae and Calculations
For the mathematically
inclined and those that like to calculate stuff, here are some interesting formulae:
Roy McBride and Dave Towers of Heriot
Watt University excellent tutorial on Torsion
of shafts with circular symmetry an MS Word .doc file. Also available in .pdf format
Conclusion
Hopefully this brief look at the
tech behind axle shafts has been informative and has shown that there's a lot
more to the topic than might first appear. It should also greatly assist
in discussions or debates about who or what is best . I certainly hope that
it illustrates that in choosing shafts for the BV-60 I didn't just pull any
manufacturer out of my hat.
For an axle shaft to be considered
the "ultimate" we must consider:
The Material |
Superior uses 4340
chrom-moly steel |
The Heat Treatment |
Superior uses a unique DUAL
heat treatment - through hardened shaft for strength, then induction hardened
for fatigue resistance |
Strength of Size |
Superior's alloy Dana60 shafts
are larger in every possible dimension than any other D60 shaft |
Proper Neckdown |
Not present on the Superior
shafts - I guess nobody's perfect! |
Torque Equalization |
Superior design this in with
what they call "Torque Equalizing Diameter Profile" |
Rolled or Hobbed involute splines |
Superior alloy D60 inner shafts
have hobbed splines and outer (stub) shafts have rolled splines. |
Notes:
[1] "Machinery's Handbook"
24th Edition. Erik Oberg, Franklin D. Jones, Holbrook L. Horton, Henry H. Ryffel,
Robert E. Green; Industrial Press Inc., 1992 p.475
[2] "Engineer to Win".
Carroll Smith; Motorbooks International, 1985 p.115
[3] "Engineer to Win".
Carroll Smith; Motorbooks International, 1985 p.119
[4] "Machinery's Handbook"
24th Edition. Erik Oberg, Franklin D. Jones, Holbrook L. Horton, Henry H. Ryffel,
Robert E. Green; Industrial Press Inc., 1992 p.2034
[5] "Machinery's Handbook"
24th Edition. Erik Oberg, Franklin D. Jones, Holbrook L. Horton, Henry H. Ryffel,
Robert E. Green; Industrial Press Inc., 1992 p.265 |
|