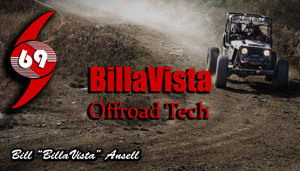 |
Basic Hydraulics
By Bill "BillaVista" Ansell
Photography: Bill Ansell
Copyright 2003 - Bill Ansell
(click any pic to enlarge)
|
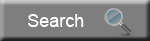 |
Introduction
What exactly is cavitation, and why
should I care? What are the functions of the fluid reservoir? Should I use pipe,
tubing, or hose to connect my components?
If you have ever pondered the answer
to these questions, and many many more, then this is the section for you.
It will be a bit dry, lots of theory
and definitions, and not many pictures. However, I felt it was vital to include
it, so that, for instance - when we later discuss hydraulic steering and talk
about concepts like flow and pressure drop and such, we know we have a good
basic understanding of the fundamentals. |
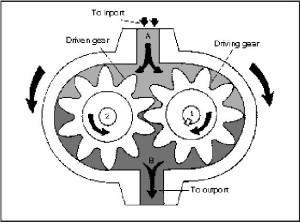 |
I know many of you will not read it
all, or even much of it. That's fine and expected, but don't complain to me
later when I explain the use of some component on your 4x4 steering system by
quoting Pascal's law and you're lost :-) If nothing else - this section can
exist as a knowledge base, so that later, should we need to debate some topic
(should my system be sealed or vented? do I need a pressure relief valve? etc.)
we will at least have some credible facts at our fingertips to back up our positions.
The information in this section is
drawn primarily from 3 main sources. They are: (click name to view the document
in .pdf format)
Much of the basics is also available
in many basic hydraulics manuals and physics text books .
I claim no credit for this material
- I am merely presenting aspects of it that I feel are relevant to our needs
and discussion. I have no ethical problems with this whatsoever because
- I have told you this is so, and
am not claiming the work as my own;
- Much of the information and data
is basic physics / hydraulics, information that exists in the open realm -
I don't think any government branch or corporate entity owns the copyright
on the plain language expression of Bernoulli's Principle
- All of my sources are freely available,
at no cost, to anyone with internet access. Clearly the authors / publishers
want everyone on the planet to know everything they have written in their
manuals.
I have bothered to extract, edit,
and add comments to this open source information because I feel it IS important
that we share common understanding of facts, and use some semblance of standard
terminology in our exploration of hydraulics and particularly hydraulic steering.
I have not simply sent you to the references (though they are available and
I do recommend you read them) because they are large and very general in nature
(the Army manual is 174 pages long), as one would expect; the documents having
been themselves written by very LARGE entities with broad interests.
So I felt that I could do a service
to my readers by extracting only that data that I feel is useful and relevant
(the study of hydraulics would, after all, fill several large books) and, in
a sweeping delusion of grandeur I actually peppered the irrefutable factual
text from the acknowledged experts with my own little comments - purportedly
to add emphasis and explanation that some might find illuminating or useful.
I guess you'll have to decide if I was right or not!
As a final note, keep in mind that
much of the basic facts of hydraulics can be applied to many more vehicular
systems than just "full hydraulic steering" for a hardcore 4x4. Normal
power steering, all vehicular service brakes, and automatic transmissions are
three of the more common applications of hydraulics of interest to the automotive
enthusiast. So you just may gain a better understanding of these as we go along
......think of it as a nice bonus!
I have highlighted what I believe
to be the most critical information in bold text. My comments are identified
by being in italics.
This part, Basic Hydraulics, is broken
up into sections that roughly follow the components that make up any basic hydraulic
system. Specifically:
- Basic Hydraulic Physics
- Hydraulic Systems
- Reservoirs
- Strainers and Filters
- Circulatory Systems
- Fittings and Connectors
- Seals
- Pumps
- Hydraulic Actuators
- Valves
- Accumulators
- Troubleshooting
- Circuit Diagrams and Symbols
- Glossary
1. Basic Hydraulic
Physics
Hydraulics is the science of transmitting
force and/or motion through the medium of a confined liquid. In a hydraulic
device, power is transmitted by pushing on a confined liquid. |
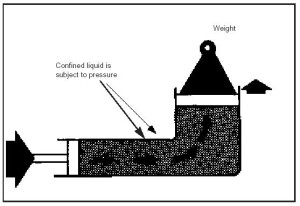 |
Basic hydraulic
device |
1-1. Pressure and Force.
Pressure is force exerted against
a specific area (force per unit area) expressed in pounds per square inch (psi).
A fluid is any liquid or gas (vapour). Force is anything that tends to produce
or modify (push or pull) motion and is expressed in pounds.
Pressure can be created by squeezing
or pushing on a confined fluid only if there is a resistance to flow. The two
ways to push on a fluid are by the action of a mechanical pump or by the weight
of the fluid.
Force. The relationship of force,
pressure, and area is as follows: F = PA
where—
F = force, in pounds
P = pressure, in psi
A = area, in square inches |
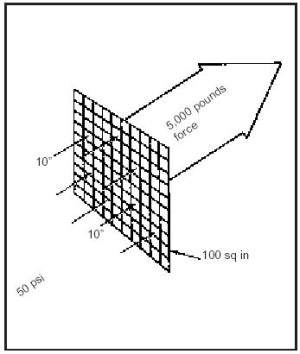 |
The relationship
between Pressure, Area, and Force. |
1-2. Pascal's Law.
Pressure in a confined fluid is transmitted
undiminished in every direction and acts with equal force on equal areas and
at right angles to a container's walls. |
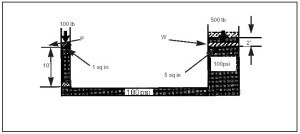 |
Pascal's Apparatus. |
The above picture shows the apparatus
that Pascal used to develop his law. It consisted of two connected cylinders
of different diameters with a liquid trapped between them. Pascal found that
the weight of a small piston will balance the weight of a larger piston as long
as the piston’s areas are in proportion to the weights. In the small cylinder,
a force of 100 pounds on a 1-squareinch piston creates a pressure of 100 psi.
According to Pascal's Law, this pressure is transmitted undiminished in every
direction. In the larger cylinder, the 100 psi of pressure from the small cylinder
is transmitted to an area of 5 square inches, which results in a force of 500
pounds on the second piston. The force has been multiplied 5 times—a mechanical
advantage of 5 to 1. Using the same factors, you can determine the distance
the pistons move. For example, if the small piston moves down 10 inches, the
larger piston will move up 2 inches. Use the following to determine the distance:
D2= F1 x D1 / F2
where—
F1 = force of the small piston, in pounds
D1 = distance the small piston moves, in inches
D2 = distance the larger piston moves, in inches
F2 = force of the larger piston, in pounds
If you think about these basics,
they explain the extreme utility of hydraulics. They explain why it is possible
to lift massive weights using a hydraulic jack with very little input force
required. They also explain the basics of automotive hydraulic service breaks,
where one piston (the small piston) is the master cylinder piston, and one piston
(the large [piston) is the disc break calliper piston. These basic laws also
explain why statements like "using larger diameter brake lines (or any
hydraulic line) will cause the brakes (or any hydraulic device) to operate more
quickly" are completely false. Remember, once the brake system is full
of fluid and bled of air, think of the hydraulic fluid as just a very flexible
mechanical connection. It doesn't compress, it doesn't "travel" along
the lines - it transmits pressure "undiminished in every direction and
acts with equal force on equal areas (including the brake calliper pistons)
and at right angles to a container's walls."
1-3. Flow.
Flow is the movement of a hydraulic
fluid caused by a difference in the pressure at two points. In a hydraulic system,
flow is usually produced by the action of a hydraulic pump—a device used
to continuously push on a hydraulic fluid. The two ways of measuring flow are
velocity and flow rate.
a. Velocity.
Velocity is the average speed at which a fluid's particles move past a given
point, measured in feet per second (fps). Velocity is an important consideration
in sizing the hydraulic lines that carry a fluid between the components.
b. Flow Rate.
Flow rate is the measure of how much volume of a liquid passes a point in a
given time, measured in gallons per minute (GPM). Flow rate determines the speed
at which the hydraulic system is able to accomplish work, like lifting a
load or steering wheels and, therefore, is important when considering power.
1-4. Energy, Work,
and Power.
Energy is the ability to do work
and is expressed in foot-pounds (ft/lbs). Three forms of energy most important
in hydraulics are potential, kinetic, and heat. Work measures accomplishments;
it requires motion to make a force do work. Power is the rate of doing work
or the rate of energy transfer Recall that energy can never be created or
destroyed, merely converted from one form to another. Power then, is the rate
at which energy is converted from one form to another. For example, your engine's
power is a measure of the rate at which it can convert chemical energy in the
gasoline to kinetic energy (truck motion) and heat and noise.
a. Potential Energy.
Potential energy is energy due to position. An object has potential energy in
proportion to its vertical distance above the earth's surface. A car resting
at the top of a hill has potential energy.
b. Kinetic Energy.
Kinetic energy is the energy a body possesses because of its motion. The greater
the speed, the greater the kinetic energy. That same car, rolling down the
hill (motor off) is converting potential energy to kinetic energy (and of course,
some to noise, heat, etc. too)
c. Heat Energy and Friction.
Heat energy is the energy a body possesses because of its heat. Friction is
the resistance to relative motion between two bodies. When liquid flows in a
hydraulic circuit, friction produces heat. This causes some of the kinetic energy
to be lost in the form of heat energy. This is to be avoided as much as
possible because it wastes kinetic energy (that could otherwise be used to perform
useful work) and worse, the heat created has a negative effect on the systems
components, notably the fluid and seals etc. Although friction cannot be
eliminated entirely, it can be controlled to some extent. The three main causes
of excessive friction in hydraulic systems are:
- Extremely long lines.
- Numerous bends and fittings or
improper bends
- Excessive velocity from using
undersized lines.
|
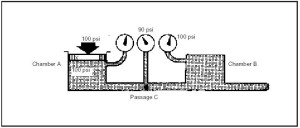 |
Bernoulli's Principle. |
d. Relationship Between Velocity
and Pressure.
Bernoulli's Principle, which states that the static pressure of a moving liquid
varies inversely with its velocity; that is, as velocity increases, static pressure
decreases.
e. Work. To do work in a hydraulic
system, flow must be present. Work, therefore, exerts a force over a definite
distance. It is a measure of force multiplied by distance.
f. Power. The standard unit of power
is horsepower (hp). One hp is equal to 550 ft/lbs of work every second. Use the
following equation to find power:
P = f x d/t
where—
P = power, in hp
f = force, in lbs
d = distance, in psi
t = time (1,714)
2. Hydraulic Systems
2-1. Hydraulic System
Components
Most hydraulic systems (also
called circuits, just like in electronics) contain the same basic components.
Obviously, there are some systems that are very simple, and may only have the
barest essential components (like a hydraulic floor jack), and others can be
enormously complicated, containing hundreds of complicated components. Regardless
of the design, all hydraulic systems contain:
- a reservoir - to hold the
hydraulic fluid
- hydraulic fluid - to do the
work
- a circulatory system (tubes,
pipes, and lines , as well as fittings, connectors, and seals) - to convey
and contain the fluid
- a pump - to create flow and
pressure in the fluid
- valves - to control the flow
and pressure of fluid
- an actuator (cylinder, ram,
motor) - powered by the fluid, to do the work
Most systems also have:
- strainers and filters - for
conditioning the fluid
- coolers - for cooling the
fluid, and preventing fluid deterioration / breakdown
- pressure and temperature gauges
- for monitoring the system condition and performance
And some systems have:
- Accumulators - for storing
pressurized fluid for times of high demand.
The majority of the remainder
of this article will be devoted to exploring each of these in a little more
detail.
A hydraulic system contains and
confines a liquid in such a way that it uses the laws governing liquids, explained
above, to transmit power and do work.
2-2. Basic Hydraulic
Systems.
The advantages of hydraulic systems
over other methods of power transmission are:
- Simpler design. In most cases,
a few pre-engineered components will replace complicated mechanical linkages.
- Flexibility. Hydraulic components
can be located with considerable flexibility. Pipes and hoses in place of
mechanical elements virtually eliminate location problems.
- Smoothness. Hydraulic systems
are smooth and quiet in operation. Vibration is kept to a minimum.
- Control. Control of a wide range
of speed and forces is easily possible.
- Cost. High efficiency with minimum
friction loss keeps the cost of a power transmission at a minimum.
- Overload protection. Automatic
valves guard the system against a breakdown from overloading.
The main disadvantage of a hydraulic
system is maintaining the precision parts when they are exposed to bad climates
and dirty atmospheres. Protection against rust, corrosion, dirt, oil deterioration,
and other adverse environment is very important. This is especially critical
in the harsh, dirty, mobile, stressful, vibration filled environment in which
we operate hydraulic systems on our 4x4s
Most hydraulic systems that are
more complicated than your basic floor-jack are grouped into two broad categories.
This is certainly true of hydraulic steering systems. The two categories are
defined based on how a main fluid control valve functions when the system is
working and not-working. The valve function is dependant on the type of pump
in use (more on pumps and valves later). Suffice to say, at this stage, that
some pumps continuously pump, providing fluid pressure and flow constantly.
When a system with this type of pump is not working (i.e. when the fluid is
not directed to the actuators) the fluid must be able to pass through the valve
and back to the reservoir. The valve is "open" in the center to allow
this, hence these systems are known as "open center" design. In contrast,
some pumps only create flow and pressure when required (on demand) and as such,
their main control valves do not need to allow the fluid back into the reservoir,
and so are closed in the center. Not surprisingly, these are called closed-center
systems. |
 |
Open-Center System. |
Open-Center System. In this system,
a control-valve spool must be open in the center to allow pump flow to pass
through the valve and return to the reservoir. To operate several functions
simultaneously, an open-center system must have the correct connections, which
are discussed below. An open-center system is efficient on single functions
but is limited with multiple functions. This system is satisfactory as long
as only one valve is operating at a time. When this happens, the full output
of the pump at full system pressure is available to that function. However,
if more than one valve is operating, the total of the pressures required for
each function cannot exceed the system’s relief setting. |
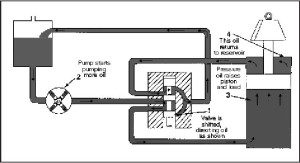 |
Closed-Center System. |
Closed-Center System. In this system,
a pump can rest when the oil is not required to operate a function. This means
that a control valve is closed in the center, stopping the flow of the oil from
the pump.
2-3. Rules for working
with hydraulics
Three most important rules to be
followed when working with hydraulics are:
- CLEANLINESS
- CLEANLINESS
- CLEANLINESS
Rule 1 Concerns cleanliness during
the installation of the hydraulic system. Hoses, pipes and fittings are never
clean after being worked on and must therefore always be cleaned immediately
prior to installation. Pipes, including pipe bends, should preferably be cleaned
with a plug of crepe paper or lint-free cloth soaked in paraffin and blown through
the pipe with compressed air. This process must be repeated with several plugs
until a completely clean plug emerges.
The blanking plugs fitted in all
pumps, motors, valves, etc. must not be re-moved until just before the components
are installed. Workshops, work stations, tools and clothing must also be as
clean as possible.
Rule 2 Concerns cleanliness during
daily operation of a hydraulic system. The tools used for filling must of course
be perfectly clean and the oil filled into the system must be filtered through
filters of the same fineness as the finest in the system, normally 5 µm,
but in any event no coarser than 10 µm nominal.
Rule 3 Concerns cleanliness during
inspection and repair. Before a hydraulic component is removed, both the component
itself and the immediate surroundings must be clean. All open parts, pipes,
hoses, etc. must be blanked off with, for example, plastic bags bound on so
that dirt and dust cannot enter the system when it is in standstill.
The other critical concern with
hydraulic systems is fluid temperature. Most suppliers prescribe 194 °F
(90°C) as an absolute maximum. We shall examine why, and what to do about
it in the section on fluid.
2-4. System Design
Each component in the system must
be compatible with and form an integral part of the system. For example, an
inadequate size filter on the inlet of a pump can cause cavitation and subsequent
damage to the pump. Each component in the system has a maximum rated speed,
torque or pressure. Loading the system beyond the specifications simply increases
the possibility of failure
All lines must be of proper size
and free of restrictive bends. An undersized or restricted line results in a
pressure drop in the line itself.
Some components must be mounted in
a specific position with respect to other components or the lines. The housing
of an in-line pump, for example, must remain filled with fluid to provide lubrication.
Systems should be designed for a
correct operating pressures. The correct operating pressure is the lowest pressure
which will allow adequate performance of the system function and still remain
below the maximum rating of the components and machine. Always set and check
pressures with a gauge
Knowing the System is probably the
greatest aid to troubleshooting problems later on.
3. Reservoirs
3-1. Reservoirs.
A reservoir stores a liquid that
is not being used in a hydraulic system. It has many other important functions
too:
- It also allows gases to expel
and foreign matter to settle out from a liquid.
- It functions as a cooler
- It functions as a "coarse
strainer", providing sedimentation of impurities
- It functions as an air and water
separator
- It functions as a foundation for
pumps etc.
a. Construction. A properly constructed
reservoir should be able to dissipate heat from the oil, separate air from the
oil, and settle out contaminates that are in it. Reservoirs range in construction
from small steel stampings to large cast or fabricated units. The large tanks
should be sandblasted after all the welding is completed and then flushed and
steam cleaned.
b. Shape. Design features of a reservoir.
It should be high and narrow rather than shallow and broad. The oil level should
be as high as possible above the opening to a pump's suction line. This prevents
the vacuum at the line opening from causing a vortex or whirlpool effect, which
would mean that a system is probably taking in air. Aerated oil will not properly
transmit power because air is compressible. Aerated oil has a tendency to break
down and lose its lubricating ability. To increase the ability of the tank to
separate dirt and water, the bottom must be slightly inclined (deepest end opposite
the inlet/outlet end). An ordinary cock (without handle) is fitted so that impurities
can easily be drained off. Increased separation of the air that is always present
in the oil can be obtained by fitting an inclined coarse metal strainer (approx.
25-50 mesh/ inch) by the return line. Both suction and return pipes must be
cut diagonally. The ends of the pipes must be located 2-4 times the pipe diameter
above the bottom of the tank, partly to avoid foaming at the return line, and
partly to prevent air from being drawn into the suction line, especially when
the vehicle/vessel heels over to one side.
c. Size. A reservoir must be large
enough so that it has a reserve of oil with all the cylinders in a system fully
extended. An oil reserve must be high enough to prevent a vortex at the suction
line's opening. A reservoir must have sufficient space to hold all the oil when
the cylinders are retracted, as well as allow space for expansion when the oil
is hot. A common-size reservoir on a mobile machine is a 20- or 30-gallon tank
used with a 100- GPM system. Many 10-GPM systems operate with 2- or 3-gallon
tanks because these mobile systems operate intermittently, not constantly. For
stationary machinery, a rule of thumb is that a reservoir’s size should
be two to three times a pump’s output per minute. A large size tank is
highly desirable for cooling. The large surface areas exposed to the outside
air transfer heat from the oil. Also, a large tank helps settle out the contaminates
and separates the air by reducing recirculation. If the application is mobile,
if there is no cooler built into the system, and provided the tank is located
where air circulation is good, ideally the size of the tank should be approx.
2-3 times the capacity of the pump per minute. In our 4x4 systems we are unlikely
to be able to achieve such large reservoir capacities as this, but the important
lesson is that your reservoirs cannot be too big - it is best to use the largest
possible reservoir space and weight restrictions allow.
d. Location. Most mobile equipment
reservoirs are located above the pumps. This creates a flooded-pump-inlet condition.
This condition reduces the possibility of pump cavitation—a condition
where all the available space is not filled and often metal parts will erode.
Flooding the inlet also reduces the vortex tendency at a suction pipe's opening.
The location of a reservoir affects heat dissipation. Ideally, all tank walls
should be exposed to the outside air. Heat moves from a hot substance to a cold
substance; heat transfer is greatest when there is a large temperature difference.
e. Ventilation and Pressurization.
Most reservoirs are vented to the atmosphere. A vent opening allows air to leave
or enter the space above the oil as the level of the oil goes up or down. This
maintains a constant atmospheric pressure above the oil. A reservoir filter
cap, with a filter element, is often used as a vent. Some reservoirs are pressurized,
using a simple pressure-control valve rather than a vented one. A pressure-control
valve automatically lets filtered air into a tank but prevents air release unless
the pressure reaches a preset level. A pressurized reservoir takes place when
the oil and air in a tank expand from heat.
f. Line Connections. A pump suction
and a tank's return lines should be attached by flanges or by welded heavy-duty
couplings. Standard couplings usually are not suitable because they spread when
welded. If a suction line is connected at the bottom, a coupling should extend
well above the bottom, inside the tank; residual dirt will not get in a suction
line when a tank or strainer is cleaned. A return line should discharge near
a tank's bottom always below the oil level. A pipe is usually cut at a 45-degree
angle and the flow aimed away from a suction line to improve circulation and
cooling. A baffle plate is used to separate a suction line from a return line.
This causes the return oil to circulate around an outer wall for cooling before
it gets to the pump again. A baffle plate should be about two-thirds the height
of a tank. The lower corners are cut diagonally to allow circulation. They must
be larger in area than a suction line's cross section. Otherwise the oil level
between a return and a suction side might be uneven. Baffling also prevents
oil from sloshing around when a machine is moving. Many large reservoirs are
cross-baffled to provide cooling and prevent sloshing.
g. Maintenance. Maintenance procedures
include draining and cleaning a reservoir. A tank should have a dished bottom
that is fitted with a drain plug at its lowest point; a plug fitting should
be flushed with the inside of a tank to allow for full drainage. A reservoir
should have a sight gauge or dipstick for checking the oil level to prevent
damage from lubrication loss. An element in a filter in a return line will require
regular changing. When a reservoir is pressurized by compressed air, moisture
can become a maintenance problem. A tank should have a water trap for moisture
removal
4. Strainers
and Filters
4-1. Strainers and
Filters.
To keep hydraulic components performing
correctly, the hydraulic liquid must be kept as clean as possible. Foreign matter
and tiny metal particles from normal wear of valves, pumps, and other components
are going to enter a system. Strainers, filters, and magnetic plugs are used
to remove foreign particles from a hydraulic liquid and are effective as safeguards
against contamination.
a. Strainers. A strainer is the primary
filtering system that removes large particles of foreign matter from a hydraulic
liquid. Even though its screening action is not as good as a filter's, a strainer
offer less resistance to flow.
b. Filters. A filter removes small
foreign particles from a hydraulic fluid and is most effective as a safeguard
against contaminates. They are classified as full flow or proportional flow.
(1) Full-Flow Filter . In a full-flow
filter, all the fluid entering a unit passes through a filtering element. Although
a full-flow type provides a more positive filtering action, it offers greater
resistance to flow, particularly when it becomes dirty.
(2) Proportional-Flow Filters This
filter operates on the venturi principle in which a tube has a narrowing throat
(venturi) to increase the velocity of fluid flowing through it. Flow through
a venturi throat causes a pressure drop at the narrowest point. This pressure
decrease causes a sucking action that draws a portion of a liquid down around
a cartridge through a filter element and up into a venturi throat.
4-2. Filtering Material
and Elements.
The general classes of filter materials
are mechanical, absorbent inactive, and absorbent active.
Mechanical filters contain closely
woven metal screens or discs. They generally remove only fairly coarse particles.
Absorbent inactive filters, such
as cotton, wood pulp, yarn, cloth, or resin, remove much smaller particles;
some remove water and water-soluble contaminants. The elements often are treated
to make them sticky to attract the contaminants found in hydraulic oil.
Absorbent active materials, such
as charcoal and Fuller's Earth (a clay like material of very fine particles
used in the purification of mineral or vegetable-base oils), are not recommended
for hydraulic systems.
The three basic types of filter
elements are surface, edge, and depth.
A surface-type element is made of
closely woven fabric or treated paper. Oil flows through the pores of the filter
material, and the contaminants are stopped.
An edge-type filter is made up of paper or metal discs; oil flows through the
spaces between the discs. The fineness of the filtration is determined by the
closeness of the discs.
A depth-type element is made up of thick layers of cotton, felt, or other fibers.
4-3. Filter selection
The degree of filtering and filter
size are based on many different criteria, so that generalization is seldom
possible. The most important factors to be considered are as follows:
- Operational environment: How serious
would the consequences be if the system failed because of dirt?
- Oil quantity: Would there be a
few litres or several hundred litres in the system? Is it an expensive or
a cheap oil?
- Operational down time: What would
it cost per hour/day if the system shut down? How important is this factor?
- Dirt sensitivity: How dirt-sensitive
are the components? What degree of filtering is recommended by the component
manufacturers?
If you answer these questions
about a 4x4 hydraulic steering system, you can see that high quality filtration
of your full hydraulic steering system is an absolute must.
5. Plumbing / Lines
5-1. Types of Circulatory
Systems.
Pipes and fittings, with their necessary
seals, make up a circulatory system of liquid-powered equipment. Properly selecting
and installing these components are very important. If improperly selected or
installed, the result would be serious power loss or harmful liquid contamination.
The following is a list of some of the basic requirements of a circulatory system:
- Lines must be strong enough to
contain s liquid at s desired working pressure and the surges in pressure
that may develop in s system.
- Lines must be strong enough to
support the components that are mounted on them.
- Terminal fittings must be at
all junctions where parts must be removed for repair or replacement.
- Line supports must be capable
of damping the shock caused by pressure surges.
- Lines should have smooth interiors
to reduce turbulent flow.
- Lines must have the correct size
for the required liquid flow.
- Lines must be kept clean by regular
flushing or purging.
- Sources of contaminants must
be eliminated.
The three common types of lines in
liquid-powered systems are pipes, tubing, and flexible hose, which are also
referred to as rigid, semi rigid, and flexible line.
a. Tubing. The two types of tubing
used for hydraulic lines are seamless and electric welded. Both are suitable
for hydraulic systems. Seamless tubing is made in larger sizes than tubing that
is electric welded. Seamless tubing is flared and fitted with threaded compression
fittings. Tubing bends easily, so fewer pieces and fittings are required. Unlike
pipe, tubing can be cut and flared and fitted in the field. Generally, tubing
makes a neater, less costly, lower-maintenance system with fewer flow restrictions
and less chances of leakage. Knowing the flow, type of fluid, fluid velocity,
and system pressure will help determine the type of tubing to use. (Nominal
dimensions of tubing are given as fractions in inches or as dash numbers. A
dash number represents a tube’s outside diameter [OD] in sixteenths of
an inch.) A system’s pressure determines the thickness of the various
tubing walls. Tubing is commonly used in automotive braking systems.
b. Piping. You can use piping that
is threaded with screwed fittings with diameters up to 1 1/4 inches and pressures
of up to 1,000 psi. Where pressures will exceed 1,000 psi and required diameters
are over 1 1/4 inches, piping with welded, flanged connections and socket-welded
size are specified by nominal inside diameter (ID) dimensions. The thread remains
the same for any given pipe size regardless of wall thickness. Piping is used
economically in larger-sized hydraulic systems where large flow is carried.
It is particularly suited for long, permanent straight lines. Piping is taper-threaded
on its OD into a tapped hole or fitting. However, it cannot be bent. Instead,
fittings are used wherever a joint is required. This results in additional costs
and an increased chance of leakage. Piping is of no use to us as hydraulic
line in our 4x4s.
c. Flexible Hosing. When flexibility
is necessary in liquid-powered systems, use hose. Examples would be connections
to units that move while in operation to units that are attached to a hinged
portion of the equipment or are in locations that are subjected to severe vibration.
Flexible hose is usually used to connect a pump to a system. The vibration that
is set up by an operating pump would ultimately cause rigid tubing to fail. A 4x4 Hydraulic Steering System will most likely be exclusively plumbed
with flexible hose.
When installing flexible hose, do
not twist it. Doing so reduces its lift and may cause its fittings to loosen.
An identification stripe that runs along the hose length should not spiral,
which would indicate twisting. Protect flexible hose from chafing by wrapping
it lightly with tape, when necessary. The minimum bend radius for flexible hose
varies according to its size and construction and the pressure under which a
system will operate. Consult the applicable publications that contain the tables
and graphs which show the minimum bend radii for the different types of installations.
Bends that are too sharp will reduce the bursting pressure of flexible hose
considerably below its rated value. Install flexible hose so that it will be
subjected to a minimum of flexing during operation. Never stretch hose tightly
between two fittings. When under pressure, flexible hose contracts in length
and expands in diameter.
Keep the lines as short and free
of bends as possible.
Install all the lines so you can
remove them without dismantling a circuit’s components or without bending
or springing them to a bad angle. Add supports to the lines at frequent intervals
to minimize vibration or movement; never weld the lines to the supports. Since
flexible hose has a tendency to shorten when subjected to pressure, allow enough
slack to compensate for this problem.
5-2. Sizing hydraulic
lines.
The size of tubing or flexible hose
required in a given hydraulic system depends on:
- max. system pressure
- max. oil flow
- length of pipe system
- environmental conditions
Pressure drop must be as small as
possible. Remember that when the internal diameter is doubled, the flow area
of the pipe is quadrupled.
In order to calculate the exact size
required for your lines, you need a nomogram like this: |
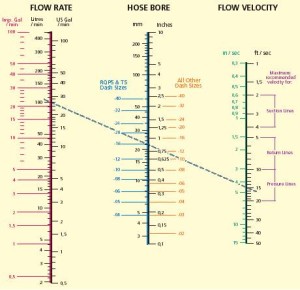 |
Hydraulic line
size selection nomogram.
Click on pic to access full
nomogram in .pdf format, perfect for printing and using, complete with
instructions and examples. |
Use of the nomogram to determine
line size requires knowledge of 2 variables - the flow rate of the system (likely
determined by the pump's rated capacity - for example 5 gpm) in gallons per
minute. With that knowledge, one then only needs to know whether the line is
to be used as suction line, pressure line or return line. This is because the
second variable required to use the nomogram is flow velocity, which is based
on whether the line is suction, return, or pressure. The recommended flow velocity
for the different line uses are as follows (also represented by dashed regions
on the nomogram):
- Suction lines 2-4 ft/s
- Return lines 5-10 ft/s
- Pressure lines 10-20 ft/s
Once the flow rate in gpm and flow
velocity in ft/sec are known, simply draw a straight line between the 2 values
and where it crosses the middle diagram, read off the required line size.
5-3. Tubing Do’s
And Don’ts.
- Don’t take heavy cuts on
thin wall tubing with a tubing cutter.
- Use light cuts to prevent deformation
of the tube end. If the tube end is out of round, a greater possibility of
a poor connection exists.
- Ream tubing only for removal of
burrs. DO NOT over ream tubing as it can weaken the connection.
- Do not allow chips to accumulate
in the tubing. They can be difficult to remove after bending.
- Bend tubing instead of cutting
and using a fitting. This reduces pressure drop and minimizes system losses.
- The minimum radius of a tubing
bend should be at least three times the inside diameter of the tube. Larger
bends are preferred.
*** The following EXCELLENT information
on hydraulic hoses are pdf files from Ryco
Hydraulics. They are excellent, and should be read by all ****
5-4.
Hose Selection and Maintenance
5-5.
Safety guide for selection and use of Hose and fittings
5-6.
Hose Assembly and Installation Guide
5-7.
Circulatory Systems maximum temperature and working pressures
6. Fittings and Connectors
6-1. Fittings and Connectors.
Many different types of connectors
are available for fluid-powered systems. The type that you will use will depend
on the type of circulatory system (pipe, tubing, or flexible hose), the fluid
medium, and the maximum operating pressure of a system. Some of the most common
types of connectors are described below:
a. Threaded Connectors. Threaded
connectors are used in some low-pressure liquid powered systems. They are usually
made of steel, copper, or brass, in a variety of designs. Standard pipe threads
are tapered slightly to ensure tight connections. To prevent seizing (threads
sticking), apply a pipe-thread compound to the threads. Keep the two end threads
free of the compound so that it will not contaminate the fluid. Pipe compound,
when improperly applied, may get inside the lines and harm the pumps and the
control equipment.
b. Flared Connectors. The common
connectors used in circulatory systems consist of tube lines. These connectors
provide safe, strong, dependable connections without having to thread, weld,
or solder the tubing. The most common example being the standard automotive
double-flared hydraulic brake lines. A connector consists of a fitting,
a sleeve, and a nut. Tubing used with flared connectors must be flared before
being assembled. A nut fits over a sleeve and, when tightened, draws the sleeve
and tubing flare tightly against a male fitting to form a seal. A male fitting
has a cone-shaped surface with the same angle as the inside of a flare. A sleeve
supports the tube so that vibration does not concentrate at the edge of a flare
but that it does distribute the shearing action over a wider area for added
strength. Tighten the tubing nuts with a torque wrench to the value specified
in applicable regulations. If an aluminium alloy flared connector leaks after
tightening to the specified torque, do not tighten it further. Disassemble the
leaking connector and correct the fault. If a steel connector leaks, you may
tighten it 1/6 turn beyond the specified torque in an attempt to stop the leak.
c. Hose couplings. Hose Couplings
can be broadly divided into two types:
- Field Attachable Couplings. Attached
to the hose using commonly available hand tools. Push On Hose Couplings and
Suction and Return Hose Couplings are often classed as Field Attachable couplings. However, field attachable high pressure hose couplings are commonly available.
I use them in my hydraulic steering system. They have 2 distinct advantages:
- When designing and assembling
the system, you do not need to measure precisely for lines before everything
is mounted in final position. You can buy the fittings and a length of
hose, and make your own lines when everything is in place. This keeps
the lines neater and prevents you from having to measure at the end and
return to the hydraulic supplier for exact fit crimp-on lines
- It is easy to carry a
few fittings and a length of hose as spares that can be trimmed to fit
any of the lines, and you can attach the fittings in the field. This prevents
you from having to carry a spare of each hose.
- Crimp, or Swage Couplings. Permanently
attached to the hose using a crimping or swaging machine.
|
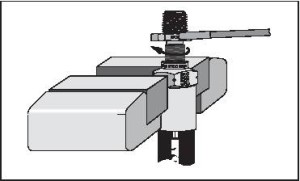 |
A field attachable
fitting that can be assembled onto the hose with only a vise and hand tools. |
|
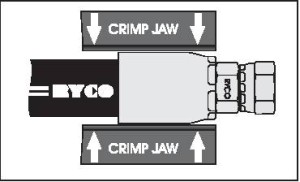 |
A crimp-on fitting that
requires a special crimping machine to assemble t onto the hydraulic hose. |
6-2. Coupling / Fitting
data
The following pdf files from Ryco
Hydraulics. include all you would ever need to know about various hydraulic
couplings (fittings)
7. Fluid
7-1. Fluid basics
The oil in a hydraulic system must
first and foremost transfer energy, but the moving parts in components must
also be lubricated to reduce friction and consequent heat generation. Additionally,
the oil must lead dirt particles and friction heat away from the system and
protect against corrosion.
Oil requirements include:
- good lubricating properties
- good wear properties
- suitable viscosity
- good corrosion inhibitor
- good anti-aeration properties
- reliable air separation
- good water separation Motor oil
Motor oils and most transmission
oils contain self-cleaning additives. These are a disadvantage in hydraulic
systems. For example, water condensed from the oil cannot be drained off; it
forms an emulsion with the oil. This in turn leads to filters becoming clogged
too quickly.
There is evidence that more than
70% of all problems with hydraulic systems can be traced directly to the condition
of the oil.
Normally an oil operating temperature
of 86°F- 140°F (30-60°C) ought to be aimed at since the life of
hydraulic oil is strongly dependent on its operating temperature. The rule-of
thumb is that the useful life of an oil is halved for every 4.4°F (8°C)
the temperature rises above 140°F (60°C). That is to say, at 194°F
(90°C) the life of the oil is only about 10% of its life at 140°F (60°C).
The reason for this is oxidation. At atmospheric pressure, all oils contain
a little less than 0.03 gal (0.1 litres) of air per 0.264 gal (litre) of oil.
Therefore, in practice, oxygen is always present and it reacts with the hydrocarbons
making up the oil. Gradually, as oxidation increases, the oil becomes darker
in colour and its' viscosity rises. Finally, the products of oxidation can no
longer be dissolved in the oil, but instead settle everywhere in the system
as a brown sticky layer. This will cause sticking valves and high friction in
ball bearings, valve spools and pump pistons. Oxidation also produces corrosive
acids. The oxidation process begins gradually, but at a certain stage the oxidation
rate suddenly rises and the viscosity rises. The resulting increase in operating
temperature accelerates the oxidation process even more and soon the oil becomes
quite unusable as a hydraulic oil because of deposits, high viscosity and accumulated
acids. It therefore pays to take care of the oil. |
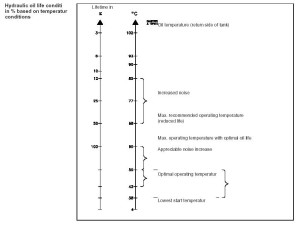 |
Hydraulic oil life conditions. |
|
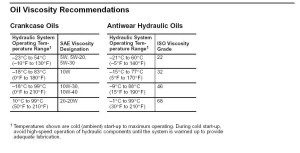 |
Oil viscosity recommendations. |
7-2. Hydraulic Fluid
And Temperature Recommendations For Industrial Machinery
a. General Data
Oil in hydraulic systems performs
the dual function of lubrication and transmission of power. It constitutes a
vital factor in a hydraulic system, and careful selection should be made with
the assistance of a reputable supplier. Proper selection of oil assures satisfactory
life and operation of the system components with particular emphasis on hydraulic
pumps and motors. Generally, oil selected for use with pumps and motors are
acceptable for use with valves. Critical servo valves may need special consideration.
Some of the factors especially important in the selection of oil for use in
an industrial hydraulic system are:
- The oil must contain the necessary
additives to ensure high anti wear characteristics. Not all hydraulic oils
contain these in sufficient amounts.
- The oil must have proper viscosity
to maintain adequate sealing and lubricating quality at the expected operating
temperature of the hydraulic system.
- The oil must have rust and oxidation
inhibitors for satisfactory system operation.
Two specific types of oil meet the
requirements of modern industrial hydraulic systems:
- Anti wear type industrial hydraulic
oils. A new generation of industrial hydraulic oils containing adequate quantities
of anti wear compound is recommended by Vickers for general hydraulic service.
- Automotive type crankcase oils
having API letter designation “SE”, “SF”, “SG”,
“SH”, per SAE J183. The above classes of oils in the 10W and 20-20W
SAE viscosity ranges are for severe hydraulic service where there is little
or no water present. The only adverse effect is that the “detergent”
additive tends to hold water in a tight emulsion and prevents separation of
water, even on long time standing. Automotive type crankcase oils generally
exhibit poorer shear stability which could result in some loss of viscosity
during their service life. More shear stable multiple viscosity industrial
grade hydraulic fluids will provide improved viscosity control.
b. Viscosity
Viscosity is the measure of the fluid’s
resistance to flow.
Very high viscosities at start-up
temperatures can cause noise and cavitational damage to pumps. Continuous operation
at moderately high viscosities will tend to hold air in suspension in the oil
as well as generate higher operating temperatures. This can cause noise and
early failure of pumps, motors and erosion of valves. Low viscosities result
in decreased system efficiency and impairment of dynamic lubrication which causes
wear.
c. Temperature
To obtain optimum service life from
both the oil and the hydraulic system, operate between 49°C (120°F)
and 54°C (130°F). The maximum oil temperature normally recommended is
66°C (150°F).
d. Cleanliness
Thorough precautions should always
be observed to ensure that the hydraulic system is clean.
- Clean (flush) entire system to
remove paint, metal chips, welding shot, lint, etc.
- Filter each change of oil to
prevent introduction of contaminant into the system.
- Provide continuous oil filtration
to remove sludge and products of wear and corrosion generated during the life
of the system.
- Provide continuous protection
of system from entry of airborne contamination by proper filtration of air
through breathers.
- During usage, proper oil filling
of reservoir and servicing of filters, breathers, reservoirs, etc. cannot
be over emphasized.
e. Synthetic Fluid Type - Phosphate
Ester
Phosphate ester type fluids are manufactured
from chemically produced esters. These types of fluids require fluorocarbon
seals. Consult your fluid supplier for the types of seals which are compatible.
7-3. Hydraulic Fluid
And Temperature Recommendations For Mobile Hydraulic Systems
The oil in a hydraulic system serves
as the power transmission medium. It is also the system’s lubricant and
coolant. The selection of proper oil is a requirement for satisfactory system
performance and life.
Important Factors In Selecting An
Oil
Additives
Hydraulic fluids contain a number
of additive agents which materially improve various characteristics of oil for
hydraulic systems. These additives are selected to reduce wear, increase chemical
stability, inhibit corrosion and depress the pour point.
Anti-wear
Pump performance and reliability
are directly affected by the anti-wear additive formulation contained in the
oil. Oils providing a high level of anti-wear protection are recommended for
optimum performance and long life.
Viscosity
Viscosity is the measure of the fluid’s
resistance to flow. The oil selected must have proper viscosity to maintain
an adequate lubricating film at system operating temperature. In addition to
dynamic lubricating properties, oil must have sufficient body to provide an
adequate sealing effect between working parts of pumps, valves, cylinders and
motors, but not enough to cause pump cavitation or sluggish valve action. Optimum
operating viscosity of the oil should be between 16 cSt (80 SUS) and 40 cSt
(180 SUS).
8. Seals
Seals are packing materials used
to prevent leaks in liquid-powered systems. A seal is any gasket, packing, seal
ring, or other part designed specifically for sealing. Sealing applications
are usually static or dynamic, depending if the parts being sealed move in relation
to one another. Sealing keeps the hydraulic oil flowing in passages to hold
pressure and keep foreign materials from getting into the hydraulic passages.
To prevent leakage, use a positive sealing method, which involves using actual
sealing parts or materials. In most hydraulic components, you can use non-positive
sealing (leakage for lubrication) by fitting the parts closely together. The
strength of an oil film that the parts slide against provides an effective seal.
Types of seals include:
a. Static Seals.
Pipe-threaded seals, seal rings used
with tube fittings, valve end-cap seals, and other seals on nonmoving parts
are static seals. Mounting gaskets and seals are static, as are seals used in
making connections between components. A static seal or gasket is placed between
parts that do not move in relation to each other.
b. Dynamic Seals.
In a dynamic sealing application,
either a reciprocating or a rotary motion occurs between the two parts being
sealed; for example, a piston-to-barrel seal in a hydraulic cylinder or a drive-shaft
seal in a pump or motor.
c. O-ring Seals.
An O-ring is a positive seal that
is used in static and dynamic applications. It has replaced the flat gasket
on hydraulic equipment. When being installed, an O-ring is squeezed at the top
and bottom in its groove and against the mating part. It is capable of sealing
very high pressure. Pressure forces the seal against the side of its groove,
and the result is a positive seal on three sides. Dynamic applications of an
O-ring are usually limited to reciprocating parts that have relatively short
motion.
Preventing Seal Deterioration
Premature deterioration of the seal
can result from excessive fluid temperature. A good guide is that seal life
is halved by every 20°F. rise. The cure: Incorporate sufficient heat exchangers
to keep fluid temperatures below 150°F.
Another factor may be compatibility
of the fluid with the seal material where special fluids are used. If a doubt
arises, contact your Vickers representative. The following brief review of seal
materials may be helpful.
- Nitrile (Buna N) is the most widely
used and best all around elastomer for petroleum (mineral) oils, fuel and
fire-resistant fluids – with the exception of phosphate esters.
- Fluoroelastomer (Viton or Fluorel)
costs more than Nitrile, can be used instead of Nitrile but has the added
advantage of longer life when fluid temperatures consistently run above 150°F.
It can be used with phosphate ester fluids (except Skydrol).
- Polyurethane shows extrusion and
abrasion resistance superior to Nitrile in petroleum oils, fuel and silicate
esters, but deteriorates if contaminated with hot water.
9. Pumps
Hydraulic pumps convert mechanical
energy from a prime mover (engine or electric motor) into hydraulic (pressure)
energy. The pressure energy is used then to operate an actuator. Pumps push
on a hydraulic fluid and create flow.
9-1. Pump Classifications.
All pumps create flow. They operate
on the displacement principle. Fluid is taken in and displaced to another point.
Pumps that discharge liquid in a continuous flow are non-positive-displacement
type. Pumps that discharge volumes of liquid separated by periods of no discharge
are positive-displacement type.
a. Non-positive-Displacement Pumps.
With this pump, the volume of liquid delivered for each cycle depends on the
resistance offered to flow. A pump produces a force on the liquid that is constant
for each particular speed of the pump. Resistance in a discharge line produces
a force in the opposite direction. When these forces are equal, a liquid is
in a state of equilibrium and does not flow. If the outlet of a non-positive-displacement
pump is completely closed, the discharge pressure will rise to the maximum for
a pump operating at a maximum speed. A pump will churn a liquid and produce
heat. Automotive power steering pumps are non-positive-displacement type
pumps.
b. Positive-Displacement Pumps. With
this pump, a definite volume of liquid is delivered for each cycle of pump operation,
regardless of resistance, as long as the capacity of the power unit driving
a pump is not exceeded. If an outlet is completely closed, either the unit driving
a pump will stall or something will break. Therefore, a positive-displacement-type
pump requires a pressure regulator or pressure-relief valve in the system. As
the fluid flows out of the other side, it is sealed against backup. This sealing
is the positive part of displacement. Without it, the fluid could never overcome
the resistance of the other parts in a system.
c. Characteristics. The three contrasting
characteristics in the operation of positive- and non-positive-displacement pumps
are as follows:
- Non-positive-displacement pumps
provide a smooth, continuous flow; positive- displacement pumps have a pulse
with each stroke or each time a pumping chamber opens to an outlet port.
- Pressure can reduce a non-positive
pump’s delivery. High outlet pressure can stop any output; the liquid
simply recirculates inside the pump. In a positive displacement pump, pressure
affects the output only to the extent that it increases internal leakage.
- Non-positive-displacement pumps,
with the inlets and outlets connected hydraulically, cannot create a vacuum
sufficient for self-priming; they must be started with the inlet line full
of liquid and free of air. Positive-displacement pumps often are self-priming
when started properly.
|
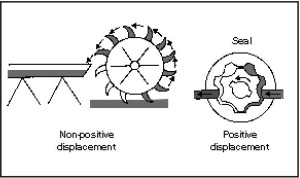 |
|
9-2. Pump Performance.
Pumps are usually rated according
to their volumetric output and pressure. Volumetric output (delivery rate or
capacity) is the amount of liquid that a pump can deliver at its outlet port
per unit of time at a given drive speed, usually expressed in GPM or cubic inches
per minute. Because changes in pump drive affect volumetric output, pumps are
sometimes rated according to displacement, that is the amount of liquid that
they can deliver per cycle or cubic inches per revolution.
Pressure is the force per unit area
of a liquid, usually expressed in psi. (Most of the pressure in the hydraulic
systems covered in this manual is created by resistance to flow.) Resistance
is usually caused by a restriction or obstruction in a path or flow. The pressure
developed in a system has an effect on the volumetric output of the pump supplying
flow to a system. As pressure increases, volumetric output decreases. This drop
in output is caused by an increase in internal leakage (slippage) from a pump's
outlet side to its inlet side. Slippage is a measure of a pump’s efficiency
and usually is expressed in percent. Some pumps have greater internal slippage
than others; some pumps are rated in terms of volumetric output at a given pressure.
3-3. Displacement. Displacement is the amount of liquid transferred from a pump’s
inlet to its outlet in one revolution or cycle. In a rotary pump, displacement
is expressed in cubic inches per revolution and in a reciprocating pump in cubic
inches per cycle. If a pump has more than one pumping chamber, its displacement
is equal to the displacement of one chamber multiplied by the number of chambers.
Displacement is either fixed or variable.
a. Fixed-Displacement Pump. In this
pump, the GPM output can be changed only by varying the drive speed. The pump
can be used in an open-center system—a pump’s output has a free-flow
path back to a reservoir in the neutral condition of a circuit. Automotive
power steering pumps are fixed-displacement pumps.
b. Variable-Displacement Pump. In
this pump, pumping-chamber sizes can be changed. The GPM delivery can be changed
by moving the displacement control, changing the drive speed, or doing both.
The pump can be used in a closed-center system—a pump continues to operate
against a load in the neutral condition.
9-3. Slippage.
Slippage is oil leaking from a pressure
outlet to a low-pressure area or back to an inlet. A drain passage allows leaking
oil to return to an inlet or a reservoir. Some slippage is designed into pumps
for lubrication purposes. Slippage will increase with pressure and as a pump
begins to wear. Oil flow through a given orifice size depends on the pressure
drip. An internal leakage path is the same as an orifice. Therefore, if pressure
increases, more flow will occur through a leakage path and less from an outlet
port. Any increase in slippage is a loss of efficiency.
9-4. Designs.
In most rotary hydraulic pumps the
design is such that the pumping chambers increase in size at the inlet, thereby
creating a vacuum. The chambers then decrease in size at the outlet to push
fluid into a system. The vacuum at the inlet is used to create a pressure difference
so that fluid will flow from a reservoir to a pump. However, in many systems,
an inlet is charged or supercharged; that is, a positive pressure rather than
a vacuum is created by a pressurized reservoir, a head of fluid above the inlet,
or even a low-pressure-charging pump. The essentials of any hydraulic pump are—
- A low-pressure inlet port, which
carries fluid from the reservoir.
- A high-pressure outlet port connected
to the pressure line.
- Pumping chamber(s) to carry a
fluid from the inlet to the outlet port.
- A mechanical means for activating
the pumping chamber(s).
Pumps may be classified according
to the specific design used to create the flow of a liquid. Most hydraulic pumps
are either centrifugal, rotary, or reciprocating.
a. Centrifugal Pump. This pump generally
is used where a large volume of flow is required at relatively low pressures.
It can be connected in series by feeding an outlet of one pump into an inlet
of another. With this arrangement, the pumps can develop flow against high pressures.
A centrifugal pump is a non-positive-displacement pump,
b. Rotary Pump. In this positive
displacement- type pump, a rotary motion carries a liquid from a pump’s
inlet to its outlet. A rotary pump is usually classified according to the type
of element that actually transmits a liquid, that is, a gear-, vane-, or piston-type
rotary pump.
c. Reciprocating Pump. A reciprocating
pump depends on a reciprocating motion to transmit a liquid from a pump’s
inlet to its outlet. It consists of a cylinder that houses a reciprocating piston.
9-5. Types of Pumps.
a. Gear Pumps. Gear pumps are external,
internal, or lobe types. |
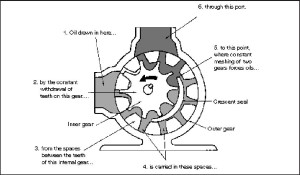 |
Internal Gear Pump. |
|
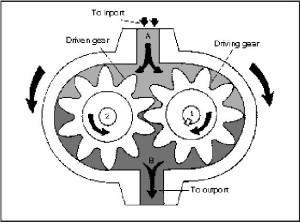 |
External Gear Pump. |
b. Vane Pumps. In a vane-type pump,
a slotted rotor splined to a drive shaft rotates between closely fitted side
plates that are inside of an elliptical- or circular shaped ring. Polished,
hardened vanes slide in and out of the rotor slots and follow the ring contour
by centrifugal force. Pumping chambers are formed between succeeding vanes,
carrying oil from the inlet to the outlet. A partial vacuum is created at the
inlet as the space between vanes increases. The oil is squeezed out at the outlet
as the pumping chamber’s size decreases.
Balanced design vane pumps all are
fixed displacement. An unbalanced design can be built in either a fixed- or
variable-displacement pump. Vane pumps have good efficiency and durability if
operated in a clean system using the correct oil. They cover the low to medium-high
pressure, capacity, and speed ranges. Package size in relation to output is
small. A vane pump is generally quiet, but will whine at high speeds. |
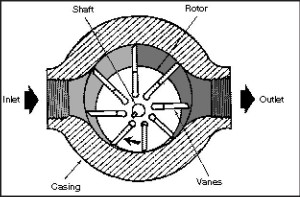 |
Unbalanced Vane Pump. |
9-6. Pump Operation.
The following paragraphs address
some of the problems that could occur when a pump is operating:
a. Overloading. One risk of overloading
is the danger of excess torque on a drive shaft.
b. Excess Speed. Running a pump at
too high a speed causes loss of lubrication, which can cause early failure.
If a needed delivery requires a higher drive speed than a pump's rating, use
a higher displacement pump. Excess speed also runs a risk of damage from cavitation.
c. Cavitation. Cavitation occurs
where available fluid does not fill an existing space. It often occurs in a
pump’s inlet when conditions are not right to supply enough oil to keep
an inlet flooded. Cavitation causes the metal in an inlet to erode and the hydraulic
oil to deteriorate quicker. Cavitation can occur if there is too much resistance
in an inlet’s line, if a reservoir’s oil level is too far below
the inlet, or if an oil’s viscosity is too high. It can also occur if
there is a vacuum or even a slight positive pressure at the inlet. A badly cavitating
pump has oil bubbles exploding in the void. The only way to be sure a pump is
not cavitating is to check the inlet with a vacuum gauge. To prevent cavitation,
keep the inlet clean and free of obstructions by using the correct length of
an inlet’s line with minimum bends. Another method is to charge an inlet.
The easiest way to do this is to flood it by locating the reservoir above the
pump’s inlet. If this is not possible and you cannot create good inlet
conditions, use a pressurized reservoir.
Cavitation happens when the pressure
in the fluid falls below the vapour pressure of THAT fluid at THAT temperature.
In other words, when the physical conditions are right - a "change of state"
spontaneously occurs, and the liquid turns to vapour, creating a vapour pocket
or bubble that will then collapse very rapidly as it is exposed to higher surrounding
pressure. The individual bubbles formed and then collapsing are very small,
even microscopic, but they from and collapse very quickly and with great force
and in great numbers.
It's roughly analogous to condensation
forming on your cold drink glass on a warm summer day. You have H2O, which can
be solid (ice), liquid (water) or gas (water vapour ). Warm air can hold more
water in suspension in vapour form than cold air. So if you take warm air full
of water vapour and cool it, (like what happens when that warm, vapour laden
air comes into contact with your cold drink glass) the water vapour will spontaneously
change state from gas to liquid, and condensation forms (and runs down the glass
and makes ring on the table if you didn't use a coaster!)
So - in our pump (or any other
part of the system for that matter - cavitation is not limited to the pump)
if a pressure drop occurs (perhaps because of venturi effect or velocity or under
changing conditions of temp and pressure) and the pressure drop occurs to a
point below the vapour pressure of the fluid (whatever it may be) - voila -
state change, vapour "bubble" and then when that vapour bubble encounters
a region of higher pressure - it collapses with a "pop" and that's
the noise you hear.
d. Operating Problems. Pressure loss,
slow operation, no delivery, and noise are common operating problems in a pump.
(1) Pressure Loss. Pressure loss
means that there is a high leakage path in a system. A badly worn pump could
cause pressure loss. A pump will lose its efficiency gradually. The actuator
speed slows down as a pump wears. However, pressure loss is more often caused
by leaks somewhere else in a system (relief valve, cylinders, motors).
(2) Slow Operation. This can be
caused by a worn pump or by a partial oil leak in a system. Pressure will not
drop, however, if a load moves at all. Therefore, hp is still being used and
is being converted into heat at a leakage point. To find this point, feel the
components for unusual heat.
(3) No Delivery. If oil is not being
pumped, a pump—
- Could be assembled incorrectly.
- Could be driven in the wrong
direction.
- Has not been primed. The reasons
for no prime are usually improper start-up, inlet restrictions, or low oil
level in a reservoir.
- Has a broken drive shaft.
(4) Noise. If you hear any unusual
noise, shut down a pump immediately. Cavitation noise is caused by a restriction
in an inlet line, a dirty inlet filter, or too high a drive speed. Air in a
system also causes noise. Air will severely damage a pump because it will not
have enough lubrication. This can occur from low oil in a reservoir, a loose
connection in an inlet, a leaking shaft seal, or no oil in a pump before starting.
Also, noise can be caused by worn or damaged parts, which will spread harmful
particles through a system, causing more damage if an operation continues.
10. Hydraulic Actuators
A hydraulic actuator receives pressure
energy and converts it to mechanical force and motion. An actuator can be linear
or rotary. A linear actuator gives force and motion outputs in a straight line.
It is more commonly called a cylinder but is also referred to as a ram, reciprocating
motor, or linear motor. A rotary actuator produces torque and rotating motion.
It is more commonly called a hydraulic motor or motor.
10-1. Cylinders.
An actuating cylinder is a device
that converts fluid power to linear, or straight line, force and motion. Since
linear motion is a back-and-forth motion along a straight line, this type of
actuator is sometimes referred to as a reciprocating, or linear, motor. The
cylinder consists of a ram or piston operating within a cylindrical bore. Actuating
cylinders may be installed so that the cylinder is anchored to a stationary
structure and the ram or piston is attached to the mechanism to be operated,
or the piston or ram may be anchored to the stationary structure and the cylinder
attached to the mechanism to be operated. Actuating cylinders for pneumatic
and hydraulic systems are similar in design and operation. Some of the variations
of ram- and piston-type actuating cylinders are described in the following paragraphs.
RAM-TYPE CYLINDERS
The terms ram and piston are often used interchangeably. However, a ram-type
cylinder is usually considered one in which the cross-sectional area of the
piston rod is more than one-half the cross-sectional area of the movable element.
In most actuating cylinders of this type, the rod and the movable element have
equal areas. This type of movable element is frequently referred to as a plunger.
The ram-type actuator is used primarily to push rather than to pull. Some applications
require simply a flat surface on the external part of the ram for pushing or
lifting the unit to be operated. Other applications require some mechanical
means of attachment, such as a clevis or eyebolt. The design of ram-type cylinders
varies in many other respects to satisfy the requirements of different applications.
Single-Acting Ram |
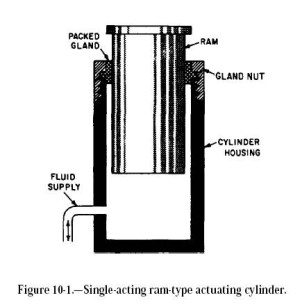 |
Single-Acting Ram. |
The single-acting ram (fig. 10-1)
applies force in only one direction. The fluid that is directed into the cylinder
displaces the ram and forces it outward, lifting the object placed on it. Since
there is no provision for retracting the ram by fluid power, when fluid pressure
is released, either the weight of the object or some mechanical means, such
as a spring, forces the ram back into the cylinder. This forces the fluid back
to the reservoir. The single-acting ram-type actuating cylinder is often used
in the hydraulic jack. The elevators used to move aircraft to and from the flight
deck and hangar deck on aircraft carriers also use cylinders of this type. In
these elevators, the cylinders are installed horizontally and operate the elevator
through a series of cables and sheaves. Fluid pressure forces the ram outward
and lifts the elevator. When fluid pressure is released from the ram, the weight
of the elevator forces the ram back into the cylinder. This, in turn, forces
the fluid back into the reservoir.
Double-Acting Ram |
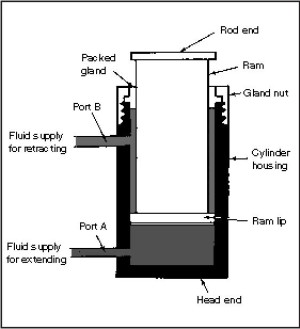 |
Double-Acting Ram. |
A double-acting ram-type cylinder
is illustrated in figure 10-2. In this cylinder, both strokes of the ram are
produced by pressurized fluid. There are two fluid ports, one at or near each
end of the cylinder. Fluid under pressure is directed to the closed end of the
cylinder to extend the ram and apply force. To retract the ram and reduce the
force, fluid is directed to the opposite end of the cylinder.
A four-way directional control valve
is normally used to control the double-acting ram. When the valve is positioned
to extend the ram, pressurized fluid enters port A (fig. 10-2), acts on the
bottom surface of the ram, and forces the ram outward. Fluid above the ram lip
is free to flow out of port B, through the control valve, and to the return
line in hydraulic systems or to the atmosphere in pneumatic systems. Normally,
the pressure of the fluid is the same for either stroke of the ram. Recall that
force is equal to pressure times area (F= PA). Notice the difference of the
areas upon which the pressure acts in figure 10-2. The pressure acts against
the large surface area on the bottom of the ram during the extension stroke,
during which time the ram applies force. Since the ram does not require a large
force during the retraction stroke, pressure acting on the small area on the
top surface of the ram lip provides the necessary force to retract the ram.
Telescoping Rams
Figure 10-3 shows a telescoping ram-type
actuating cylinder. A series of rams is nested in the telescoping assembly.
With the exception of the smallest ram, each ram is hollow and serves as the
cylinder housing for the next smaller ram. The ram assembly is contained in
the main cylinder assembly, which also provides the fluid ports. Although the
assembly requires a small space with all the rams retracted, the telescoping
action of the assembly provides a relatively long stroke when the rams are extended.
An excellent example of the application of this type of cylinder is in the dump
truck. It is used to lift the forward end of the truck bed and dump the load.
During the lifting operation, the greatest force is required for the initial
lifting of the load. |
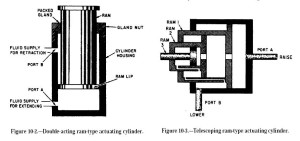 |
Telescoping ram-type
actuating cylinder. |
As the load is lifted and begins
to dump, the required force becomes less and less until the load is completely
dumped. During the raise cycle, pressurized fluid enters the cylinder through
port A (fig. 10-3) and acts on the bottom surface of all three rams. Ram 1 has
a larger surface area and, therefore, provides the greater force for the initial
load, As ram 1 reaches the end of its stroke and the required force is decreased,
ram 2 moves, providing the smaller force needed to continue raising the load.
When ram 2 completes its stroke, a still smaller force is required. Ram 3 then
moves outward to finish raising and dumping the load. Some telescoping ram-type
cylinders are of the single-acting type. Like the single-acting ram discussed
previously, these telescoping ram-type cylinders are retracted by gravity or
mechanical force. Some hydraulic jacks are equipped with telescoping rams. Such
jacks are used to lift vehicles with low clearances to the required height.
Other types of telescoping cylinders, like the one illustrated in figure 10-3,
are of the double acting type. In this type, fluid pressure is used for both
the extension and retraction strokes. A four way directional control valve is
commonly used to control the operation of the double-acting type. Note the small
passages in the walls of rams 1 and 2. They provide a path for fluid to flow
to and from the chambers above the lips of rams 2 and 3. During the extension
stroke, return fluid flows through these passages and out of the cylinder through
port B. It then flows through the directional control valve to the return line
or reservoir. To retract the rams, fluid under pressure is directed into the
cylinder through port B and acts against the top surface areas of all three
ram lips. This forces the rams to the retracted position. The displaced fluid
from the opposite side of the rams flows out of the cylinder through port A,
through the directional control valve to the return line or reservoir.
Dual Rams |
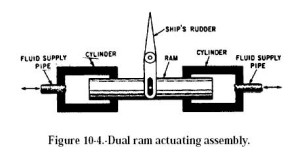 |
Dual Rams. |
A dual ram assembly consists of a
single ram with a cylinder at either end (fig. 10-4). Fluid can be directed
to either cylinder, forcing the ram to move in the opposite direction. The ram
is connected through mechanical linkage to the unit to be operated. A four-way
directional control valve is commonly used to operate the dual ram. When the
control valve is positioned to direct fluid under pressure to one of the cylinders
(let’s say the left one), the ram is forced to the right. This Figure
10-4.-Dual ram actuating assembly. action displaces the fluid in the opposite
cylinder. The displaced fluid flows back through the directional control valve
to the return line or reservoir in hydraulic systems or to the atmosphere in
pneumatic systems. Dual ram actuating assemblies are used in steering systems
of most ships. In some systems, one assembly is used to actuate the rudder in
either direction; while in other systems, two assemblies are used for the same
purpose.
PISTON-TYPE CYLINDERS
An actuating cylinder in which the
cross sectional area of the piston is less than one-half the cross-sectional
area of the movable element is referred to as a piston-type cylinder. This type
of cylinder is normally used for applications that require both push and pull
functions. The piston type cylinder is the most common type used in fluid power
systems. The essential parts of a piston-type cylinder are a cylindrical barrel,
a piston and rod, end caps, and suitable seals. The end caps are attached to
the ends of the barrel. These end caps usually contain the fluid ports. The
end cap on the rod end contains a hole for the piston rod to pass through. Suitable
seals are used between the hole and the piston rod to keep fluid from leaking
out and to keep dirt and other contaminants from entering the barrel. The opposite
end cap of most cylinders is provided with a fitting for securing the actuating
cylinder to some structure. This end cap is referred to as the anchor end cap.
The piston rod may extend through either or both ends of the cylinder. The extended
end of the rod is normally threaded so that some type of mechanical connector,
such as an eyebolt or a clevis, and a locknut can be attached. This threaded
connection of the rod and mechanical connector provides for adjustment between
the rod and the unit to be actuated. After the correct adjustment is made, the
locknut is tightened against the connector to prevent the connector from turning.
The other end of the connector is attached, either directly or through additional
mechanical linkage, to the unit to be actuated. In order to satisfy the many
requirements of fluid power systems, piston-type cylinders are available in
various designs.
Single-Acting Cylinder
The single-acting piston-type cylinder
is similar in design and operation to the single-acting ram-type cylinder. The
single-acting piston-type cylinder uses fluid pressure to provide the force
in one direction, and spring tension, gravity, compressed air, or nitrogen is
used to provide the force in the opposite direction. |
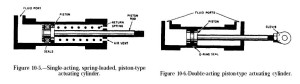 |
Single-acting,
spring-loaded, piston-type actuating cylinder. |
Figure 10-5 shows a single-acting,
spring-loaded, piston-type actuating cylinder. In this cylinder the spring is
located on the rod side of the piston. In some spring-loaded cylinders the spring
is located on the blank side, and the fluid port is on the rod side of the cylinder.
A three-way directional control valve is normally used to control the operation
of the single-acting piston-type cylinder. To extend the piston rod, fluid under
pressure is directed through the port into the cylinder (fig. 10-5). This pressure
acts on the surface area of the blank side of the piston and forces the piston
to the right. This action moves the rod to the right, through the end of the
cylinder, thus moving the actuated unit in one direction. During this action,
the spring is compressed between the rod side of the piston and the end of the
cylinder. The length of the stroke depends upon the physical limits within the
cylinder and the required movement of the actuated unit. To retract the piston
rod, the directional control valve is moved to the opposite working position,
which releases the pressure in the cylinder. The spring tension forces the piston
to the left, retracting the piston rod and moving the actuated unit in the opposite
direction. The fluid is free to flow from the cylinder through the port, back
through the control valve to the return line in hydraulic systems or to the
atmosphere in pneumatic systems. The end of the cylinder opposite the fluid
port is vented to the atmosphere. This prevents air from being trapped in this
area. Any trapped air would compress during the extension stroke, creating excess
pressure on the rod side of the piston. This would cause sluggish movement of
the piston and could eventually cause a complete lock, preventing the fluid
pressure from moving the piston. The spring-loaded cylinder is used in arresting
gear systems on some models of carrier aircraft. To raise (retract) the arresting
hook, fluid pressure is directed through the arresting hook control valve to
the rod side of the cylinder. This force moves the piston, which, through the
rod and mechanical linkage, retracts the arresting hook. The arresting hook
extends when fluid pressure is released from the rod side of the cylinder, allowing
the spring to expand. Leakage between the cylinder wall and piston is prevented
by adequate seals. The piston in figure 10-5 contains O-ring seals.
Double-Acting Cylinder
Most piston-type actuating cylinders
are double-acting, which means that fluid under pressure can be applied to either
side of the piston to apply force and provide movement. One design of the double-acting
cylinder is shown in figure 10-6. This cylinder contains one piston and piston
rod assembly. The stroke of the piston and piston rod assembly in either direction
is produced by fluid pressure. The two fluid ports, one near each end of the
cylinder, alternate as inlet and outlet ports, depending on the direction of
flow from the directional control valve. This actuator (fig. 10-6) is referred
to as an unbalanced actuating cylinder because there is a difference in the
effective working areas on the two sides of the piston. Therefore, this type
of cylinder is normally installed so that the blank side of the piston carries
the greater load; that is, the cylinder carries the greater load during the
piston rod extension stroke. A four-way directional control valve is normally
used to control the operation of this type of cylinder. The valve can be positioned
to direct fluid under pressure to either end of the cylinder and allow the displaced
fluid to flow from the opposite end of the cylinder through the control valve
to the return line in hydraulic systems or to the atmosphere in pneumatic systems. |
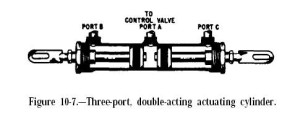 |
Three-port, double-acting cylinder. |
|
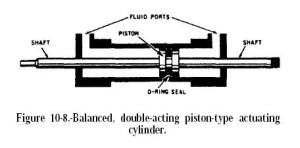 |
Balanced double-acting cylinder. |
There are applications where it is
necessary to move two mechanisms at the same time. In this case, double-acting
piston-type actuating cylinders of different designs are required. See figures
10-7 and 10-8. Figure 10-7 shows a three-port, double-acting piston-type actuating
cylinder. This actuator contains two pistons and piston rod assemblies. Fluid
is directed through port A by a four-way directional control valve and moves
the pistons outward, thus moving the mechanisms attached to the pistons’
rods. The fluid on the rod side of each piston is forced out of the cylinder
through ports B and C, which are connected by a common line to the directional
control valve. The displaced fluid then flows through the control valve to the
return line or to the atmosphere. When fluid under pressure is directed into
the cylinder through ports B and C, the two pistons move inward, also moving
the mechanisms attached to them. Fluid between the two pistons is free to flow
from the cylinder through port A and through the control valve to the return
line or to the atmosphere. The actuating cylinder shown in figure 10-8 is a
double-acting balanced type. The piston rod extends through the piston and out
through both ends of the cylinder. One or both ends of the Figure 10-8.-Balanced,
double-acting piston-type actuating cylinder. piston rod may be attached to
a mechanism to be operated. In either case, the cylinder provides equal areas
on each side of the piston. Therefore, the same amount of fluid and force is
used to move the piston a certain distance in either direction.
Tandem Cylinders |
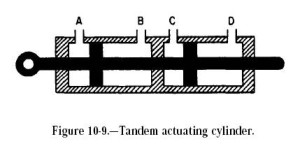 |
Tandem Cylinder. |
A tandem actuating cylinder consists
of two or more cylinders arranged one behind the other but designed as a single
unit (fig. 10-9). This type of actuating cylinder is used in applications that
require two or more independent systems; for example, power-operated flight
control systems in naval aircraft. The flow of fluid to and from the two chambers
of the tandem actuating cylinder is provided from two independent hydraulic
systems and is controlled by two sliding spool directional control valves. In
some applications, the control valves and the actuating cylinder are two separate
units. In some units, the pistons (lands) of the two sliding spools are machined
on one common shaft. In other applications, the valves and the actuator are
directly connected in one compact unit. Although the two control valves are
hydraulically independent, they are interconnected mechanically. In other units,
the two sliding spools are connected through mechanical linkages with a synchronizing
rod. In either case, the movement of the two sliding spools is synchronized,
thus equalizing the flow of fluid to and from the two chambers of the actuating
cylinder. Since the two control valves operate independently of each other as
far as hydraulic pressure is concerned, failure of either hydraulic system does
not render the actuator inoperative. Failure of one system does reduce the output
force by one-half; however, this force is sufficient to permit operation of
the actuator.
10-2. Cylinder Maintenance.
Hydraulic cylinders are compact and
relatively simple. The key points to watch are the seals and pivots. The following
lists service tips in maintaining cylinders:
- External Leakage. If a cylinder’s
end caps are leaking, tighten them. If the leaks still do not stop, replace
the gasket. If a cylinder leaks around a piston rod, replace the packing.
Make sure that a seal lip faces toward the pressure oil.
- Internal Leakage. Leakage past
the piston seals inside a cylinder can cause sluggish movement or settling
under load. Piston leakage can be caused by worn piston seals or rings or
scored cylinder walls. The latter may be caused by dirt and grit in the oil.
NOTE: When repairing a cylinder, replace all the seals and packings before
reassembly.
- Creeping Cylinder. If a cylinder
creeps when stopped in mid stroke, check for internal leakage. Another cause
could be a worn control valve.
- Sluggish Operation. Air in a
cylinder is the most common cause of sluggish action. Internal leakage in
a cylinder is another cause. If an action is sluggish when starting up a system,
but speeds up when a system is warm, check for oil of too high a viscosity
(see the machine's operating manual). If a cylinder is still sluggish after
these checks, test the whole circuit for worn components.
- Loose Mounting. Pivot points
and mounts may be loose. The bolts or pins may need to be tightened, or they
may be worn out. Too much slop or float in a cylinder’s mountings damages
the piston-rod seals. Periodically check all the cylinders for loose mountings.
- Misalignment. Piston rods must
work in-line at all times. If they are side-loaded, the piston rods will be
galled and the packings will be damaged, causing leaks. Eventually, the piston
rods may be bent or the welds broken.
- Lack of Lubrication. If a piston
rod has no lubrication, a rod packing could seize, which would result in an
erratic stroke, especially on single-acting cylinders.
- Abrasives on a Piston Rod. When
a piston rod extends, it can pick up dirt and other material. When it retracts,
it carries the grit into a cylinder, damaging a rod seal. For this reason,
rod wipers are often used at the rod end of a cylinder to clean the rod as
it retracts. Rubber boots are also used over the end of a cylinder in some
cases. Piston rods rusting is another problem. When storing cylinders, always
retract the piston rods to protect them. If you cannot retract them, coat
them with grease.
- Burrs on a Piston Rod. Exposed
piston rods can be damaged by impact with hard objects. If a smooth surface
of a rod is marred, a rod seal may be damaged. Clean the burrs on a rod immediately,
using crocus cloth. Some rods are chrome-plated to resist wear. Replace the
seals after restoring a rod surface.
- Air Vents. Single-acting cylinders
(except ram types) must have an air vent in the dry side of a cylinder. To
prevent dirt from getting in, use different filter devices. Most are self
cleaning, but inspect them periodically to ensure that they operate properly.
11. Valves
Valves are used in hydraulic systems
to control the operation of the actuators. Valves regulate pressure by creating
special pressure conditions and by controlling how much oil will flow in portions
of a circuit and where it will go. The three categories of hydraulic valves
are pressure-control, flow- (volume-) control, and directional-control. Some
valves have multiple functions, placing them into more than one category. Valves
are rated by their size, pressure capabilities, and pressure drop/flow.
Simple Valves: |
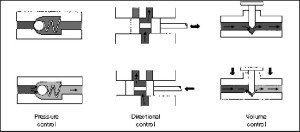 |
Simple Valves. |
11-1. Pressure-Control
Valves.
A pressure-control valve may limit
or regulate pressure, create a particular pressure condition required for control,
or cause actuators to operate in a specific order.
Most pressure-control valves are
classified as normally closed. This means that flow to a valve's inlet port
is blocked from an outlet port until there is enough pressure to cause an unbalanced
operation.
a. Relief Valves. Relief valves are
the most common type of pressure-control valves. The relief valves’ function
may vary, depending on a system's needs. They can provide overload protection
for circuit components or limit the force or torque exerted by a linear actuator
or rotary motor.
b. Pressure-Reducing Valves. These
valves limit pressure on a branch circuit to a lesser amount than required in
a main circuit.
c. Sequence Valves. Sequence valves
control the operating sequence between two branches of a circuit.
11-2. Directional-Control
Valves.
Directional-control valves also control
flow direction. However, they vary considerably in physical characteristics
and operation. The valves may be a
- Poppet type, in which a piston
or ball moves on and off a seat.
- Rotary-spool type, in which a
spool rotates about its axis.
- Sliding-spool type, in which
a spool slides axially in a bore. In this type, a spool is often classified
according to the flow conditions created when it is in the normal or neutral
position. A closed-center spool blocks all valve ports from each other when
in the normal position. In an open-center spool, all valve ports are open
to each other when the spool is in the normal position.
Directional-control valves may also
be classified according to the method used to actuate the valve element. A poppet-type
valve is usually hydraulically operated. A rotary-spool type may be manually
(lever or plunger action), mechanically (cam or trip action), or electrically
(solenoid action) operated. A sliding-spool type may be manually, mechanically,
electrically, or hydraulically operated, or it may be operated in combination.
Directional-control valves may also
be classified according to the number of positions of the valve elements or
the total number of flow paths provided in the extreme position. For example,
a three-position, four-way valve has two extreme positions and a center or neutral
position. In each of the two extreme positions, there are two flow paths, making
a total of four flow paths.
Spool valves are popular on modern
hydraulic systems because they
- Can be precision-ground for fine-oil
metering.
- Can be made to handle flows in
many directions by adding extra lands and oil ports.
- Stack easily into one compact
control package, which is important on mobile systems.
Spool valves, however, require good
maintenance. Dirty oil will damage the mating surfaces of the valve lands, causing
them to lose their accuracy. Dirt will cause these valves to stick or work erratically.
Also, spool valves must be accurately machined and fitted to their bores.
Four-Way Valves. Four-way, directional-control
valves are used to control the direction of fluid flow in a hydraulic circuit,
which controls the direction of movement of a work cylinder or the rotation
of a fluid motor. These valves are usually the sliding-spool type. A typical
four-way, directional-control valve has four ports:
- One pressure port is connected
to a pressure line.
- One return or exhaust port is
connected to a reservoir.
- Two working ports are connected,
by lines, to an actuating unit.
Open-center valves are used when
a work cylinder does not have to be held in position by pressure and where power
is used to perform a single operation. These valves also avoid shock to a system
when a valve spool is moved from one position to another, since in the intermediate
position, pressure is temporarily relieved by liquid passing from a pump directly
to the reservoir.
11-3. Flow-Control
Valves.
Flow-control valves are used to control
an actuator’s speed by metering flow. Metering is measuring or regulating
the flow rate to or from an actuator. A water faucet is an example of a flow-control
valve. Flow rate varies as a faucet handle is turned clockwise or counterclockwise.
In a closed position, flow stops. Many flow-control valves used in fluid-powered
systems are similar in design and operation to a water faucet’s. In hydraulic
circuits, flow-control valves are generally used to control the speed of hydraulic
motors and work spindles and the travel rates of tool heads or slides. Flow-control
valves incorporate an integral pressure compensator, which causes the flow rate
to remain substantially uniform regardless of changes in workload. A non-pressure-compensated flow control, such as a needle valve or fixed restriction, allows
changes in the flow rate when pressure drop through it changes. Variations of
the basic flow-control valves are the flow-control-and-check valves and the
flow-control-and-overload relief valves.
12. Accumulators
Accumulators. Like an electrical
storage battery, a hydraulic accumulator stores potential power, in this case
liquid under pressure for future conversion into useful work. This work can
include operating cylinders and fluid motors, maintaining the required system
pressure in case of pump or power failure, and compensating for pressure loss
due to leakage. Accumulators can be employed as fluid dispensers and fluid barriers
and can provide a shock-absorbing (cushioning) action.
13. Assembly, Troubleshooting
& Maintenance
13-1. Good Assembly
Practices
Most important – cleanliness.
All cylinder, valve, pump and hose
connections should be sealed and/or capped until just prior to use.
Air hoses can be used to clean fittings
and other system components. However, the air supply must be filtered and dry
to prevent contamination of the parts. Examine pipe fittings and hose assemblies
prior to use to be certain that burrs, dirt and/or scale are not present. All
pipe and tubing ends should be reamed to prevent restriction and turbulent flow.
Do not use Teflon tape on straight thread connections.
When installing V-belt pulleys on
pumps or motors, line up both pulleys as closely as possible. Always install
the pulleys with a minimum amount of overhang as close to the pump or motor
face as possible. This increases bearing service life.
13-2. Troubleshooting.
Causes of Improper Operations. If
improper operation does occur, the cause can generally be traced to one of the
following:
- Use of the wrong oil viscosity
or type.
- Insufficient fluid in the system.
- Presence of air in the system.
- Mechanical damage or structural
failure.
- Internal or external leakage.
- Dirt, decomposed packing, water,
sludge, rust, and other foreign matter in the system.
- Improper adjustments.
- Heat exchanger that is plugged,
dirty, or leaking.
Trouble shooting general
- Is the oil level correct when
the pump is operating?
- Is the condition of oil and filters
acceptable?
- Are pressure, flow and flow direction as specified?
- Is the oil temperature too high
or too low (oil viscosity)?
- Are there any vibrations
or noise (cavitation)?
For more EXCELLENT troubleshooting
information, see the following pdf files I compiled from the US Army Hydraulics
Manual and Danfoss Hydraulics Manual. |
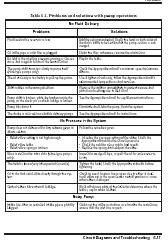 |
Army
Hydraulic Troubleshooting charts |
|
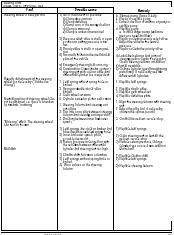 |
Danfoss
Hydraulic Troubleshooting charts |
13-3. Aeration / Cavitation
The following are candidates for
the formation of air in a system.
- Leaking inlet lines.
- Control valve “O”
rings leaking.
- Shaft seal leakage.
- Leaking cylinder packings caused
by cavitating cylinders.
- Turbulence or sloshing in the
reservoir.
- Vortexing fluid in the reservoir
- Release of air suspended within
the fluid.
Effects
Aeration can be in many forms; large
bubbles, foam or in various degrees of suspension. It usually causes pump noise
(cavitation). Small bubbles cause extreme and rapid ring wear, with corresponding
vane tip wear. Larger bubbles cause vanes to collapse and pound.
Causes and Cures
- Leaking Inlet Lines
- Pipe threaded fittings can
be porous. Use an approved type of pipe thread sealer on all pipe threads.
- If the pump inlet flange
surface is rough, scored or mutilated, air leakage past the “O”
ring seal can result. With any of the above defects, air can be pulled
into the system.
- Control Valve “O”
Rings Leaking
- “O” rings are
used to seal against port leakage in many control valves. These seals
can be checked by applying heavy grease around the part to be checked.
If the noise stops, the trouble has been located and repair can be initiated.
- Shaft Seal Leakage
- Most vane pumps are internally
drained. The shaft seal cavity is connected to the pump inlet. Excessively
high inlet vacuums can cause air leakage at the shaft seal. The maximum
vacuum measured at the pump inlet should not exceed five inches of mercury.
Shaft misalignment can increase the probability of air leakage past the
shaft seal. Universal jointed couplings or splined couplings can cause
seal leakage if not properly aligned. Straight (direct) coupling should
never be used.
- Leaking Cylinder Packings Caused
By Cavitating Cylinders
- On applications where a rapid
raise and lower cycle is experienced, air can enter the system through
a cylinder rod seal. Vacuums in excess of 20 inches of mercury have been
recorded in systems without anti-cavitation check valves. This is enough
to force dirt particles past the shaft seal into the system with the air.
An anti-cavitation check will allow flow from the reservoir to enter the
rod area of the cylinder during a vacuum condition from developing. This
will lower the possibility of fluid contamination through the rod seal
of a working cylinder.
- Turbulence or Sloshing in the
Reservoir
- Return lines, if improperly
located, can cause turbulence and aeration. Return lines emptying above
the fluid level cause bubbles to form in the system. Return lines should
always be terminated below the fluid level. Vehicle movement can cause
sloshing within the reservoir. Reservoir must be deep enough to prevent
aeration.
- Vortexing Fluid in the Reservoir
- If the fluid level in the
reservoir is low and the inlet demand is great, a vortex condition can
develop which pulls air into the pump inlet. In a hydraulic system, vortexing
is normally the result of low fluid or poor reservoir design. One of the
best ways of curing a vortex problem is to place an anti-cavitation plate
over the outlet of the reservoir. This is a common piece of sheet metal
at lease 1/8 inch thick set over and above the outlet opening. This plate
will allow flow into the outlet from a horizontal direction and effectively
extends and enlarges the reservoir opening. This prevents the vortex condition
from developing.
- Release of Air Suspended in Fluid
- There is considerable air
suspended in cold hydraulic fluid. As the fluid warms, air is released
into the system. A reduction of fluid pressure will also release air out
of suspension. A simple relief valve poppet can create an orifice that
increases velocity of the fluid and lowers its pressure. The reduced pressure
condition releases air out of suspension into the system. Relief valves
should be returned below the fluid level of the reservoir as far from
the reservoir outlet as possible. This allows time for the air released
by the relief valve to be removed before leaving the reservoir and entering
the inlet area of the pump. In some cases, special return line configurations
are needed, or air bleed valves used, to remove air from the system.
13-4 Cause Of Leaks
Almost all hydraulic system leaks
occurring after extended service result from three conditions:
- Loosening of fittings and connectors
by shock and vibration
- Wear of dynamic seals and mating
parts especially in hydraulic cylinders
- Deterioration of the elastomer
because of elevated fluid temperatures or an incompatibility with the hydraulic
fluid
13-5 Combatting Shock
And Vibration
Many things can be done to minimize
leakage from loose fittings and connectors subject to shock and vibration:
- Support all pipe lines with damped
mountings to absorb both shock and vibration.
- Reduce shock with low-shock valves
or accumulators.
- Use pressure controls with low
override and strategically placed to protect all parts of the system.
- Use a minimum number of fittings
and connectors. Use welded joints wherever practical.
- Use parallel thread connectors,
tees and elbows in place of tapered pipe threads.
- Use manifolds instead of individual
lines wherever possible.
- Specify proper bolt and plug
torques for expected peak pressures to prevent surface separation and static
seal nibbling.
- Stress good workmanship to avoid
poorly assembled fittings and connectors.
13-6 Reducing Dynamic
Seal Wear
- Eliminate side loads on cylinder
rod and drive shaft seals.
- Protect cylinder rods from abrasive
dirt with scrapers, shields or rubber gaiters.
- Provide the requisite filtration
and easily cleaned reservoirs to prevent dirt build-up in the oil.
- Keep cylinder rod and shaft speeds
as low as possible.
13-7 Draining the System
Draining The System. The system should
be started and fluid heated before draining. This will lower the time it takes
to drain the system and allow impurities suspended in the fluid to be removed.
It is desirable to remove all fluid from the system. Bleeding of the fluid at
the lowest point in the system will help in most cases. Systems which have accumulated
deposits that were not removed during draining must be flushed with a light
viscosity fluid. The fluid should contain a rust inhibitor to protect metal
surfaces against rust formation after draining. When hydraulic fluid is added
to replenish the system, it should be pumped through a 25 micron filter. If
such a filter is not available, a funnel with a fine wire screen (200 mesh or
finer) can be used. It is important that fluid be clean and free of all substances
which will cause improper operation.
13-8. Maintenance
Three simple maintenance procedures
have the greatest effect on hydraulic system performance, efficiency and life.
- Maintaining a clean sufficient
quantity of hydraulic fluid of the proper type and viscosity.
- Changing filters and cleaning
strainers.
- Keeping all connections tight,
but not to the point of distortion, so that air is excluded from the system.
|
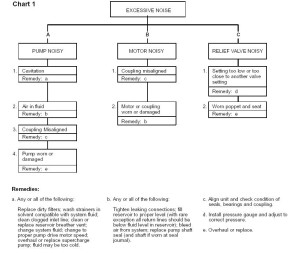 |
13-9 Noise diagnosis: |
|
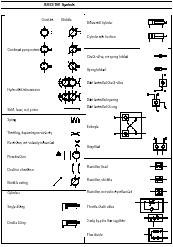 |
Circuit Diagrams
and Symbols
Click on the image to open a .pdf file of standard
international hydraulic circuit symbols |
Bernoulli's Principle |
Law which states
that the static pressure of a moving liquid varies inversely with its velocity;
that is, as velocity increases, static pressure decreases. |
capacity |
Same as volumetric output. |
cavitation |
A condition that occurs in pumping
when available fluid does not fill the existing space; cavitation causes
erosion of the metal in the inlet and speeds deterioration of the hydraulic
oil. |
closed-center system |
A pump system where the pump
continues to operate against a load in the neutral condition. |
cylinder |
A hydraulic actuator that is
constructed of a piston or plunger which operates in a cylindrical housing
by the action of liquid under pressure; a cylinder can be one of several
types: single acting, double acting, differential, non-differential, ram
type, piston type, cushioned, or lockout. |
delivery rate |
Same as volumetric output. |
directional-control valves |
Valves that control the flow
direction; they can be a poppet, a sliding-spool, a check, a two-way, or
a four-way valve. See also flow-control valves, pressure control valves;
valves. |
displacement |
The amount of liquid that is
transferred from the pump's inlet to its outlet in one revolution or cycle;
displacement is either fixed or variable. See also fixed-displacement pump;
variable-displacement pump. |
displacement principle |
Principle which explains how
fluid is taken in at one point and is displaced to another point; displacement
is either non-positive or positive. See also non-positive-displacement pump;
positive-displacement pump. |
energy T |
The ability to do work, expressed
in ft/lbs. See also friction; heat energy; kinetic energy; potential energy. |
fixed-displacement pump |
A pump in which the GPM output
can be changed only by varying the drive speed. See also displacement; variable-displacement
pump. |
flow |
The movement of the hydraulic
fluid caused by a difference in the pressure at two points; velocity and
flow rate are the two ways to measure flow. See also flow rate; velocity. |
flow rate |
The measure of how much volume
of a liquid passes a point in a given time, measure in GPM. See also flow;
velocity. |
flow-control valves |
Valves that are used to control
the actuator speed by metering the flow; they can be a gate, a globe, a
needle, a restrictor, an orifice-check, or a flow-equalizer valve. See also
directional-control valves; pressure-control valves; valves. |
force |
Anything that tends to produce
or modify motion, expressed in pounds. |
friction |
The resistance to relative motion
between two bodies. See also energy; heat energy; kinetic energy; potential
energy. |
GPM |
gallon(s) per minute |
head |
The vertical distance between
two levels in a fluid. |
heat energy |
The energy a body possesses
because of its heat; considered a dynamic factor. See also energy; friction
kinetic energy; potential energy. |
hp |
horsepower; standard unit of
power; one HP is equal to 550 ft/lbs of work every second. |
HP |
hydraulic hp |
hydraulic actuator |
A piece of equipment that receives
pressure energy |
hydraulics |
The science of transmitting
force and/or motion through the medium of a confined liquid. |
JIC |
Joint Industry Conference |
kinetic energy |
The energy a body possesses
because of its motion; the amount of kinetic energy in a moving liquid is
directly proportional to the square of its velocity; considered a dynamic
factor. See also friction; heat energy; potential energy; velocity pressure. |
laminar flow |
Flow that occurs when particles
of a liquid move in straight lines parallel to the flow direction. See also
turbulent flow. |
non-positive-displacement pump |
This type of pump discharges
liquid in a continuous flow. See also displacement principle; positive displacement
pump. |
open-center system |
A pump system where the pump's
output has a free flow path back to the reservoir in the circuit's neutral
condition. |
Pascal's Law |
Basic law of hydraulics that
Blaise Pascal formulated in the 17th century; Pascal states that pressure
in a confined fluid is transmitted undiminished in every direction and acts
with equal force on equal area and at right angles to the container's walls. |
positive-displacement pump |
This type of pump discharges
volumes of liquid that are separated by periods of no discharge. See also
displacement principle; non-positive-displacement pump. |
potential energy |
Energy due to position; in hydraulics,
potential energy is a static factor. See also energy; friction; heat energy;
kinetic energy. |
pressure |
The force exerted against a
specific area, expressed in psi. |
pressure-control valves |
Valves that may limit or regulate
pressure, create a particular pressure condition required for control, or
cause actuators to operate in a specific order. Pressure- control valves
can be a relief, a pressure-reducing, a sequence, or a counterbalance valve.
See also directional-control valves; flow-control valves; valves. |
psi |
pound(s) per square inch |
resistance |
A condition in a hydraulic system
that is usually caused by a restriction or obstruction in the path or flow. |
rotary pump |
A positive-displacement pump
in which rotary motion carries the liquid from the pump's inlet to its outlet. |
slippage |
The measure of a pump's efficiency
expressed in percent; oil leaks from the pressure outlet to a low-pressure
area or back to the inlet; some slippage is designed into pump systems for
lubrication purposes. |
turbulent flow |
Flow that develops when flow
speed increases beyond a given point. See also laminar flow. |
two-stage pump |
A pump that consists of two
separate pump assemblies that are contained in one housing. |
valves |
Objects in a hydraulic system
that control the operation of the actuators; valves regulate pressure by
creating special pressure conditions and by controlling how much oil will
flow in portions of the circuit and where it will go. See also directional-control
valves; flow-control valves; pressure-control valves. |
vane-type pump |
A pump in which a slotted rotor
splined to a drive shaft rotates between closely fitted side plates that
are inside of an elliptical- or circular-shaped ring; vane pumps can be
double, unbalanced, or balanced. |
variable-displacement pump |
A pump in which the pumping-chamber
sizes can be changed; the GPM delivery can be changed by moving the displacement
control, changing the drive speed, or doing both. See also displacement;
fixed displacement pump. |
velocity |
The average speed of a fluid's
particles past a given point, measured in fps. See also flow; flow rate. |
velocity pressure |
Pressure caused by kinetic energy.
See also kinetic energy. |
volumetric output |
The amount of liquid a pump
can deliver at its outlet port per unit of time at a given drive speed,
usually expressed in GPM or cubic inches per minute. Also called delivery
rate or capacity. |
work |
The measure of force multiplied
by distance. |
|
|
|