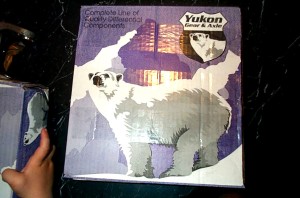 |
The kit comes
in a Yukon brand box. Yukon remain a bit of a mystery to me - I have
never ben quite able to figure out exactly what there gig is - but
as near as I can figure, they themselves don't actually manufacture
anything - they are a mass buy and re-badge company. This works out
very well for me here - as the kits I got from 4WDFACTORY were 100%
genuine Dana/Spicer parts. |
|
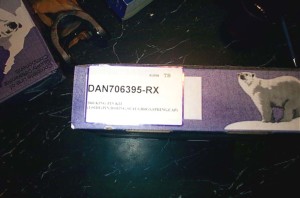 |
The Yukon boxes are even
marked with the Dana/Spicer part number - DAN706395-RX |
|
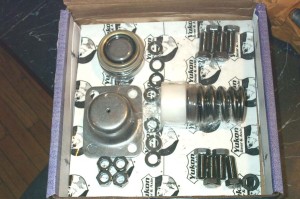 |
Inside, there is absolutely
everything you need, neatly shrink wrapped on a piece of card. All
parts interchange between all kingpin Dana 60 front axles, be they
GM, Dodge, or Ford. The only difference is that the 85-91 Ford use
a different upper kingpin seal (#32) than all the rest - but both
seals are included in the kit. The complete listing, with numbered
diagram is below: |
|
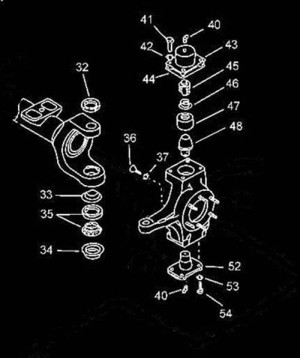 |
Diag. # |
Dana
Spicer part number |
Description |
Kit
Contains |
32 |
620058 |
Upper
kingpin seal |
2 |
33 |
37305 |
Lower
kingpin seal |
1 |
34 |
41777 |
Lower
kingpin bearing oil seal |
1 |
35 |
706150x |
Lower
kingpin bearing and race |
1 |
40 |
|
Grease
Zerk (nipple) |
2 |
41 |
30875 |
Upper
kingpin cap bolt |
4 |
42 |
|
Upper
kingpin cap lock washer |
4 |
43 |
GM
part no. 0047-1750 |
Upper
kingpin cap (cover) |
1 |
44 |
37307 |
Upper
kingpin cap gasket |
2 |
45 |
37300 |
Kingpin
spring |
1 |
46 |
620180 |
Kingpin
spring retainer |
1 |
47 |
41886 |
Upper
kingpin bushing |
1 |
48 |
37302 |
Kingpin |
1 |
52 |
37299 |
Lower
kingpin bearing cap |
(not
incl.) |
53 |
500357-13 |
Lower
kingpin cap lock washer |
4 |
54 |
500412-13 |
Lower
kingpin cap bolt |
4 |
|
|
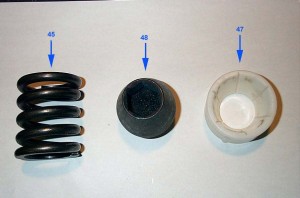 |
From L to
R this is the kingpin spring, Kingpin, and kingpin bushing. |
|
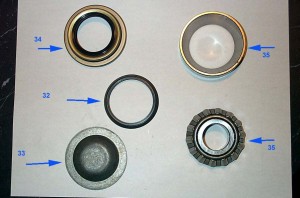 |
This pic shows the
bottom lower kingpin oil seal (#34) [a confusing name, as there
is no oil present, just grease] , upper kingpin seal (#32), lower
kingpin seal (#33) [again, a slightly confusing name, as it is a
metal dust cap more than a seal], and the lower kingpin bearing
and race (also called cone and cup).
The kit from $WDFACTORY.com
includes Timkin Made in U.S.A. Bearing and race. |
|
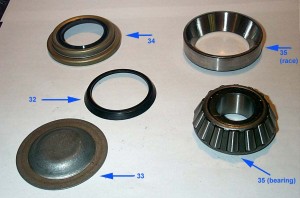 |
Another view of the
parts, you can see how the lower kingpin seal (lower left) is actually
a metal cap. |
|
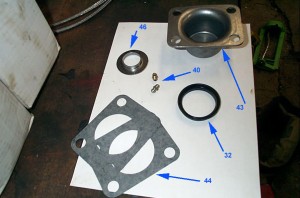 |
The remainder of the
parts in the kit, including the kingpin spring retainer (#46) ,
grease fittings (#40), upper kingpin cap gaskets (#44 ), upper kingpin
cap (#43 ), and upper kingpin seal (#32 ).
Not pictured are the
8 SAE Grade 8 bolts and lock-washers included in the kit. |
Kingpin
Disassembly |
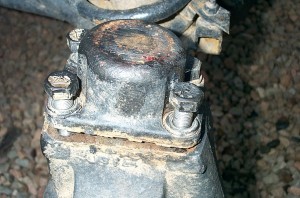 |
Step one is to raise
the vehicle, set the axle on jack-stands, and remove the front wheels.
Begin by removing the
4 bolts from the upper kingpin cap. Loosen each one a little at
a time, as the cap is under tension from the large spring inside.
Note that on most drivers (left) side knuckles, the cap may be part
of the steering arm, and is held on by 4 studs and tapered nuts.
These parts are NOT included in the kit, so if your setup includes
this, you will have to re-use the old hardware or acquire new studs,
washers, and nuts ahead of time. |
|
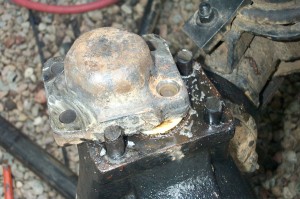 |
Note that the fun can
start right here! If you're working on a well abused older truck like
me, just saying "remove the bolts" can be a 3 hour job.
The torched studs and ground cap should attest to the fun I had getting
this side off. It seems any job I do that requires a wrench or socket,
I end up using a torch and grinder! |
|
 |
Once you get the cap off,
remove the spring and spring retainer from on top of the kingpin bushing. |
|
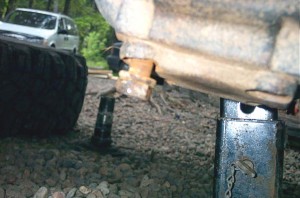 |
Next, remove the 4
bolts and lock washers holding on the lower kingpin bearing cap.
You can discard the old bolts and washers as new ones are included
in the kit. |
|
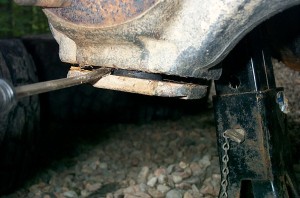 |
With the bolts removed,
pry the cap down with a screwdriver. Try not to hammer a chisel in
there and mar the machined surfaces where the bearing cap and knuckle
mate. |
|
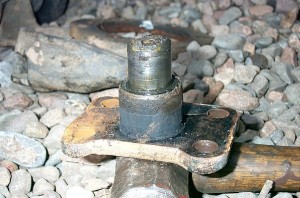 |
When the cap is removed
it looks like this. |
|
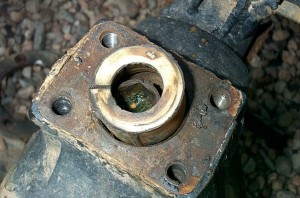 |
Pry up the upper kingpin
bushing. |
|
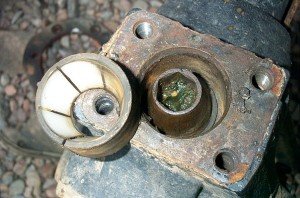 |
And remove it from on
top of the kingpin. |
|
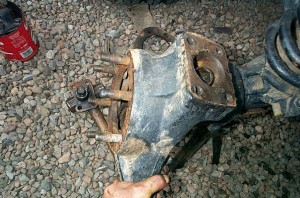 |
You can now grab the
knuckle firmly by the steering arm and tilt it inboard, tipping
it over the kingpin, and remove it from the axle.
You will be left with
the axle with a bare end forging ("C" or "inner knuckle")
with the kingpin in the top, and the lower grease seal, bearing,
race, and dust cap in the bottom bore. |
|
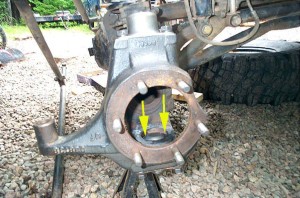 |
First remove the lower
grease seal, bearing, race, and dust cap from the lower bore of
the end forging by striking it around the edge with hammer and chisel.
Don't worry about using excessive force, there isn't anything in
here to damage that you won't be replacing. That's another nice
thing about ordering a complete kit - use force at will ;-). Don't
just hammer the center of the dust cap though, as you need to hammer
around the edge of the race to press it out. heat always helps -
but there's a lot of grease in there. |
|
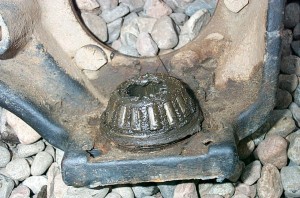 |
When you drive it all
out, you will get the grease seal and bearing out, as well as the
race and dust cap. This is how the grease seal and bearing sit when
the knuckle is installed! |
|
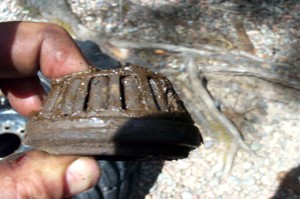 |
Gee, do you think I'm
replacing this bearing too early? Maybe it's good for another 23 years?
:-) |
|
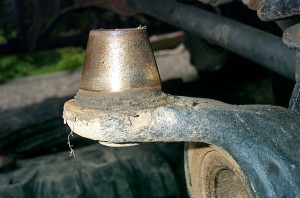 |
The manuals will tell
you to remove the kingpin itself first, so that you can then place
a punch / driving tool down through the upper bore of the end forging
to drive the lower components out straight. This makes sense, and
I'm sure works well, but there is a very good reason I didn't describe
it that way - I wanted to prove that it is possible to remove the
lower components WITHOUT removing the kingpin at all.
Because - removing the
kingpin is a humongous bi#ch. I mean, it was really challenging.
As such, you may want to carefully inspect it and decide not to
replace it. Mince was pitted and corroded, and I'm a sucker for
punishment, so I went ahead and replaced it. |
|
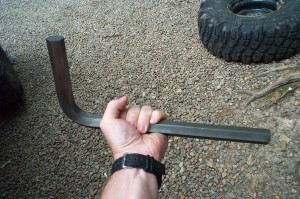 |
The upper kingpin itself
has a 7/8" Allen (hex) key socket head. Meaning you need one
big mother of an Allen key to remove it - especially since it will
be well rusted in there, and was installed with some 600 ft/lbs
of torque!!
I tried all the regular
tricks, welding nuts together and using an impact, etc. etc. I snapped
all kinds of stuff, I swore, I sweat. I checked every tool store
in town - nobody had a 7/8" allen key.
In the end, I MADE this
monster. I believe it may well be the world's largest Allen key!
I went to my steel supplier and bought a few feet of 7/8" hex
stock. I then went to the local 18 wheeler place, and had the guys
bend the hex stock 90°. |
|
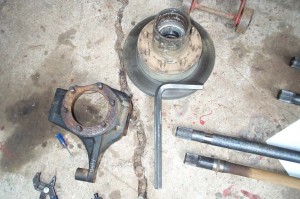 |
Look at the size of it!!! |
|
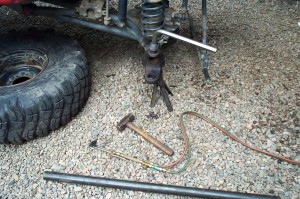 |
Even with this monster
tool, I still needed the rest of this gear to remove the kingpins.
Pictured are a 4' long cheater bar (Sched 80 pipe), oxy/acetylene
torch, BFH, and the monster Allen key. |
|
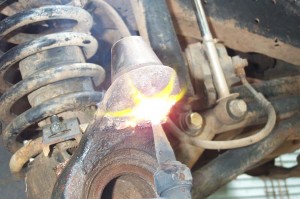 |
The process required heating
the wee out of the kingpin (careful not to overdo it and distort the
end forging though)... |
|
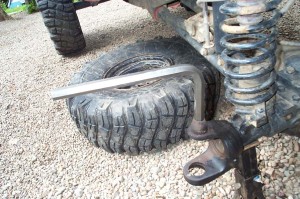 |
...hammering the monster
Allen key into the kingpin... |
|
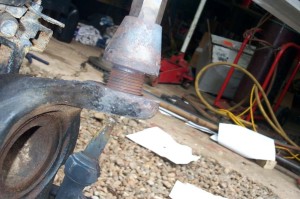 |
...slipping the 4' cheater
bar over the monster Allen key and reefing on the end of it. |
|
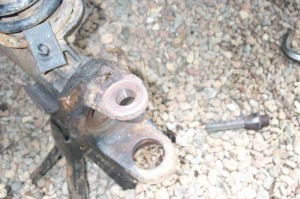 |
Once it broke free, I
whipped out the monster Allen key, dropped in a short straight section
of 7/8" hex stock, and slipped a 7/8" deep socket over that
so I could wind it out with a ratchet. You can see the removed kingpin
with the straight 7/8" hex stock still in it in the pic to the
right of the end forging. It stayed there for a long time while it
cooled! |
Kingpin
Re-assembly |
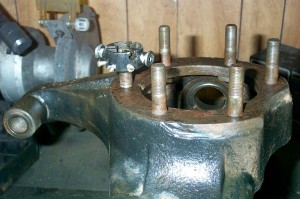 |
Before I slapped everything back together, while the knuckles were
off, I took the time to clean them up a bit, including running a die
over the threads of the spindle studs. |
|
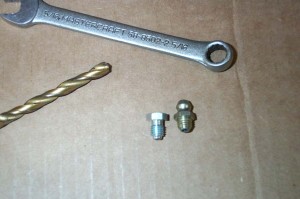 |
I also decided to make another small, custom modification. All the
grease fittings on my original knuckles had been ground or broken
off. As a result, maintenance suffers, and you can see the results
above! I went to my local 18 wheeler supply house, and sourced these
flush-style grease fittings to use instead of the regular-style supplied
in the kit. This pic shows how much less the will protrude. |
|
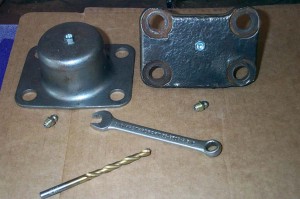 |
Note that the threads
are slightly different on the flush style fittings compared to the
regular style. This is done intentionally so they are not mixed up
in driveline and axle U-joint applications where using the longer
regular style where it wasn't intended would cause interference or
binding and breakage. In the upper kingpin cap, I just carefully turned
the new flush style fittings in anyway, but you have to be very careful
not to strip them out completely. In the lower bearing cap, the old
fitting was broken off flush in the hole anyway, so I just hit it
with a 7/32" drill bit first, then the new grease fittings tightened
in nicely. |
|
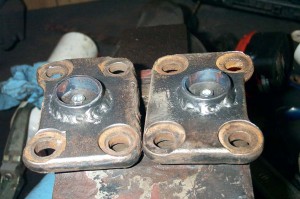 |
I still felt the grease fitting was vulnerable on the very bottom
of the knuckle like that though, so I but a couple of thin sections
from a piece of DOM tube that was lying around, and welded them around
the grease fittings for protection. |
|
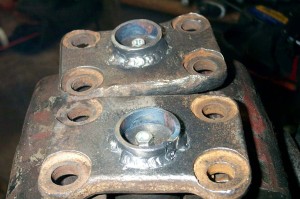 |
I got the idea from seeing tractors with steel rings welded around
valve stems for protection. |
|
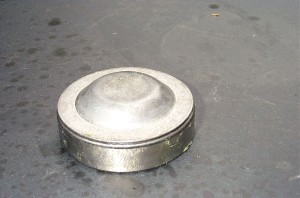 |
Now that I had finished goofing around, it was time to reinstall
everything. First thing to go back is the lower kingpin race and dust
cap. When installed in the end forging the dust cap goes on top of
the race, the opposite side to where the bearing goes (obviously!),
like this. |
|
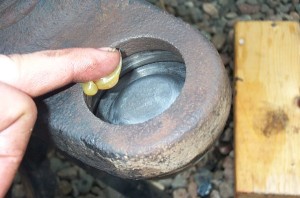 |
I placed the dust cap in first, and secured it there with a dab
of grease. |
|
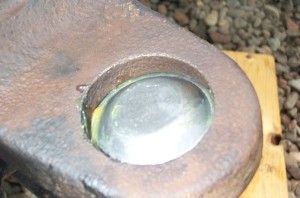 |
Note. If you try this while the end forging is still warm from having
used heat to remove things, the grease will melt, and the cap will
fall out and into the gravel and the remaining un melted grease will
then cause dirt and grit to stick to it that you will then have to
clean off before you can reinstall the cap and then it will happen
again just as you are trying to line up and carefully drive in the
new race while lying on your side on the gravel and you may just get
a little annoyed and then you will suddenly figure it out! |
|
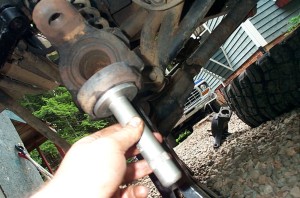 |
Driving the race in nice and square while lying under the truck
can be a bit of a challenge. I used a little aluminum race/seal driver
kit and ALL of my patience! It would be far easier with the axle upside
down on a workbench! |
|
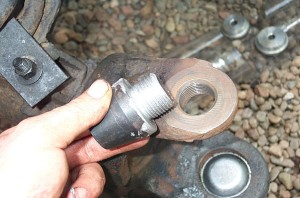 |
Once the lower kingpin dust cap and race are installed, install
the kingpin. I coated the threads with a little anti-seize first. |
|
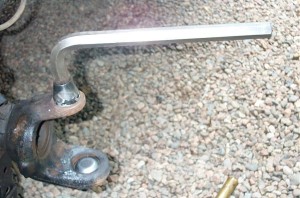 |
The book calls for 500-600 lb/ft of torque. I slipped the monster
Allen key in, slid the pipe over the end of it, and yanked till she
was good and tight! |
|
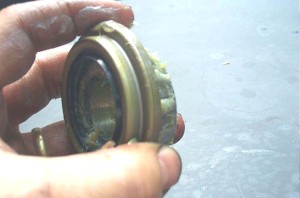 |
Next go the lower kingpin bearing and grease seal. When installed
the bearing sits in the grease seal in this orientation, with the
smaller diameter part of the seal to the bottom... |
|
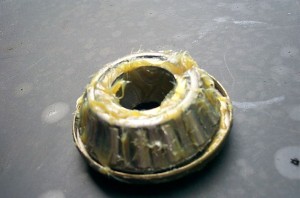 |
...like this. |
|
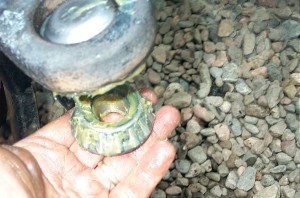 |
After packing the bearing thoroughly with grease (I used a good
quality EP Wheel Bearing Grease) I stuck it up in the race... |
|
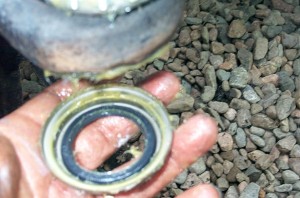 |
...and then placed the
grease seal in place. |
|
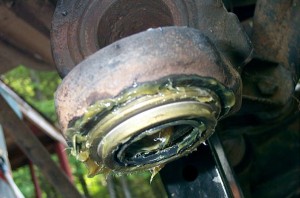 |
I fit it in place by hand, and then placed a small block of wood
over it to tap it into place with a hammer. |
|
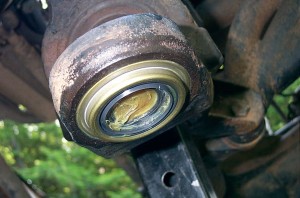 |
When it's fully seated in place, there will be a short part protruding
from the bottom of the end forging, like this. |
|
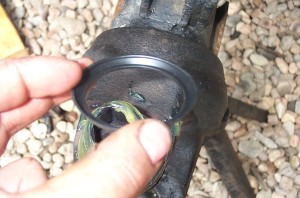 |
The next step is to install the upper kingpin seal over the kingpin,
making sure the lip is facing up. |
|
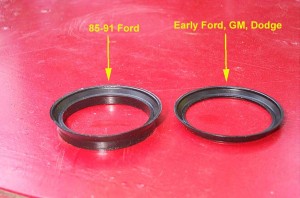 |
The kit includes 2 different
seal, one for 85-91 Ford Dana60F, and a shorter one for all the rest.
Of course I only learned this AFTER I had assembled everything, and
so, based on trial fit, I had actually used the taller Ford seal in
my Chevy Dana60. I do not see this as a major issue. |
|
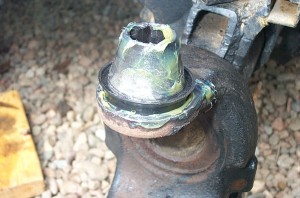 |
It simply slips over the kingpin. When it is in place, fit the knuckle
back over the kingpin so that is on the end forging. |
|
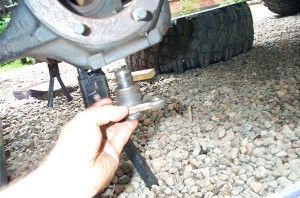 |
Next, the lower kingpin bearing cap is installed to secure the knuckle
in place on the end forging. |
|
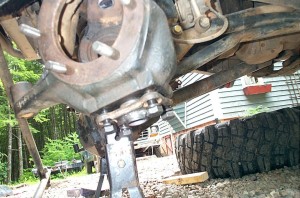 |
Make sure the mating surfaces are clean... |
|
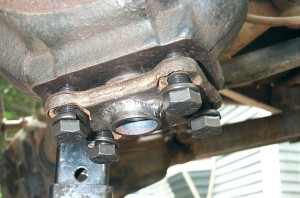 |
...and torque the bolts to 80 ft/lbs. |
|
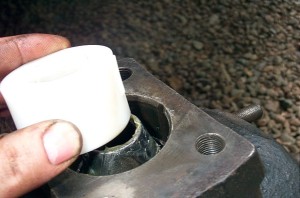 |
Fill the cavity surrounding the kingpin with grease... |
|
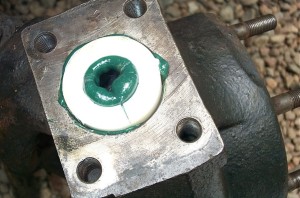 |
...and install the kingpin bushing over the kingpin. Note that there
is a ridge on the bushing that indexes with a slot in the knuckle,
so that the bushing only fits one way. |
|
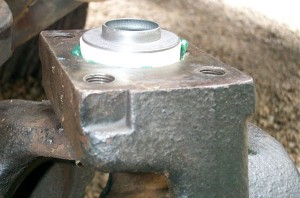 |
Then place the spring retainer on the bushing... |
|
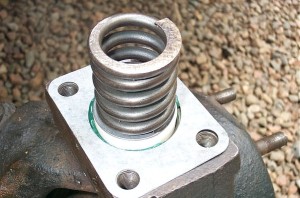 |
...and the spring on the spring retainer. |
|
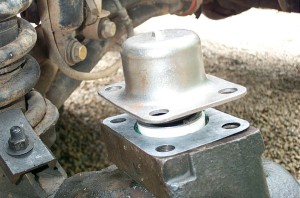 |
Finally, the cap goes on over the spring. |
|
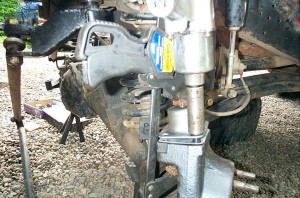 |
I used a clamp to compress the cap down over the spring so that
I could tighten the bolts down in stages to 80 ft/lbs.
All that is left after that is to fully grease the upper and lower
grease fittings. |
|
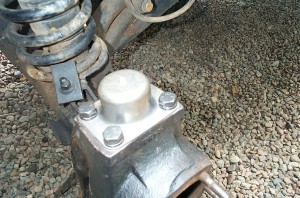 |
The top is all buttoned up... |
|
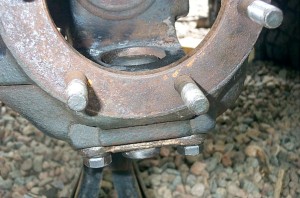 |
...and the bottom, with the fancy new grease nipple skidplates!
:-) |
|
 |
And that's it. Fully rebuilt
kingpins....that should improve steering response and help eliminate
/ prevent any death wobble that commonly arises from worn kingpin
springs, bushings, and bearings. |
Conclusion
This is a nice, complete kit. The only thing required for the rebuild
that is not included is the grease, and new studs/tapered nuts for the
drivers side. The components are all top quality, including made in USA
Timkin bearings. the only thing a little light duty are the upper kingpin
caps, that are just a thin stamped steel. However, this part doesn't really
see any stress or load, so I don't think it's an issue.
I do have one recommendation for the guys at 4WDFACTORY.com - it might
be a good idea to offer a BIG 7/8" Allen key as an option for the
kit, for those that plan to change out the kingpins like I did. I found
that an Allen key that size is pretty hard to find, and all but impossible
to do without.
References:
|
|