This first article will actually be comprised of two different parts, as follows:
RPO’s and Generations
It’s a little ironic that I, as uptight as I am about the accurate naming of things, should actually use a misnomer in the title of this article. Let me explain.
GM uses a 3-digit code, called an RPO (an acronym for Regular Production Option), to identify the options with which a specific vehicle is built. They are listed on a label or sticker called the Service Parts Identification (SPID) label. On late-model GM cars and trucks this label is found inside the glove box. One of the most famous RPO's of all time is “Z28”. Z28 is the GM code, or RPO, that designates an optional performance package available on Chevy Camaros. This code has become so well known, and so often used, that it has actually come to be used to describe the car itself, as in, “Yea, I drive a Z28”.
In a similar fashion, “LS1”, which is the RPO code for the very first GM all-aluminum, third generation, V8 small block engine, has become so popular a term that is has come to be commonly used (if somewhat inaccurately) to describe any of the third, and even fourth generation GM V8s. As you will shortly read, GM designed the first third-generation (or Gen III) V8 – the LS1 - to power the 1997 Chevy Corvette. It was so successful that many folks use the term “LS1” or “LS motor” to refer to any Gen III or later Gen IV V8, despite the fact that the LS1 hasn’t been produced since 2005 and the RPO for many of the third and fourth generation motors does not contain the letters “LS”.
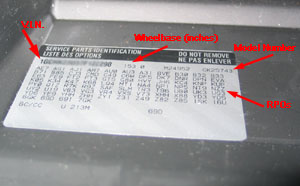 |
The Service Parts Identification (SPID) label found in my 2007 Chevy Silverado truck. This label includes other information along with the list of RPO's, including the V.I.N., wheelbase, paint codes, and vehicle model number. |
So what is the proper way to refer to the latest GM engines? To answer that, we’ll take a brief step back in time and look at the GM V8’s generation by generation, leading up to a brief look at the development history of the latest Gen III and Gen IV motors – the so-called “LS Motors” <-cringe! ;-)
Gen I
The first GM small block V8 engine was introduced in 1955 by Chevy in 265 cu. in. form. It was a now-familiar 90° V8 cam-in-block pushrod V8. Back then, GM didn’t refer to their V8 engines by any “generation” label, but retroactively these first motors are now referred to as the “first generation” or Gen I motors. And what a long generation it was! The Gen I small-block V8 has existed in one form or another as a vehicle production engine from 1955 until 2000 – and is still produced today in many forms for marine, industrial, and after-market crate-motor use. That’s 54 years and counting! Over 90 million have been produced worldwide and the old Gen I small block Chevy, or SBC, still reigns as one of the most popular, purchased, modified, swapped, and successful engines of all time. They came in many forms from carbureted, points ignition to Throttle Body Injection (TBI) to Tuned Port Injection (TPI).
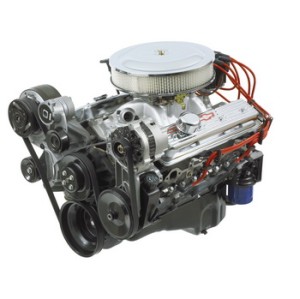
Photo © GM Corp. |
Gen I 350 HO Small Block Chevy V8 Crate Motor. |
So what happened?
Gen II
The second generation, or Gen II, V8’s were as short-lived as the Gen I’s were long. Introduced in the ’92 model year to power the Chevy Corvette, the Gen II LT1 (LT1 being the RPO) and later upgraded Gen II LT4 were short-lived, used in only a few applications until 1997. The Gen II motors feature cast-iron blocks, aluminum heads, reverse-flow cooling, and a dubious “Optispark” optical distributor ignition system mounted low on the motor. They retained the traditional 1-8-4-3-6-5-7-2 firing order of the original Gen I motors. They were hardly lemons, as the reverse-flow cooling system allowed coolant to start at the heads and flow down through the block, keeping the heads cooler, and creating more power by allowing a higher compression ratio and greater spark advance. However, it wasn’t long before the Gen II motors were struggling to meet fuel efficiency, stringent emissions, and weight goals.
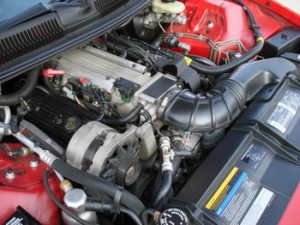 |
Gen II LT1 Small Block Chevy V8. |
What now?
Then, in 1991 GM realized they were at a watershed moment in powertrain development. The results of, and response to, the Gen II LT1/LT4 motors had been underwhelming. At the same time, so the story goes, the tooling at the GM engine factories was at the end of its useful life – making it the perfect time for a redesign of the V8 family. In addition, GM were facing the same pressures as all other engine manufactures of the time – customer needs and regulatory changes were demanding newer engines with:
- Higher performance (more horsepower and torque)
- Better fuel economy
- Reduced emissions
- Less noise, vibration, harshness (NVH)
- Less weight and size to fit in more compact vehicles of the era
- Enhanced quality, reliability, and durability.
In other words, the time was ripe for a complete redesign of the venerable small block V8.
From the start, GM knew that such a redesign would have to be broadly applicable to a wide range of products from trucks to SUV’s to luxury and high performance cars.
To DOHC or not to DOHC?
Another notable feature of the time was the move to double overhead cam (DOHC) engine architecture that was sweeping the automakers of the day. DOHC allows the elimination of pushrods, lifters, and rocker arms as well as removing the cam from the block. However, it is a generally expensive and complicated way to build an engine. It also generally results in a top-heavy and top-wide engine. On the other hand, at least in the early 1990’s, it was considered the “hi-tech” way to build a motor and some in the industry at that time considered pushrod architecture to be old-fashioned and antiquated. So GM had a decision to make – move to DOHC architecture or design a new pushrod V8. As the story goes, sometime in 1992 GM executives conducted a blind comparison test by driving otherwise identically equipped Corvettes – one with the “low tech” LT4 pushrod V8, and the other with the Corvette ZR1-spec Lotus-designed, all-aluminum 32-valve DOHC LT5 engine. Apparently the pushrod V8 LT4 ruled the day and the future of GM V8 development was decided – Gen III was to be a brand-new pushrod V8 design. Although I have no real basis for this claim, I have personally long suspected that perhaps a little stubborn pride crept into the decision as well. After all – most of the European and Japanese manufacturers had already gone DOHC and many scorned GM’s antiquated pushrod technology. I wouldn’t be surprised to learn that GM set out to prove the rest of the world wrong and show they could produce a class-leading V8 engine based on “old” pushrod technology…in any case, that’s just what they did!
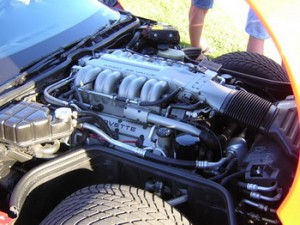
|
ZR1-spec Lotus-designed, all-aluminum 32-valve DOHC LT5 Small Block Chevy V8. |
Gen III
And so it was that in late 1991 GM began development of a brand new small block V8. They started with a completely clean sheet of paper and an ambitious plan to develop a world-class family of V8 engines that would use the same basic architecture to power everything from the flagship Chevy Corvette to the full-size trucks.
The basic design called for a 90° V8 cam-in-block pushrod engine with deep skirt blocks of either cast iron or aluminum, six-bolt cross-bolted main bearing caps, long head bolts that pulled from the bottom of the block, an internally balanced crank, and bigger cam bearings than Gen I or II. The oil pan would be a cast-aluminum structural component designed to add stiffness to the aluminum engine block, while the oil pump would be a gerotor design driven off the nose of the crank as opposed to the older camshaft-driven style. The heads were to be of aluminum with replicated (identical) ports and a 15-degree valve angle. The valve-train would use inline geometry, roller rockers, and roller followers. The intake manifold would be a composite nylon piece formally called the integrated air/fuel module (IAFM) as it is produced and shipped to the engine assembly plant as a unit, complete with fuel rails installed. Coil-near-plug ignition, and sequential multiport fuel injection with a revised firing order of 1-8-7-2-6-5-4-3 completed the basic design. The only features the Gen III’s share with the earlier Gen I/II motors are:
- 4.400 inch bore spacing.
- 90° V8 cylinder orientation.
- Two overhead valves per cylinder.
- Valvetrain oiled through pushrods.
- Connecting rod crank pin diameter of 2.100 inches.
- Lifter diameter of 0.842 inch.
- One-piece rear crank seal design.
- Starter located on lower passenger side of block.
- Oil filter located on lower driver side of block.
- Almost identical bellhousing bolt pattern.
The bellhousing pattern is an extremely cool feature of the Gen III (and IV) motors for those of us swapping them into older or custom rigs. It means that you can sling virtually any GM standard or manual transmission behind a new Gen III/IV motor – from SM465 gear grinder to the legendary TH400 auto to the latest and greatest GM 6-speed manuals and electronically controlled automatics. The only catch is that only five of the six bellhousing bosses on the motor are drilled and tapped. Drilling and tapping the sixth, located on the passenger side, would cause you to cut into the number 8 cylinder water jacket. However, five have proven enough for virtually any setup.
 for Chevrolet Corvette 2004_5_7L_V8_LS1_Y_resize.jpg)
Photo © GM Corp. |
Gen III LS1 - 5.7L all-aluminum V8 |
Gen III LQ4 - 6.0L iron block / aluminum head V8
|
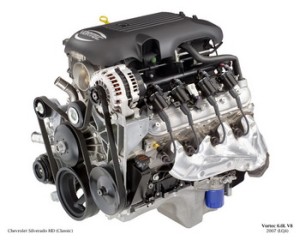
Photo © GM Corp. |
The first Gen III V8 released was the all-aluminum 5.7L LS1 powering the 1997 Corvette. Gen III motor production included 4.8, 5.3. 5.7, and 6.0L car and truck versions, with iron or aluminum blocks. Gen III motors were discontinued in cars in 2005, to be replaced by Gen IV, but their use in trucks continued until 2007. The most common Gen III motors include the:
- LS1 –5.7L all aluminum Corvette, Camaro, and Firebird
- LS6 – H.O. version of the LS1, used in Corvette
- LQ4 – 6.0L iron block truck motor
- LQ9 – H.O. version of the LQ4
- LM7 – 5.3L iron block truck motor
And then came the Gen IV.
Gen IV
The jump from Gen I to II was evolutionary. The jump from Gen II to III was a revolutionary leap. The jump from Gen III to IV was again an evolutionary step, rather than a leap. In fact, a great many of the basic architectural elements remain in place from the Gen III to IV motors (which also means a lot of parts and go-fast goodies are interchangeable). So much so, that one may question why the latest Gen IV’s deserve a separate generation of their own at all. Apart from continued refinements, the biggest changes between Gen III and IV are those not so obvious to the eye. Advances in computing power, injection technology, and other high-tech improvements are what set the fourth generation apart from the third. Again, reacting to both customer's and regulator’s demands – the fourth generation GM V8’s make use of huge advances in computer control and electronic engine management to enable advanced new features such as active fuel management (AFM) – also called displacement on demand (DOD), variable valve timing (VVT), and Electronic Throttle Control (ETC) (so-called throttle-by-wire) – and all still in the “old” 90° V8 pushrod architecture! Another feature of the Gen IV motors is even greater availability of all-aluminum motors including all-aluminum truck engines available in 4.8, 5.3, 6.0, and 6.2L displacements.
 for Chevrolet Corvette_resize.jpg)
David Kimble Illustration © GM Corp. |
Gen IV LS2 - 6.0L all-aluminum V8. |
Gen IV L9H - 6.2L all-aluminum V8 with Variable valve Timing (VVT). |
 X09PT_8C081_resize.jpg)
Photo © GM Corp. |
Gen IV refinement of the Gen III platform also included greater power production through increased displacement (generally larger bore but same stroke as the Gen III), higher compression, higher flow cylinder head improvements, flat top pistons, floating wrist pins, larger intakes, larger throttle bodies, larger exhaust, more aggressive camshafts and increased max RPM enabled by stronger and lighter valve trains. Other fine-tuning improvements to the Gen IV motors include reduced internal friction through things like piston rings with less spring tension.
In order to accommodate the new technologies like AFM, the Gen IV motors have several subtle differences from the Gen III’s.
- A "lifter oil manifold assembly" (LOMA) was installed in the valley under the intake manifold in place of the conventional engine block cover used on the Gen III. As a result, the knock sensors were moved to the left and right sides of the block and the cam position sensor was moved from the rear of the block to the front cover.
- The cam sprocket was redesigned to provide the signal for the cam sensor.
- A new high-volume oil pump replaced the original design.
- Additional oil galleys in the block were added to provide high pressure oil to the LOMA.
Details of the Gen IV advanced technologies like AFM and VVT will be described shortly.
Some of the most common or desirable Gen IV motors include the:
- LS2 – 6.0L aluminum block used in Corvette, GTO, CTS-V, and SSR.
- LS3 – 6.2L aluminum block used in Corvette.
- LS7 – 7.0L aluminum block used in Corvette.
- LS9 – 6.2L supercharged aluminum block used in Corvette.
- LH6 – 5.3L aluminum block truck motor.
- LY6 – 6.0L iron block truck motor.
- L76 - 6.0L aluminum block truck motor.
- L92 – 6.2L aluminum block truck motor.
LSX, LSx, LS(X)?
As previously mentioned, the industry has tended to use the designation “LS” to refer to any Gen III or Gen IV motor. From this grew the tendency to use the term LSX where X was intended to be a “variable” (like in algebra) to mean any number. Thus, the term LSX could refer to any motor who’s RPO started with the letters LS. In other words: LS1, LS2, LS3, LS4, LS6, LS7, or LS9 could all be referred to as being an “LSX”. Alternatively, the whole group could be collectively referred to as the “LSX motors”.
The only problem with this method is that there is an actual engine, or more accurately an engine block, whose actual real name is “LSX”.
Introduced in 2006, the LSX is a special cast-iron racing block based on the aluminum Gen IV LS7 engine block. Designed in conjunction with NHRA legend Warren “The Professor” Johnson, it offers displacements ranging from 364 cubic inches to 511 cubic inches. Capable of withstanding up to 2500 bhp, it is available from GM Performance Parts and has the following specs:
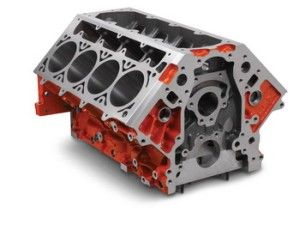
Photo © GM Corp. |
LSX Tall Deck Block
- 3.990' finished siamese cylinder bores (ready to be honed to your specifications)
- 9.70 semi-finished standard deck height (ready to be decked to your specifications)
- Max 4.50 recommended stroke (some additional machining required)
- Capable of 364 to 500+ cid (some machining may be required)
- Orange powder coat finish
- Accepts all Gen III & IV LS heads, cranks, cams, etc.
- Approximate finished weight : 250 lbs.
|
So, there is some possible confusion if one refers to the “family of Gen III and IV V8 motors having RPO codes starting with LS” as “LSX”. In order to avoid confusion, possible alternatives might be to place the X in brackets when referring to the Gen III/IV motors, as in: LS(x), or to simply use the term “LS motors”.
There, I feel better just for having pointed that out.
Vortec
Just to add to the confusion – something GM is almost as good at as building engines – we also have to deal with the name “Vortec”.
Vortec is a trademarked name that GM uses in its line of truck engines. There are no Vortec car engines and never have been. The name has been used by GM to describe truck motors since Gen I, and continues to be used to this day. The name first appeared in 1986 on a 4.3L V6. Vortec engines are named for their approximate displacement (in cubic centimetres for Gen I Vortecs and in litres for the Gen III/IV engines). For example, the Vortec 5700 (RPO L31) is a Gen I 5.7L V8 truck engine. The Vortec 5700 also happens to be the last production Gen I small-block from Chevrolet, last produced for the 2000 model year C-K series pickups (it’s also the basis for the Ramjet 350 crate engine). A 2008 “Vortec 6.0L” could refer to either an iron block (RPO LY6) or an aluminum block (RPO L76) V8 truck motor.
Ramjet 350 - GM Performance Parts small-block V8 crate engine, based on the Gen I "Vortec 5700" (L31). |
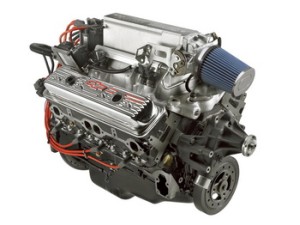
Photo © GM Corp. |
In other words, there are Gen I Vortec truck motors, Gen III Vortec truck motors, and Gen IV Vortec truck motors. Obviously they are very different motors. The problem is, given people’s tendency to shorten or abbreviate things, many folks use the term “Vortec” in isolation, as in: “it’s a Vortec motor”, which doesn’t really mean much because it could be a Gen I, III, or IV. In reality, the word “Vortec” should be read as meaning only “GM truck engine”. More info is needed to narrow down what it is – it could be anything from a 1996 all-iron Gen I SBC, all the way up to the 2008 6.2L all-aluminum Gen IV L92 with variable valve timing technology.
_resize.jpg)
Photo © GM Corp. |
2007 Gen IV "Vortec 5.3L" - all-aluminum truck V8, RPO LC9. |
As such, my recommendation is to always refer to any engine by its specific year and RPO (it’s an ’05 LS2) or at least its generation and displacement (it’s an ’06 Gen III 6.0 litre).
In the latter case, if the listener knows a thing or two about the Gen III and IV motors they would know that their were three 6.0L V8’s in 2006, two iron-block Gen III truck motors (LQ4 and LQ9), the other an aluminum block Gen IV car and truck motor (LS2). Therefore, by saying Gen III 6.0L we would know it’s an iron-block truck motor (either the LQ4 or LQ9), because the aluminum LS2 is a Gen IV. But you can see this is already getting complex – which is why it would be better to always use the RPO, and say, for example, “it’s an ’06 LQ4”, and if the listener goes “huh?” then add, “Gen III iron block 6.0L truck motor”.
Common Features of the Gen III / IV Design / Architecture
In this section, the following paragraphs detail the basic design elements of the first Gen III engine – the famous LS1. Where comparative descriptions are made, they are to be read as “in comparison to the earlier Gen I/II small block designs” which preceded the Gen III LS1. Because of the common architecture approach that was taken with Gen III/IV development, all later Gen III and IV engines that follow the LS1 will share these same design elements, except where specifically noted in the later sections on individual engines. To underscore this point (one of the greatest features of these engines), many of the pictures used in this section to illustrate these design elements and features are of much later engines like the 2009 LS9 – produced 12 years after the original LS1. Basically, this section describes the features and design elements common to the family of Gen III/IV small block V8’s, especially as they compare to the original small-block design. This is what makes a Gen III/IV motor a Gen III/IV motor:
Block
The geometry of the cylinders was changed to provide a slightly smaller bore and longer stroke than Gen I/II motors. This design creates more area between the cylinders for rigidity, durability and cooling.
The LS1 engine block is designed to be more rigid, based on its overall shape, to help reduce the effects of combustion heat and energy which can bend and distort an engine block and generate noise and vibration.
Typically, an engine block ends at the centreline of the crankshaft. The LS1 has a “deep skirt” that extends down past the main bearing caps. Two bolts were added that tie the bearing caps directly into the engine block from the side, for greater durability as well as reduced noise and vibration. The 6 main-bearing cap bolts are 4 x 10mm bolts vertically, and two 8mm bolts horizontally, or “cross-bolted”.
Early LS1 blocks have machined holes through the main webs in the block between the cylinder bores for crankcase bay-to-bay breathing. LS6 and all later blocks have cast-in ports for bay-to-bay breathing. These windows or ports are very important for allowing the oil vapour to move around in the bottom end at high RPM without creating excessive back-pressure against the pistons during their down-travel strokes.
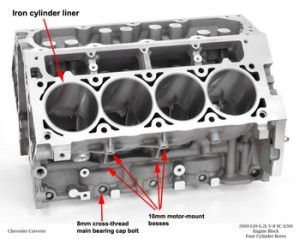
Photo © GM Corp. |
Some features of the Gen III/IV engine block. |
Top arrow indicates the engine block crankcase breathing hole.
Note also the "deep-skirt" design and the 6-bolt cross-bolted main bearing caps in place. |
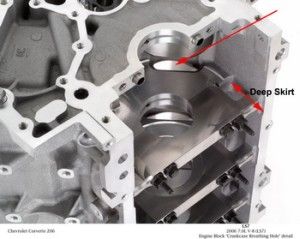
Photo © GM Corp. |
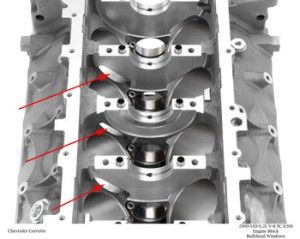
Photo © GM Corp. |
Crankcase breathing holes, aka bulkhead windows, for improved "bay-to-bay" breathing. |
Crank & Pistons
The crank featured larger main bearing journals. The connecting rods are made with an innovative new process with powdered metal, forged and then shot-peened. These rods are stronger and more balanced that previous methods would allow.
Gen III/IV engines have “cracked” connecting rods. They are called “cracked” because, after the rod is created, a groove is machined into the ID of the big end, and then a side-load is applied until the big end cracks into two pieces – the rod and the cap. Because of this process, the two halves have jagged micro edges that mate perfectly and lock tightly together.
Thanks to uniform cylinder bores that result from the new 4-bolt head design (see below), LS1 pistons are able to use piston rings with less tension than previous designs, reducing friction and improving fuel economy. LS1 pistons and rods are lightweight, enabling higher engine RPM.
Detail of "cracked" big end of connecting rod. |
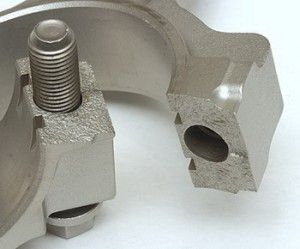
Photo © GM Corp. |
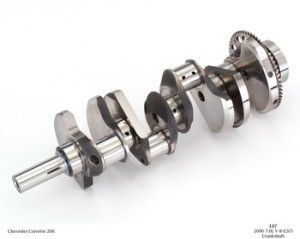
Photo © GM Corp. |
Crank. This one from the Gen IV 7.0L LS7 |
Piston and connecting rod. This particular example a forged titanium piece from the 2006 Corvette Z06 7.0L aluminum LS7. |
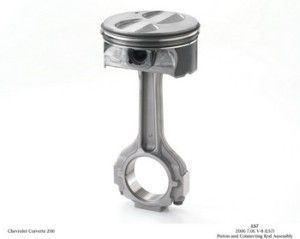
Photo © GM Corp. |
Cylinder Heads
Gen III/IV cylinder heads use “replicated ports” to optimize airflow into the engine. Replicated ports are identical in every detail, allowing for consistent cylinder-to-cylinder airflow distribution. The incoming air also has a “straight shot” into the combustion chamber.
A four-bolt cylinder head design is used for Gen III/IV, rather than the five-bolt design used in previous years. This four-bolt design virtually eliminates bore distortion. Head bolts are threaded deeply into the block, resulting in better sealing, less friction and enhanced fuel economy.
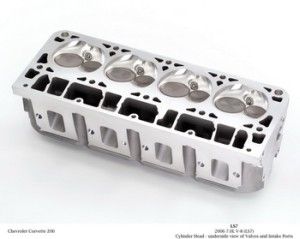
Photo © GM Corp. |
Gen IV LS7 cylinder head with "replicated" intake ports. |
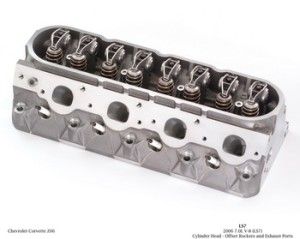
Photo © GM Corp. |
Replicated exhaust ports on the Gen IV LS7. |
Intake Manifold
LS1 uses a composite thermoplastic intake manifold that is strong, yet lighter than aluminum. The composite material is smoother and runs cooler, and allows high-density intake air to flow with less restriction through the tubular intake manifold. This new intake design enhances performance and reduces mass. This design allows for perfectly equal length and volume intake runners, smoother runner walls and better manufacturing economics over previous cast steel and aluminum styles.
Gen III LS6 5.7L bare "intake manifold".
The design is very lightweight, being made from about 8lbs of injected nylon composite. |
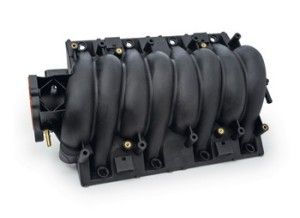
Photo © GM Corp. |
Intake manifold with throttle body and fuel rails. This assembly GM calls the IAFM for "integrated air/fuel module". |
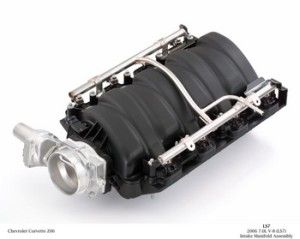
Photo © GM Corp. |
Valvetrain
The LS1 valvetrain offers significant performance benefits and quieter operation.
- Hollow steel camshaft takes mass out of the engine for "lighter equals faster" performance.
- The valves, rocker arms and push rods are all positioned inline, eliminating the compound angles of the previous design that can add to valvetrain stress.
- The camshaft has larger bearing journals that allow larger lobes, reducing lobe stress for greater durability.
- Cast-steel roller rocker arms add stiffness to the valvetrain structure, reducing friction and enabling higher engine speeds. Rocker ratio is 1.7:1
- Hydraulic roller valve lifters also help to minimize friction and eliminate internal power loss. This also maximizes fuel economy and improves wear resistance over time.
- Beehive oval-wire chromium-silicate valvesprings. The beehive shape eliminates the need for a damper spring inside the main spring, and the oval wire helps to improve high-rpm valve control.
A roller timing chain with nylon tensioners improve engine sound quality.
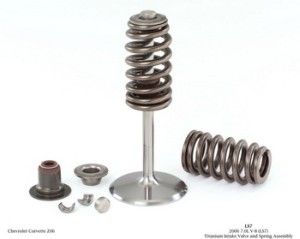
Photo © GM Corp. |
Intake valve and spring. |
Rocker arms. |
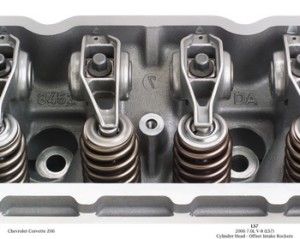
Photo © GM Corp. |
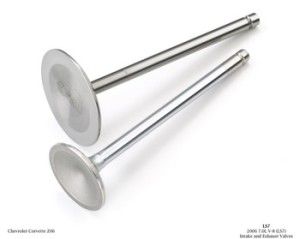
Photo © GM Corp. |
Intake and exhaust valves. |
"Gun-drilled" (hollow) billet steel camshaft - this one from the LS7. |

Photo © GM Corp. |
Accessory Drive
The Gen III/IV accessory drive system was developed with quality, reliability and durability in mind, as well as low noise and vibration. Direct-mount accessories eliminate bolts and brackets, helping to reduce engine noise and enhance durability.
The design also lends itself well to custom mixing and matching of components to suit specific needs.

Photo © Lonny Handwork. |
Custom hybrid Gen III/IV accessory drive system mixing Gen III LS1 parts with a Gen IV LS2 - built to customers spec by Turn Key Engine Supply. |
Oil System
The LS1 oil pan has a unique shape and is made from lightweight cast aluminum. It features extended sumps that contain additional oil to ensure a good supply of oil to the pick-up tube. Other benefits of the LS1 oil pan include better sealing and greater structural integrity over previous generations. The deep skirt LS1 has a large flat surface to which the oil pan is bolted, eliminating curves and corners that are hard to seal. The specially shaped oil pan is also a structural member, enhancing overall engine rigidity.
The LS1 incorporates a high-efficiency Gerotor oil pump, driven off the front of the crankshaft, eliminating the old cam-driven design.
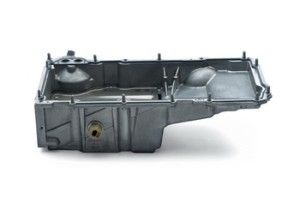
Photo © GM Corp. |
LS1 Camaro cast aluminum oil pan. |
Gerotor oil pump.
(This one happens to be from the LSA) |
5_resize.jpg)
Photo © GM Corp. |
Ignition System
LS1 uses a new coil-per-cylinder ignition system comprised of eight individual coils attached to the two aluminum rocker covers. Each coil is located near its spark plug for high ignition energy, which results in more efficient combustion and better performance. The electronic spark timing signals for the coils originate from the crankshaft and camshaft position sensors enabling high-accuracy spark delivery and misfire detection. Electronic Spark Control sensors (knock sensors), located in the valley of the block, help reduce spark knock or “pinging”.
The firing order of the LS1’s ignition, and all Gen III/IV engines, is 1-8-7-2-6-5-4-3 for better idle stability and reduced vibration.
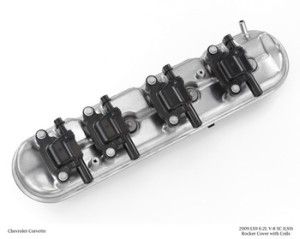
Photo © GM Corp. |
Individual (per cylinder) coil-near-plug ignition coils mounted to the rocker cover. |
Individual coils mounted very close to spark plugs. |
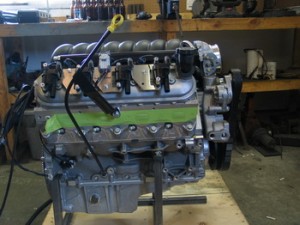 |
Fuel Injection
The LS1 incorporates Sequential Fuel Injection (SFI). SFI is a very precise fuel delivery system which uses one injector and nozzle per cylinder and where the ECM controls the fuel injectors individually. Each of the eight injectors are fired sequentially, one at a time, in a sequence that matches the firing order, timed to the intake cycle for accuracy and metering control. This design improves fuel timing for optimum combustion. The fuel is precisely metered, taking into account several engine operating parameters. With non-SFI, or “batch fire” fuel injection, fuel is injected through all injectors at the same time, once per engine revolution. With SFI, the fuel injection timing is much more precise, improving performance throughout the engine’s range. A mass airflow meter constantly measures the engine’s air requirements under varying conditions, such as changes in load, altitude and temperature and sends this data to the ECM which uses it do determine how much fuel to inject (by controlling how long the injector opens). The injector nozzle’s design and optimum location produce a highly effective spray pattern. In all, SFI offers great idle stability, performance, durability, fuel efficiency and driveability.
Oiling
The Gen III/IV oiling system goes like this:
Oil pan – pickup tube – crank driven gerotor pump – main oil galley (driver’s side of block) – oil filter – up rear driver’s side of block – main feed galley (runs through the lifter bodies) – up to top of engine through pushrod passages – drains back to pan through drain-back passages throughout the heads and block – oil pan.
Cooling
Gen III/IV cooling is slightly different from previous small blocks. The flow path is the traditional “out at the top, return at the bottom” style as found on Gen I small blocks, but the thermostat is on the inlet (return) side of the engine (instead of at the engine outlet as on traditional SBC’s). This means the coolant circulates through the engine and heater core until the the engine comes up to temperature, at which time the thermostat opens and coolant circulates back into the engine from the radiator. Steam ports in the top of the engine are necessary to help eliminate steam pockets and ensure there are no localized hot spots that can lead to pre-ignition and detonation.
Specs
All Gen III and IV V8’s share these common specs
Arrangement |
Longitudinal 90° V8* |
Valves |
Overhead valves (2 valves per cylinder)# |
Valvetrain |
Hydraulic roller |
Fuel System |
Sequential fuel injection |
Intake |
Composite thermoplastic |
Main bearing caps |
6-bolt cross bolted |
Oil Pan |
Structural, cast aluminum |
Ignition |
Coil-near-plug |
Firing Order |
1-8-7-2-6-5-4-3 |
* Except certain 4.4L and 4.6L “Northstar” Cadillac engines and the 4.8L LS4 that were transverse motors (engine sits in chassis sideways, with crank orientation side-to-side) for use in front-wheel-derive (FWD) cars.
# Except certain 4.4L and 4.6L “Northstar” Cadillac engines that were DOHC.
Gen III / IV Benefits Over Gen I/II
There are dozens of Gen III and IV GM V8 engines to choose from – but what makes them all so special, so much more attractive than a well-built version of a Gen I or II motor?
The reason Gen III and IV engines are so superior to the earlier Gen I/II engines is because, compared to the earlier motors, the Gen III/IV engines feature:
- decreased rotating mass for quicker revs
- decreased ring friction, yet with better oil / compression control
- a deeper engine skirt for increased engine rigidity leading to a decrease in distortion and less noise, friction, vibration, and wear
- six-bolt main bearing caps instead of two- or four-bolt caps
- vastly improved head designs increasing volumetric efficiency and creating more power at all engine speeds
- quieter and more efficient valve train operation
- a new firing order for smoother idle and less vibration throughout the operational range
- elimination of Exhaust Gas Recirculation on most Gen III/IV engines by achieving more complete combustion
- coil-near-plug ignition using shorter plug wires with less resistance
- one coil per spark plug so that individual cylinder timing can be tuned via the ECM using knock sensing
- powerful and reliable engine control module (ECM) computer technology giving the ability to control and tune all engine processes and parameters
- throttle-by-wire capability (in most models) for driveability and traction control
- all models are internally balanced without any need for balance shafts, etc.
- better sealing methods at the engine's covers and mating components
- advanced technologies such as AFM (DOD), and VVT for increased fuel economy and decreased emissions
- the same overall size as the original small block, offering tremendous power output for such a compact size
- All-aluminum versions significantly lighter than previous generation motors (approx 90 lbs lighter)
- 400,000 mile longevity design
Gen IV advanced technologies - AFM and VVT
Active Fuel Management
AFM, also known as Displacement on Demand (DOD), temporarily de-activates four of the eight cylinders under light to moderate load conditions. AFM saves fuel by using only half of the engine’s cylinders during some driving conditions, and seamlessly reactivates the other cylinders when a driver demands full power for acceleration.
AFM automatically shuts down every second cylinder, according to firing order, during light-load operation. In engineering terms, this allows the working cylinders to achieve better thermal, volumetric and mechanical efficiency by reducing heat loss, combustion loss and friction, and lowering cyclical combustion variation from cylinder to cylinder. AFM is designed to deliver better fuel economy and lower operating costs. Active Fuel Management relies on three primary components: De-Ac (for deactivation), or collapsible, valve lifters, a Lifter Oil Manifold Assembly (LOMA), and the ECM.
When loads are light, the E38 ECM automatically closes both intake and exhaust valves for half of the cylinders and cuts fuel delivery to those four. The valves re-open to activate all cylinders when the driver demands brisk acceleration or full torque to move a load. The engine’s electronic throttle control (ETC) is used to balance torque following cylinder deactivation or reactivation. The transition takes less than 20 milliseconds, and can’t be detected by the driver.
In the L76 Gen IV V8, the De-Ac lifters are installed in cylinders 1, 4, 6 and 7, while the remaining cylinders use conventional lifters. The hydraulically operated De-Ac lifters have a spring-loaded locking pin actuated by oil pressure. For deactivation, hydraulic pressure dislodges the locking pin, collapsing the top portion of the lifter into the bottom and removing contact with the pushrod. The bottom of each De-Ac lifter rides up and down on the cam lobe but the top does not move the push rod. The valves do not operate and combustion in that cylinder stops. During reactivation, the oil pressure is removed, and the lifter locks at full length. The pushrods, and therefore the valves, operate normally.
The final AFM component is the LOMA. This cast-aluminum assembly is installed in the valley of the engine in place of a conventional engine block cover. The LOMA holds four solenoids, control wiring and cast-in oil passages. The solenoids are managed by the ECM, and each one controls oil flow to a De-Ac Lifter, activating and de-activating the valves at one cylinder as required for Active Fuel Management.
Variable Valve Timing
The Gen IV Vortec 6.2L brings cam-in-block variable valve timing (VVT), or cam phasing, to the small block V8. VVT eliminates the compromise inherent in conventional fixed valve timing and allows a previously unattainable mix of low-rpm torque, even torque delivery over a broad range of engines speeds, and free-breathing high-rev horsepower.
The cam-phasing system in the Vortec 6.2L is similar in concept to that introduced in GM’s 3.9L and 3.5L V6 car engines for 2006. The 6.2L’s dual-equal cam phaser adjusts camshaft timing at the same rate for both intake and exhaust valves. A vane-type phaser is installed on the cam sprocket to turn the camshaft relative to the sprocket, thereby adjusting the timing of valve operation.
The vain phaser is actuated by hydraulic pressure from engine oil, and managed by a solenoid that controls oil pressure on the phaser. The phaser uses a wheel or rotor with four vanes (like a propeller) to turn the camshaft relative to the cam sprocket, which turns at a fixed rate via chain from the crankshaft. The solenoid directs oil to pressure points on either side of the four phaser vanes; the vanes, and camshaft, turn in the direction of the oil flow. The more pressure, the more the phaser and camshaft turn. The Gen IV Vortec 6.2L’s new E38 engine control module directs the phaser to advance or retard cam timing, depending on driving demands. The dual-equal phaser can turn the camshaft over a range of 31 degrees relative to the cam sprocket (or 17 degrees advance, 45 degrees retard relative to the crank).
The benefits are considerable. The cam phaser changes valve timing on the fly, maximizing engine performance for given demands and conditions. At idle, for example, the cam is at the full advanced position. This allows exceptionally smooth idling. Under other operating demands, the phaser adjusts to deliver optimal valve timing for performance, driveability and fuel economy. At high rpm it might retard timing to maximize airflow through the engine and increase horsepower. At low rpm it can advance timing to increase torque. Under a light load (say, casual everyday driving), it can retard timing at all engine speeds to improve fuel economy. Without cam phasing, a cam design must be biased toward one strength or another—high-end horsepower or low-end torque, for example—or profiled at some compromise level that maximizes neither.
Variable valve timing allows linear delivery of torque, with near-peak levels over a broad rpm range, and high specific output (horsepower per litre of displacement) without sacrificing overall engine response, or driveability. It also provides another effective tool for controlling exhaust emissions. Because it manages valve overlap at optimum levels, it eliminates the need for an Exhaust Gas Recirculation (EGR) system.
The Car Motors.
All Gen III and IV V8’s having RPO’s starting with “LS” are all-aluminum car motors except that the LS2 was also used in Chevy SSR sport trucks and and Chevy Trailblazer SS / Saab 9-7X Aero sport utilities. The LS motors were most often used in the Chevrolet Corvette, but also see use in other premium performance cars such as the “F-body” Camaro and Firebird, Pontiac GTO, and Cadillac CTS-V. On the flip side, all cars using Gen III/IV motors use “LS” motors, except the 2008-09 Pontiac G8 GT which uses the all-aluminum L76 6.0L (also used in 2007+ trucks) and the 2009+ Cadillac CTS-V which uses the brand new supercharged all-aluminum 6.2L LSA designed specifically for that car. Nothing’s ever easy!
Car Motors At a Glance
RPO |
Gen |
Displ. |
Power |
Applications |
Notes |
LS1 |
III |
5.7L |
305-350 hp / 335-375 lb-ft |
97-04 Corvette
98-02 Camaro / Firebird
04 GTO |
Original Gen III |
LS2 |
IV |
6.0L |
390-400 hp / 395-405 lb-ft |
05-07 Corvette
05-06 GTO
06-07 CTS-V
05-06 SSR
06-08 Trailblazer SS
08+ Saab 9-7X Aero |
Replacement for LS1 |
LS3 |
IV |
6.2L |
430 hp / 424 lb-ft |
08+ Corvette
2010 Camaro |
Replacement for LS2 |
LS4 |
IV |
5.3L |
303 hp / 323 lb-ft |
05-08 Pontiac Grand Prix GXP
06-09 Chevrolet Impala SS
06-07 Chevrolet Monte Carlo SS
08-09 Buick Lacrosse " Super" |
Transverse for FWD car |
LS6 |
III |
5.7L |
385-405 hp / 385-400 lb-ft |
01-05 Corvette Z06
04-05 Cadillac CTS V |
H.O. Version of LS1 |
LS7 |
IV |
7.0L |
470 hp / 505 lb-ft |
06-08 Corvette Z06 |
Replacement for LS6
Dry Sump |
LS9 |
IV |
6.2L |
638 hp / 604 lb-ft |
09 Corvette ZR1 |
Replacement for LS7
Supercharged |
LSA |
IV |
6.2L |
556 hp / 551 lb-ft |
09+ Cadillac CTS-V |
Similar to LS9
Supercharged
For Cadillac CTS-V |
L76 |
IV |
6.0L |
361 hp / 385 lb-ft |
08-09 Pontiac G8 GT |
Cross between truck L76 and LS3
For Pontiac G8 GT |
Car Motors in Detail
LS1
Generation: III
Type: 5.7L All Aluminum V8
Platform: Car
First Year: 1997
Purpose: Original Gen III V8 to power 1997 Corvette
Description:
Output |
305 - 350 hp / 335-375 lb-ft, depending on application |
Displacement |
5665cc (346 ci) |
Compression Ratio |
10.1:1 |
Valves |
2.00” hollow stainless steel intake / 1.55” sodium-filled stainless steel exhaust |
Bore x Stroke |
99 x 92mm |
Block |
Deep skirt cast 319-T5 aluminum |
Cylinder Head |
Cast 356-T6 aluminum, symmetrical ports, square 4-bolt pattern |
Main bearing caps |
6-bolt powder metal |
Crank |
Cast nodular iron, internally balanced, with undercut and rolled fillet journals |
Camshaft |
Gun-drilled billet 5150 steel with hydraulic roller lifters and roller-bearing-pivot rockers |
Connecting Rods |
Cracked, hot-forged powder-metal of steel alloy |
Pistons |
Mahle flat-top, cast eutectic M124 aluminum/silicon alloy |
LS1 - 2004 Corvette
 for Chevrolet Corvette 2004_5_7L_V8_LS1_Y_resize.jpg)
Photo © GM Corp.
|
LS1 - 2004 Pontiac GTO
 for Pontiac GTO X04PT_8C012_resize.jpg)
Photo © GM Corp.
|
Notable Features:
Launched in the 1997 C5 Corvette, the 5.7L LS1 moved cam-in-block overhead-valve V8 engine design into a new era, as described above.
LS1 air conditioning compressor is mounted on the lower right side of the engine and uses a separate drive belt for efficient packaging and noise reduction (7 db).
Changes to the 2000 LS1 include:
- Revised engine block - a new cored rear cover oil passage improves engine oil distribution and flow
- New progressive throttle cam replaces linear design
- New engine rear cover
- Water pump and one-piece pulley drive
- Improved high flow air pump
- Revised EGR pipe
- New starter motor and heat shield.
Changes to the 2001 LS1 include
- Higher-flowing intake from the LS6 with increased plenum volume and smoother-flowing intake runners. This increased volume of air, delivered to the combustion chamber with less turbulence, allows camshaft lift and overlap to be moderated
- Revised camshaft to broaden the torque curve
- EGR system removed from F-body LS1 (97-00 Corvette LS1 never used an EGR system)
- Revised block is very similar to that of the higher-output LS6; beginning in 2002, some LS1 engines were actually built using the LS6 block instead (there is no performance gain to this block).
In 2001, GM - for the first time since 1955 - changed the crank depth and its pilot bore diameter of the Gen. III. Pilot bushings differ for these motors and transmissions built from this time forward had a deeper bellhousing and different torque converter.
Camaro / Firebird LS1’s have an F-body specific oil pan and accessory drive package.
GTO LS1s camshaft is the same as the Corvette LS1 cam.
The GTO, Camaro, and Firebird LS1s uses a mechanical throttle body rather than the Corvette’s electronic throttle control (ETC).
The GTO LS1 requires a unique oil pan with a front sump to clear the GTO’s steering rack. The oil filter moves with it. Baffles and channels in the oil pan have been redesigned to match the GTO’s oil filter location.
The GTO LS1 has application-specific engine mounts, and its accessory drive belt routing is different than the Corvette’s. Because the GTO uses a different power steering pump and different mounting brackets, the drive belt path was adjusted to accommodate these changes.
Applications & Power:
1997-2000 Chevrolet Corvette C5 - 345 hp / 350 ft-lbs
2001-2004 Chevrolet Corvette C5 - 350 hp / 375 ft-lbs
1998-2000 Chevrolet Camaro & Pontiac Firebird - 305 hp / 335 ft-lbs
1998-2000 Chevrolet Camaro SS & Pontiac Firebird Ram Air - 320 hp / 345 ft-lbs
2001-2002 Chevrolet Camaro & Pontiac Firebird - 310 hp / 340 ft-lbs
2001-2002 Chevrolet Camaro SS & Pontiac Firebird Ram Air - 325 hp / 350 ft-lbs
2004 Pontiac GTO - 350 hp / 365 ft-lbs
LS6
Generation: III
Type: 5.7L All Aluminum V8
Platform: Car
First Year: 2001
Purpose: High Output Version of LS1 to power 2001 C5 Corvette Z06
Description:
Output |
385-405 hp / 385-400 lb-ft, depending on application |
Displacement |
5665cc (346 ci) |
Compression Ratio |
10.5:1 |
Valves |
2.00” hollow stainless steel intake / 1.55” sodium-filled stainless steel exhaust |
Bore x Stroke |
99 x 92mm |
Block |
Deep skirt cast 319-T5 aluminum |
Cylinder Head |
Cast 356-T6 aluminum, symmetrical ports, square 4-bolt pattern |
Main bearing caps |
6-bolt powder metal |
Crank |
Cast nodular iron, internally balanced, with undercut and rolled fillet journals |
Camshaft |
Gun-drilled billet steel with hydraulic roller tappets |
Connecting Rods |
Cracked, hot-forged powder-metal of steel alloy |
Pistons |
Flat-top, cast eutectic M142 aluminum/silicon alloy |
LS6 - 2004 Corvette
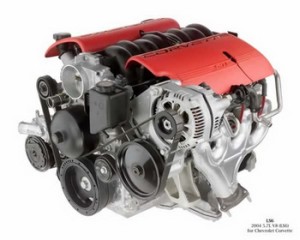
Photo © GM Corp.
|
LS6 - 2005 Cadillac CTS-V
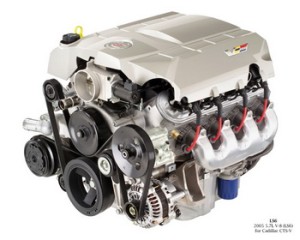
Photo © GM Corp.
|
Notable Features:
The 5.7-liter LS6 builds on the inherent strengths of the Corvette's LS1 engine, but benefits from a higher-lift camshaft and higher-compression pistons to raise HP from 350 to 405, and torque from 340 lb-ft. to 400 lb-ft. Power is produced through the use of hollow-stem valves, a more aggressive camshaft, improved intake and higher-rate valvesprings. Maximum engine speed rises from 6200 to 6600 rpm.
Transforming the LS1 into the LS6 involved dozens of enhancements to increase volumetric efficiency and maximum rpm, starting with an all-new engine block. The aluminum block casting on the LS6 deletes machined holes in the LS1 bulkhead and adds cast in "windows" which allow better bay-to-bay breathing. On the downstroke, the pistons push air back toward the crankcase, creating backpressure or resistance, and that translates into parasitic horsepower loss because it resists piston motion. With the overtravel windows air is allowed to move more freely between crankcase bays thus relieving the unwanted pressure.
The LS6 composite intake manifold is revised and combined with a higher flow MAF-sensor to increase airflow to the cylinder head intake ports.
The LS6 crankshaft features a light-alloy torsional dampener, which balances shaft twist and flex to reduce vibration.
LS6 pistons are cast from high-strength M142 aluminum alloy and reshaped with a slightly different profile than those in the LS1. In side view, the LS6 pistons have a slight barrel shape, almost imperceptible to the naked eye. The new alloy increases engine durability at racetrack operating levels, while the shape reduces internal mechanical noise.
The LS6's aluminum cylinder heads are cast with smaller pent-roof combustion chambers than the LS1. Compression ratio increases from 10.1:1 to 10.5:1, improving thermal efficiency and increasing horsepower. Intake and exhaust ports in the LS6 head are refined and more-precisely cast, contributing to the engine's overall increase in volumetric efficiency.
The LS6-specific, steel-billet camshaft with higher lift and more duration contributes to the LS6's horsepower gain more than any other single piece of hardware. In simple terms, the cam opens the valves quicker and allows more air to flow into the combustion chambers. Cam lift increases from the LS1's 12.7 to 13.3 mm.
To accommodate valve operation with the high lift/high duration cam, the LS6's valve springs are stiffer and sturdier. They are made from the same steel wire as those in the LS1 but are wound tighter for a higher spring rate.
Additional air flowing into the LS6 heads would serve no purpose without an equivalent increase in the amount of fuel to take advantage of it. New injectors increase maximum fuel delivery from the LS1's 3.3 grams/sec to 3.6 grams/sec - a 10 percent improvement.
The LS6's application on the Corvette Z06 creates additional demands on the crankcase ventilation system. The Z06 is capable of cornering at more than 1 lateral "g" requiring a special high-performance ventilation system. To prepare the Z06 for full-on driving, the LS6's PCV system is moved into the engine's V, or valley. The unique aluminum valley cover has composite oil-separating baffles and PCV plumbing incorporated. All of this reduces oil consumption during high-performance driving - and as an added benefit also reduces the amount of external plumbing, eliminating potential oil leak sources.
Applications & Power:
2001 Chevrolet Corvette C5 Z06 – 385 hp / 385 ft-lbs
2002-2005 Chevrolet Corvette C5 Z06 - 405 hp / 400 ft-lbs
2004-2005 Cadillac CTS V- 400 hp / 395 ft-lbs
LS2
Generation: IV
Type: 6.0L All Aluminum V8
Platform: Car
First Year: 2005
Purpose: Gen IV V-8 engine with more power and technical innovation for Corvette, SSR, & GTO, replacement for LS1
Description:
Output |
390-400 hp / 395-405 lb-ft, depending on application |
Displacement |
5970cc (364.3 ci) |
Compression Ratio |
10.9:1 |
Valves |
Hollow stainless steel intake / Sodium-filled stainless steel exhaust |
Bore x Stroke |
101.6 x 92mm |
Block |
Deep skirt cast 319-T5 aluminum alloy, with pressed-in iron cylinder liners. |
Cylinder Head |
Cast aluminum, symmetrical ports, square 4-bolt pattern |
Main bearing caps |
6-bolt powder metal |
Crank |
Cast nodular iron, internally balanced, with undercut and rolled fillet journals |
Camshaft |
Gun-drilled billet steel with hydraulic roller tappets |
Connecting Rods |
Cracked, hot-forged powder-metal of steel alloy |
Pistons |
Flat-top, cast eutectic aluminum |
LS2 - 2005 Corvette
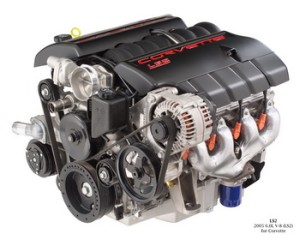
Photo © GM Corp.
|
LS2 - 2005 Pontiac GTO
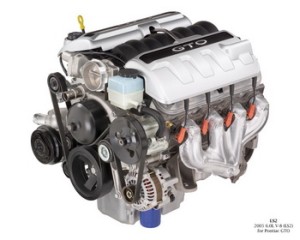
Photo © GM Corp.
|
Notable Features:
A bigger, more powerful next-generation small-block to replace the LS1, the 400-HP LS2 was introduced as the standard engine in the 2005 Corvette as well as the ‘05 Chevy SSR and ‘05 Pontiac GTO. The Gen IV 6.0-liter LS2 builds on the success of the popular Gen III V-8 engine with more displacement, power and technical innovation.
The LS2 features:
- All-new 319-T5 aluminum deep-skirt block casting
- Cylinder head design derived from the Corvette C5R racing program
- Compression raised to 10.9:1
- Camshaft lift increased to take advantage of increased head flow
- Throttle body increased from 75mm to 90mm
- New higher-flow intake
- More powerful ECU incorporates all electronic throttle control functions
The all-new 319-T5 aluminum deep-skirt LS2 block with cast-in-place iron cylinder bore liners and cross-bolted main caps remains precision sand cast, but is strengthened with controlled cooling during the casting process.
The new LS2 heads applied flow characteristics developed in the Corvette C5R racing program. The shape of the combustion chambers was optimized; with new flat-top pistons, the compression ratio increased to 10.9:1 (compared to 10.1:1 in the LS1).
The maximum speed of the engine was increased with stronger valve springs, rising from a redline of 6000 rpm in the LS1 to 6500 rpm in the LS2
A higher-lift camshaft developed to take advantage of the free-flowing cylinder heads was introduced, and the electronic throttle body was enlarged from 75 mm to 90 mm. It is mounted to a new multi-piece welded composite intake manifold tuned to improve airflow.
To improve durability in the bottom end, the LS2 features polymer-coated pistons with floating wrist pins. To reduce friction as the pistons mover through the cylinder bore, piston ring spring tension was reduced.
LS2 displacement was increased over the LS1 through enlarging the bore from 99 to 101.6 mm, and stroke remains the same 92 mm as the LS1.
Power output is measured with premium fuel; however its advanced control system and efficient combustion chamber design allow the LS2 to operate safely on pump fuel as low as 87 octane.
Because it is a Gen IV design, even though it doesn’t feature AFM or VVT, it still features the subtle Gen IV changes explained earlier that accommodate these technologies, like the relocated knock sensors, cam position sensor, and the crankcase vent moved to the top of the valley.
2006 LS2 Improvements
New engine control module
The E38 engine control module (ECM) uses a 32-bit processor, with more memory and a host of advanced features compared to previous controllers, it can handle the advanced computing needs of advanced direct ignition and electronic throttle control. It replaces the previous 24-bit controller.
The 2006+ LS2 as well as all future Gen IV V8’s with ETC and E38 ECM, incorporate the electronic throttle control (ETC) functionality within the ECM, eliminating the separate Throttle Actuator Control (TAC) module used in earlier designs. The previous TAC takes commands from the ECM and then operates the electric motor that opens and closes the throttle. The E38 manages the throttle directly, without a TAC. Eliminating the TAC reduces cost and improves reliability. The direct link between the ECM and the throttle motor improves throttle response time (albeit in millisecond increments that are not apparent to the driver) and improves system security by removing a device (the TAC) that must be monitored for malfunction.
Advanced direct ignition system & improved target ring for camshaft position sensing
The 2006 LS2 incorporates a more advanced timing system, with a 58X crankshaft position encoder and sensor that provide more immediate, accurate information on the crankshaft’s position during rotation. This allows the E38 ECM to adjust ignition timing with greater precision, which optimizes performance and economy. In conjunction with the 58X crankshaft timing, the LS2 was equipped with the latest digital cam-timing technology. The cam sensor was relocated to the front engine cover, and it reads a 4X sensor target on the cam sprocket. The target ring has four equally spaced segments that communicate the camshaft’s position more quickly and accurately than previous systems with a single segment. The dual 58X/4X measurement ensures extremely accurate timing for the life of the engine, and it provides an effective back-up system in the event one sensor fails.
2007 LS2 Updates
Improved Timing Chain Dampener
In 2007 the LS2 timing chain got a new, leaf-spring type dampener to help ensure smooth, quiet operation. The new design maintains optimal chain tension for the life of the engine and eliminates any flapping motion that might develop as the chain stretches with mileage.
Oil Filter with Internal Bypass
The LS2 V8’s oil filter switched to an internal filter bypass in 2007. The bypass is a safety device that protects the engine in the event the filter is neglected for an extended period of time. If the filter becomes completely clogged with debris, the bypass opens and does not allow the filter to restrict oil flow through the engine. Previous LS2s had the bypass mechanism installed in the oil pan. Moving the bypass to the filter insures that the mechanism is fresh and unobstructed each time the filter is changed.
Applications & Power:
2005-2007 Chevrolet Corvette - 400 hp / 400 ft-lbs
2005-2006 Pontiac GTO - 400 hp / 400 ft-lbs
2006-2007 Cadillac CTS-V - 400 hp / 395 ft-lbs
2005 Chevrolet SSR – 390 hp / 405 ft-lbs
2006 Chevrolet SSR - 395 hp / 400 ft-lbs (400 hp / 400 ft-lbs with manual transmission)
2006-2007 Chevrolet TrailBlazer SS - 395 hp / 400 ft-lbs
2008 Chevrolet TrailBlazer SS - 390 hp / 400 ft-lbs
2008- Saab 9-7X Aero - 390 hp / 400 ft-lbs
LS7
Generation: IV
Type: 7.0L All Aluminum V8
Platform: Car
First Year: 2006
Purpose: 7.0L dry-sump, race-ready motor for Corvette Z06, replacement for LS6
Description:
Output |
470 hp / 505 lb-ft |
Displacement |
7008cc (427.6ci) |
Compression Ratio |
11.0:1 |
Valves |
Titanium 2.20 in (55.9 mm) intake / sodium-filled 1.61 in (40.9 mm) exhaust |
Bore x Stroke |
104.775 X 101.6 |
Block |
Deep skirt cast A356-T6 aluminum alloy, with pressed-in iron cylinder liners. |
Cylinder Head |
Cast aluminum, symmetrical ports, square 4-bolt pattern |
Main bearing caps |
6-bolt forged steel |
Crank |
Forged 4140 steel |
Camshaft |
Gun-drilled billet steel with hydraulic roller tappets |
Connecting Rods |
Forged titanium |
Pistons |
Forged hypereutectic aluminum |
LS7 - 2008 Corvette

Photo © GM Corp.
|
LS7 - 2009 Corvette
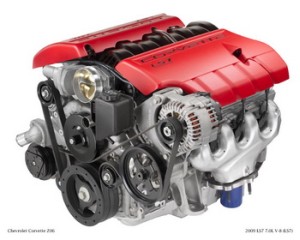
Photo © GM Corp.
|
Notable Features:
Introduced a year after the 6.0L LS2 as a replacement for the 5.7L LS6, the 7.0L LS7 block has a larger bore and longer stroke than the LS2. The crankshaft and main bearing caps are forged steel for durability, the connecting rods are forged titanium, and the pistons are hypereutectic. The two-valve arrangement is retained, though the titanium intake valves by Del West have grown to 2.20 in (55.9 mm) and sodium-filled exhaust valves are up to 1.61 in (40.9 mm).
The LS7 is hand-built by the General Motors Performance Build Centre in Wixom, Michigan for the Corvette Z06, and to be sold as a GM Performance Parts crate engine.
LS7 features:
- Increased displacement to 7.0L
- Maximum engine speed increased
- Low restriction intake and ported cylinder heads
- Valve angle decreased
- Revised pistons and pins
- Lighter connecting rods
- Higher lift camshaft
- Dry sump oil system
To increase the displacement, both the bore and stroke are enlarged over the 6.0L LS2. The 7.0L V8 bore is now 4.125 in (104.9 mm), versus the 101.6 mm of the LS2, and the stroke is now 4.00 in (101.6 mm), versus the 92.0 mm of the LS2. Larger pressed-in cylinder sleeves, versus cast-in for the LS2, required reshaping the block to fit inside. The block features machined bay-to-bay ports between cylinders to improve bay-to-bay breathing and reduce pumping losses. The crankshaft is forged steel with a longer stroke than the LS2.
To reduce weight while increasing strength, the connecting rods are titanium, and are about 27 percent lighter than forged powdered-metal rods used in the LS2. The lighter rods reduce the pressure on the rod end bearings and the main bearings, and allow the bearings to be optimally sized for the least amount of friction. Six-bolt doweled-in-place forged steel main bearing caps hold the balanced crankshaft in place. To reduce weight, tapered piston wrist pins are used. The piston rings are anodized to reduce blow-by and friction. The piston skirts are coated with a polymer to reduce engine noise.
The weight trimming, friction-reducing features in the LS7’s bottom end lower reciprocating mass and contribute to its 500-rprm maximum speed increase over the LS2 - redline is increased to 7000 on the LS7. Fuel shutoff is at 7100 rpm. This engine speed is also significant for an engine with overhead valves, a single cam, and two valves per cylinder.
A new low-restriction intake system is used, with approximately 20 percent less restriction than the intake in the LS2. A new drop-in mass airflow sensor minimizes flow restriction. The intake manifold is a new 3-piece friction welded port-matched composite unit. The large straight intake runners are designed to maintain fast airflow velocity, while air volume increases 18 percent over the LS2.
All new cylinder heads with fully CNC-ported intake and exhaust ports and combustion chambers reduce flow restrictions. High machining consistency aids airflow and allows a higher compression ratio. Valve angles are moved to 12 degrees as compared to the LS2 angle of 15 degrees. The rocker arm ratio increases from 1.7:1 in the LS2 to a 1.8:1 ratio. Valves are larger and taller with titanium intake valves and hollow stem, sodium-filled exhaust valves to optimize heat transfer away from the valve face. Siamesed valve seats are designed similar to those used in the C5R race cars.
The camshaft profile is revised to take advantage of the higher flowing cylinder heads and intake manifold. The new profile provides higher lift than the camshaft in the LS2. The valves also operate at the highest lift of any engine produced by GM. Hydraulic roller lifters with a larger lift ratio actuate the valves.
To improve oil control during high-rpm driving and high lateral acceleration loads, a dual gerotor oil pump is added. The first stage of the pump scavenges the small sump under the engine and delivers it to an eight-quart reservoir. The second stage collects oil from the reservoir and sends it under pressure to the engine. The reservoir is mounted remotely in the engine compartment. The oil cools slightly in the reservoir, and then cools again in an air-to-oil cooler after it is collected by the second stage of the pump. The total oil capacity is 8.0 quarts, 2.5 quarts larger than the capacity of the LS2.
At its introduction, the 7.0L LS7 V8 was the most powerful production small-block V8 ever; with the highest operating speed (rpm) ever; more torque than the high-performance V10 in Porsche’s Carrera GT or the V12 in Ferarri’s 575M Maranello.
Applications & Power:
2006-2008 Chevrolet Corvette Z06 - 470 hp / 505 lb-ft
LS7 Pics:
LS7 Engine Block - Left Front
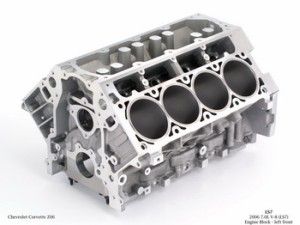
Photo © GM Corp.
|
LS7 Engine Block - Right Rear
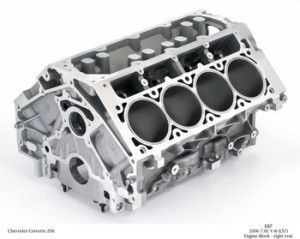
Photo © GM Corp.
|
LS7 Dry Sump Oiling System
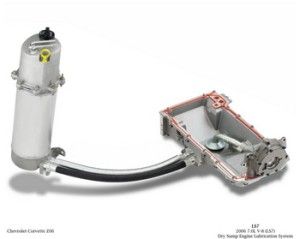
Photo © GM Corp.
|
LS7 Cylinder Head Combustion Chamber
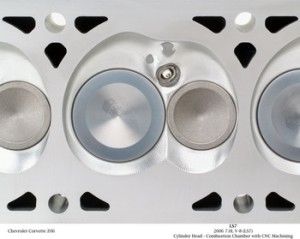
Photo © GM Corp.
|
LS7 Forged Titanium Rod
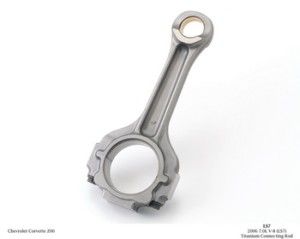
Photo © GM Corp.
|
LS7 Cylinder Head Intake Ports
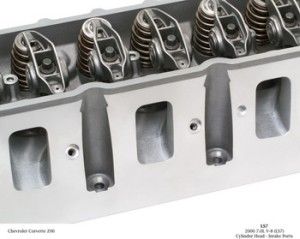
Photo © GM Corp.
|
LS7 Piston
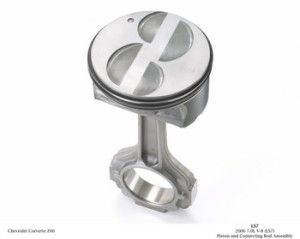
Photo © GM Corp.
|
LS7 Valvetrain
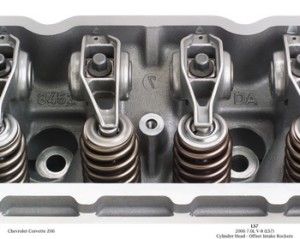
Photo © GM Corp.
|
LS7 Offset Intake Rocker
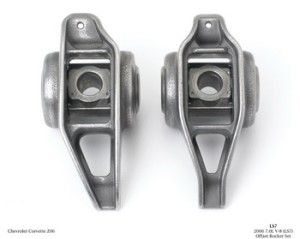
Photo © GM Corp.
|
LS7 Valves
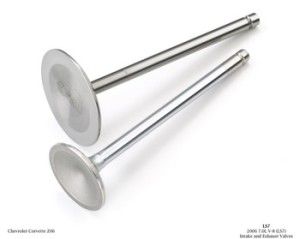
Photo © GM Corp.
|
LS3
Generation: IV
Type: 6.2L All Aluminum V8
Platform: Car
First Year: 2008
Purpose: 6.2L for 2008 Corvette, replacement for LS2
Description:
Output |
430 hp / 424 lb-ft |
Displacement |
6162cc (376.0 ci) |
Compression Ratio |
10.7:1 |
Valves |
2.165 in (55.0 mm) hollow stem intake / sodium-filled 1.59 in (40 mm) exhaust |
Bore x Stroke |
103.25 x 92mm |
Block |
Deep skirt cast A356-T6 aluminum alloy, with pressed-in iron cylinder liners. |
Cylinder Head |
Cast aluminum, symmetrical ports, square 4-bolt pattern |
Main bearing caps |
Powder metal |
Crank |
Cast nodular iron, internally balanced, with undercut and rolled fillet journals |
Camshaft |
Gun-drilled billet steel with hydraulic roller tappets |
Connecting Rods |
Cracked, hot-forged powder-metal of steel alloy |
Pistons |
Flat-top, cast hypereutectic aluminum/silicon alloy |
LS3 - 2009 Corvette
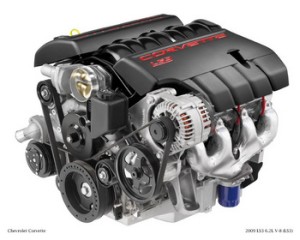
Photo © GM Corp.
|
LS3 - 2009 Pontiac G8 GXP
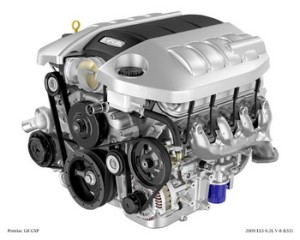
Photo © GM Corp.
|
Notable Features:
The LS3 was introduced in 2008 to replace the LS2 as the Corvette base engine. The 2008 6.2L LS3 V8 with 430 Hp @ 5900 rpm and 424 lb.ft. torque @ 4600 rpm is the most powerful Corvette base engine ever.
LS3 Features:
- Displacement increase to 6.2L from the 6.0L LS2
- Horsepower increase from 400 to 430
- Torque increase from 400 to 424 lb-ft.
- High flow cylinder heads
- Enhanced valvetrain
- Higher flow intake manifold with acoustic shell
- Larger bore block with structural improvements
- New pistons
- Higher flow injectors
The LS3 continues the Gen IV evolution by using multiple design elements to increase flow efficiency, in addition to a displacement increase, to meet the desired performance enhancement over LS2. The bore was increased to a larger 103.25 mm diameter compared to the LS2 bore of 101.6. Engine stroke remains at 92.0mm. Intake flow efficiency was optimized by straightening out and optimizing the flow path from the intake manifold into the cylinder heads. A high flow efficiency induction system is borrowed from the LS7. The cylinder head exhaust ports have been modified to increase flow.
The intake port shape size and shape have been modified to increase flow. The higher flow intake ports are similar to the L92 6.2L. Casting changes were made to increase the opening at the exhaust face to improve exhaust port flow. A new exhaust manifold opening is required to match the heads.
The inlet rocker arm is offset 6 mm between the valve tip and rocker bolt/push rod to enable a more direct intake port. The intake valve diameter is increased from 50.8 to 55.0 mm. Hollow stem intake valves were implemented to enable the 6600 rpm capability (13% reduction in mass from LS2). The 40.4 mm diameter exhaust valves are carried over from L92. Carryover LS2 high load valve springs are also included for 6600 rpm capability. Intake lift increases from 13.25mm to 14.0mm. Exhaust lobes are carryover LS2. Camshaft timing is revised.
Intake ports are revised to match the new cylinder head. The new composite intake manifold is manufactured with a lost core process to improve runner to runner variation and to reduce flow losses. In order to reduce radiated engine noise acoustic foam is sandwiched between the outside top of the intake manifold and an additional “skull cap” acoustic shell. Structural enhancements have been added to the manifold bosses.
The LS3 features an improved block with structural improvements. Casting and machining in the bulkheads was revised to improve block structure and to improve bay to bay breathing. The enhanced block is shared with the 6.2L L92 truck motors.
LS3 uses a new larger diameter piston which includes design enhancements for the higher engine output.
Higher flow 5.0 g/s injectors from the LS7 engine are used in the LS3.
Applications & Power:
2008- Chevrolet Corvette - 430 hp / 424 lb-ft
2009 Pontiac G8 GXP
2010 Chevrolet Camaro
LS9
Generation: IV
Type: 6.2L Supercharge All Aluminum V8
Platform: Car
First Year: 2008
Purpose: For 2008 Corvette ZR1, replacement for LS7
Description:
Output |
638 hp / 604 lb-ft |
Displacement |
6162cc (376 ci) |
Compression Ratio |
9.1:1 |
Valves |
2.165 in (55.0 mm) intake / sodium-filled 1.59 in (40 mm) exhaust |
Bore x Stroke |
103.25 x 92mm |
Block |
Deep skirt cast 319-T7 aluminum alloy, with cast-in iron cylinder liners. |
Cylinder Head |
A356-T6 rotocast cast aluminum |
Main bearing caps |
Forged steel |
Crank |
Forged steel |
Camshaft |
Gun-drilled billet steel with hydraulic roller tappets |
Connecting Rods |
Forged Titanium |
Pistons |
Forged aluminum |
LS9 6.2L Supercharged V8
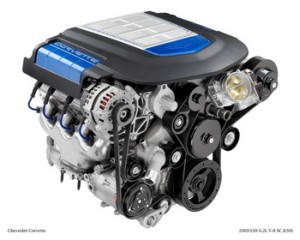
Photo © GM Corp.
|
LS9 6.2L Supercharged V8
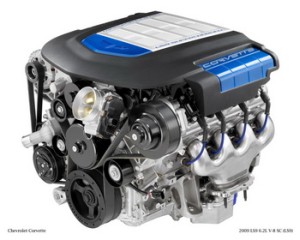
Photo © GM Corp.
|
Notable Features:
Simply put, the supercharged LS9 is the most powerful production engine ever offered by GM Powertrain--a company with a 100-year tradition of building very powerful engines. The LS9 generates 638 horsepower at 6500 rpm and 604 pound-feet of torque at 3800 rpm – yes 3800 RPM!!!! Its specific output of 103 horsepower per litre, or 1.70 horsepower per cubic inch, is remarkable for an engine of its displacement. According to published figures, the LS9-equipped ZR1 has more horsepower and torque than the Dodge Viper SRT10, Ferrari 599 GTB Fiorano, and Porsche 911 GT2 Lamborghini Murcielago LP640— all benchmarks among exotic international sports cars.
The LS9 is a Gen IV 6.2 L supercharged V8 based on the LS3. The reason the LS3 block was used as the basis, and not the 7.0L LS7 block is the higher cylinder pressures created by the supercharger requiring the thicker cylinder walls of the LS3. Cylinder dimensions are now 4.06 in (103.25 mm) bore with a 3.62 in (92 mm) stroke. The LS9 is equipped with an Eaton four-lobe Roots-type 2.3 L/rev supercharger and integrated dual coolant-to-air intercooler. It also features piston oil-spray cooling and direct-mount ignition coils.
LS9 Features:
- Gen VI Supercharger with Twin Four-Lobe Rotors
- Integrated Dual-Brick Air-to-Liquid Intercooler
- Enhanced Gen IV Cylinder Block
- Forged-Aluminum Pistons with Oil-Spray Cooling
- Lightweight Reciprocating Assembly with Titanium Connecting Rods
- Refined Low Overlap Cam
- High-Flow Rotacast Cylinder Heads with High Performance Valves
- Centre-Feed Fuel System
- Direct-Mount Ignition Coils
- E67 Control Module
- Dry-Sump Oiling System
- Heavy-duty Accessory Drive
The LS9 is fitted with Eaton’s twin-rotor R2300 supercharger—one of the company’s Twin Vortices Series (TVS), which displaces 2.3 litres per revolution, compared to more conventional superchargers of 1.5 litres or less. The R2300 in the LS9 generates a maximum boost pressure of 10.5 pounds per square inch (0.72 bar).
A supercharger is essentially an air pump driven by the engine’s crankshaft. It forces more air into the engine’s combustion chambers than that engine could otherwise draw on its own. The increased volume of oxygen allows the engine to efficiently process more fuel, and thus generate more power.
The TVS design is highly refined and efficient. Each of its two rotors has four distinct lobes, or spiral-shaped vanes that intermesh precisely with those on the other rotor as they spin at high speed. Efficiency gains with the four-lobe rotors are substantial, compared to comparably sized, previous-generation superchargers: approximately 20 percent more airflow, with an improvement in thermal efficiency up to 15 percent. Moreover, parasitic power loss—the amount of power the engine uses to operate the supercharger—is reduced 35 percent. That improves both supercharger response time and the engine’s overall efficiency.
Integrated Dual-Brick Air-to-Liquid Intercooler
An advanced intercooling system increases the 6.2L LS9’s performance and extends its supercharger’s benefits. The engine’s charge cooler is integrated in the supercharger case just above the rotors, with two air-to-liquid cooling “bricks” that substantially lower the temperature of air used in the combustion process.
Intercoolers are familiar features on supercharged and turbocharged engines. Similar in concept to an engine’s radiator, intercoolers cool the air pumped by the charging device into the cylinders. Cooler air is denser air, which means more oxygen in a given volume, resulting in optimal combustion and more power. Traditionally, intercoolers look like small radiators mounted somewhere outside the engine, with air fed into the engine through a plumbing network.
The LS9’s intercooling system raises the bar in both packaging and efficiency. It uses two low-profile, aluminum tube-and-fin heat exchangers mounted longitudinally above the rotors in the supercharger case. Air pumped by the supercharger flows directly through these bricks to the intake ports on the cylinder heads. The bricks are cooled by their own coolant circuit, with a remote pump and 3.62-liter capacity heat exchanger mounted in front of the Corvette’s radiator.
Bottom line: The temperature of air fed to the LS9’s cylinder heads is reduced 140 degrees F (60 degrees C), substantially increasing the amount of oxygen available for the combustion process because cooler air is denser air. The intercooler design also contributes to the supercharger’s quiet operation. The cooling bricks help dampen sound radiating from the supercharger case, while ribs cast into the top of the intercooler housing add strength and reduce vibration.
LS9 Supercharger Rotors
7_resize.jpg)
Photo © GM Corp.
|
LS9 Intercoolers
3_resize.jpg)
Photo © GM Corp.
|
LS9 Supercharger
10_resize.jpg)
Photo © GM Corp.
|
LS9 Supercharger
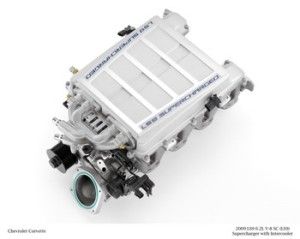
Photo © GM Corp.
|
The original 6.2L Gen IV LS2 block has been further refined for the LS9. It’s cast from 319-T7 aluminum and the cylinder liners are cast in and machined with a deck plate installed over the cylinder bores. The deck plate simulates the pressure and tiny dimensional changes that occur when the cylinder heads are bolted to the block. The process enhances assembly quality and fit, ensuring precise head sealing, improved piston ring sealing and peak performance as the engine accumulates miles.
Bulkheads in the LS9 engine block have been strengthened 20 percent by optimizing the size of the bulkhead “windows” to take advantage of material thickness in the bulkhead. This is additional improvement beyond a 20% gain obtained in the naturally aspirated 6.2L LS3 V-8 by increasing the radius of the hone over-travel fillets from three to 10 millimetres. The enlarged bulkhead windows also improve bay-to-bay breathing by managing airflow inside the engine more efficiently, thereby decreasing pumping loss (reducing resistance to the pistons’ downward movement).
LS9’s six-bolt, cross-threaded main-bearing caps are forged steel, fully machined on all surfaces and dowel aligned for precise fit and minimal vibration.
LS9 Block Crankcase Bulkhead Windows
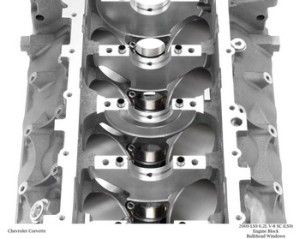
Photo © GM Corp.
|
LS9 Main Bearing Caps
9_resize.jpg)
Photo © GM Corp.
|
LS9 Block Hone Over-travel Fillet
_resize.jpg)
Photo © GM Corp.
|
LS9 Main Bearing Cap studs
11_resize.jpg)
Photo © GM Corp.
|
LS9 Main Cap Dowel
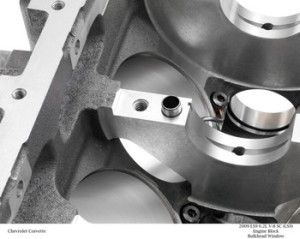
Photo © GM Corp.
|
LS9 Engine Block
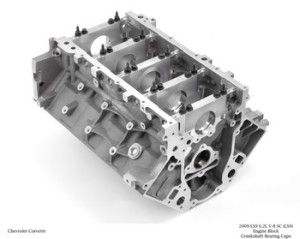
Photo © GM Corp.
|
LS9 pistons are forged aluminum for a high-performance combination of low mass, high strength and durability. These are considerably lighter than conventional aluminum pistons, which translates to less reciprocating mass inside the engine. Less mass means greater efficiency, high-rpm capability and a feeling of immediate response as the engine builds revs.
The combustion surface of the LS9 pistons, or the crown, lacks the valve-relief pockets typical on high-performance engines with relatively high-lift valves. Rather, the LS9 crown is sumped, with a saucer-shaped indent that dips gradually from the outer edge of the piston. This design promotes a thorough mixing of air and fuel and, with other durability enhancing features such as an anodized top ring groove, allows a 9.1:1 compression ratio: higher than a conventional supercharged or turbocharged engine, for improved combustion efficiency.
The anodized top ring groove reduces wear and accepts the heat generated during combustion between the top ring and its groove. To further reduce wear, the piston skirt is coated with a polymer material, which eliminates bore scuffing, or abrasion of the cylinder wall over time from the piston’s up-down motion. The polymer coating also dampens noise generated by the piston’s movement. The tapered wrist pins, which attach the piston to the connecting rod, were developed for maximum durability, and “float” inside the rod bushing and pin bores in the piston barrel. Compared to a conventional fixed pin assembly, in which the connecting rod is fixed to the piston’s wrist pin and the pin rotates in the pin bore, the floating pins reduce stress on the pin. They allow tighter pin to pin-bore tolerances and reduce noise generated as the piston moves through the cylinder. The benefit is less engine wear, improved durability and quieter operation.
LS9 Piston
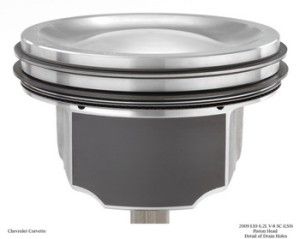
Photo © GM Corp.
|
LS9 Piston and Rod
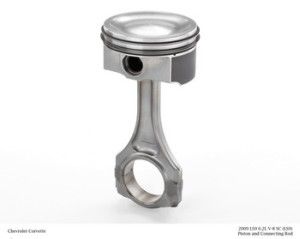
Photo © GM Corp.
|
LS9 Piston and Rod
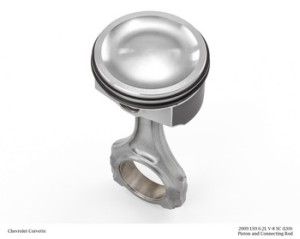
Photo © GM Corp.
|
LS9 Piston and Rod
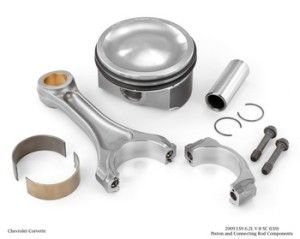
Photo © GM Corp.
|
Finally, the 6.2L LS9 represents the first line of small block V-8s equipped with oil-spray piston cooling. Eight oil-squirting jets in the engine block drench the underside of each piston and the surrounding cylinder wall with an extra layer of cooling, friction-reducing oil. The oil spray reduces piston temperature, promoting extreme output and long-term durability. The extra layer of oil on the cylinder walls and wristpin also dampens noise emanating from the pistons.
LS9 Piston Cooling Oil-spray Jets
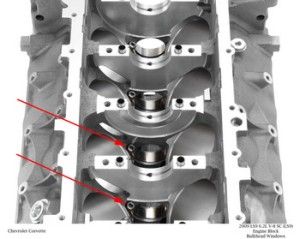
Photo © GM Corp.
|
LS9 Piston Cooling Oil-spray Jets
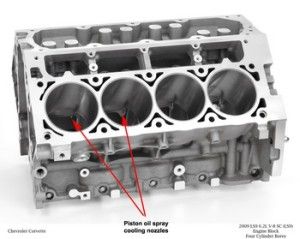
Photo © GM Corp.
|
LS9 Piston Cooling Oil-spray Jet.
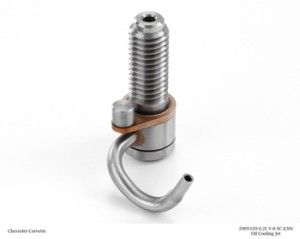
Photo © GM Corp
|
The LS9 uses a balanced, dropped-forged micro-alloy steel crankshaft with a nine-bolt flange to mount the flywheel. The nine-bolt pattern increases clamping strength compared to naturally aspirated 6.2L Gen IV V-8s, which use a six-bolt crank flange. A smaller-diameter ignition-timing reluctor wheel trims weight and ensures clearance to the pistons as they move in the bore. At the front end of the crank, the torsional damper is secured with a keyway and friction washer for an added element of security, given the LS9’s exceptional torque.
LS9 Crank
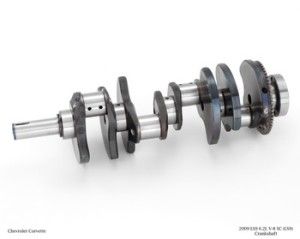
Photo © GM Corp.
|
LS9 Crank Keyway
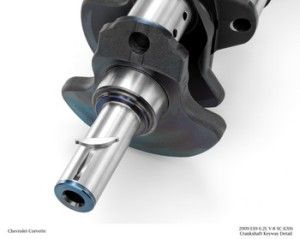
Photo © GM Corp.
|
Titanium connecting rods mate the crank with the pistons, for the ultimate combination of strength and light weight. The titanium rods weigh roughly 25 percent less than conventional iron or steel. They reduce pressure on both the rod-end bearings and main bearings, and allow the bearings to be optimally sized for the least amount of friction.
A refined camshaft is used in the LS9. The torque enhancing benefits of the supercharger allowed GM Powertrain engineers to develop a “softer,” lower-lift camshaft for the LS9, compared to the typical high-rev, high-power exotic car engine. The LS9 cam delivers maximum lift of 14.3 mm for the intake valves and 14.2 mm for the exhaust valves. Moreover, the cam lobes are profiled to reduce the amount of time that both intake and exhaust valves are partially open at the same time. Valve overlap is reduced 27 percent compared to the track-bred 7.0L LS7. The result is smoother operation at low speeds, and particularly at idle. Idle quality improves 11 percent compared to the LS7.
The 6.2L Supercharged LS9 cylinder heads are similar to those used on the naturally-aspirated 6.2L LS3 with enhancements for supercharged induction and maximum durability.
The LS9 heads feature a unique “wing’’ cast into each intake port to promote a swirling motion that blends the pressurized air-fuel charge. The heads are also cast from a premium A356T6 alloy, which better manages the heat generated in a supercharged engine. A356T6 pays particular dividends in the thin bridge area between the intake and exhaust valves, where effective heat dissipation is crucial to both performance and long-term durability. Finally, the LS9 heads are rotocast. This process rotates the head mould as the molten alloy cools and essentially eliminates porosity, or microscopic pockets of air trapped in the casting. Rotacasting delivers a stronger part that helps maintain performance and structural integrity over the life of the engine.
Low-friction hydraulic roller lifters actuate the LS9’s valves, with unique offset rocker arms for the intake valves. On the inlet rocker, the valve tip is offset six millimetres from the pushrod. This configuration allowed Powertrain engineers to locate the intake port for a more direct air-fuel flow into the combustion chamber.
Intake valves measure 55 mm in diameter and are fabricated from titanium—chosen for its combination of strength, light weight and high-rpm potential. Perhaps more crucial to durability are the exhaust valves, which are typically the hottest part in the engine. Those in the LS9 measure 44.0 mm in diameter, and they’re manufactured from a high-chromium steel alloy called SilChrome 1, with hollow, sodium-filled stems. At normal operating temperatures, the sodium inside the valve stem melts and becomes liquid. The liquid sodium improves conductivity, promoting heat transfer away from the valve face to the cooler end of the stem, where it more readily dissipates through the valve guide. This maintains a lower, more uniform valve temperature, reducing wear on the valve seat for a consistent seal between the valve and head over the life of the engine.
Given the LS9’s pressurized induction, Powertrain engineers focused special attention on sealing. Head gaskets are extra-robust, four-layer stainless steel, and the 12 mm cylinder head bolts are hardened stainless. The 12 mm bolts increase head-gasket clamp strength (compared to 11 mm bolts on other small block engines), ensuring gasket sealing under the high combustion pressures generated by the LS9.
LS9 Cylinder Head
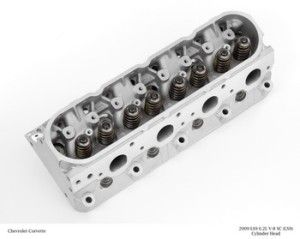
Photo © GM Corp.
|
LS9 Cylinder Head
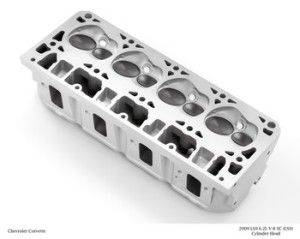
Photo © GM Corp.
|
LS9 Cylinder Head Gasket
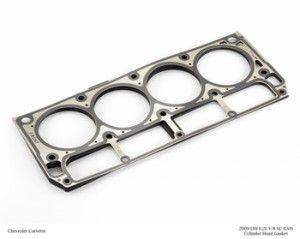
Photo © GM Corp.
|
LS9 Cylinder Head Gasket
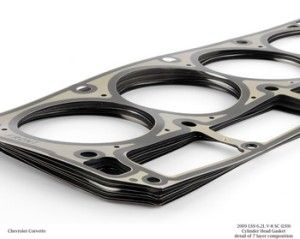
Photo © GM Corp.
|
Centre-Feed Fuel System
The 6.2L LS9’s fuel system was developed to deliver adequate fuel volume precisely consistently and quietly.
To ensure appropriate fuelling in all conditions, from casual cruising to race track-type wide-open throttle, GM has equipped the LS9 with a dual- pressure fuel system. The system delivers 250 kPa (about 36 psi) at idle or low speeds. Yet the electronic throttle management system can almost instantaneously increase fuel pressure to 600 kPa for sustained high-speed operation or wide-open throttle. The dual-pressure system reacts according to throttle application, and presents several advantages. It limits the energy used by the fuel pump at low speeds, for maximum efficiency, and it reduces operational noise. It also ensures adequate fuel delivery when the LS9 demands its maximum flow rate of 58 grams per second.
The LS9 also employs a new centre-feed fuel rail that delivers gasoline to the centre of the injector rail on each bank. The delivery point is roughly equidistant to each of the injectors, which have a maximum flow rate of 6.52 grams per second at 400 kPa. Fuel pressure variation among the injectors is reduced, and so is noise. The rapid ticking sound often generated by fuel injectors is alleviated.
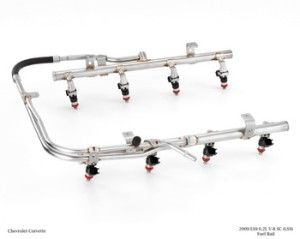
Photo © GM Corp. |
LS9 Centre-Feed Fuel Rail. |
An 87-mm, single-bore throttle body draws air into the engine. The electronic throttle maps have been optimized for excellent response and modulation in a multitude of driving scenarios.
The LS9’s coil-on-plug ignition features advanced coils developed for the 7.0L LS7. These coils are smaller and lighter than those used on previous small-block V8s. The coils mount directly on LS9-specific rocker covers. Those on the LS3 and LS7 are joined by a bracket. The individual LS9 coils provide a cleaner look and a shorter lead between the coil and the iridium-tip, centre-electrode spark plug.
An advanced controller manages the multitude of operations that occur within the 6.2L Supercharged LS9 V-8 every split second. The E67 is the high-line controller in GM’s family of three engine control modules, which was developed to direct nearly all the engines in GM’s line-up. It features 32-bit processing, compared to conventional 16-bit processing, with 32 megabytes of flash memory, 128 kilobytes of RAM and a high-speed CAN bus. The E67 synchronizes more than 100 functions, from spark timing to cruise control operation to traction control calculations.
The E67 also applies a new, rate-based monitoring protocol sometimes known as run-at-rate diagnostics. Rate-based diagnostics improve the robustness of the Onboard Diagnostics System (OBD II) and ensure optimal performance of emissions control systems. The software increases the frequency at which the ECM checks various systems, and particularly emissions-control systems such as the catalytic converter and oxygen sensors.
The LS9 uses the LS7-introduced racing-style dry sump lubrication system and dual-gerotor oil pump. The LS9 version extends the system’s lubricating capability 33 percent. This is accomplished with a larger 10.5-quart reservoir capacity, increased with a 2.5-quart auxiliary tank attached to the main reservoir, and higher-flow, 32.5-gpm gerotor pump. The increased capacity dry sump system is also used on the 2009 LS7.
LS9 Dry Sump Oil Pan with Oil Cooler
2_resize.jpg)
Photo © GM Corp.
|
LS9 Dry Sump Oil Pan with Oil Cooler
5_resize.jpg)
Photo © GM Corp.
|
LS9 Dual-Stage Gerotor Oil Pump
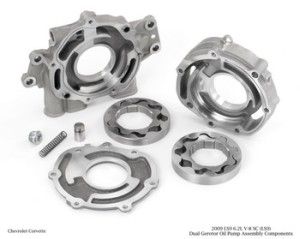
Photo © GM Corp.
|
LS9 Oil Cooler
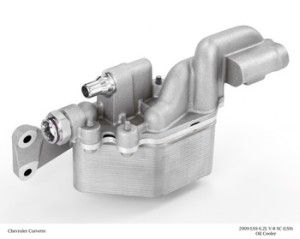
Photo © GM Corp.
|
To tailor the 6.2L LS9 to the Corvette’s engine bay, the supercharger drive is integrated into the main accessory drive system. The LS9’s two-belt accessory drive has one belt turning the air conditioning compressor and alternator, and another operating power steering, the water pump and the supercharger. The supercharger requires the most force to turn, so its circuit uses a wider, 11-rib belt. To compensate, the LS9 water pump has improved bearing capacity. Bearing diameter is increased from 16 mm to 19 mm, compared to the LS7. To allow a common power steering pump with other small block V8’s, the LS9 pump is spline driven through a bracket and bearing system that takes the load off the supercharger.
Applications & Power:
2009+ Chevrolet Corvette ZR1
LSA
Generation: IV
Type: 6.2L All Aluminum Supercharged V8
Platform: Car
First Year: 2009
Purpose: For 2009+ Cadillac CTS-V, similar to LS9
Description:
Output |
556 hp / 551 lb-ft |
Displacement |
6162cc (376 ci) |
Compression Ratio |
9.1:1 |
Valves |
2.165 in (55.0 mm) intake / sodium-filled 1.59 in (40 mm) exhaust |
Bore x Stroke |
103.25 x 92mm |
Block |
Deep skirt cast 319-T5 aluminum alloy, with cast-in iron cylinder liners. |
Cylinder Head |
A356-T6 rotocast cast aluminum |
Main bearing caps |
Nodular Iron |
Crank |
Forged steel |
Camshaft |
Gun-drilled billet steel with hydraulic roller tappets |
Connecting Rods |
Cracked, hot-forged powder-metal of steel alloy |
Pistons |
Cast aluminum |
LSA - 2009 Cadillac CTS-V
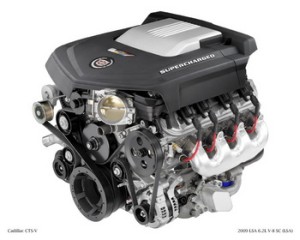
Photo © GM Corp.
|
LSA
 for Cadillac CTS-V - David Kimble Illustration_resize.jpg)
David Kimble Illustration © GM Corp.
|
Notable Features:
The LSA is the most powerful engine ever offered in Cadillac’s nearly 106-year history.
Based on the LS9, the LSA is a slightly lower-tech version designed for the 2009+ Cadillac CTS-V. Design considerations focused more on reducing NVH than did LS9 design, befitting for the intended Cadillac application. Like the LS9 it’s a 6.2 L (6,162 cc/376.0 cu in) supercharged engine, but is equipped with a smaller 1.9L/rev Eaton four-lobe roots-type supercharger. It also has only a single integrated coolant-to-air intercooler compared to the LS9’s dual. The LSA also gives up a few of the 9’s internal goodies, using nodular iron mains instead of forged steel, forged powder metal connecting rods in place of forged titanium, and cast instead of forged pistons. The LSA crank mounts the balancer to an 8-bolt flange compared to the LS9’s 9-bolt. The block is the same design as the LS9 but is cast from 319-T5 aluminum as opposed to the LS9’s 319-T7. The LSA cam is a low lift, low overlap design but delivers maximum lift of 12.2 mm for both the intake and exhaust valves, slightly less than the LS9 cam. However, the LSA shares the LS9’s:
- Hypereutectic Aluminum Pistons with Oil-Spray Cooling
- Lightweight Reciprocating Assembly
- High-Flow Rotacast Cylinder Heads
- Centre-Feed Fuel System
- Direct-Mount Ignition Coils
- E67 Control Module
- Upgraded Oiling System
- Revised Accessory Drive
Because its intended application is the luxury-performance Cadillac CTS-V, as opposed to the all-out performance Corvette ZR-1, the LSA forgoes the latter’s dry-sump oiling system for a more traditional wet-sump arrangement. It has a more powerful oil pump than the naturally aspirated 6.2L LS3, so that pump capacity increases to 33.8 gallons per minute. The LSA’s six-quart oil pan is fitted with a liquid-to-air oil cooler.
The LSA’s accessory drive system accommodates the supercharger with a third track on the crankshaft pulley. The supercharger is operated by its own belt, which is wider than a conventional belt (eight ribs) to turn the rotors without slip. The other drive belts are conventional five-rib widths, with one operating the air conditioning compressor and another operating the water pump, power steering pump and alternator.
2009 LSA Exploded View
4_resize.jpg)
Photo © GM Corp.
|
LSA Engine Block
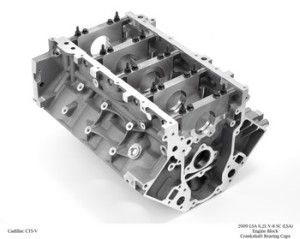
Photo © GM Corp.
|
Applications & Power:
2009+ Cadillac CTS-V - 556 hp / 551 lb-ft
L76 (Car)
Generation: IV
Type: 6.0L All Aluminum V8
Platform: Car
First Year: 2008 (in cars)
Purpose: Cross between truck L76 and LS3 for Pontiac G8 GT
Description:
Output |
361 hp / 385 lb-ft |
Displacement |
5967cc (364 ci) |
Compression Ratio |
10.4:1 |
Valves |
Hollow stainless steel intake / Sodium-filled stainless steel exhaust |
Bore x Stroke |
101.6 x 92mm |
Block |
Deep skirt cast A356-T6 aluminum alloy, with pressed-in iron cylinder liners. |
Cylinder Head |
Cast aluminum, symmetrical ports, square 4-bolt pattern |
Main bearing caps |
6-bolt powder metal |
Crank |
Cast nodular iron, internally balanced, with undercut and rolled fillet journals |
Camshaft |
Gun-drilled billet steel with hydraulic roller tappets |
Connecting Rods |
Cracked, hot-forged powder-metal of steel alloy |
Pistons |
Flat-top, cast aluminum |
Notable Features:
Based on the Vortec 6.0L V8 L76 found in the Chevrolet Avalanche, Silverado and Suburban, and the GMC Sierra and Yukon XL, the 2008+ Pontiac G8 GT L76 has many unique, car-specific modifications and features in this application; many borrowed from the LS3.
- High-Flow cylinder heads with offset rockers and larger valves than truck L76
- No VVT
- Active Fuel Management Calibrated For Pontiac G8 GT Passenger Car
- Structural Cast Aluminum Oil Pan Specific To G8
- Intake Manifold From LS3 Corvette Application
- Induction System Specific To G8
- Advanced Electronic Throttle Control Similar To LS2 & LS3 V8
- Smaller Ignition Coils From LS3 V8
- E38 Engine Control Module
- 58X Ignition System
Structural Cast Aluminum Oil Pan Specific To G8
To facilitate the Active Fuel Management system not used in all L76 applications, an oil return valve was added to the pan.
Intake Manifold From LS3 Corvette Application
Packaging the L76 under the lower hoodline of the G8 GT passenger car required a lower intake system than is used by the engine in truck applications, and so the thoroughly developed intake from the LS3 is used with the car L76.
Electronic Throttle Control from LS3 Corvette Application
The advanced and sophisticated electronically controlled throttle control and integrated cruise control used on the LS3 is also used on the car L76.
High-Flow Cylinder Heads
The Gen IV car L76 is fitted with high-flow cylinder heads that have offset intake rockers like those in the LS3 and LS7. They also have larger valves than the truck Vortec L76 heads used in trucks & SUV’s.
The L76 uses the same Gen IV E38 Engine Control Module, and 58X Ignition System as other Gen IV V8s as introduced on the 2006 LS2. It also uses the smaller individual coil-near-plug ignition originally developed for the LS2, LS3, and LS7. The new coils are smaller and lighter than those used on previous “L76” V8s, and while they are still mounted on the rocker covers, they attach with a new mounting.
Truck L76 - 2008 Chevy Silverado
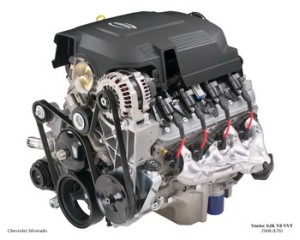
Photo © GM Corp.
|
Car L76 - 2009 Pontiac GT G8
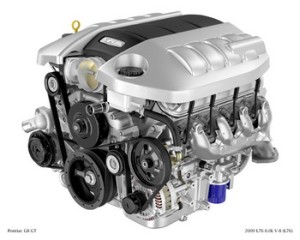
Photo © GM Corp.
|
Applications & Power:
2008-2009 Pontiac G8 GT - 361 hp / 385 lb-ft
LS4
Generation: IV
Type: 5.3L All-aluminum Transverse V8
Platform: Car
First Year: 2005
Purpose: Transverse V8 for FWD cars
Description:
Output |
303 hp / 323 lb-ft |
Displacement |
5328cc (325 ci) |
Compression Ratio |
10.0:1 |
Valves |
Hollow stainless steel intake / Sodium-filled stainless steel exhaust |
Bore x Stroke |
96.0 x 92.0 mm |
Block |
Deep skirt cast A356-T6 aluminum alloy, with pressed-in iron cylinder liners. |
Cylinder Head |
Cast aluminum, symmetrical ports, square 4-bolt pattern |
Main bearing caps |
6-bolt powder metal |
Crank |
Cast nodular iron, internally balanced, with undercut and rolled fillet journals |
Camshaft |
Gun-drilled billet steel with hydraulic roller tappets |
Connecting Rods |
Cracked, hot-forged powder-metal of steel alloy |
Pistons |
Cast eutectic aluminum |
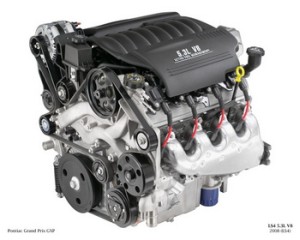
Photo © GM Corp. |
LS4 - 2008 Pontiac Grand Prix GXP |
Notable Features:
Engineered specifically for front-wheel-drive layouts, the 5.3L LS4 V8 is produces 303 horsepower and 323 ft-lbs of torque. It incorporates AFM (DOD).
To fit the “sideways” positioning in the Pontiac Grand Prix, the first platform to use the LS4 in 2005, several changes were made to shorten the engine’s overall length. The crankshaft was shortened by 13 mm – 3 mm at the rear and 10 mm at the front – and the entire accessory drive system was designed to reduce space. The water pump and all other accessories, including the power steering pump, are driven on a single-belt drive system – the longest drive system in a GM vehicle.
Because of the 5.3L V-8’s relatively low inertia, which can be up to 50 percent less at the crankshaft damper than a 6.0L V-8, a hydraulic belt tensioner was used instead of a conventional rotary tensioner.
Other 5.3L V-8 features include:
- Electronic throttle control integrated with a new E40 engine controller
- Lightweight, three-piece friction-welded composite intake manifold with throttle located at rear (driver’s side) of engine
- Cylinder heads derived from the 6.0L V8 LS2 engine
- 10.0:1 compression ratio
- Unique camshaft designed to accommodate DOD technology
- PCV valve replaced with maintenance-free fixed orifice
Applications & Power:
2005-2008 Pontiac Grand Prix GXP - 303 hp / 323 lb-ft
2006-2009 Chevrolet Impala SS - 303 hp / 323 lb-ft
2006-2007 Chevrolet Monte Carlo SS - 303 hp / 323 lb-ft
2008-2009 Buick Lacrosse “Super” - 300 hp / 324 lb-ft
Next
Well, that pretty much covers the intro and the car motors. In Part 2 we'll be looking at the truck motors in detail, the differences between the car and truck motors, how to choose an "LS motor", and more.
Until then, if you already have a hankering for serious Gen III/IV power - check out Turn Key Engine Supply - they do custom engine packages for on- and off-road vehicles, including LS1, LS2, LS3, LS7, LQ9, and 5.3L.
 

|