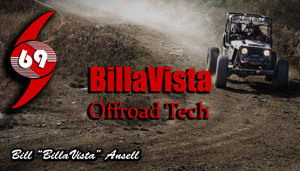 |
Suspension Joints
By Bill "BillaVista" Ansell
Photography: Bill Ansell
Copyright 2008 - Bill Ansell
(click any pic to enlarge)
|
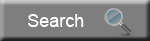 |
Introduction
There are many choices on
the market today for suspension-link joints. A wide selection is a good thing,
but it can also make the decision more complicated. And the decision is an important
one. In today's multi-link suspension, there can be up to 16
or more joints - all of which are going to have a profound effect on how the
suspension performs and the durability of the rig, as well as your budget -
buying 16 joints can add up to serious money pretty quickly. Choose the wrong
joint and you may not get the most out of your carefully designed suspension.
You might also find yourself rebuilding or replacing joints more frequently
than you'd like. |
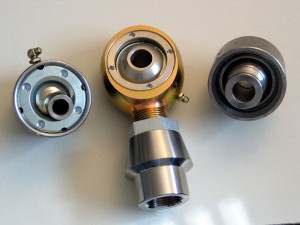 |
|
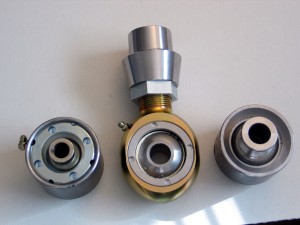 |
The selection
of the joint for the suspension link is also at least as important as selection
of the tube. Having destroyed countless rubber and poly bushings I am a
firm believer in using some sort of cartridge-style joint or spherical rod
end (Heim joint). For this article I evaluated and reviewed three of the
best. Shown in the pic at left, from left to right are the Rubicon Express
Large Cartridge Joint, the Evolution Machining and Fabrication Rebuildable
Heim Joint, and the Poly Performance Uniball. |
In selecting a joint, there
are a number of factors to consider:
- Cost – the more
expensive joints can add up quickly, especially since a standard 4-link front
and rear suspension uses 16 joints.
- Adjustability –
if you need adjustable-length links, you will have to choose a joint with
a threaded shank that offers this feature.
- Strength – you
need to match the strength of your tube to the strength of your joint. It
is pointless to attach a 2” x ½” Cr-Mo tube to a cheap
¾” Heim joint.
- Size – As with
all things, as strength increases, generally so does size. Make sure your
link / bracket design and placement leave adequate room for the joints
- Rebuildability –
Damage and wear are almost a given – any good joint should offer the
ability to be rebuilt without having to fabricate a whole new link.
- Lubrication –
The “sealed vs greasable” debate is timeless and boils down to
personal choice. Depending on the conditions of use and your preference, you
may wish to use joints that can be periodically lubricated. Some joints are
“self lubricating” meaning they use some sort of chemical-impregnated
cup or liner that lubricates the bearing.
- Size of bolt hole –
Something you need to consider, especially before fabricating brackets, as
many of the largest and strongest joints use a very large bolt hole.
- Misalignment capacity
– Make sure the joint you use will work with your suspension design
without causing excessive binding that will limit suspension performance and
cause excessive wear and damage to components. Consider whether the joint
offers spacers to increase misalignment capacity.
The following table provides
a comparison of the basic specs of the different joints. |
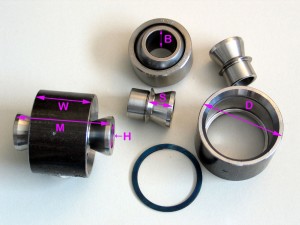 |
|
RE
(large) Bearing |
Poly
Performance |
Evolution |
Body Material |
DOM |
DOM |
4140 |
Bearing Material |
Chrome-plated steel |
Ball – 440C heat treated
stainless steel
Race - 17-4 PH heat treated stainless steel |
Stainless Steel |
Body diameter
(D) |
2-5/8" |
2-5/8" |
3.0" |
Body Width
(W) |
1.875" |
1.750" |
1.625" |
Bearing width
(B) |
2.625" |
1.375" |
1.750" |
Spacer width
(S) |
built in |
2 x 0.815" |
2 x 0.50" |
Total mounted
width (M) |
2.625" |
3.000" |
2.750" |
Bolt hole (H) |
9/16" |
3/4" |
3/4" |
Shank thread |
n/a |
n/a |
1.250 - 12 UNF |
Shank length |
n/a |
n/a |
3.0" |
Tubing Size |
Up to 2" OD |
Up to 2" OD |
1.750" ID |
Misalignment |
23 degrees |
32 degrees |
28 degrees |
Features |
UHMW bearing cups,
hardened, chrome-plated ball, adjustable preload, greasable, |
All metal, PTFE lined,
self-lubricating bearing, non-greasable, no preload adjustment, no special
tool required |
Stainless steel pre-load
ring with locking screw, grease nipple, composite bearing cups. Available
in left and right hand thread. Left & right hand jam nuts and tubing inserts
available. |
|
RE
Large Bearing |
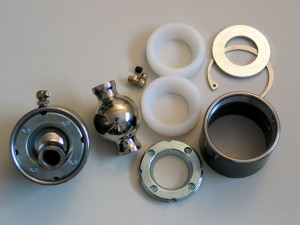 |
A great
low-cost option, the large RE bearing is a good all-round joint. It uses
a chrome-plated ball with integrated spacers, replaceable Delrin bearing
cups, and a threaded ring that can be used to set and adjust pre-load on
the ball. They are greasable via a supplied grease nipple and rebuildable.
Being quite common, individual parts are available from many locations.
A special tool is required to build and adjust the joints, but costs only
a few bucks. As supplied, they offer no adjustability for link length, but
one could weld some threaded rod to the joint and create and adjustable
joint. |
|
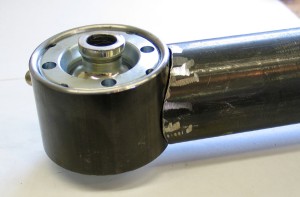 |
The RE
joints are designed to be welded directly to the notched end of your link.
Due to the width of the cartridge, or body, of the joint there is a practical
limit to the OD of the tube you can use with them. Much wider than 2”
OD tubing and you will have problems getting a satisfactory weld without
gaps between the tube and the joint. The pic at left shows a large RE joint
being test-fitted to a 2" OD tube. When using tube with an OD approaching
the limit, be aware that you will be welding to the outside of the threaded
area of the joint body. Care is required to avoid warping the internal threads,
and I recommend you thread the adjustable ring into the body when welding
to the tube. The quality of the plated ball does not approach that of the
other two joints I evaluated, but the cost is quite a bit lower. The joint
uses a decent-sized 9/16” bolt. |
Poly Performance Uniball |
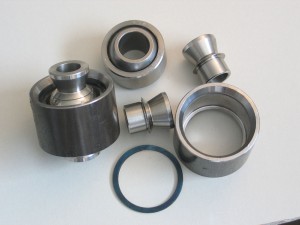 |
A relatively
new offering from one of my favourite suppliers in the industry, Dave
at Poly Performance had the Uniball created with performance
in mind. This joint is designed for those seeking a tight, maintenance
free, extremely high quality joint with maximum misalignment capabilities.
It uses a high-quality, precision, FK spherical bearing and trick custom-machined
misalignment spacers held in a tubular cartridge body much like the RE
bearing. However, the FK bearing has neither provision for lubrication
nor pre-load adjustment as it is PTFE lined and factory-set. This means
that because the FK bearing is a self-lubricating precision assembly,
pre-load adjustment and lubrication are not required, either during initial
assembly or throughout the life of the joint. In most cases this is an
advantage: you need not guess at an appropriate pre-load setting - the
bearing is already set for maximum strength and durability - and periodic
re-greasing isn't required. However, some users may feel more comfortable
with a joint they can adjust and grease as required. The catch is - you
have to actually do it. Much like the age-old argument surrounding sealed
vs. greasable U-joints - the greasable joint is only advantage to those
who religiously do so. If you're inclined to neglect maintenance from
time to time, you're probably much better off with a self-lubricating,
factory-set joint like the Uniball. |
The Poly Performance
Uniballs are a high-end joint that combine the best features of traditional
high-quality Heim joints (precision, maintenance-free bearings) with the
benefits of a cartridge joint (ease of use - just weld to tube and go.
Rebuildability - the FK bearing can be replaced without having to fabricate
a whole new link). Mix in the trick missalignment spacers and you have
a unique and compact joint.
Compact, strong, precise,
and capable of wicked articulation this joint is an excellent choice for
top-end buggies and other rigs seeking maintenance-free high-end performance.
Evolution Rebuildable Heim |
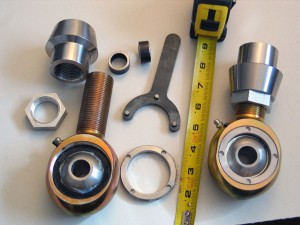 |
The
monstrous rebuildable Heim joint from newcomers Evolution Machining
and Fabrication is the king of size and brute strength. Because they
are custom made specifically for use in link suspensions, the Evolution
joints have several very attractive features. Custom machined from chrom-moly
and stainless steel these brutes are greasable, rebuildable, and feature
adjustable pre-load. They are also designed to use a large but reasonable
¾” bolt, which is a very nice feature in a joint of this
size – often a very large joint requires the use of a 1” or
larger bolt which can make bracket fabrication and sourcing the bolts
difficult.
They come supplied
with a special spanner for adjusting the pre-load ring, as well as with
two half-inch wide DOM spacers to be placed either side of the ball to
achieve misalignment. One advantage of this is that, because the spacers
are simply 3/4" ID DOM tube, should they be too long or too short,
you can fairly easily make your own.
If you look carefully
at the joint in the right of this picture you can see the hex socket set-screw
that keeps the preload ring tight. |
|
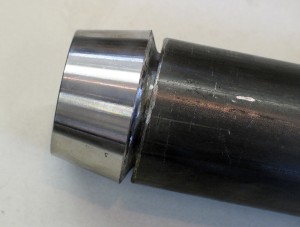 |
The Evolution Joints
come in both left- and right-hand thread, as do the accompanying jam nuts
and weld-in threaded tube adapters. One nice thing about using a joint
with a threaded shank is that making the links is extremely easy, since
all you need to do is cut the tube to length, drop in the tube insert,
and weld. The pic at right shows an Evolution tube adapter inserted into
a 2-1/4” x ¼” 1026 DOM tube. The tube adapters come
with a generous bevel, allowing for a good, strong weld joint. Another
advantage to this style joint is the fact that the joints themselves are
completely removable from the link so that, should you damage a link beyond
repair, you can remove the joint and jam nut, simply buying a new tube
and insert to make the new link.
Evolution can also
supply the threaded inserts in either mild-steel (for use in DOM) or in
chrom-moly for those using chrom-moly tubing for their links. This is
an excellent option as welding a mild steel insert or cartridge joint
body to a chrom-moly tube defeats the purpose of using chrom-moly in the
first place. |
|
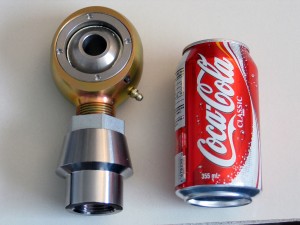 |
The boys from Evolution
have a long history of building and abusing hardcore rigs, and it's
clear their experience has gone into these joints.
The Evolution joints
are truly impressive, offering first-rate machining, from the joint
itself to the accompanying tube inserts and jam nuts - all fully custom
made, in-house, with one goal in mind - to be the biggest, baddest,
toughest joint available. I noted that the thread-forms on the joint's
shanks and in the jam nuts and inserts were excellent.
It's hard to fully
appreciate the truly massive size of these joints without holding one
in your hand, but the pic at left should give you some indication. Because
of the massive size of these joints, including the 1-1/4” threaded
shanks, there are a limited number of options for the size of tube you
can use. The threaded tube inserts take a tube with a 1.75” inside
diameter. The following table gives some options for this size tube. |
Tube
OD |
Wall |
Tube
ID |
2" |
1/8" |
1.75" |
2-1/8" |
3/16" |
1.75" |
2-1/4" |
1/4" |
1.75" |
2-3/8" |
5/16" |
1.75" |
2-1/2" |
3/8" |
1.75" |
2-5/8" |
7/16" |
1.75" |
2-3/4" |
1/2" |
1.75" |
|
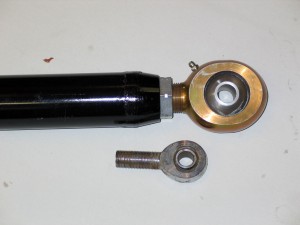 |
For my links using
the Evolution joint I chose 2-1/4” x ¼” 1026 DOM.
The pic at right shows one end of a completed link next to a standard
3/4" Heim joint. Interestingly, this tube is both lighter and stronger
than the 2” x 3/8” tube I used with the other joints. The
only drawback is size – a 2-1/4” OD tube is a big tube,
and you need quite a bit of clearance to use it.
I was extremely
impressed and pleased with the quality of the Evolution joints –
they are perfect for use in the top link of my front-end 3-link where
I need maximum strength and durability to withstand the loads a single
top-link sees from counteracting axle wrap; and their adjustability
makes setting and adjusting pinion angles a snap. If you need adjustability
combined with unmatched strength, and have the space, these are the
joints to use. |
All three of these joints have their strengths and weaknesses, and their appropriate applications. Looking for a low-cost all-round joint that will perform well and not break the bank? - then the RE bearing is your choice. Have a big, hardcore rig you love to abuse and afraid that plastic inserts and 9/16" mounting bolts won't stand up? If it's the ultimate in adjustable brute strength you need - Evolution is the way to go. Have a smaller or high-performance buggy that needs super-tight, trouble free, max performance suspension links and/or just have to have the bling - look to Poly Performance's trick Uniball joints.
In my own rig I used a combination of all three joints as follows:
For my front lower links I used fixed length links with an RE bearing at each end for the following reasons:
- I don't need adjustable-length links as my front axle location has been dialled in and fixed for some time.
- I needed the smaller mounting width of the RE joints to fit in the brackets on my axle.
- The frame-side brackets were also already in place for RE bearings, as I had used them before in that location and been very happy with them.
- Because front lower links take a lot of abuse, but making them over-size eats up valuable clearance I wanted to use 2" OD x 3/8" wall tube for my front lowers, which is a perfect size for these joints.
For my front upper link I used two Evolution joints and 2-1/4” x ¼” tube because:
- As a single upper link, this link sees tremendous stress from both locating the axle and counteracting drivetrain torque (preventing pinion wrap).
- I wanted an adjustable joint at each end, one left-hand and one right-hand so that I could adjust the links length and therefore front pinion angle without removing the link from the vehicle.
- I had plenty of room to fit both the large tube and the brackets required for the Evolution joints.
For my rear links I chose a mix of Poly Performance Uniballs and Evolution Joints as follows:
- I used the Uniballs at the frame-end of the lower links and upper wishbone for their precision, compact size, and misalignment capability. Up near the frame they are relatively well protected and less subject to immersion in water and mud. Also, because there are no internal threads in the body of the joint to warp, they are easier than the RE joints to weld to the tube.
- I used Evolution joints at the axle-end of the lowers so that I'd have some adjustability in the links, and because their beef makes them ideal for this location where they hang low and often get bashed and abused. I also had plenty of room to locate new brackets on the rear axle.
- I used an Evolution joint as the single joint at the back of my rear-upper wishbone link as, being a single joint, it sees a lot of force and loading. Once again, the shear size and strength of the Evolution Joints make them ideal for this sort of use.
|
Conclusion
Whatever your particular needs may be, or whatever your design may call for, I'm certain that one of these joints can fill the need. Also, both Poly and Evolution are top-notch professional companies to deal with and I can highly recommend them both. |
|
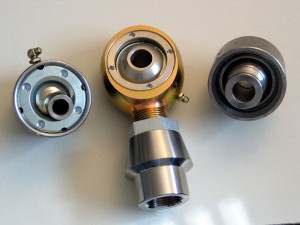 |
Sources: Evolution Joints:
Evolution Machining & Fabrication Inc.
#1 - 4115 64th Ave. S.E..
Calgary, Alberta T2C 2C8
Phone: (403) 236-3545
www.evolutionmachine.com
RE Bearings & Poly Performance Uniballs:
Poly Performance Offroad Products
234 Tank Farm rd, Unit L & M
San Luis Obispo, CA 93401
Phone: (805) 783-2060
sales@polyperformance.com
www.polyperformance.com |
|