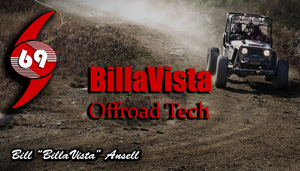 |
Engine Oiling
By Bill "BillaVista" Ansell
Photography: Bill Ansell
Copyright 2010 - Bill Ansell
(click any pic to enlarge)
|
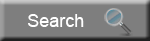 |
Introduction
Engine oil and oiling - welcome to one hell of a complicated subject!
Let me state right now - I do not claim to know the truth, the whole truth, and nothing but the truth about engine oil and oiling.
The reason is, it's actually a very complicated topic. In fact, I'd venture to say that the physics and chemistry of engine oil and lubrication is THE most complicated topic relating to your car or truck. Heck - even the experts don't yet understand or agree on all of it. |
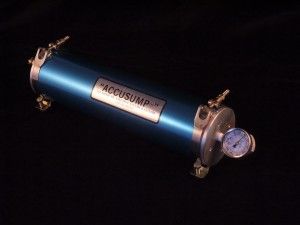 |
For example, from SAE paper J357 "Physical and Chemical Properties of Engine Oils":
High-shear-rate viscosity measured at 150 °C and reported in mPa·s (centipoise) is widely accepted as a rheological parameter which is relevant to high-temperature engine performance. In particular, it is generally believed to be indicative of the effective oil viscosity in high-shear components of an internal combustion engine (for example, within the journal bearings and between the rings and cylinder walls) under severe operating conditions.
The bold yellow text in that statement are some pretty qualifying statements that indicate that there is not complete agreement among the experts. And those are some dudes with some really big heads! They even have really big names. For example - a "tribologist" is a scientist or engineer that studies the science of wear and friction.
So what is the average enthusiast like you or I supposed to do? .
What I did was read a ton of papers and articles to form a basic understanding of the principles involved so that I would be reasonably educated on the topic, allowing me to form at least semi-educated opinions when deciding what was best for my engine. I also built my own engine oiling system for my LS2 by assembling a collection of quality aftermarket parts including cooler, accumulator, remote filter, and custom plumbing.
So that's what I'm going to document here in hopes that you may find it useful. The bottom line is - I do not, in any way, claim to be an expert in this field, and some of what follows will unavoidably be opinion or educated guess. To paraphrase a friend of mine, "Oil...It's that damn complicated!"
So with that said, I'm first going to tackle an introduction to engine oil; and then finish with a look at the components that make up a quality oiling system - from pan to pump to accumulator and back.
Oil
What is oil?
Engine oil is not just a liquid - it's actually a "dilute polymer solution". What the heck does that mean? A polymer is a chemical compound made up of a long chain of repeating molecules. It means oil is a whole bunch of different chemical components and molecules combined is specific ways to create a sort of "liquid machine". Think of it like a whole bunch of tiny, microscopic molecular machines combined in long links like a bicycle chain.
Why is it so complicated?
The science of engine oiling is, in part, complicated because oil has so many important functions in the modern internal combustion engine. Ask someone what oil is for, and they usually get one or two from the list, but rarely all.
The purpose of engine oil is to:
- lubricate moving parts and protect against wear
- cool
- seal
- clean and maintain cleanliness
- provide necessary hydraulic action (e.g. hydraulic valve lifters)
- protect against corrosion
Basic oil composition
In order to be able to do all that, over a wide range of operating conditions (esp. at different temperatures), the oil you put in your engine is made from about 80% base oil and 20% additives.
In the case of so-called "dino oils" the base stock is refined from crude oil extracted from the ground. In the case of synthetic oils, the base stock is chemically synthesized. Base stocks typically have molecular weights ranging from 300-600, whereas additives such as viscosity modifiers are very large polymers with molecular weights of 10,000 or more.
Why is it important?
Well, the obvious answer can be gleaned from looking at the above list of jobs the oil has. We wouldn't want to be lacking any of these in our engine.
In addition, and particularly important in high performance applications, using the proper oil with the correct physical and chemical properties for the application ( matched to the engine and operating conditions) minimizes friction and thus increases available power output and minimizes engine wear.
The specific physical and chemical properties come from the "formulation" of the oil - that is, from the specific combination of base stocks and additives.
Base Stocks
A variety of different processes are used in the manufacture of base stocks for engine oils. They include:
- Distillation
- Solvent refining
- Hydrogen processing
- Oligomerization
- Esterification
- Recycling & Re-refining
- Synthesizing
We're not going to go into these methods and talk about hydrocracking, converting aromatics to napthenes, isomerization, and the rest of the organic chemistry involved. While it may be interesting to some - it doesn't really mean much to we users because you can't usually buy an oil based on the method by which the base stock was refined.
Additive Packages
It is far more important for us to understand a little about additives in the oil - why they are required and what they do, because it is possible to do your research and buy certain oils based on their additive packages. This is true to a point, however people often way over-state the importance of a single additive, without realizing that in the complex polymeric machine that is modern oil - it is the combination, the whole package, that is important (and not just "buy brand X because it has a lot of additive Y in it").
A lubricant additive is a material designed to enhance the performance
properties of the base stock or to impart to the base stock properties that do not naturally exist within the base
stock. These additive agents are used at concentration levels ranging from several parts per million to 10 percent by volume or more.
Generally, additives are materials that have been chemically synthesized to provide
the desired performance features but some are naturally occurring materials that have undergone only minor
modifications.
Additives can carry out their task of enhancing or imparting new properties to an oil in one of three ways:
- Protection of engine surfaces. Engine protectors
include seal swell agents, antiwear agents, antirust agents, corrosion inhibitors, detergents, dispersants, and
friction modifiers.
- Modification of oil properties. Oil modifiers include pour point depressants, antifoam agents, and viscosity index (VI)
improvers.
- Protection of base stocks. Base stock protectors include antioxidants and metal deactivators.
Some additives possess
multifunctional properties.
It is an important consideration for oil manufacturers to use additives that are compatible with each other as well as with the base stock. From the consumer's perspective, it is equally important to use engine lubrication products that are compatible. The best way to achieve this is to:
- Not mix different types, brands or grades (viscosities) of oil in the engine.
- Not use any aftermarket additives in the oil - the manufacturer has already spent considerable effort engineering the optimum additive package for the oil and if you have chosen the right oil for the application, no extra additives are necessary.
Definitions
CLOUD POINT
The cloud point of a moisture-free oil is defined as the temperature at which
a cloud or haze appears in the lower portion of the test oil when tested (i.e., cooled) by ASTM D 2500. The
haze indicates the presence of some insoluble fractions, such as wax, at the temperature noted. In most
applications, this haze will have little practical significance.
POUR POINT
The pour point of an oil is defined as the lowest temperature at which the oil can be poured when tested by
ASTM D 97. The pour point can be directly related to whether or not the oil can be poured from a container
at low temperatures. Although pour point is a simple measure of wax crystal structure and low temperature
viscosity, more precise and correlatable viscometric methods, such as ASTM D 3829 and ASTM D 4684,
have been developed which better predict the ability of an oil to flow to the oil pump and throughout the
system at low temperature.
Viscosity
The most critical of an oil's properties is its viscosity, and how that viscosity varies with temperature, shear rate and pressure. The variation of lubricant viscosity with temperature, shear rate, and pressure is crucial to how the lubricant performs in an engine.
These properties are important in controlling oil film thickness and friction in the bearings, the piston assembly, and the valvetrain.
(Shear rate is the stress or force put on the oil molecules by sliding metal surfaces that tends to shear or break-up the molecular chains.)
The goal is to maintain correct/optimum oil film thickness (to separate the moving parts in the engine) while minimizing engine friction and therefore power losses. The oil must be able to do this under widely varying conditions of temperature and rpm/load, while remaining pumpable at low temperatures when cranking/starting the engine. No small task!
While the physical and chemical properties of an oil at operating temperatures (such as viscosity) are not related to oil
performance in a simple way, these individual properties are meaningful and are related to the oil's ability to
fulfill its function as a lubricant.
Viscosity is defined as the internal resistance to flow of any fluid. It is commonly thought of as how "thick" or "thin" the fluid is, or how "pourable" it is. For example, at room temperature, molasses has a very high viscosity, while water has a fairly low viscosity.
Viscosity is expressed as:
Dynamic Viscosity = (
Force / Sheared Area) / (Velocity / Film Thickness) = Sheer Stress / Shear Rate
The unit of measure for dynamic viscosity is the millipascal second (mPa·s), although the centipoise (cP) is
also commonly used. One mPa·s equals 1 cP. Oils that exhibit a constant viscosity at all shear rates in this
equation are known as “Newtonian” oils. Most single grade oils without additives are in
this category at temperatures above their cloud point. We don't generally use oils such as these in engines because, having a constant viscosity, they are either too viscous (thick) to be pumped when cold or too "thin" to provide adequate oil film when heated to operating temperature.
Oils that exhibit a viscosity which varies with changing shear rates in this equation are known as “non-
Newtonian” oils. Multi viscosity graded oils formulated with polymeric additives are generally in this category.
Almost any oil you put in your engine is going to be a non-Newtonian oil.
Another way you may see viscosity expressed is by Kinematic Viscosity. Kinematic Viscosity is determined by measurement using a method where the result is directly affected by the density of the liquid at the temperature the measurement was made. This method is easier than determining all the variables needed for the equation to calculate dynamic viscosity (above), but has the disadvantage that results are less directly comparable because of the effect of density. As such, strictly speaking it is best to either measure dynamic viscosity or to measure kinematic viscosity and density of the liquid at the temperature of
interest and convert kinematic viscosity to dynamic viscosity using the equation:
Kinematic Viscosity= Dynamic Viscosity / Density of Liquid
The unit of measurement for kinematic viscosity is the millimetre squared per second (mm^2/s), although the centistroke (cSt) is
also commonly used. One mm^2/s equals 1 cSt.
What does all this mean? It means that the viscosity of an engine oil changes with both temperature and with the load we place on it in the engine (pressure and shear rate). Since temperature, pressure and and shear rate can all vary widely in the engine (for example engine oil may be at 30°F when the engine is cold and first started, but rise to 300°F under hard use), we need a way to both identify and control (as much as possible) the viscosity of the oil under different conditions, because the viscosity plays such a huge role in achieving our goal, which we said was to maintain correct/optimum oil film thickness (to separate the key moving parts in the engine) while minimizing engine friction and therefore power losses. For an engine oil, the viscosity must be sufficiently
high so that the phenomenon of hydrodynamic lubrication can occur. This is where the flow of the oil forces the
bearing surface to ride on a thin film of oil and, thus, protect the lubricated surface from wear. Neither identifying the viscosity of an oil under different conditions nor controlling it is a simple task.
Before we move on, let's have a look at a simplified chart of some typical engine oil viscosities in cSt to give us some perspective:
SAE Motor Oil Grade |
Kinematic viscosity at low-shear-rate, in cSt at 100°C (212°F) |
30 |
10.3 |
0W20 |
8.3 |
5W30 |
9.9 |
10W30 |
10.8 |
15W40 |
14.9 |
20W50 |
17.8 |
Flow & Oil Pressure
What does all this complicated talk of viscosity translate to in the real world? The viscosity of the oil directly affects its pressure and flow as it is pumped around the engine to do its many jobs. Time to dispel a huge misnomer about engine oil and lubrication. Many folks mistakenly believe that oil pressure is the be-all end-all of engine lubrication - and understandably - as we have an oil pressure gauge after all. Unfortunately, this is not quite true. It is in fact the flow of oil that lubricates, cools, and cleans the engine. Adequate pressure to create this required flow is vital, to be sure. But do not be mislead into thinking that pressure is everything and the higher the oil pressure the better. In fact, pressure and flow are inversely proportional - as one goes up, the other must go down. So, for example, if you were to use a very thick (viscous) oil in your engine - pressure would go way up, but flow would go way down (it is, in fact, the resistance to the flow of the thick, viscous oil that causes the pressure to go up). The reason we have an oil pressure gauge is that it is much easier to measure oil pressure than oil flow.
So - adequate pressure is critical - but too much can be as bad as too little if it's an indication that the oil is too thick to flow adequately for lubrication and cooling. Imagine you used 90W/140 gear oil in your engine - a very thick, viscous oil. You'd have tremendous oil pressure - for a short while, anyway! But the oil would not flow enough to cool and lubricate and the engine would soon be destroyed. We'll return to this topic a little later when we discuss selecting and engine oil, but for now, keep in mind that oil pressure is vital, but not at the expense of flow - and that too much pressure is often a result of too little flow - more is not always better when it comes to oil pressure!
The golden rule for almost any engine is 10 psi oil pressure per 1000 RPM.
Viscosity Variation
Viscosity decreases rapidly with increasing temperature. For most oils, the
relationship between viscosity and temperature can be approximated by the empirical relationship
in the following equation:
loglog(kinematic viscosity+ 0.7 ) =A+B (log absolute temperature)
where:
A and B are constants, specific for each oil.
This relationship, which is an approximation of the MacCoull, Walther, Wright equation, forms the basis for
special viscosity temperature charts published in ASTM D 341. These charts permit the plotting of viscosity-temperature
data as straight lines over the temperature range in which the oils are homogeneous liquids.
The slope of these lines is a measure of the change in viscosity with temperature. It is dependent on the
chemical composition of the oil and is described by an empirical relationship called the Viscosity Index or VI. The higher the VI, the
smaller the change in viscosity with temperature (slope). ASTM D 2270 is used to determine VI values.
ASTM DS 39b is based on ASTM D 2270 and allows for more convenient determination of VI.
The Viscosity Index is calculated as such:
VI = 100+(10^(LN((EXP(1.0727+0.6175*LN(cSt@100)+0.9744*(LN(cSt@100)^2)+
(-0.3764)*(LN(cSt@100)^3)+0.04824*(LN(cSt@100)^4)))/cSt@40)/LN(cSt@100))-1)/0.00715
I warned you it was a complicated topic - didn't I?!
Let's try and simplify things a bit.
For engine oils, a relatively small change in viscosity with temperature (high VI) is desirable to provide a
wider range of operating temperatures over which a given oil will provide satisfactory lubrication. At low
temperatures, a relatively low viscosity oil is desirable to permit adequate cranking speed during starting,
and then adequate flow to the oil pump and the entire engine oiling system after starting.
At high temperatures in a running engine, the oil viscosity must be high enough to maintain adequate film
thickness between rotating or rubbing parts to minimize wear. Using a higher viscosity oil generally reduces
oil consumption (past piston rings and valve guides) and blowby, but increases friction associated with oil
film shearing in the piston/piston ring cylinder wall interface and in the bearings.
To extend the upper temperature limit at which an oil will still provide
satisfactory lubrication, polymeric additives, called Viscosity Index (VI) improvers, are widely used. Engine
oils properly formulated with VI improvers generally contain lower viscosity base stocks which provide better
low temperature cranking/starting and pumpability properties. As the oil temperature increases, the viscosity
of the oil containing a VI improver decreases more slowly than the same oil without a VI improper, thus
increasing the VI. The result is an oil that can give good starting/pumping response and is also effective in
providing a more viscous oil film at operating temperatures than could be obtained with a single grade oil
providing equivalent startability at low temperatures.
Oils containing a polymeric VI improver exhibit a decrease in viscosity as the shear rate or stress is
increased. Because the viscosity of such oils depends on shear stress, they are called “non-Newtonian oils.”
Such change generally lasts only as long as the oil is operated under such high shear stress. When the
shear stress is relieved, the oil reverts to its previous viscosity. This reversible decrease in viscosity due to
shear is called “temporary shear (or viscosity) loss.” When certain critically high shear stresses are imposed
on a VI improver in oil solution, the viscosity contribution of the VI improper to both low and high shear rate
viscosity can be permanently reduced. This nonreversible reduction in viscosity is called “permanent shear
(or viscosity) loss.” The magnitude of these temporary and permanent losses is dependent on the type and
molecular weight of the VI improver used, as well as the actual service conditions. In other words - VI Improvers can wear out.
Note that, in addition to VI Improvers, other chemical
additives, fuel dilution, contaminants from within and outside of the engine, wax in the oil, oil oxidation,
volatilization, and many other materials found in or added to the oil affect the viscosity. This is, of course, one of the reasons why even the best oils need to be changed regularly.
The use of VI Improvers is what gives us the "multi-grade" oils we are so used to today. Sadly, no oil is labelled with its VI, and the SAE labelling system in use today is actually a fairly broad system of classification which, if not well understood, can cause a lot of confusion and misunderstanding.
Let's have a look at it now.
SAE Standard Oil Labelling System.
So what does the labelling on the can, like "5W30", really mean and what does it tell us?
First and foremost, we must understand that the labelling on an oil can IS NOT telling us the viscosity of the oil - it is telling us the "Grade" of the oil according to the methods published by the SAE. That is, the SAE grade is a classification or grouping of oils based on viscosity, but not a measurement or statement of the oil's actual viscosity. In other words - the actual viscosity of oils of the same grade can vary - and sometimes by quite a bit.
Let's take a step back first, and look at things from the engine designer's perspective.
OK, if we refer back to our first chart of typical viscosities, we see that a straight 30 weight oil has a viscosity of about 10 cSt at 100°C. Simple then - the designer builds the engine and simply tells the user to use 30 weight oil. Done. What's all the fuss?
Not so fast grasshopper - remember all the things we just discussed that affect viscosity - chiefly temperature?
Our simple plan of "just use 30" would work fine if the engine and oil were always at a constant 100°C, and if it operated such that there were no changes in shear rate and pressure, nor any contaminants ever introduced. Alas, we know this is not the case. In the real world, we must contend with all these things, the biggest being temperature.
As we discussed, the viscosity of oil varies with its temperature. A straight "30”weight" oil may have the desired viscosity at 100°C (212°F), but look how it varies with temperature:
Temp ( °F ) |
Actual viscosity (cSt) |
Conditions |
Notes |
302°F |
3 |
Typical oil temp under racing conditions. |
Too thin to provide adequate hydrodynamic lubrication (metal-metal separation) |
212°F |
10 |
Typical oil temp under "Normal" operating conditions. |
OK |
104°F |
100 |
Typical oil temp at start-up, hot summer day. |
Too thick to pump and flow. |
32°F |
250+ |
Typical oil temp at start-up, winter day. |
Far too thick - will not pump or flow at all, engine will not crank or start. |
Clearly, as the temperature varies from the designed operating temperature the oil become unsuitable. As the engine heats up under hard use, the oil thins unacceptably and will not lubricate sufficiently. As the engine cools down to ambient temperature, the oil thickens unacceptably and will neither lubricate sufficiently, nor pump and flow sufficiently. Straight 30 weight oil has a very low Viscosity Index (VI).
The Solution?
While not perfect, the solution to this dilemma lies in the use of so-called "multi-grade" oils that do not exhibit the same change in viscosity with temperature as the good old straight 30 weight oil does. This is achieved either by adding VI improvers to mineral-base oils, or by the actual molecular synthesis of synthetic-base oils. The idea being to create an oil that neither thickens too much when cooled, nor thins too much when heated - but rather remains as close as possible to the ideal viscosity throughout the range of temperatures in which it is to be used.
DO NOT confuse multi-grade with multi-viscosity. Remember, the goal is to produce an oil that has a near-constant viscosity regardless of temperature (as much as is possible). Oils are assigned grades based on a number of criteria. In order to understand multi-grade oils, we must first understand single-grade oil classifications.
Single Grade Oils
There are two different groups or series of grades used by the SAE to classify engine oils. The difference between the series is the type of testing done on the oil.
The low-temperature-use or "W" grade oils:
In one series, the grade an oil is assigned is based on maximum low-temperature cranking viscosity, maximum low-temperature pumping viscosity, and a minimum kinematic viscosity at
100 °C. Oils in this series are identified by a number (often referred to as the "weight" of the oil") followed by the letter "W" (e.g. "10W"). Many folks believe the W stands for "winter use", presumably because these oils go though low-temperature testing. In fact, the W doesn't stand for "winter", but is just the method chosen to identify the series of oil grades that include low-temperature (below-freezing) testing - so it's easy to see why the connection was made between W and "winter".
SAE
Viscosity
Grade |
Low-Temperature Cranking
Viscosity (mPa·s)
Max |
Low-Temperature Pumping
Viscosity (mPa·s)
Max
(with no Yield Stress) |
Low-Shear-Rate
Kinematic
Viscosity (mm2/s)
at 100 °C
Min |
0W |
6200 at –35°C |
60 000 at –40°C |
3.8 |
5W |
6600 at –30°C |
60 000 at –35°C |
3.8 |
10W |
7000 at –25°C |
60 000 at –30°C |
4.1 |
15W |
7000 at –20°C |
60 000 at –25°C |
5.6 |
20W |
9500 at –15°C |
60 000 at –20°C |
5.6 |
25W |
13 000 at –10°C |
60 000 at –15°C |
9.3 |
Note that the figures in the table are LIMITS, either minimum or maximum, as indicated, that an oil must meet in order to be classified into that grade. They are not actual SPECIFIC guaranteed specifications. This is one reason why the performance of identicaly classified (and therefore labelled) oils can vary.
Column 1, Low-Temperature Cranking
Viscosity, correlates with the ability of an engine to start at low temperatures. Thus, for example, if you plan to start your engine when temperatures are colder than –25°C, you would need to choose a 5W or 0W grade oil.
Column 2, Low-Temperature Pumping
Viscosity, is a measure of an oil's ability to flow to the engine oil pump and provide adequate
oil flow during the initial stages of operation.
Don't ask me why the temperatures don't correlate between columns 1 and 2 - I don't know and it doesn't make sense to me why not - take for example the criteria for a 10W grade oil - it's hardly likely that you'd want to start an engine at only –25°C but run it at –30°C. (This is actually a sneak-peek at one of the conclusion I shall eventually draw - that the SAE labelling on the can doesn't really tell the average user a whole heck of a lot!)
Column 3, Low-Shear-Rate
Kinematic
Viscosity, has been shown to be related to certain forms of oil consumption (e.g. if kinematic viscosity is too low, the engine may suffer excessive oil consumption past the rings) and
have been traditionally used as a guide in selecting oil viscosity for use under normal engine operating
temperatures.
Obviously, since the criteria in the three columns are maximums and minimums, it is possible for an oil's actual test results to satisfy the requirements of more than one W grade. In labelling a W grade, only the lowest W grade satisfied may be referred to on the label. Thus, an oil meeting the
requirements for SAE grades 10W, 15W, 20W, and 25W, must be referred to as an SAE 10W
grade oil.
An oil must meet the pumping requirements of the lowest W grade satisfied by the cranking viscosity. If
the W grade defined by the pumping viscosity is higher than the lowest grade satisfied by the cranking
viscosity, the oil does not meet the requirements of SAE J300 and is, therefore, inappropriate for use.
If the kinematic viscosity at 100°C of an oil does not meet the requirements of the lowest W grade satisfied by the
cranking viscosity, then the oil does not meet the requirements of SAE J300 and is, therefore,
inappropriate for use.
The high-temperature-use grade oils:
In the second series, the grades are defined by a number only. In order to be assigned one of these grades, an oil must meet certain different criteria. Oils are assigned one of these grades based on their meeting a set of minimum and maximum kinematic
viscosities at 100 °C, and a minimum high-shear-rate viscosity at 150 °C.
SAE
Viscosity
Grade |
Low-Shear-Rate
Kinematic
Viscosity (mm2/s)
at 100 °C
Min |
Low-Shear-Rate
Kinematic
Viscosity (mm2/s)
at 100 °C
Max |
High-Shear-Rate
Viscosity (mPa·s)
at 150 °C
Min |
20 |
5.6 |
<9.3 |
2.6 |
30 |
9.3 |
<12.5 |
2.9 |
40 |
12.5 |
<16.3 |
3.7 |
50 |
16.3 |
<21.9 |
3.7 |
60 |
21.9 |
<26.1 |
3.7 |
Columns 1 & 2, Low-Shear-Rate
Kinematic
Viscosity, as for the W grade oils, has been shown to be related to certain forms of oil consumption and
have been traditionally used as a guide in selecting oil viscosity for use under normal engine operating
temperatures.
Column 3, High-Shear-Rate
Viscosity measured at 150 °C, is widely accepted as a
rheological parameter which is relevant to high-temperature engine performance. In particular, it is
generally believed to be indicative of the effective oil viscosity in high-shear components of an internal
combustion engine (for example, within the journal bearings and between the rings and cylinder walls)
under severe operating conditions. While the specific temperature and shear rate conditions experienced
by an oil in a particular application depend on mechanical design and operating parameters, the
measurement conditions specified are representative of a wide range of engine operating
conditions.To insure that polymer-containing oils do not create a situation in which the viscosity of the oil decreases
to less than a specified limit, minimum values of high-shear-rate viscosity are assigned to each of the
non-W viscosity grades as per column 3.
Multi-Grade Oils
So, let's return to our theoretical engine that we have designed to run at a water and oil temperature of approximately 100°C (212°F) and that requires an oil that has a kinematic viscosity of 10 cSt at this temperature.
Let's assume further that we need to be able to start and run this engine at temperatures down to -30°C.
Examining the SAE grade tables shows us that no single-grade SAE oil, whether W or non-W, will satisfy our requirements - the same conclusion we reached when we looked at the properties of straight 30 grade oil.
Enter the multi-grade oil.
In order to be classified as a multi-grade oil, and be assigned both a low and high-temperature SAE grade, an oil must meet the low-temperature cranking and pumping viscosity requirements of one of the W grades and all of the requirements of one of the non-W grades.
Depending on which combination of grades it meets, and subject to the requirement that only the lowest W grade satisfied may be referred to on the label, an oil may be assigned a multi-grade designation, such as 10W-30. In this case, the the W grade must precede the non-W grade, and the two grades must be separated by a hyphen.
If this is the case, it means we have an oil that satisfies both low-temperature performance requirements as well as high-temperature, high-shear requirements.
Many folks will refer to a multi-grade oil such as 10W-30 as an oil that "acts like a 10-weight oil when cold, and then acts like a 30-weight oil when hot". By looking at the tables above, we can see that this is not strictly accurate. All it means is that any oil so labelled meets the requirements of both a 10W oil and a 30 oil. The precise change of that oil's viscosity with temperature can only be achieved by plotting the Viscosity Index - something few if any users are ever going to do. That said, it's not entirely inaccurate to think of a multi-grade oil in this manner.
What we can say for certain is that a multi-grade oil will do a much better job of being thin enough at low or cold start-up temperatures to crank, pump, and flow well, while remaining thick enough at high temperatures to lubricate properly and provide the necessary hydrodynamic separation of metal parts.
By combining the requirements of the W and non-W grades into a single table it is easy to compile a table of requirements for any multi-grade oil. Here are some of the more popular multi-grades available on the market:
SAE
Viscosity
Grade |
Low-Temperature Cranking
Viscosity (mPa·s)
Max |
Low-Temperature Pumping
Viscosity (mPa·s)
Max
(with no Yield Stress) |
Low-Shear-Rate
Kinematic
Viscosity (mm2/s)
at 100 °C
Min |
Low-Shear-Rate
Kinematic
Viscosity (mm2/s)
at 100 °C
Max |
High-Shear-Rate
Viscosity (mPa·s)
at 150 °C
Min |
0W-20 |
6200 at –35°C |
60 000 at –40°C |
5.6 |
<9.3 |
2.6 |
0W-30 |
6200 at –35°C |
60 000 at –40°C |
9.3 |
<12.5 |
2.9 |
0W-40 |
6200 at –35°C |
60 000 at –40°C |
12.5 |
<16.3 |
2.9 |
|
|
|
|
|
|
5W-20 |
6600 at –30°C |
60 000 at –35°C |
5.6 |
<9.3 |
2.6 |
5W-30 |
6600 at –30°C |
60 000 at –35°C |
9.3 |
<12.5 |
2.9 |
5W-40 |
6600 at –30°C |
60 000 at –35°C |
12.5 |
<16.3 |
2.9 |
5W-50 |
6600 at –30°C |
60 000 at –35°C |
16.3 |
<21.9 |
3.7 |
|
|
|
|
|
|
10W-30 |
7000 at –25°C |
60 000 at –30°C |
9.3 |
<12.5 |
2.9 |
10W-40 |
7000 at –25°C |
60 000 at –30°C |
12.5 |
<16.3 |
2.9 |
|
|
|
|
|
|
15W-40 |
7000 at –20°C |
60 000 at –25°C |
12.5 |
<16.3 |
3.7 |
15W-50 |
7000 at –20°C |
60 000 at –25°C |
16.3 |
<21.9 |
3.7 |
|
|
|
|
|
|
20W-40 |
9500 at –15°C |
60 000 at –20°C |
12.5 |
<16.3 |
3.7 |
20W-50 |
9500 at –15°C |
60 000 at –20°C |
16.3 |
<21.9 |
3.7 |
Note: A special situation exists regarding the SAE 40 grade. Historically,
SAE 0W-40, 5W-40, and 10W-40 oils have been used primarily in light-duty engines. These multigrade
SAE 40 oils must meet a minimum high-temperature, high-shear-rate viscosity limit of 2.9 mPa·s.
In contrast, SAE 15W-40, 20W-40, 25W-40, and 40 oils have typically been used in heavy-duty engines.
The manufacturers of such engines have required high-shear-rate viscosity limits consistent with good
engine durability in high-load, severe service applications. Thus, SAE 15W-40, 20W-40, 25W-40, and
single-grade 40 oils must meet a minimum high-temperature, high-shear-rate viscosity limit of 3.7 mPa·s.
Of course, you cannot, and should not, use this table as the only method to selecting a grade of engine oil for your application. There is a great deal that isn't shown in the table - all the variables we've already discussed. All it shows is the criteria that must be met for an oil to be assigned an SAE grade. For example, if you look at the table, you could conclude that the only difference between a 5W-30 and a 10W-30 is that the 5W-30 has better cold start capabilities. While this is certainly true, it isn't the whole story. Consider that for both, the Kinematic Viscosity requirements at 100°C (normal operating temperature) are a range - from 9.3 - 12.5 cSt. It may be reasonable to assume that the 5W-30 may have a lower actual viscosity at this temperature, and probably at all temperatures below this.
When we recall that manufacturer's generally recommend oils based on the required viscosity at operating temperature, and we recall that all oils will be thicker than this at start-up (even if ambient temperatures are well above freezing) we may decide that 5W-30 is a better choice than 10W-30, even if we have no intention of operating at below-freezing temperatures, as it's viscosity will be less than the 10W-30 and therefore closer to the optimum viscosity, even as the engine is warming up to normal temp.
Mineral vs Synthetic
The method by which mineral and synthetic oils achieve multi-grade capability is different. Remember, multi-grade doesn't mean multi-viscosity - quite the opposite, it means the greatest possible ability to maintain a constant viscosity with changing temperature.
Mineral oils achieve this performance by adding VI Improvers that prevent the oil from thinning too much as temperatures increase. For example, a 10W-30 multi-grade mineral-based oil is made from a 10 weight oil and has VI improvers added to prevent it from thinning as much as a straight 10-weight oil when the engine reaches operating temp so that it has the properties of a 30 weight oil when hot.
In contrast, a 10W-30 multi-grade synthetic oil is based on a 30 weight oil. Because of this, no VI improver is needed as the oil will have the correct desired viscosity in an engine at normal operating temperature of 100°C (212°F). The difference is, because of the way a synthetic oil is manufactured using custom molecular structures, a synthetic oil can be produced that meets the requirements of a 10 weight oil when cold while also meeting the requirements of a 30 weight oil when hot. And since they are able to achieve this without VI improver additives, there are no additives to wear out as the oil is used. This is one of the advantages of a synthetic oil. By design they are less thick at start-up temperatures than mineral-based oils - even between oils with the same SAE grade.
This is one of the limitations of the SAE grading system - we can't tell from it that identically labelled oils can have dramatically different properties, including viscosity. However, much research, testing, and comparisons have been done and we know conclusively that a 10W-30 synthetic oil will have lower actual viscosity and better pourability, pumpability, and lubricating ability at cold temperatures than an identically graded 10W-30 mineral-based oil - even though they both qualify for the same SAE grading and labelling.
Without getting into any more complicated chemistry, other properties of synthetic oil make it a superior choice for engine lubrication, resulting in less wear, less friction, cooler running, and better power and economy. It is the all-round better choice except when breaking in a newly built or re-built engine where its superior lubricating properties can actually interfere with proper bedding in of the piston rings and cylinder.
But the main advantage that the synthetic has over the mineral based oil is the ability to lubricate at startup. Synthetics have lower viscosities and much better fluidity as the temperature drops (regrdless of their labelled grade). If temperatures get cold enough, mineral based oils eventually become unpourable and unpumpable - whereas synthetics can be used at much lower temperatures - this is why there are no 0W-xx graded mineral-based oils.
Engine vs Gear Oils
Before we leave the topic of oil labelling and SAE grades, let's just make one other point. Not all oils use the same grade structure. For example, gear oils use a different scale altogether from engine oils, and so the numbers are not directly comparable, even though they look very similar. For example, a 75W-90 gear oil has about the same viscosity as a 10W-40 or 10W-50 engine oil! The following table offers a rough comparison of different oil grades.
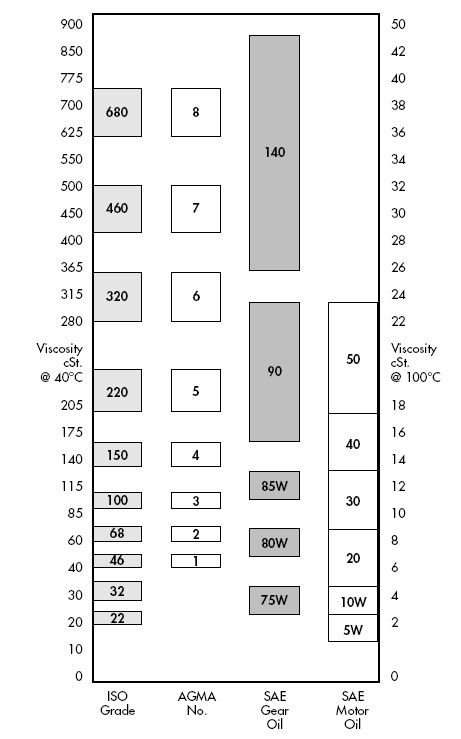
So - at this point you are probably about as sick of reading about oil viscosity as I am of writing about it. And yet we haven't come to any iron-clad conclusions or solid rules on choosing engine oil viscosity. About the only thing that we know for sure is that the detailed science and chemistry involved is WAY complicated. This may lead to the one best conclusion we can draw being: "deviate from the manufacturer's or engine-builder's recommendations with caution." Hopefully, what we have accomplished though is to at least have increased our understanding of the subject so that we are better able to evaluate further research we do or advice we are offered. For example, if you read on some forum some piece of advice or opinion about what to use - now you can evaluate that from at least a semi-educated perspective. This might just be the most useful lesson to take away from all this.
Choosing an Oil
OK, so we have learned that selection of the optimum oil:
- Ensures adequate cold start cranking, pumpability, and flow.
- Minimizes engine friction (and thus maximizes available power).
- Protects against engine wear (providing the optimum oil film thickness for the engine design and service conditions).
- Provides adequate flow for cooling and lubrication while maintaining suitable oil pressure throughout the operating range (temperature, speed, load etc.) of the engine.
- Maintains the fine line between minimizing friction and maximizing lubrication, as the two are somewhat at odds, most notably in the bearings (main and con-rod), piston assembly, and valvetrain.
There are also other properties and qualities the optimum oil must have, with most of these related to the additive packages used in the oil's formulation. For example, oil must also have good anti-foaming performance (esp. in high rpm applications) because aerated oil can cause problems with hydraulic actuation (for example, in hydraulically activated valve lifters) - like air in the brakes. Also, aerated oils can cause cavitation damage in bearings.
However, the bottom line is, none of the the physical and
chemical tests described in any of the many ASTM, API, or SAE documents listed in the references section can be used effectively for accurately defining performance characteristics at operating loads and
temperatures. Only actual performance evaluations in special laboratory engines or in actual field tests will define
the capabilities of an engine oil.
What that means is that reading an oil's specification, examining the formulation, pouring over the list of additives, arguing over the brand or type - none of these things will actually determine how an oil will perform in any particular application. Only laboratory testing, dyno testing, and real-world testing can determine this
Although laboratory engine tests like those described in SAE J304 are necessary and valuable aids to engine oil development and
evaluation, they have limitations. In many instances, the final proof-of-performance is established by field tests
of the oil in actual vehicle service.
Although oil performance in the engine is related to
base stock and additive composition, it is often difficult to assign a specific aspect of such performance totally
to the use of a specific additive or base stock. Part of the reason is that some of the physical and chemical
properties of the oil overlap in their influences on engine performance and durability and it is presently difficult
to directly and unambiguously attribute such effects to either the chemical or the physical properties of the oil.
Progress in developing this level of understanding is being made. Some of these performance characteristics
of engine oils are discussed in SAE J183, SAE J300, SAE J1423, and SAE J2227. At the present time, oil
physical and chemical properties can be related to engine performance and durability only with the guidance of
engine manufacturers and with appropriate and jointly accepted engine and/or field tests successfully
completed on that oil.
What does this mean for us?
It means that the truly dedicated looking for every ounce of performance are in for a LOT of research, testing, and evaluation. A good place to start is by reading the papers listed in the reference section at the end of this article, contacting and working with oil manufacturers and engine builders, and developing and performing relevant performance tests to be followed by analysis of used oil samples. That's a lot of work. Most of us will never have the resources to do this.
So where does that leave the rest of us? Fortunately, not hung out to dry. The lubrication requirements for modern engines are extremely complex. Current engine oils
are the result of extensive research and development aimed at meeting these requirements. Lubricant and additive
manufacturers, engine manufacturer organizations, the
Society of Automotive Engineers, Society of Tribologists and Lubrication Engineers, American Society of
Mechanical Engineers, American Petroleum Institute, American Society for Testing and Materials, etc. are all full of very smart folks whose life's work it is to produce the best engine lubricants possible - and they do a damn fine job. Today's oils are FAR superior to those available even a decade or two ago.
One of the most common and familiar methods for engine manufacturer's to specify suitable oils for their engines is by use of the API Engine Oil Licensing and Certification System. This is a system of engine oil performance categories and classifications developed through
the efforts of the Alliance of Automobile Manufacturers (AAM), American Petroleum Institute (API), the
American Society for Testing and Materials (ASTM), the Engine Manufacturers Association (EMA),
International Lubricant Standardization and Approval committee (ILSAC) and SAE.
It provides a communications tool for both
engine manufacturers and oil marketers to describe a complex series of performance specifications
to the user through a simple designation of several letters or symbols. This simplifies the oil
marketer’s job of communicating the applications for which his oil is suitable by using the same
designations on his containers. More importantly, the consumer can easily link the engine
manufacturer’s recommendation with the information on the oil marketer’s label to assist him in
selecting the proper oil for his engine.
The system embodies several different types of classifications including the API “S” series
which describes engine oil standards primarily for gasoline engine service, the API “C” series which
defines standards for diesel engines, and the ILSAC GF Series, “Minimum Performance Standard for
Passenger Car Engine Oils.”
The latest "S" series specification is "SM". This can be found on the back of an oil bottle or can in the familiar circular symbol, like this ("SJ" specification shown):
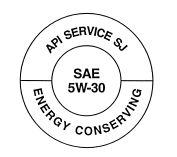
For those interested in further details of the API Engine Oil Licensing and Certification System, I recommend reading SAE J183 "Engine Oil Performance and Engine Service Classification
(Other than “Energy Conserving”)" and SAE 1423 "Classification of Energy Conserving Engine Oil for Passenger Cars,
Vans, Sport Utility Vehicles, and Light-Duty Trucks"
On the whole, engine oil performance improves with each successive specification in the series - for example, SH oils outperform SG oils. However, in some cases, engine oils with newer classifications may not always provide satisfactory performance where older
classifications are recommended. A recent example I have read about but don't have a lot of experience with is the recent reduction of ZDDP levels in the change from SL to SM oils. Basically, the most common additive package for motor oils designed to reduce wear (anti-wear) is a combination of zinc and phosphorous that is commonly called ZDDP. When ZDDP burns it produces ash that tends to be detrimental to catalytic converters and other emissions equipment, so levels of it have been reduced in SM oils, and replaced with other no-ash antioxidants. There's a whole lot of people out there pouring over spec sheets and how many parts per million of ZDDP there are in various oils - some claiming SM oils are the devil. As I said - I don't have a lot of personal experience with this topic - but a lot of what I have read doesn't seem to be backed up by a whole lot of solid science. Most of all, remember that:
Although oil performance in the engine is related to
base stock and additive composition, it is often difficult to assign a specific aspect of such performance totally
to the use of a specific additive or base stock. Part of the reason is that some of the physical and chemical
properties of the oil overlap in their influences on engine performance and durability and it is presently difficult
to directly and unambiguously attribute such effects to either the chemical or the physical properties of the oil.
At the present time, oil
physical and chemical properties can be related to engine performance and durability only with the guidance of
engine manufacturers and with appropriate and jointly accepted engine and/or field tests successfully
completed on that oil.
Rules of Thumb
After all this, I hope you weren't expecting me to be able to tell you exactly what the best oil to run in your engine is?
About the best I can do is offer you my opinions and thoughts on the matter in the form of some semi-educated rules-of-thumb.
- Choose a high-quality, name brand, synthetic oil meeting the latest API "S" series performance specification.
- Follow the engine builder's recommendation for viscosity unless you really know what you're doing.
- Failing that, choose a viscosity as low as possible while still achieving 10psi of oil pressure per 1000 rpm.
- Failing that - full synthetic 5W30 will do a good job in most engines.
- Most of us, even weekend racers, will not benefit from "racing oils" and in fact they can do harm if you're not doing full race tear-down maintenance, since many lack additives such as cleaners and dispersants.
- Always take what you read on the internet with a huge grain of salt - including this article I guess! (ironic, eh?). When researching, beware of the tenancy for people to justify their own decisions rather than share honest experience (including mistakes).
- Be aware of marketing influences - Ferrari may recommend nothing but Shell oils now - same for GM and Mobil - but those are big dollar marketing deals - it doesn't mean no other oil is as good. However, it does mean that you can probably trust that oil though - since no marketing deal is going to be good enough to get Ferrari to recommend a sub-standard oil that would cause damage in their engines.
- Change your oil frequently.
- Cool it. One of the best things you can do is add a quality oil cooler in high load, high rpm applications.
- Filter it well - use a quality aftermarket full-flow canister style filter.
- Don't expect too much of your oil - it already has a lot to do, under brutal conditions - keep it cool, clean, and filtered to give it a chance to do it's job. Do not expect a switch to a different oil to make up for worn rings or valves or leaky seals or gaskets - fix the problem then use the proper oil!
- Keep the entire oiling system well maintained - even the best oil in the world won't work well if you're upside down with a clogged filter, worn oil pump, leaky plumbing, and no accumulator.
- Err on the side of lighter oils. There has been a steady trend over the last couple of decades towards lighter and lighter oils, despite engine performance, heat, rpm, and power steadily increasing. Thirty or forty years ago, 300hp 4 and 6 cylinder engines were unheard of, as were 0W-xx oils. Today, however, it's is not uncommon for a small 4 cylinder engine to produce a couple of hundred horsepower, rev to 7 or 8 grand, possibly be turbo- or super-charged and be designed to use a 5W-20 oil. I see a clear trend where engines performance and demands are rising steadily, while at the same time recommended oil viscosities are falling.
- Closely related to the above point, treat with caution the advice of some of the old-timers. As experienced as they are - they cannot help but be influenced heavily by their early experience and teachings - and for many it can be quite a challenge to cast aside much of what they knew to be true in the past in favour of newer, highly complicated technologies such as those involved in the modern tribology and rheology of light viscosity synthetic oils. A guy who cut his teeth building old-school carbureted small block hot rod engines using 20W-50 mineral oils may have a hard time switching his thinking to all-aluminum fuel-injected V8's using 0W-30 synthetic oils.
- If you're truly dedicated to finding the optimum oil for you application, and have the time and money to do the research and testing, look into having oil analysis performed on your used oil. There are plenty of companies that offer a used oil analysis service for reasonable rates. Try a Google search for "used oil analysis" to get started. Regular and repeated teardown and inspection of the engine after controlled testing under consistently controlled conditions would also be required to produce the most thorough and reliable results. Oil performance could then be evaluated in terms of rust and
corrosion, sludge, varnish, piston ring zone deposits and condition, wear, bearing corrosion, fuel
efficiency, and peak power produced. Yea - that's a stupid amount of work. F1 teams, maybe NASCAR, they may do it - but probably few others.
My LS2 Oiling System
The stock GM Gen III/IV oiling system routing goes like this:
Oil pan – pickup tube – crank driven gerotor pump – main oil galley (driver’s side of block) – oil filter – up rear driver’s side of block – main feed galley (runs through the lifter bodies) – up to top of engine through pushrod passages – drains back to pan through drain-back passages throughout the heads and block – oil pan.
It's a very well engineered system, but for hardcore use it can stand to be upgraded a bit. So here's the what and why of what I did. Although what follows features my LS2, it can be directly applied to any GM Gen III/IV, and many other engines as well.
Oil Pan
Being a Corvette motor, the first thing I did was swap the relatively shallow Corvette oil pan for a Camaro LS1 oil pan. The LS1 oil pan has a unique shape and is made from lightweight cast aluminum. It features extended sumps that contain additional oil to ensure a good supply of oil to the pick-up tube. Compared to older small-block pans, the LS1 pan has better sealing and greater structural integrity. The Gen III/IV motors also have a large flat surface to which the oil pan is bolted, eliminating curves and corners that are hard to seal. The specially shaped oil pan is also a structural member, enhancing overall engine rigidity. |
Photo © GM Corp. |
LS1 Camaro cast aluminum oil pan. |
There are aftermarket stamped-steel or welded oil pans available for the LS motors that are quite popular with some folks. They are built with additional baffles or trap doors to help keep the oil from sloshing around and keep it close to the pickup. I took a good look at these before going with the LS1 pan, but ultimately decided against one for the following reasons:
- I couldn't find one built with a level of quality I was happy with. One of the most popular brands actually exhibits terrible build quality with poor welds and spatter all over the place.
- They are all built for racing, where the primary concern is to keep the oil in place under high lateral G forces encountered during high-speed cornering. After studying the designs, I wasn't convinced of their effectiveness for off-road use.
- All the pans I looked at suffered a common design problem - an advantage under one condition would always confer a disadvantage in another. For example, a sump/baffle/trapdoor setup optimized for steep climbs or hard acceleration would work against you in steep descents and hard braking.
- I've done a lot of research on the development of the aluminum block Gen III/IV V8 motors, and one thing that was constantly repeated was the amount of engineering that went into ensuring the aluminum block had the required rigidity, and how the cast aluminum oil pan was an integral structural member of the overall assembly. This fact, combined with the poor and flimsy construction of the aftermarket pans I looked into made me uncomfortable with replacing the GM unit. In fact, GM consider the pan such an important part of the overall assembly that they took the trouble and expense of having a warning cast into the pan itself about proper alignment and torque values.
- I use a 3-quart accumulator on my engine (more on this in a bit), and so felt that any benefit of a gated/trap door pan I may be missing, would be more than compensated for by the accumulator for those brief times when I may experience a drop in oil pressure due to the pickup becoming uncovered.
Altogether, I personally am just happier with the cast aluminum pan.
For reference, here are the depths of some different Gen III/IV oil pans:
- LS7 – dry sump - 4.5”
- Bat-wing Vette – 4.75” (C5 corvette (with LS1)
- Corvette – 5” (non bat-wing)
- Camaro/Firebird – 5.5”
- GTO – front sump – 6”
- Cadillac CTS-V – 6.75”
- Hummer H3 5.3L – 7.5”
- Truck - 8.25”
Note, an F-body (Camaro/Firebird) LS1 oil pan makes the bottom of the oil pan level with the bottom of a TH400 transmission pan. When swapping an oil pan you need the pan, the dipstick and tube, the pickup tube, and the gasket.
Oil Pump
Gen III/IV motors use a high-efficiency Gerotor oil pump, driven off the front of the crankshaft, eliminating the old cam-driven design. |
5_resize.jpg)
Photo © GM Corp. |
Gerotor oil pump, disassembled view. |
Because of their design, these pumps are more efficient, reliable, and better performing than the old-style oil pumps. However, if you are planning on running your engine oil outside the engine, as I do, for a cooler, remote filter, or accumulator it is good insurance to invest in a quality modified or aftermarket high-volume oil pump. |
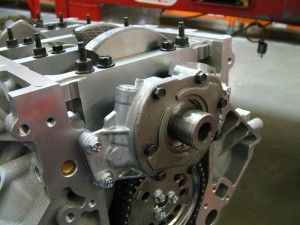 |
Turn Key Engine Supply built my LS2 with this high-flow oil pump that provides approximately 30% more volume than the stock LS2 oil pump.
In this pic you can see how it is driven off the front of the crankshaft. |
Remote Filter
Modern stock automotive engine filtration systems are actually pretty good. Unlike years ago, most systems employing the common "spin-on" type oil filter are full-flow systems - meaning all of the oil is filtered all the time - it all passes through the filter on each circuit of the system. (Years ago, in early "bypass" systems, not all of the oil passed through the filter all the time. Most of the oil bypassed the filter and was pumped straight from the tank to the engine oil galleys. Only some of the oil passed through the filter via a second flow path in parallel with the first, and therefore it took some time to filter all the oil).
Stock-style spin-on filters also incorporate a different kind of bypass (not to be confused with the old-style bypass system). In this case, the bypass is either incorporated into the filter unit, or as part of the oil filter housing on the engine, and is pressure activated. Should the filter become extremely clogged, the pressure differential across the filter would rise sharply, causing the bypass valve to open, and the oil to bypass the filter. The theory is - lubrication with unfiltered oil is better than none at all.
Other advantages to the popular "spin-on" filter include reduced cost and greater convenience since they are entirely disposable units that need only be removed and discarded when changed. |
 |
U = legacy oil filter bypass housing.
Early Gen III motors had the oil-filter bypass mechanism located here. The oil filter bypass allows oil to bypass the oil filter and continue to circulate in the event that the oil filter becomes sufficiently plugged to cause a dangerous drop in oil pressure. If the filter becomes completely clogged with debris, the bypass opens and does not allow the filter to restrict oil flow through the engine.
LS2 and other later Gen IV motors switched to an internal filter bypass, located in the oil filter, in 2007. Moving the bypass to the filter ensures that the mechanism is fresh and unobstructed each time the filter is changed. |
|
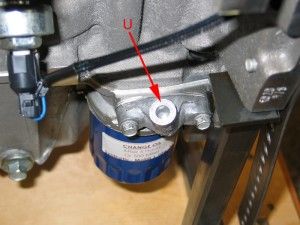 |
The bypass housing remains though, which is a good thing, as it can easily be drilled and tapped to 1/8" NPT and makes a good location for an oil temperature sensor. |
As good as they are, though, typical parts store "spin-on" filters may not be the best choice.
Before we look at the alternatives, let's take a quick look at what the filter does and how.
The filter's job is simple - it must filter out contaminants in the oil as the oil flows through. Contaminants include external contaminants - airborne particles such as bacteria and dust that are ingested by the engine; as well as internal contaminants - trace amounts of wear metals from bearings and other internal parts.
The trick in making a good filter is balancing efficiency vs flow. Efficiency is the filter’s ability to capture contaminants. The more efficient a filter is, the higher the percentage of contaminants it will remove from the oil. To make a filter more efficient, the spaces between the fibres in the media are made smaller. It would be fairly simple to make a filter 99.99% efficient - the problem is, by doing so, you restrict the flow through the filter. Obviously restricting the flow of the oil is not a good thing, and so the filter's construction must balance efficiency with flow.
This is where aftermarket high-quality oil filters can outperform the more common spin-on style. Oil filter design is a delicate balance between efficiency, flow, and lifespan that hinges on the the filter medium, surface area of filter medium and oil pressure. The finer the medium, the smaller the particles it will filter, the greater the percentage of particles it will filter - but the greater the flow restriction across the filter and the more quickly the filter will clog.
Designed for the mass market and cheaply produced, most spin-on filters use a paper-based media and reach a compromise between efficiency and flow based on normal automotive use and relying on the pressure bypass valve for backup.
Racing filters take a different approach - they use more expensive media (often synthetic), higher quality construction, and do not incorporate a bypass valve.
A typical parts store paper-media spin-on oil filter may filter about 60% of particles in the 20-30 micron range (a human hair is about 60 microns in diameter), whereas a cartridge-style racing filter may achieve efficiencies upwards of 80% at the 8-10 micron range. |
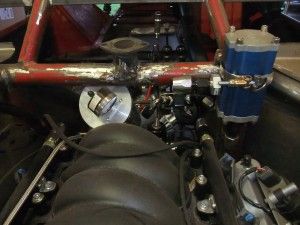 |
The blue cylinder to the right side of this pic shows my remote-mounted Canton Racing Products CM -45 canister (cartridge) style filter.
The housing is machined aluminum and is plumbed using -12AN fittings. "IN" is at the bottom and "OUT" is on the left side in this pic.
This unit is part number 25-106-CM-45. |
|
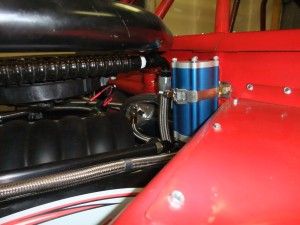 |
This canister oil filter has a 6" tall remote housing, and uses a 4-5/8" synthetic fibre element. The housing is made from a light weight 3-1/4" aluminum square extrusion, 1-1/16" -12 straight O-ring ports, and a removable top cap that allows for easy element replacement. The filter has a blue anodized body and a clear anodized end cap. A stainless steel mounting clamp is included. |
|
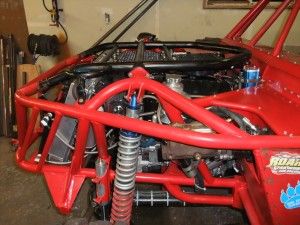 |
Another advantage of the an aftermarket racing filter is the "cartridge" design. Unlike a spin-on filter where the filter housing and filter element are contained in a single disposable unit, a cartridge style filter employs a permanent filter housing, with a replaceable inner filter element or cartridge. This design can be a significant advantage in high load, high rpm, high pressure applications as the oil filter housing is much more solidly attached. With a spin-on filter, the only thing keeping all the oil in the engine is the gasket at the base of the filter. If it should loose tension - from heat, vibration, or pressure, the single threaded mounting boss will quickly vibrate loose, the filter housing will depart the vehicle followed shortly thereafter by all the oil. Which isn't good.
In contrast, a cartridge style filter uses a filter housing that can be more securely mounted rather than relying only on the base gasket tension. |
|
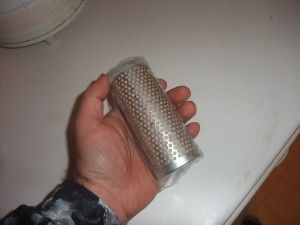 |
This is a picture of the synthetic fibre filter element.
CM filters were developed to better protect expensive racing engines. They are designed to handle a continuous high flow of oil while filtering out small particles and without the flow becoming restricted even when the filter is partially contaminated. The synthetic element is not affected by moisture which erodes paper elements, and it withstands pressure surges without collapsing or rupturing. In the years since their development these elements have proven themselves in NASCAR, SCCA, IMCA, IRL, and NHRA racing. |
CM elements filter out particles down to 8 microns, half the size of what the average spin-on filter can do, and have a flow rate that is far greater than that required by any automotive application, even when contaminated. Depth filtration extends filter element life because it can catch more contaminates without restricting flow. CM Elements can not be cleaned because they work on depth filtration design where particles are caught within millions of tiny passages which run throughout the element. This design allows for a much greater flow and the ability to hold far more particles than a conventional surface filter.
Placement of the filter in the oil circuit is a critical design element, one in which there are two different schools of thought.
One method is to place the filter just before the oil re-enters the engine. That is, as late as possible in the circuit. The thinking is, should an external component of the oiling system (like the cooler, plumbing, etc.) either allow entry of foreign material or suffer some internal breakdown (e.g. rust flaking off the inside of a cooler passge); then these contaminents will be filtered before they enter the engine.
The other methos is the opposite approach - place the filter as soon as possible after the pump. The thinking here is that the external components themselves deserve protection and that one of the greatest source of contaminents in oil is the engine itself from wear between metal parts. By placing the filter as early as possible in the circuit, these internally generated contaminents can be filtered before they can damage any of the external components of the oiling system. This is particularly useful in the case of an oil accumulator where the internal surfaces are precisely machined and require clean oil for sealing. As another example, should the pump fail or experience wear, if the filter is fitted early in the curcuit, it will protect the downstream components such as accumualtor, cooler, thermostat, and plumbing. One thing to note, if a filter is placed early in the curcuit it will experience, and therefore must be able to withstand, full system pressure; wheras a filter placed after the external circuit and just prior to the engine will experience less pressure as pressure will drop across the circuit.
One important consideration in the selection of filter location in the circuit, is the age and condition of the other extrenal components. For example, if the cooler, thermostat, and accumulator are brand new and known to be clean and free of contaminents, as well as of high quality construction and therefore unlikely to break down and introduce contaminents, then placing the filter first in the circuit is a viable option. If, on the other hand, the cooler is a used unit of unknwon history, even if well cleaned prior to installation, it is difficult to be sure of the exact condition, and it therefore could be harbouring contaminents that might enter the oiling circuit. If this were the case and the filter was first in the circuit, such contaminets would reach and pass through the engine before being filtered. In this case, it would be far better to place the filter at the end of the external circuit just prior to the oil entering the engine oil galleys.
Cooler
Under hard use, engine oil temperatures can easily exceed 300°F. To help ensure the longest possible oil and engine life, an oil cooler can be a very wise investment. |
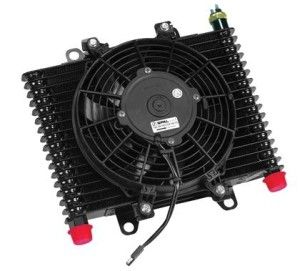 |
I chose a B&M Hi-Tek Cooler with integrated electric fan, Part # 70297.
It's a plate & fin oil-to-air cooler with 1/2" NPTF female inlet & outlet fittings.
It comes with a
9.5" diameter 12V DC SPAL suction fan.
The cooler measures 13.5 in. x 9 in. x 3.5 in.
The fan is controlled by a bi-metal
temperature switch.
ON-OFF points:
ON is 80°C±3°C (176°F±5.4°F)
OFF is 60°C±3°C(140°F±5.4°F) |
|
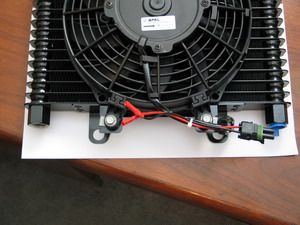 |
I chose this particular unit for 3 reasons:
1) The plate & fin construction is quite rugged and will hold up much better in an off-road environment than other styles (like the copper tube and fin style).
2) It has large 1/2" ports, which is important in an engine oil cooler. Anything smaller would cause an unacceptable pressure drop across the cooler. (for more tech on flow, pressure, and plumbing, see: The Plumbing Bible).
3) It uses a built-in fan, which gives me some flexibility in mounting location without having to mount it in front of the radiator and reduce or block flow through the radiator. In addition, it's a SPAL fan which i know to be high quality, reliable units. |
|
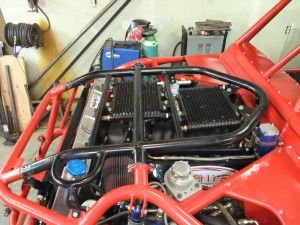 |
In fact, I chose to install two of these units, one for an oil cooler, and one for a transmission cooler.
Like everything else, cooler selection and placement is a matter of compromise - in this case between cooling capacity/efficiency, room for packaging, airflow, and the amount of plumbing you are comfortable running.
As mentioned - my top priority was to not place the coolers in front of the rad - I wanted to ensure maximum cool airflow through my rad so the only thing in front is a small PS cooler. These two big oil coolers would have blocked the whole rad and I wasn't happy with that. |
That left quite a challenge trying to find space to mount two large coolers where they wouldn't be too vulnerable and where they wouldn't be subjected to excessive heat from the exhaust.
Originally I had planned to mount them at the back of the rig, in the same way that some folks mount radiators in the rear. In the end, I got nervous about running the many extra feet of plumbing required and routing the engine's life-blood out of the engine all the way to the rear and back forward again; so I ended up mounting the coolers above the engine as shown. So far they have worked well positioned here, but I'm not convinced this is the aerodynamically optimal placement. The problem is, I'm out of options as the two of them take up a lot of space. |
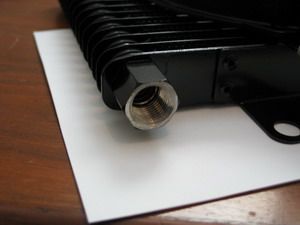 |
The ports are female 1/2" NPTF. NPTF are not the same as regular NPT threads, they are Dryseal USA (American) Standard Taper Pipe Threads aka American National Standard Taper Pipe Thread - Fuel. |
|
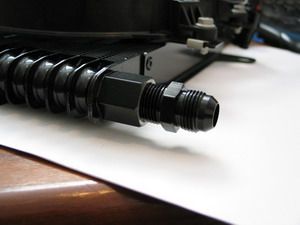 |
You can create a successful seal by screwing an NPT male thread into an NPTF female, as shown here (although you must use a supplementary sealant such as Teflon tape, just as you would in an all-NPT joint). |
This is the diagram for wiring the fan on the cooler using the integrated thermal switch.
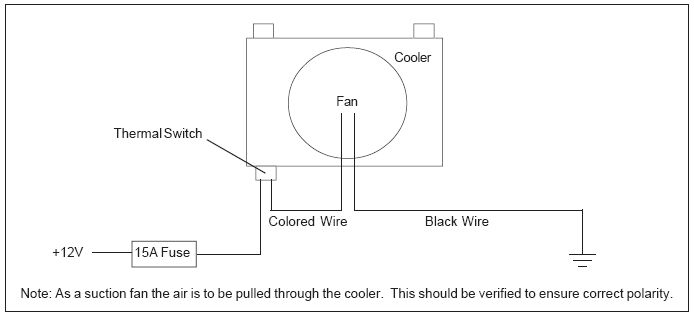
This is what I did at first, but I found the performance of the thermal switch to be poor. That is, it did not reliably switch the fan on and off. The fact that I have the cooler mounted flat horizontally may have been partially responsible for this, but in general these cheap, mass-produced, bi-metallic switches are not real thermostats and not the best way to switch a fan. Also, the on-off settings of the supplied switch are not optimized for engine oil - they are a little on the cool side. |
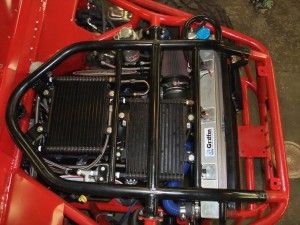 |
For the time being, I simply bypassed the thermal switches so that the fans come on with the ignition. This is simple and reliable.
Of course, the disadvantage to this is that it increases the time it takes the oil to come up to operating temperature, and given what we now know about temperature, viscosity, and lubrication - we know too-cold oil is as bad as too-hot.
The proper solution would be to install a true oil thermostat like the one shown below. |
Unfortunately, I hadn't originally planned for one and by the time I realized I needed one I was out of money, out of time, and out of patience with the project. It's the one thing in my entire LS2 install project that I wish I had done differently. |
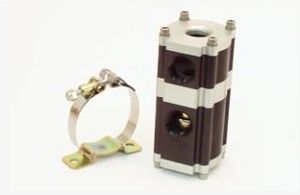 |
This is an example of a proper oil thermostat - this one is part # 22-480 from Canton Racing Products.
A proper thermostat like this operates on the same principle as the radiator thermostat and helps your engine’s oil come up to temperature quickly and holds it at the right temperature.
Remember, cold oil does not flow and does not lubricate correctly. Plus, pumping cold, viscous oil robs power. |
|
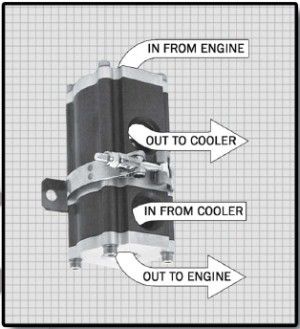 |
This particular thermostat is designed to bypass the oil cooler until the oil reaches 215°F. At 215°F water condensation in the oil will evaporate and the oil will be warm enough to flow and lubricate properly.
The thermostat housing is machined from a 3-1/4" square 6061 T6 aluminum extrusion, measures 6" tall and come with a black and clear anodized finish and stainless steel mounting clamp.
The oil ports accept 1-1/16" -12 O-ring fittings. (4 fittings required per unit). |
Accumulator
The heart of my oiling system is the Accusump 3-quart oil accumulator.
The purpose of the accumulator is to store a volume or "charge" of pressurized oil when the engine is operating normally so that it can release this pressurized oil to lubricate the engine if normal oil pressure should drop for any reason. This makes it a perfect addition to any offroad rig and invaluable insurance against engine damage that can be caused by flops, rolls, steep climbs, or off-camber driving. How long the engine is protected from oil pressure loss depends on the size of the accumulator used, engine size, and RPM. I chose the biggest available, which holds 3 quarts of pressurized oil. Anecdotally, this will provide from 15 to 60 seconds of running time with total loss of oil pressure (e.g. upside-down with the oil pickup completely uncovered). This should provide plenty of time to get the situation under control and/or shut down the engine before engine damage occurs. However, an accumulator is not designed for, nor will it allow you to drive for extended periods of time with no oil pressure - like when the rubber is sky-side up. Nothing can help you with that except perhaps an aerobatic-aircraft-style dry-sump system. Even the more common automotive-style dry-sump systems (like those on LS7-equipped Corvettes) won't do it, as they are designed for oil control under hard braking and high lateral G loads from cornering. If you look into the complexity of fitting a real aircraft-style dry-sump system that will truly allow you to run the engine indefinitely at any angle (including highly specialized internal engine modifications, multiple scavenge pumps, gimballed tanks, etc.); and realize the cost of such a system quickly outstrips the cost of the engine in the first place; you may well decide, as I did, that a decent accumulator and learning to keep the rubber side down might just be your best option.
Due to the way in which it functions, an accumulator can also act as a pre-oiler. That is, it can be installed and plumbed so that just before the engine is shut off a valve is closed, trapping the pressurized oil in the tank. Then, just before the engine is started, the valve can be opened, releasing the pressurized oil to lubricate the engine before the engine is started. I will have some more thoughts on this when we discuss the options for plumbing and valving the accumulator.
First let's have a look at the unit and exactly how it works. |
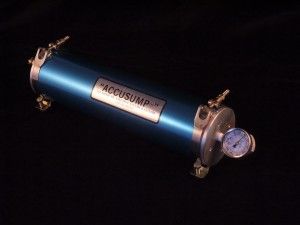 |
This is the 3-quart Accusump oil accumulator from Canton Racing products.
It is essentially a machined aluminum cylinder with an internal floating piston that separates it into two parts - a gas chamber at one end and an oil chamber at the other.
The internal floating piston seals against the inside of the tube creating two entirely separate chambers that are sealed from one another and the contents of which never mix.
In fact, it is very like the remote reservoir of a coil-over shock. |
|
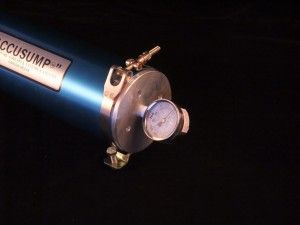 |
The gas end is the end with the pressure gauge... |
|
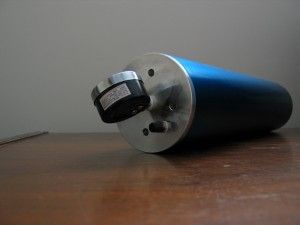 |
... this end also has a Schrader valve through which the gas charge is added.
The user charges this end with about 10-15 psi of nitrogen (you can use air, but nitrogen is best if you have it available as it contains less moisture, is more pure and stable and is therefore affected less by temperature changes.)
When you do this, the pressure you have added will force the internal piston all the way to the other end. |
|
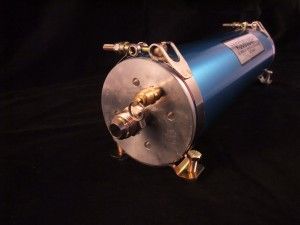 |
At the other end there is an inlet port which is connected to a pressurized oil supply line, and a safety valve that opens in the case of over-pressurization. |
|
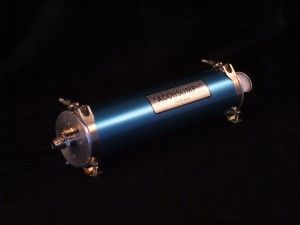 |
When the unit is installed and connected to the engine's oil supply circuit, nothing happens, the piston stays at the oil end until... |
|
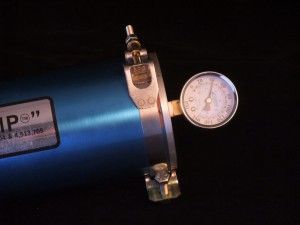 |
... the user starts the engine. at this point the engine develops oil pressure that exceeds the pressure of the gas charge in the gas chamber.
When this happens, the oil pressure pushes back against the piston and forces it back near the gas end. In this way, the majority of the accumulator is filled with pressurized oil when the engine is running normally. The engine's oil pressure will now register on the gauge.
Now, when there is a drop in oil pressure below the value of the pressure in the gas side (say 10 psi), the gas pressure takes over and forces the oil back out of the accumulator and into the engine for lubrication. |
When normal oil pressure is restored by the oil pump, the pressurized oil again overcomes the gas pressure and the accumulator is once again charged with oil and ready to work again.
The following animated graphic illustrates the charging of the oil accumulator when the oil pump is functioning normally.
As you can see, the oil pump draws oil from the tank (oil pan), and sends it to the engine for lubrication. Along the way, some of this pressurized oil is diverted and fills the accumulator, pushing the IFP towards the gas side (the end with the pressure gauge).
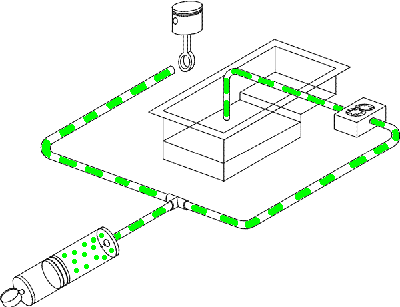
When the oil pickup tube in the oil pan is uncovered, as here, the oil pump loses suction and no longer pumps, and therefore system oil pressure drops.
When this happens, the pressure in the gas side of the accumulator takes over and forces the piston down which pushes the oil out and into the engine for lubrication. If the supply line to the accumulator uses a "T" from the normal oil circuit, as shown in this example, a check-valve is used to ensure the precious supply of oil is not wasted by being sent backward through the circuit into the oil tank (oil pan).
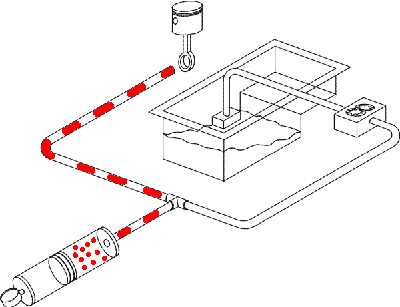
|
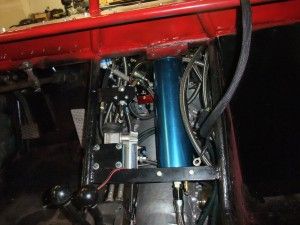 |
The length of time the accumulator buys you depends on its size and therefore the amount of oil it can store.
I chose the largest available, which is the 3-quart model, but fitting such a beast can be a real challenge.
Mine is mounted in the "transmission tunnel" just below the interior panels. You don't want to mount an accumulator in the passenger compartment as you want to avoid running hot pressurized oil in the vicinity of personnel. |
|
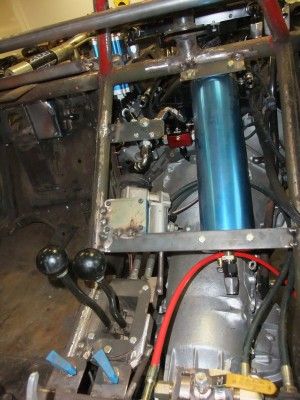 |
You can mount the unit in any orientation and it will work, but there are a couple of considerations to keep in mind as you struggle to find the room to fit the beast.
1) It is best if you can mount it with the oil-end at least slightly higher than the gas-end, as this will ensure any bubbles in the oil (engine oil can cavitate and aerate under hard use) do not get trapped. Note that this is NOT how mine is mounted in this picture as I needed to mount it as shown so the plumbing routing would work and I would still be able to access the pressure gauge and schrader valve.
2) The cylinder must ONLY be clamped at the very ends, otherwise tightening the clamps may slightly distort the tube and thereby cause the floating piston to hang up.
3) Mount the accumulator where it will not be stressed, twisted, bent, subjected to exhaust heat, misused as a support or step, or where it will be vulnerable to rock or debris damage.
4) For safety, avoid plumbing hot pressurized oil through the passenger compartment.
5) Install the accumulator with due consideration to the required plumbing and the placement of any valves, if used. See below for plumbing and valve considerations. |
|
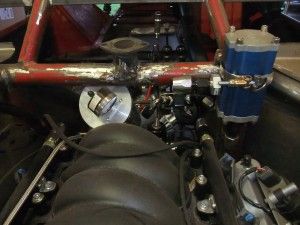 |
This picture shows the gas-end of my accumulator in its installed position. It is important that access to the schrader valve be maintained in the installed position so that necessary adjustments or top-up to the gas charge can be made.
In this picture, the supplied pressure gauge is still installed. However, after installation I found myself wanting to monitor the gauge and the accumulator's performance. So, I installed a slight modification. The port for the gauge is 1/4" NPT, so I removed the gauge, installed a 1/4" NPT to 1/8" NPT adapter, and then installed an old mechanical-style oil pressure gauge I had lying around. |
|
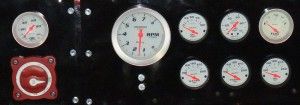 |
In this pic, the accumulator gauge is immediately above the large red power switch, and the normal oil pressure gauge is on the top row just to the right of the tachometer.
When the accumulator is charged, the accumulator gauge will show this pressure (note, accumulator not charged when this pic taken). This pressure will of course vary somewhat with ambient temperature, so adjustments at the schrader valve may need to be made (one reason why you need to be able to access it).
The instructions say to charge to 7-10 psi. This is the pressure below which oil pressure must fall for the accusump to kick in and discharge oil to the engine. It is also then, the pressure above which oil pressure must build in order for the accusump to fill or "recharge".
On my gauge 7-10 psi is almost unreadable and so I run my accumulator at 10-15 psi gas charge pressure. |
Accumulator Plumbing.
Obviously, the accumulator must be installed in the pressure side of the engine's oiling system. That is, between the pump and the engine oil galleys.
There are two main methods to plumb the accumulator, they are:
- Install it inline using a T-connection to other external oil system components (such as a remote filter or oil cooler); or
- Plumb it directly into the engine's oil passages (oil galleys).
|
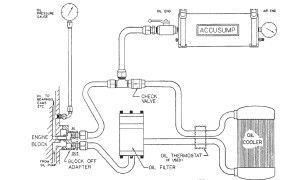 |
Inline T-connection.
The advantage to this method, pictured at left, is that it can be done on any engine. Even if you don't have any external oil system components, you can use a "sandwich" style oil filter adapter to provide a port into which you can plumb the accumulator. |
|
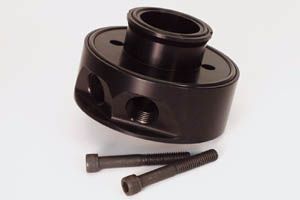 |
This is a "sandwich" adapter. It gets its name because it gets sandwiched between the engine block and spin-on style oil filter. It gets installed in the stock location of the oil filter, and then the oil filter is attached to the other side. In this manner, it provide one or more oil ports - one of which can be used to plumb the accumulator. |
Alternatively, if you have other external oiling components, including a remote oil filter, your system will already incorporate some kind of input adapter, often called an "oil cooler adapter" or a "remote oil filter adapter". |
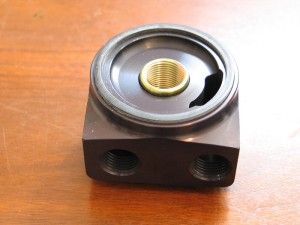 |
My system uses this 90° rotating remote oil filter adapter.Made from billet aluminum, it is Canton part number: 22-593 (53020807). It spins-on to the stock 13/16"-16TPI oil filter thread and seals against the pan with stock diameter 2-5/8" seal.
It provides 1/2" NPT in and out ports for plumbing a remote filter.
From this view, the port on the left is the INLET and the port on the right is the OUTLET.
Its design permits it to be rotated, providing for adjustable positioning of the the two 90 degree inlet and outlet ports, which can greatly simplify plumbing. |
Do not confuse a sandwich adapter with an input adapter, as the two are different and not interchangeable. Sandwich adapters access oil flow as it passes to or from the filter and provide a port for installing items such as an external oil pump, or an accumulator. A sandwich adapter will flow oil to the engine whether or not the oil ports are used.
An input adapter diverts the oil flow and provides an in and out port for installing an oil cooler or remote filter. The design of the input adapter requires the oil exiting the adapter to return back to the adapter, you cannot plug off the ports in an input (cooler/remote filter) adapter.
That said, I have chosen not to plumb the accumulator inline with my input adapter and the other oiling system components because of the disadvantages of this approach.
Namely, that it requires a T-fitting connection, and as such, a check-valve must be used to prevent oil discharged from the accumulator from flowing the wrong way. The problem with this is - in order for the orifice of the check valve to be large enough as to not cause any flow restriction (last thing you want in an external oil system is to restrict the flow of precious engine oil) the body and therefore connections of the check valve have to be way oversized - which means taking up a lot of space and cobbling together all sorts of multi-step adapters (each a potential leak point) to integrate the over-size check valve into the oil lines. I hate doing that.
The other problem with the "T" approach is the length and complexity of the plumbing to charge and discharge the accumulator when, what you really need in a system designed to protect your engine as it starves for oil, is a nice, short, simple, large diameter, high-flow, straight shot from the engine oil galley to the accumulator. |
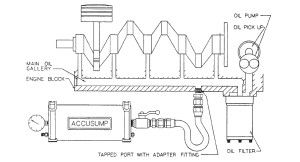 |
Direct to Block
Which leads to the other method of plumbing an accumulator - connecting it directly to the engine's oil galley.
The picture at left of this approach shows an engine with a standard spin-on style oil filter but this can obviously be done with or without a remote filter and/or other external components.
It is definitely the preferred method, but the trick is finding an appropriate port in the engine, of the correct size, to which you can connect the accumulator. An accumulator should use -06 size plumbing as a very bare minimum, with -08 being much preferred and -10 even better (though sometimes harder to fit).
Of course, the
minimum diameter will depend somewhat on the
length of the plumbing used too, with the longer the oil line to the accumulator, the larger diameter it should be. |
|
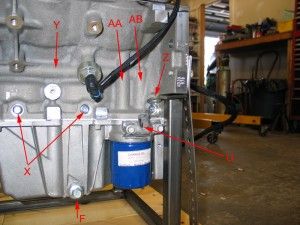 |
This pic shows some of the features of my LS2 engine block with regards to oiling. Most of these features are common to other Gen III/IV V8's.
Y = Main oil galley.
AA = Dirty oil galley, from oil pump to filter.
AB = Clean oil galley, from filter up to main feed galley (runs through the lifter bodies) and top of engine through pushrod passages.
Z = Main oil galley port, 16mm x 1.5 straight thread with crush washer. This location is post-filter and makes an excellent location to plumb an oil accumulator - IF you can get an appropriate fitting installed without having to grind the block. |
|
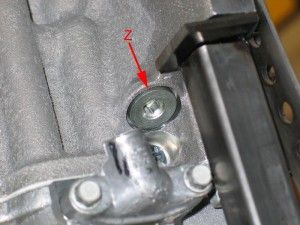 |
Z = Main oil galley port.
You can see how tight it is to try and get a fitting installed in this port, especially one that converts to a male AN fitting sufficiently large for oil accumulator plumbing (i.e. AN-10).
So, it seems this port would have been an excellent place to plumb an accumulator - I just couldn't find a way to accomplish it. |
|
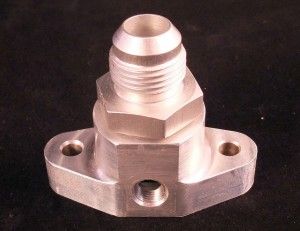 |
I was pondering what to do, and whether I would have to install my accumulator using a "T" fitting, when my friend Adam Woodlee from Wide Open Design Machine & Fab came through with a brilliant idea and a great little component to save the day.
This is the Woodlee oil accumulator adapter for Gen III/IV V8's like my LS2. |
|
 |
It is designed to fit in place of the stock oil filter bypass housing (labelled "U" in this pic). |
|
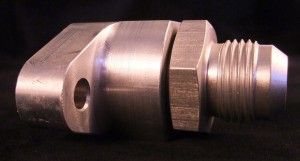 |
Machined from billet aluminum, it incorporates a built-in -10AN male port for plumbing the oil accumulator line... |
|
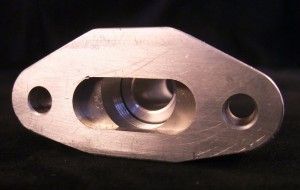 |
... and is machined on the back side to use the stock gasket and fasteners. |
|
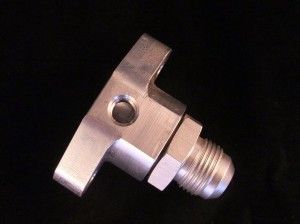 |
It also has a 1/8" NPT port machined in the top surface to facilitate an oil pressure gauge or oil temperature gauge. |
|
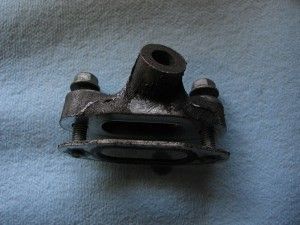 |
This is the stock oil filter bypass housing removed from the block. The Gasket and two bolts are re-used. |
|
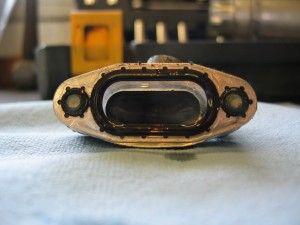 |
The stock steel-and-rubber oil filter bypass housing gasket. |
|
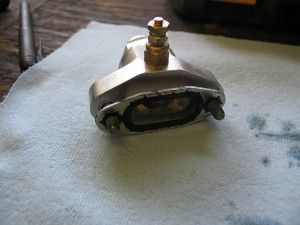 |
Here is the Woodlee adapter with an oil temperature sending unit installed and the stock bolts and gasket in place for installation to the block. |
|
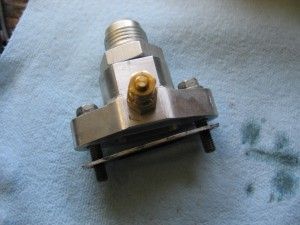 |
It is an ingenious idea and a great little component that makes for the perfect way to plumb an oil accumulator to an LS engine.
If you have an LS engine you should definitely have an accumulator to protect it, and if you have an accumulator and an LS engine, you should definitely plumb them using this clever little custom adapter. |
|
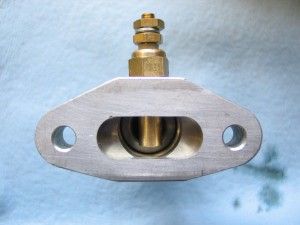 |
One catch, if you plan on using the 1/8" NPT port, depending on what you screw into it (shown is an electric gauge temp sending unit), it may block a large portion of the flow.
I found the example at left to block too much of the flow for me to be comfortable with, so I installed the temp sender in a T-fitting attached to the top of the Woodlee adapter (see picture two rows below). |
|
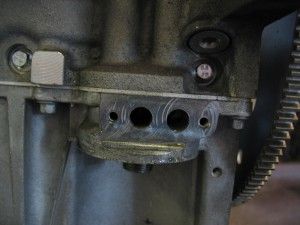 |
This is the block with the stock oil filter bypass housing removed... |
|
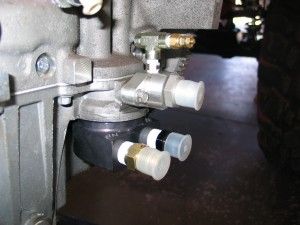 |
...and this shows both my Canton remote oil filter adapter and the Woodlee accumulator adapter installed.
You can clearly see the:
- Oil temp gauge sanding unit
- -10AN oil accumulator fitting (silver)
- -10AN out port (black) - to the remote filter.
- -10AN in port (brass) - from the oil cooler.
|
|
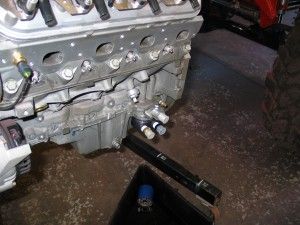 |
Another view of the oil system adapters in place on the block.
The nice thing about the male -10AN fittings... |
|
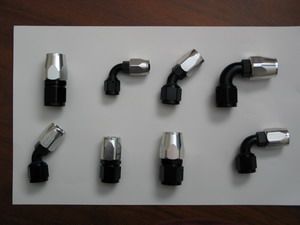 |
... is that you can connect to them using 45°, 90°, 180°, or straight hose ends, like these from Russell Performance. |
|
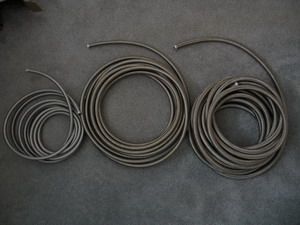 |
For the entire plumbing system in my buggy, including the oiling system, I exclusively used Russell Performance ProFlex hose in -10, -08, and -06 sizes... |
|
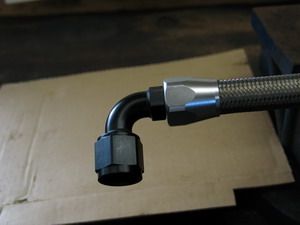 |
...combined with full-flow field-attachable AN hose-ends in ProClassic black/clear aluminum finish.
I used -10AN to plumb the entire oiling system, including remote filter, cooler, and accumulator. |
|
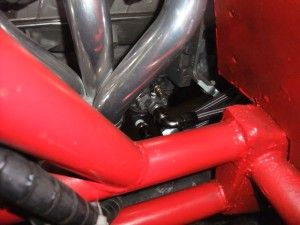 |
The result is a neat and tidy plumbing job that routes the critical oil lines in an optimum fashion.
Here, 90° hose ends are used to route the lines away from the heat of the block-hugger Doug Thorley exhaust header. |
Valving the Accumulator
One final consideration in installing and using an accumulator is
whether or not to valve the accumulator, and if so, which kind of valve to use. This decision can have a large effect on where and how you mount the accumulator and the size and routing of the plumbing to it.
Let me explain. As per the description of how the accumulator works with the engine running, we can see that it is "fully automatic", requiring no intervention or operation from the driver, and requiring only a direct connection to the pressure side of the engine oiling system (whether by "T" connection or direct connection to the block). Simple and easy.
So why the valve?
Well, if we install a valve capable of being operated by the driver, the accumulator can function as a pre-oiler as well, meaning it can be used to supply pressurized engine oil to the engine before starting, which aides in limiting wear during startup.
It works like this. As we know, while the engine is running, the accumulator is charged with pressurized oil. Before shutting off the engine, if we close a valve located between the accumulator and the engine, we can "trap" a full load of pressurized oil in the accumulator. Then we shut the engine off. Now, before starting the engine, if we open the valve, the trapped or stored pressurized oil is supplied to the engine providing lubrication in the critical first moments before the oil pump is supplying full oil pressure to the engine. Once the engine is started, the valve remains open and the accumulator functions as we have already described. |
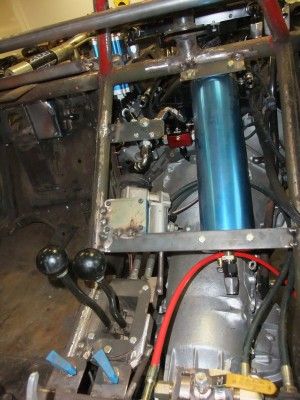 |
There are three basic ways to install a valve:
- Install a manual valve where the driver can reach it, either directly on the accumulator or in the oil line between engine and accumulator. This can place some real restraints on how/where you mount the accumulator and/or how you route the plumbing. In the pic at left you can see the manual valve with yellow handle at the bottom of the pic. Be aware that this method increases the length and complexity of the plumbing required (which is one reason I later deleted the valve and run without one - more on this below.)
- Install a manual valve and use some sort of cable activation or other remote mechanical means of actuating the valve.
- Install one of the available electrically-operated solenoid valves. These can even be wired through the ignition switch so you do not have to remember to open and close the valve at appropriate times. While convenient, and allowing more flexible mounting options, these units are generally not considered reliable or robust enough for racing use and I personally would not use one in an offroad rig or offroad racer. Also, be aware that some of the electric valves only permit a fairly slow refill of the accumulator - not what you want in an offroad racer!
|
Because I wanted a simple, reliable, bulletproof method of protecting my engine from loss of oil pressure in all conditions I ended up deciding to delete the valve altogether and run a big, fat, straight, simple -10AN stainless steel hose directly from engine oil galley to accumulator. Here's why:
- You have to remember to operate the valve. Seems simple, but if you start and stop many times, you may eventually forget one time, and if you forget with the valve closed, the accumulator is useless. Murphy's law says this is the time I will roll over with the engine at 5k rpm and need the accumulator most. Since I bought the accumulator to protect the expensive engine in case the worst happens, I'm happy to lose the pre-oiler function in return for knowing I can never forget and the accumulator will always work.
- Lots of other folks drive my rig, particularly my 11 year-old son. With triple-sticks, dual cutting brakes, and front and rear lockers, there is enough for other drivers to worry about without adding another critical valve. And again, Murphy says one of them will forget to open the valve immediately before rolling and roasting my bottom end!
- Any valve adds more fittings and therefore more potential leak points in the system. It also necessitates more plumbing required (almost certainly with more pressure- and flow-robbing twists and turns). I want a simple, effective, reliable, high-flow accumulator protection system which is best achieved with the least and straightest plumbing and fewest fittings.
- Pre-lubing is only a benefit on cold start. If you have only just shut down for a couple of minutes, there is still plenty of oil on and between the wear surfaces to make it unnecessary. And knowing what we now know about temperature and viscosity and engine oil and lubrication - I'm not at all convinced that a dump load of cold thick oil just before start is really all that beneficial. It may be, but I think to be truly worth the effort as a pre-oiler the accumulator would have to be held at a constant 200°F - and I'm certainly not about to add the complexity of a system like that!
- A system without valving and with less hose and fittings costs less, takes less space, and weighs less - but still protects the engine from oil pressure loss every bit as well as a system with a valve.
- I have a technique that provides something of a work-around for pre-lubing, but there is no work-around for an accumulator with a closed or stuck valve when you're rubber-side-up. What I do at start is this: Instead of flipping the ignition switch and then engaging the starter button, I have both ignition switch and starter button powered separately. That way, I can roll the engine over a few times on the starter (very low load and low RPM), getting the oil pumping around the circuit, and then flip up the cover and engage the ignition switch which starts the engine.
|
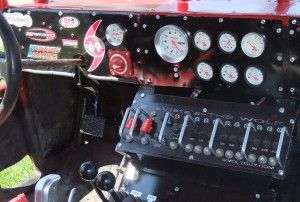 |
Plenty of knobs dials and switches - don't need any extras! |
|
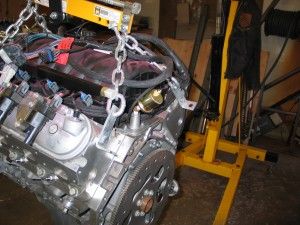 |
A not-terribly-relevant picture of the electrical oil pressure sender installed using a 45° adapter in the port at the driver side rear of the LS2 head - but I didn't have any better place to put it in this article! |
The following information on accumulator checks and procedures are taken largely from the Canton Accusump Instruction Booklet.
SETTING THE PRE-CHARGE
After your accumulator is installed, perform the following checks / procedure:
With the valve (if you have one) in the open position (electric units energized) and the engine not running; pressurize the
Accusump™ to 60 psi. This will ensure all the oil is out of the unit and the piston is all the way to the oil end. While
the Accusump™ is pressurized to 60 psi check all the fittings (gauges and lines) for leaks. Apply soapy water to each
area and check for bubbles. If possible, wait overnight to ensure there is no loss of pressure. For the unit to operate
correctly there cannot be any leaks in the air side. Temperature change will affect pressure.
Once you are sure there are no leaks, bleed down the air pre-charge to between 7 and 10 psi (BV note: as mentioned - I use 10-15 psi). Now when you
start the engine and open or energize the valve, the pressure in the air side of the Accusump™ should increase to
approximately that of your engine oil pressure. After you close the valve and shut your engine off, check your oil
level. Add oil as required to compensate for the oil being held in the Accusump™.
Under normal conditions the pre-charge should not need resetting after the initial set up. However, if a leak occurs
or if the unit's pre-charge seems to have changed you may need to reset your pre-charge to ensure your Accusump™
performs correctly. To reset your pre-charge, set the valve to the open position (electric units energized) while the
engine is not running; and pressurize the Accusump™ to 60 psi. Next bleed down the air pre-charge to between 7
and 10 psi.
Under no circumstances should the safety valve be removed, as this will void the warranty. If oil leaks from the safety valve, be sure that it is sealed with Teflon tape and tightened; the safety valve is hand tight when delivered and
requires final tightening after installation of the Accusump™ valve. If oil still leaks from the safety valve, there is a
problem in the installation. These valves are very reliable and are set to open at 175 PSI, which is far above the
pressure the unit would see if installed correctly.
NORMAL OPERATION OF THE ACCUSUMP
Pre-oiling
With manual valve units: immediately before starting the engine, open the oil valve on the Accusump™. This will
purge air from the oil gallery and pre-oil the engine before it is started. With electric units wired into the ignition, this
will happen automatically when the ignition is turned on.
Surge Control
During operation of the engine, the Accusump™ will operate automatically to supply oil to the engine any time that
the oil pump loses suction due to oil surges. Should there be a failure in the oiling system, the Accusump™ will
supply 15 to 60 seconds of oil (depending on engine size and speed) to protect the engine.
Shut Down
During shut down the Accusump™ will hold whatever pressure your engine has at the time it is shut off. On manual
valve units you will need to close the valve before shutting the engine off. On electric units, the valve will close
automatically when the engine is shut off. If the engine has low oil pressure at idle you may want to hold the engine
at a higher speed as you close the valve to develop more oil pressure for pre-oiling. If the manual oil valve is left
open when the engine is shut off, the Accusump™ will not store its oil and require refilling at start up. It may be refilled
by leaving open the oil valve during start up to allow oil to enter the Accusump™.
NORMAL CARE
There are Accusump™ units that have been in service for many years and have bores which look like new. The key
to long life for the Accusump™ is proper care and oil filtration.
1. The Accusump™ should be protected by a quality oil filter that does not have a bypass. The filter should be
replaced and inspected at frequent intervals. The life of your Accusump™, like the life of your engine, will depend
on how clean your oil remains.
2. The Accusump™ tube has close tolerances of roundness; care must be taken that the tube is not distorted. The
unit should be mounted so that it is not twisted or bent, however slightly. Do not use the Accusump™ as a step
or allow anything to be dropped on it. The Accusump™ is a precision piece of equipment.
3. Keep the dust cap on the air valve to prevent the introduction of dirt into the air end of the unit.
4. When breaking in a fresh engine do not operate your Accusump™ if it is equipped with an electric valve.
Passages in the valve can clog with the assembly lube that is present in the oil during engine break-in.
ENGINE FAILURES
Should an engine failure occur or the oil become contaminated the Accusump™ should be cleaned and tested.
All lines and components of the oil system must be flushed and cleaned. We recommend that if a unit needs to be
cleaned, tested and/or rebuilt, it should be sent back to the factory. Improper disassembly can cause damage to the
Accusump™ and may be very dangerous.
IMPORTANT PRECAUTIONS
The following precautions must be taken for your Accusump™ to operate correctly. Failure to do so can result in
damage to the unit.
1. Never allow your Accusump™ to become hydraulically locked, that is, having the unit totally filled with oil with the
valve closed. There should always be a cushion of air (gas charge) in the Accusump™ when the valve is closed.
2. There should be a 7-15 psi. pre-charge of air pressure when the unit is totally empty of oil.
CAUTION!!!
The Accusump™ tube's inside diameter has a very smooth finish. Should this finish become damaged by foreign
material (from engine failure or contaminated oil), the piston seals will wear rapidly, leading to malfunctioning of the
Accusump™. Use of an oil filter without a bypass is encouraged. We recommend our CM high flow non-bypassing
filter. Should the bore of the Accusump™ tube become scored, the entire Accusump™ unit will become unrepairable.
If possible, plumb the filter before the Accusump™.
MAINTENANCE
1. When in operation, the reading on the air gauge of the unit should increase and decrease with engine oil pressure
fluctuations.
2. Routinely check the pre-charge pressure with the unit totally empty of the oil to make sure air has not leaked out
of the unit. This is extremely important when a remote air gauge is used.
3. Never bleed air from the unit while in operation or when full of oil as this will defeat the purpose of the pre-charge
and make the unit ineffective.
4. These units should not be mounted in a place where they can become excessively hot, especially not in a place
where they will absorb heat after the engine is shut off and the Accusump™ control valve has been closed.
5. Improper disassembly can cause damage to the Accusump™ and can be very dangerous.
TESTING YOUR ACCUSUMP™
Check the Accusump's ability to fill.
Make sure your Accusump™ is working correctly. After the pre-charge has been set according to the installation
instructions, run the normal engine shut down procedure: with the engine oil pressure up, close the valve on the
Accusump™ (cut the power to electric units) and shut the engine off. The pressure showing in the air gauge should
be close to what the engine oil pressure was during shut down. The oil level in the oil pan should be at the full mark.
Check the Discharge
Open the valve (power up the electric units) with the engine off. You should hear the oil discharge into the engine
and see the pressure on the air gauge drop down to the pre-charge setting and the pressure on the engine's oil
gauge go up. If not, reset the pre-charge. The engine oil level will be above full by the amount that was stored in
the Accusump™.
Check the Refill
Start the engine, establish good oil pressure and open the valve (electric valves will automatically open to fill), oil
should enter the Accusump™ and the air pressure should increase to approximately that of the engine oil pressure.
The time involved will be based on the valve used and the size of the unit.
TROUBLE SHOOTING
Accusump™ not filling or filling too slowly
It should be noted that the standard electric valve units fill slowly. The design of the valve is to ensure that too
much oil is not diverted from the engine during refill. These units are recommended for pre-oiling and not for surge
control. The EPC electric valve will fill slowly until the pressure threshold is reached at which time it will rapid fill.
Other reasons for slow or no refill:
1) The manual valve is not being opened completely.
2) The EPC is wired incorrectly. When the pressure is above the threshold, the valve should not be energized.
3) The wrong EPC pressure threshold was selected for your engine's pressure range. The pressure threshold
should be below the engines normal operating pressure.
4) The EPC valve may be plumbed incorrectly. The pressure sender should be installed closer to the engine than
the electric valve.
5) The electric valve may be installed backwards. It should be mounted so the arrow on the valve points away
from the Accusump™. When the valve is mounted backwards oil will not enter when it is in the off position.
6) The feed lines or connecting port is too small.
7) The pre-charge is too high and not letting oil enter.
8) The unit is bent, distorted or mounted incorrectly.
Accusump™ not discharging correctly
1) The manual valve is not open fully.
2) The electric valve is installed incorrectly. The arrow should point away from the Accusump™.
3) The electric valve has become contaminated with engine assembly lube or another foreign substance and is not
working correctly. The unit will need a rebuild in this case.
4) If a check valve is used, it could be installed incorrectly. The arrow on the check valve indicates direction of flow.
5) Electric power is not reaching the electric valve.
6) The EPC valve may be plumbed incorrectly. The pressure sender should be installed closer to the engine than
the electric valve.
7) The hose or ports used to connect the unit are too small.
8) The pre-charge is set too high and no oil has entered the Accusump™.
9) The pre-charge was lost or is too low.
If you are using the canton EPC electric valve you should note that it operates in a unique way from the other valves. The
EPC valve is designed to only discharge at the threshold pressure of the EPC valve, regardless of the Accusump's
total held pressure. The EPC unit will only discharge when the engine pressure is at or below the threshold pressure.
Accusump™ not holding a pre-charge
Accusumps™ not holding a pre-charge can be an indication of a leak in the air side of the unit, most common when
remote gauges are used. Review recommendations under the leak section that follows.
Accusump™ leaking
To locate the source of the leak check all lines, fittings, and gauges. Leaks on the oil side of the unit are likely to produce
an oil drip. Leaks on the air side of the unit can be found by pressurizing the unit to 60 psi then applying soapy
water to each area and checking for bubbles. Inspect and tighten any leaking fittings or gauges. To verify your unit
is leak free we recommend pressurizing the unit to 60 psi then waiting overnight to confirm the unit has retained the
pressure. Note: A temperature change will affect pressure.
Final Accumulator Thoughts
Let me close the topic of oil accumulators with a few more thoughts on why I chose to install one, and why I prefer it over a fancy oil pan design.
The facts are:
- Engine damage is cumulative, especially that which occurs from inadequate lubrication - every time your oil pressure fluctuates below the required level, metal-to-metal contact can occur, causing wear, especially under load. When a part fails because of an oiling system problem or inadequacy, it usually will fail under load. If this is allowed to happen, the effects will be severe and expensive.
- Your engine needs a constant, sufficient volume, and uninterrupted flow of the correct viscosity pressurized oil for lubrication … this especially true for high performance, racing, high load, and high RPM applications.
- When an engine is run at high RPM's, 60% to 100% of the "usable" oil is trapped or has been pumped into the upper areas of the engine, "away" from the oil pump, and is not in the oil pan. This can lead to oil starvation when it is most needed by your engine. This is the vicious double-edged sword - it is during acceleration, hard cornering, climbing, or other condition of highest load when the engine most needs optimum lubrication but also when it is most likely to experience loss or lack of lubrication. Couple this with the fact that if an engine fails under these conditions the results are catastrophic, and the need to optimize your oiling system, particularly with the use of an accumulator, is clear - especially if you have any significant amount invested in your motor.
- Even if you have invested in expensive oil pans with trap doors, baffles, "check balls," or kick outs, If there is an insufficient amount of oil in the pan, even the "best" or most expensive oil pan on the market cannot keep enough oil around the pick up, the oil pressure will be unstable, oil flow will not be sufficient, and engine damage can occur.
That's why I don't bother with aftermarket pans and why I use an accumulator.
People with fancy oil pans that drive like old ladies are free to disagree with me ;-)
PCV Oil Control
The final topic I'm going to tackle on oil and oiling is the subject of oil control. The term "oil control" refers to designs and practices used to eliminate or minimize the unwanted consumption of motor oil as the engine is operated. It encompasses a number of diverse topics including selection of the right viscosity of oil for the engine, allowing the engine oil to warm up properly before hard use / high revs, and keeping the engine (particularly piston rings and valvetrain) in good working order.
An important component in oil control is the Positive Crankcase Ventilation or PCV system.
The purpose of the PCV system is to relieve the pressurized gasses created in the crankcase by the pumping of the pistons, scavenge these vapours, filter out the oil vapour so it is not consumed by combustion, and then return the vapours to the intake manifold to be combusted.
In order to do this, crankcase vapours are drawn from the crankcase, up through the engine where they exit through the valley cover and are carried via an external tube to the intake manifold. This is the so-called "dirty" side of the system as the gasses contain oil vapour.
Of course, if we are removing gas from the crankcase, we must also replace it. The "clean" side of the PCV system provides fresh air from the throttle body (i.e. post air filter) to a port in the right rocker cover, to replace the scavenged crankcase vapours. |
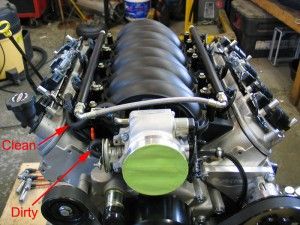 |
Uppermost hose is the clean side.
Small, looped hose is the dirty side. |
|
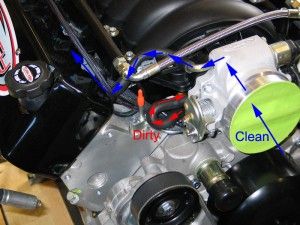 |
LS2 PCV system air-flow illustrated. |
|
 |
This pic illustrates the path that fresh, clean air takes in the system. |
|
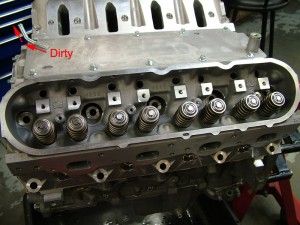 |
This pic illustrates the port in the valley cover from which the dirty crankcase vapours are drawn. |
What can't be seen in the above pics are the oil separators. Externally, the LS2 PCV system appears only to be a couple of hoses - a clean one connecting the throttle body to the rocker cover, and a dirty one connecting the valley cover to the intake.
But there is more to the system than that. There are air/oil separators on both sides of the system. The most important is the dirty-side separator, as that is where the oil is in the crankcase vapours. Essentially, the separator is a baffling system that separate the oil from the air and drops it back into the crankcase so that only the air is burned. The better the oil is separated, the less oil will be burned, and the less oil consumption will occur.
There is also a separator on the clean side. This is required because, under certain conditions (like wide open throttle), blow-by increases to the point that it exceeds the capacity of the dirty side to extract and consume the gasses. When this happens, the air flow can reverse, and air comes out of the crankcase from the clean side. Obviously, under these conditions, you don't want to dump a lot of oil into the throttle body, so a separator is also required on the clean side.
Under normal conditions, this reverse-flow situation is not a problem, because the intake manifold produces enough vacuum to constantly purge the crankcase vapours adequately. There will always be some oil consumption, but it is normally very little. However, at sustained WOT and high engine speed there is no longer sufficient manifold vacuum to help pull the air from the crankcase. At the same time, more blow-by is produced. This combination may exceed the capacity of the dirty air side, which is sized for most normal light load engine operation, (if it were sized larger, the engine would consume excessive oil under normal conditions, which would not be beneficial) and reverse flow can occur. Therefore, the clean side also has a separator to ensure reverse-flow conditions don't dump oil into the throttle body.
All of this said, as good as the stock PCV system may be, in spirited use, it can use a little help, or you can end up with oil in the intake.
The help comes in the form of installing a small air/oil separator in the "dirty side". Instead of the standard hose simply looping between the valley cover and the intake manifold, we install a small filter to separate any remaining oil vapour in the blowby gasses, before directing the gas back into the intake manifold to be combusted. |
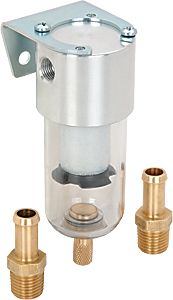 |
There are several makes and brands of oil separators for this purpose to choose from - including some pretty bling machined aluminum units.
However, I chose this cheap and simple unit from JEGS, primarily because it is transparent, and therefore the oil level in the bowl can easily be monitored.
Specs of the unit include:
- Maximum pressure 150 psi
- Clear polycarbonate bowl for easy viewing and durability
- Serviceable 5 micron element
- Twist/turn drain
- Mounting bracket included
- Two 1/4" NPT x 3/8" hose barb fittings included
- Easily cleaned with dish soap, a thorough rinse, and air dry only.
- Measures 4-1/2" tall x 1-3/4" diameter
|
If it looks a lot like a small version of the air filter on your shop compressor, that's because it is. It is essentially exactly the same thing (technically known as a coalescing filter).
Update: Reader Steve recently alerted me to these other two possibilities. I have no expeience in using either, but they may be worth checking out.
The Conceptual Polymer Oil Entrapment System
The MANN-HUMMEL Provent. |
 |
Here is the unit installed on the front of the passenger side head. |
Conclusion
The topics of engine oil, oiling, tribology, and rheology are indeed vast and complicated. If I have piqued your interest or curiosity, perhaps even given you a basic understanding of the topic as a place from which to begin further study, then I have achieved what I set out to do.
To get you started, here are a few other interesting articles or links (but remember, not every word will be true, nor does any one "expert" truly know everything, including (especially!) me.
References:
SAE PUBLICATIONS
Available from SAE, 400 Commonwealth Drive, Warrendale, PA 15096-0001.
SAE J183 —Engine Oil Performance and Engine Service Classification (Other than “Energy Conserving”)
SAE J300 —Engine Oil Viscosity Classification
SAE J304 —Engine Oil Tests
SAE J306 —Automotive Gear Lubricant Viscosity Classification
SAE J1423—Classification of Energy-Conserving Engine Oil for Passenger Cars, Vans, and Light Duty
Trucks
SAE J2227—International Tests and Specifications for Automotive Engine Oils
ASTM PUBLICATIONS
Available from ASTM, 100 Barr Harbor Drive, West Conshohocken, PA 19428-2959.
ASTM Data Series DS 62—The Relationship Between High-Temperature Oil Rheology and Engine
Operation—A Status Report
ASTM STP 1068—High-Temperature, High-Shear Oil Viscosity—Measurement and Relationship to
Engine Operation
ASTM STP 1143—Low-Temperature Lubricant Rheology: Measurement and Relevance to Engine
Operation
ASTM Research Report RR-D02-1442—Cold Starting and Pumpability Studies in Modern Engines
ASTMDS 39b—Viscosity Index Tables for Celsius Temperatures
ASTM D 56—Test Method for Flash Point by Tag Closed Tester
ASTM D 91—Test Method for Precipitation Number of Lubricating Oils
ASTM D 92—Test Method for Flash and Fire Points by Cleveland Open Cup
ASTM D 93—Test Methods for Flash Point by Pensky-Martens Closed Cup Tester
ASTM D 95—Test Method for Water in Petroleum Products and Bituminous Materials by Distillation
ASTM D 97—Test Methods for Pour Point of Petroleum Oils
ASTM D 156—Test Method for Saybolt Color of Petroleum Products (Saybolt Chromometer Method)
ASTM D 189—Test Method for Conradson Carbon Residue of Petroleum Products
ASTM D 287—Test Method for API Gravity of Crude Petroleum and Petroleum Products (Hydrometer
Method)
ASTM D 322—Test Method for Gasoline Diluent in Used Gasoline Engine Oils by Distillation
ASTM D 341—Viscosity-Temperature Charts for Liquid Petroleum Products
ASTM D 445—Test Method for Kinematic Viscosity of Transparent and Opaque Liquids (the Calculation
of Dynamic Viscosity)
ASTM D 482—Test Method for Ash from Petroleum Products
ASTMD 524—Test Method for Ramsbottom Carbon Residue of Petroleum Products
ASTM D 664—Test Method for Acid Number of Petroleum Products by Potentiometric Titration
ASTM D 874—Test Method for Sulfated Ash from Lubricating Oils and Additives
ASTM D 892—Test Method for Foaming Characteristics of Lubricating Oils
ASTM D 893—Test Method for Insolubles in Used Lubricating Oils
ASTM D 974—Test Method for Acid and Base Number by Color Indicator Titration
ASTM D 1160—Test Method for Distillation of Petroleum Products at Reduced Pressure
ASTM D 1298—Standard Practice for Density, Relative Density (Specific Gravity) or API Gravity of
Crude Petroleum and Liquid Petroleum Products by Hydrometer Method
ASTM D 1310—Test Method for Flash Point and Fire Points of Liquids by Tag Open Cup Apparatus
ASTM D 1500—Test Method for ASTM Color of Petroleum Products (ASTM Color Scale)
ASTM D 2270—Standard Practice for Calculating Viscosity Index from Kinematic Viscosity at 40 and
100 °C
ASTM D 2500—Test Method for Cloud Point of Petroleum Oils
ASTM D 2887—Test Method for Boiling Range Distribution of Petroleum Fractions by Gas
Chromatography
ASTM D 2896—Test Method for Base Number of Petroleum Products by Potentiometric Perchloric Acid
Titration
ASTM D 2982—Test Method for Detecting Glycol-Base Antifreeze in Used Lubricating Oils
ASTM D 3244—Standard Practice for Utilization of Test Data to Determine Conformance with
Specifications
ASTM D 3524—Test Method for Diesel Fuel Diluent in Used Diesel Engine Oil by Gas Chromatography
ASTM D 3525—Test Method for Gasoline Diluent in Used Gasoline Engine Oils by Gas
Chromatography
ASTM D 3607—Test Method for Removing Volatile Contaminants from Used Engine Oils by Stripping
ASTM D 3828—Test Method for Flash Point by Small Scale Closed Tester
ASTM D 3829—Test Method for Predicting the Borderline Pumping Temperature of Engine Oil
ASTM D 3945—Standard Test Methods for Shear Stability of Polymer-Containing Fluids Using a Diesel
Injector Nozzle
ASTM D 4055—Test Method for Pentane Insolubles by Membrane Filtration
ASTM D 4485—Standard Specification for Performance of Engine Oils
ASTM D 4530—Test Method for Determination of Carbon Residue (Micro Method)
ASTM D 4628—Test Method for Analysis of Barium, Calcium, Magnesium, and Zinc in Unused
Lubricating Oils by Atomic Absorption Spectrometry
ASTM D 4683—Test Method for Measuring Viscosity at High Temperature and High Shear Rate by
Tapered Bearing Simulator
ASTM D 4684—Test Method for Determination of Yield Stress and Apparent Viscosity of Engine Oils at
Low Temperature
ASTM D 4739—Test Method for Base Number Determination by Potentiometric Titration
ASTM D 4741—Test Method for Measurement of Viscosity at High Temperature and High Shear Rate
by Tapered Plug Viscometer
ASTM D 4927—Test Methods for Elemental Analysis of Lubricant and Additive Components—Barium,
Calcium, Phosphorus, Sulfur, and Zinc by Wavelength-Dispersive X-Ray Fluorescence
Spectroscopy
ASTM D 4951—Test Method for Determination of Additive Elements in Lubricating Oils by Inductively
Coupled Plasma Atomic Emission Spectrometry
ASTM D 5002—Standard Test Method for Density and Relative Density of Crude Oil by Digital Density
Analyzer
ASTM D 5119—Test Method for Evaluation of Automotive Engine Oils in the CRC L-38 Spark Ignition
Engine
ASTM D 5133—Standard Test Method for Low Temperature, Low Shear Rate, Viscosity/Temperature
Dependence of Lubricating Oils Using a Temperature-Scanning Technique
ASTM D 5185—Standard Test Method for Determination of Additive Elements, Wear Metals, and
Contaminants in Used Lubricating Oils and Determination of Selected Elements in Base
Oil by Inductively Coupled Plasma Atomic Emission Spectrometry (ICP-AES)
ASTM D 5293—Standard Test Method for Apparent Viscosity of Engine Oils Between -5 °C and -30 °C
Using the Cold Cranking Simulator
ASTM D 5481—Standard Test Method for Measuring Apparent Viscosity at High-Temperature and High-
Shear Rate by Multicell Capillary Viscometer
ASTM Special Technical Publication 315I, Part I— Multicylinder Test Sequences for Evaluating
Automotive Engine Oils
ASTM E 1131—Test Method for Compositional Analysis by Thermogravimetry
ASTMMNL 1—Manual on the Significance of Tests for Petroleum Products: 5th Edition
ASTMSTP 1068—High Temperature/High Shear (HTHS) Oil Viscosity: Measurement and Relation to
Engine Operation
ASTMSTP 1143—Low Temperature Lubricant Rheology Measurement Relevance to Engine
Operations
ASTM D 2983—Standard Test Method for Low-Temperature Viscosity of Automotive Fluid Lubricants
Measured by Brookfield Viscometer
ASTM D 5302— Standard Test Method for Evaluation of Automotive Engine Oils for Inhibition of Deposit
Formation and Wear in a Spark-Ignition Internal Combustion Engine Fueled with Gasoline and Operated
Under Low-Temperature, Light-Duty Conditions— Sequence VE Procedure
ASTM D 5533— Standard Test Method for Evaluation of Automotive Engine Oils in the Sequence IIIE,
Spark-Ignition Engine
ASTM D 6202— Standard Test Method for Measurement of the Effects of Automotive Engine Oils on the
Fuel Economy of Passenger Cars and Light Duty Trucks in the Sequence VIA Spark Ignition Engine
CEC PUBLICATIONS
Available from Coordinating European Council, Madou Plaza, 25th Floor, Place Madou 1, B-1030
Brussels, Belgium.
CEC Test Method CEC L-45-A-99—Viscosity Shear Stability of Transmission Lubricants (KRL – Tapered
Roller Bearing Test Rig) Shear Stability Test, 1999
CEC L-36-A-90—The Measurement of Lubricant Dynamic Viscosity Under Conditions of High Shear
Using the Ravenfield Viscometer
CRC Report No. 409—Evaluation of Laboratory Viscometers for Predicting Cranking Characteristics of
Engine Oils at 0 °F and –20 °F, April 1968
CEC L-40-A-93, “Evaporative Loss,” NOACK (DIN 51581) Method
CEC L-14-A-93 “Evaluation of the Mechanical Shear Stability of Lubricating Oils Containing Polymers”
Method
API PUBLICATIONS
Available from American Petroleum Institute, 1220 L Street NW, Washington, DC 20005.
API 1509— Engine Oil Licensing and Certification System
MILITARY SPECIFICATIONS AND COMMERCIAL ITEM DESCRIPTIONS
Available from Standardization Documents
Order Desk, Building 4D, 700 Robbins Avenue, Philadelphia, PA 19111-5094.
MIL-PRF-2104G— Lubricating Oil— Internal Combustion Engine— Tactical Service
MIL-L-6082E— Lubricating Oil— Aircraft Reciprocating Engine
MIL-PRF-21260E— Lubricating Oil— Internal Combustion Engine— Preservative and Break-in
MIL-L-22851D— Lubricating Oil— Aircraft Piston Engine (Ashless Dispersant)
MIL-PRF-46167C— Lubricating Oil— Internal Combustion Engine— Arctic Service
CID A-A-52039B— Lubricating Oil— Automotive Engine— API Service SH
CID A-A-52306A— Lubricating Oil— Heavy-Duty Diesel Engine
OTHER PUBLICATIONS
Federal Test Method Standard No. 791C, Method 203.1, “Pour Stability of Lubricating Oils”
Federal Test Method Standard No. 791C, Method 3470.1, “Homogeneity and Miscibility of Oils”
American Society of Lubrication Engineers, 1951, “The Physical Properties of Lubricants”
General Motors Engineering Standard GM 9099P, “Engine Oil Filterability Test (EOFT),” May 1980
C.M. Georgi, “Motor Oils and Engine Lubrication,” New York: Reinhold Publishing Corporation, 1950
William A. Gruse, “Motor Oils, Performance and Evaluation,” New York: Reinhold Publishing
Corporation, 1967
A. Schilling, “Automotive Engine Lubrication,” Broseley, England: Scientific Publications (G.B.) Ltd.,
1972
R.C. Gunderson and A.W. Hart, “Synthetic Lubricants,” New York: Reinhold Publishing Corporation,
1962
Dieter Klamann, “Lubricants and Related Products,” Weinheim: Verlag Chemie (F.R.G.) GmbH, 1984
M. Campen, D. Kendrick, and A. Markin, “Growing Use of Synlubes,” Hydrocarbon Processing, February
1982
G.J. Schilling and G.S. Bright, “Fuel and Lubricant Additives—II. Lubricant Additives,” Lubrication Vol 63,
No. 2, 1977
N. Benfaremo and C.S. Liu, “Crankcase Engine Oil Additives,” Lubrication Vol 76, No. 1, 1990 |
|
|