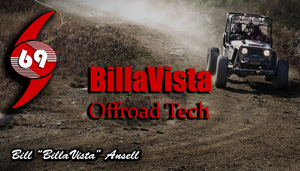 |
Chopsaw Notching & Link Construction
By Bill "BillaVista" Ansell
Photography: Bill Ansell
Chopsaw Notch Angle Calculations: Marc "Tigweld" Googer
Copyright 2006 - Bill Ansell
(click any pic to enlarge)
|
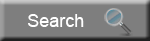 |
Introduction
In the last five years, linked suspensions have exploded in popularity, and
for good reason - they offer not only the best performance, but also the most
flexibility. By custom designing a multi-link suspension you have the most control
over how the suspension performs and also how you route nearby components such
as brakes, steering, and exhaust. However, due to their placement and the rock
smashing abuse they are often subjected to, they can be quite vulnerable. Combine
this with the critical job they have of controlling and positioning the axles,
especially in high torque rigs, and there are few things more frustrating than
bent and mangled links or destroyed bushings and joints on the trail.
Many have experienced this frustration,
and many have subsequently asked – what should I make my links from? This
article will attempt to provide some insight into the answer. |
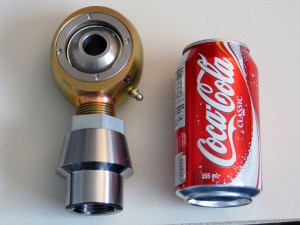 |
There are essentially five steps
to constructing suspension links that will fit your needs and hold up the way
you hope. They are
- Understanding and reconciling design
factors
- Selecting the material for the link
- Selecting a joint for the end of the links
- Deciding on specific design features, such as offset and clearance bends
- Notching the tube and joining the links to the joints.
At this point you might wonder if
I’m not overdoing it just a bit. Could I not just say “Get some
2” x 3/8” DOM tube and weld on your favourite ends” and be
done with it? Well, yes and no. Yes, that might work for some, but I know from
experience it isn’t the best solution for many – depending on their
needs. More importantly, many of the things I’ll discuss here can be applied
equally to the design, selection or fabrication of any part – whether
it be a simple suspension link or a full chassis – balancing cost, weight,
looks, etc will always be required.
Design Factors
Before we get to the specifics of
link construction, it’s important that we recognize some of the factors
that must be considered when designing any part. We need to know what these
factors are because all design is a compromise - a careful balancing act. It’s
impossible to have the best of everything – strongest, lightest, easiest,
and cheapest simply don’t go together. I’m reminds me of a sign
that hangs over the counter in a local machine shop: “We do three kinds
of work here – good, fast, and cheap – you can pick any two!”
The maxim is true of any custom work we do ourselves. When setting out to design
or fabricate any part we must have a good understanding of the relative importance
we personally attach to each of the following factors. There are no right answers
(although probably several wrong ones) and everybody’s needs will differ,
but in order to avoid disappointment and frustration we should consider:
- Cost. The most obvious factor,
but also one that can sneak up in unexpected ways. Obviously you want the
most strength and reliability you can afford, but you have to be practical
too. Titanium is wonderfully strong and light, but horrendously expensive,
and a bear to machine and weld properly. You also need to be aware of possible
future costs. Sure, maybe with all the overtime this month I could afford
chrom-moly links, and my buddy has the gear and know-how to weld them properly
– but will I be able to afford to replace a broken part in the future,
and will I still have access to the required TIG welding?
- Size. Strength almost always
goes up with size – sure, you could use a 6” OD tube, and it would
probably never bend, but how would you ever fit it? You have to take into
consideration the practical limits of the size you can use.
- Weight. May or may not be terribly
important to you. For competitors, weight is always a major factor, for others
it may not be. Be aware though, that weight, and its placement, will affect
the performance characteristics of all rigs. It can also add up a lot faster
than you might think. Remember that weight is always a trade off versus strength.
- Ease of manufacture. By this
I mean cutting, welding, bending, joining etc. This factor is strongly connected
with size. It’s probably no good buying ½” wall chrom-moly
tube if your design calls for you to bend it in your manual tube bender. Likewise,
even if you could source Titanium reasonably, it’s no good if you can’t
cut or weld it. Consider carefully whether you have the tools, time and technical
ability to turn your dream design into reality.
- Ease of repair / replacement.
Is the material you choose likely to be available in the future if you need
it or is it some one-off, unidentifiable tube you found discarded behind the
plant? If you’re using commercially produced joints for your links (as
most will) – will they be available in the future? Can the be rebuilt
and are parts available separately? Don’t forget that, no matter how
strong, anything’s breakable – will you be able to repair your
design in the field if required?
- Aesthetics. How it looks is important.
The amount of time, money, and sacrifice that goes into a rig is enormous
– I know. You need to be able to walk past it at any time and think
“Damn, I love my rig.” No matter how great a deal you got or how
strong it is, you’ll eventually hate yourself if every time you look
at your rig you think “I know my Frankenstein, re-bar reinforced, I-beam
links are strong – but damn they look booty-fab!”
- Shape & Design. I will argue
that, pound for pound, straight, round mechanical tubing is likely the best
choice for most of us. It’s readily available in a wide variety of diameters
and thicknesses to suit any need, is easily cut, notched, and welded with
tools most of us already have or can easily justify acquiring (because tube
is so prevalent and flexible on a custom rig, we will always have a need/use
for tube-working tools), looks good, takes up little space, is smooth for
sliding off and over rocks, and there are any number of adjustable or non-adjustable
suspension joints available specifically for round tubing. That’s not
to say that you cannot make perfectly good links from square or rectangular
tubing – you can. However, I shall stick to round tubing for this article.
I am also a believer in straight links. First, they are the simplest to design
and fabricate. Second, any link bent for clearance or other design purposes
will always require some sort of bracing to maintain its original strength
– and very often this takes up most of the previously gained clearance.
The result is very little clearance gained but additional weight and complexity
added. Cleverly bent shapes have their place – but for most of us they
are needlessly complicated to make or reproduce. Bend an already carefully
bent shape in the field, and it can be almost impossible to get it back into
shape - whereas a straight link can be pounded and levered back into something
resembling straight much more easily.
Of course, the most important design
factor to consider is the goal – what we are trying to build and what
do we want it to do? Suspension links will be loaded in a variety of ways –
in compression and tension as they counteract the driveline torque, in torsion
as they locate the axle during articulation, and in bending as they contact
rocks and obstacles. It is this last case where the link’s strength is
most critical. Rarely will a link fail in torsion or tension, but often we see
links that are bent from the abuse of hard driving over rough terrain. So what
we ultimately want is a link that will resist bending as much as possible. The
following list outlines the six things we have to decide in constructing our
links, and is followed by some technical proof of the factors.
The six things to consider are:
- Length. The length of the links
will be pre-determined by axle placement and suspension design. We must, however,
keep in mind that the longer the link is, the more susceptible to bending
it will be. The longer the link is, the more of a “lever” there
will be to bend the link when there is contact between the link and an object
somewhere along the link’s length. Being aware of this, we can compensate
for very long lengths by compromising in other areas (e.g. cost and weight)
and using a larger or thicker tube than might otherwise be required for a
shorter link.
- Size (outside diameter). The
OD of the tube is the single biggest factor determining its strength. No other
factor will have as great an effect on our link’s ability to resist
bending. If you want the strongest links possible, the bottom line for tube
size is pretty much "as big as you can fit”.
- Wall thickness. The thickness
of the tube has the second largest effect on the links resistance to bending.
However, since the biggest factor, OD, will likely be predetermined by the
available space for the links, the thickness will likely be the factor we
have to most carefully consider.
- Material. The material from which
we choose to make our links follows closely behind thickness in terms of determining
the strength of our links. Steel is the obvious choice for it’s combination
of strength, stiffness, rigidity, elasticity, weight, ease of fabrication,
and cost. There are four common types of steel to choose from: ASTM A-53 (or
similar) pipe, electric resistance welded (ERW) tube, drawn over mandrel (DOM)
tube, and chrom-moly DOM tube. The choice of material has a significant effect
on the properties of the link – especially when you consider that yield
strengths range from 30,000 psi for ASTM A-53 pipe to 90,000 psi for cr-mo
tube. However, this difference is not as pronounced as you may think, and
changing materials often doesn’t have nearly the same effect as changing
the OD or thickness of the tube. For example, increasing a 1020 DOM tube link
from 2” OD to 2.5” OD will have a much greater effect than staying
at 2” OD and just changing to 4340 chrom-moly.
- End termination (type of joint)
– The overall strength of the links, as well as its resistance to binding
during articulation depends a great deal on the type of joints used at the
ends. Fortunately there are many good choices available on the market today
– gone are the days when I made my first adjustable links with little
choice but to cannibalize old tractor top-links. Along with strength and deflection
capability there are many other factors to consider in joint selection, including
price, durability, availability, adjustability, and whether they can be greased
and/or rebuilt.
- Our tolerance of part failure
– The most personal and difficult to quantify of all factors, it is
arguably the most important to consider in the design stage. Some folks enjoy
the build-break-re-build cycle while others dislike/despise the results of
broken parts, including loss of time, frustration, lost competitive opportunities,
and ruined wheeling trips. Whether you are happily R&Ding the most cutting
edge, finely tuned solution you can or are replacing a bent link for the 3rd
time (and just wanting the damn thing to last) will have a big effect on your
decisions.
Fortunately for us, we don’t
have to make detailed engineering calculations in order to design a material
and have it produced for us. There are already a wealth of good choices readily
available, along with a great deal of first-hand information from folks who
have used different products. With a suppliers catalogue, this article, and
a little bit of head scratching you should be able to come up with the ideal
combination for your project. Table 2 shows the dimensions and specs of commonly
available round mechanical tubing in a range of sizes most likely to be appropriate
for suspension link construction. Note particularly the weight per foot column.
Also be advised that, though prices aren’t shown, they tend to increase
exponentially as the size and weight of the tube does.
Choosing
Size, Wall Thickness, and Material |
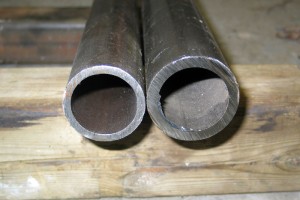 |
|
In order to make an informed decision
about what tube we want to use to construct our links, it is helpful to explore
in a little more detail the effect of tube OD and wall thickness on the relative
strength of different types of tube. In order to do this we must consider two
separate but related concepts – how much stress a tube will endure for
a given load, and what the tube’s reaction to that stress will be. The
stress is related to the cross section (shape) and size of the link. The reaction
is related to the material the link is made from.
In order to make a useful but simple
comparison it is necessary to apply some formulae to a very simplified model.
The following calculations are not intended to represent actual engineering
calculations in any way, but are sufficient to illustrate general concepts for
comparative purposes. The model contains the following simplifications and assumptions:
• Assume our suspension link
is made from tube
• Assume the tube is a round, hollow, and with uniform cross section,
consistent OD, and consistent wall thickness
• Assume that when installed the tube forms a beam supported equally at
both ends
• Assume a constant load applied at the mid-point of the tube’s
length
• Assume a tube length of 48”, and an applied load of 5000 lbs
The model doesn’t take into
account multiple loads, dynamic loads, shock loads, tapering cross sections
(as in the case of threaded adjustable links), or loads applied at locations
other than the center.
The formula for calculating the maximum
stress in a beam supported at both ends, with load applied at the centre is:
S= (W x L) / 4(Z)
where:
S = stress (psi)
W = the load (force) placed on the beam (lbs);
L = the length from where the tube is supported to where the load is applied
(in);
Z = Section modulus of the cross-section of the beam
The section modulus of a round, hollow
tube is calculated as:
Z = I / Y
where:
Z = Section modulus
I = Moment of Inertia
Y = the distance from the neutral axis (longitudinal center of the tube) to
the extreme outside fibre – in other words, the radius of the tube.
The Moment of Inertia (I) is given
by the formula:
I = 0.049(D^4 - d^4)
where:
I = Moment of Inertia
D = outside diameter of tube
d = inside diameter of the tube
Because the formula for (I) takes
into account both OD and ID of the tube, it is the same thing as taking into
account the OD and wall thickness, the two specs we use for purchasing –
i.e. the inside diameter is equal to the OD minus two times the wall thickness.
A tube’s moment of inertia
really describes how easily something bends by quantifying how much material
there is and how far from neutral axis (the line about which the bending occurs)
it is located. Common experience confirms the truth of the equation. You could
quite easily take a 3 foot long ¼ “ solid bar and bend it by hand.
However, if you were to place the ¼” of steel much further from
the neutral axis by having a 4” pipe with 1/8” thick walls, it would
be impossible to bend by hand.
So, with the OD and wall thickness
we can calculate the moment of inertia and section modulus for any tube. Calculated
values for common tube have been included in Table 2. If we then take our model
with and assume a 48” link and a theoretical load of 5000 lbs, we can
calculate the maximum stress at the center of the tube under that load. Table
2 also includes these calculations. By comparing the results of these stress
calculations we can get a good idea of the relative strength (in terms of resistance
to bending) of different sized tubes. To make the comparison even more clear,
I chose, (completely arbitrarily) to assign a value of 1 to the stress (calculated
using our model) in a 1.75” x ¼” wall tube. I then calculated
the percentage difference between the stress in any other tube compared to this
base value. The results appear in the last column of Table 2, with a (-) indicating
that the tube is x% “weaker” than 1.75 x 0.25 tube, and a positive
number indicating that that tube is x% stronger. To compare two tubes directly,
take the higher stress value from the table, subtract the lower, divide the
result by the higher and multiply by 100.
For example, if I am trying to decide
whether to use 2” x 3/8” wall tube or take the hit on cost and weight
and use 2” x ½” wall tube, I can calculate the rough strength
difference as follows:
From Table 2:
2" x 3/8" - stress = 3763
2" x 1/2" - stress = 3401
(3763-3401)/3763 = 0.096 = 9.6%.
(1/2" wall tube is ~ 10% stronger)
Therefore, at 8.0 lbs / ft, the
½” wall tube is 19% heavier than the 3/8” wall tube (6.5
lbs / ft) but only approximately 10% stronger.
Material
Now, you might reasonably ask, how
do you account for the different material different tubes are made from? Recall
that the second factor we must consider in our link’s strength is its
reaction to stress. That is, when choosing a tube based on OD and wall thickness,
you can see that the stronger the tube, the less stress it experiences for a
given load – but what does this translate to in the real world?
How does stress relate to bending? It turns out that there is an equation that
can be used to calculate how much a tube will bend or deflect under load. It
is:
f =[ (W)(L^3) ] / [48(E)(I)]
Where:
F = maximum deflection at load
W = the load (force) placed on the beam (lbs);
L = the length from where the tube is supported to where the load is applied
(in)
I = Moment of Inertia
E = Modulus of elasticity of the material.
The modulus of elasticity is a measure
of stiffness, and is a constant value for all steels (approximately 30,000,000
psi). This equation illustrates that how much the tube will bend under load
is still only related to the OD and wall thickness, not the material, since
the equation includes (I) and (E) but no variable that accounts for differences
in material. What this means is, all steels are comparably stiff, they will
all resist bending about the same amount - from cheap pipe to expensive cr-mo
tubing. The difference between them is what happens when they bend. The better,
more expensive steels, due to their much higher yield points and greater elastic
ranges (Table 2), will be able to easily shrug off the load, returning to shape.
The lesser materials may yield (take a permanent set, or bend) or actually rupture.
The key to the difference between
different steels is the relationship between the stress and the yield strength
of the material. When stress is greater than yield strength, the link will yield
or permanently change shape, if stress is less than yield strength, the link
will simply return to shape after the load is removed. Table 2 shows a list
of common materials used in link and other 4x4 related construction. Note the
very different yield strengths of the different steels.
Don’t be tempted to directly
compare the stress numbers in Table 2 to the Yield Strengths in Table 1, because
the numbers in Table 2 are purely arbitrary, for purposes of comparison only,
and not representative of any real-world scenario. For example, don’t
be tempted to look at Table 2 and note that the stress example for a 5000 lb
load is only about 15,000 psi, and then look at Table 1 and calculate that this
15,000 psi is only half the yield strength of pipe and conclude that 1-1/2”
x 1/8” pipe will be strong enough, as this would be a mistake. Actual
calculations of real-world dynamic loads are for more complicated than I have
shown here, and it is likely that in service your links will see stresses tens,
possibly hundreds of times greater than those shown in Table 2. The equations
and values shown here are simply for the purpose of understanding and illustrating
the concepts discussed; they are not to be used for calculations, and do not
include critical elements such as design factor, impact loads, safety margins,
and fatigue factors!
When observing Tables 1 and 2 together
the bottom line becomes apparent:
- The larger the OD and the
thicker the wall of the tubing you choose, the less stressed the tube will be
for any given load.
- The higher the grade of steel you use, the less likely any given stress will
be to exceed the tube’s yield strength and cause a permanent bend or break. |
Material |
Yield Strength, PSI* |
ASTM Grade A-53 pipe |
30, 000 |
1020 ERW tube |
40, 000 |
1020 DOM |
70, 000 |
4130 Cr-Mo |
90,000 |
4340 Cr-Mo |
120,000 |
|
Table
1- Average Yield Strengths for Different Materials |
* Average representative values only
– actually values vary greatly and depend on the condition of the product.
For example, 4340 chrom-moly steel can have a yield strength ranging from 68,000
PSI (annealed at 1490°F) to 243,000 PSI (quenched and tempered at 400° F). Consult
exact product specification from product supplier for accurate figures.
In my opinion, the best over-all
choice for link construction is DOM tubing in the 1020-1026 range. Pipe is too
weak and soft for hard duty in a critical application like this. Hot-rolled
ERW (HREW) tubing varies in dimension too much and is supplied with a rough,
scale-covered finish, making it unpleasant to work with and requiring clean-up
before welding. Cold rolled ERW (CREW) is stronger, cleaner, and has better
dimensional tolerance than HREW, but is uncommon and therefore difficult to
source. Also, it is not appreciably cheaper than DOM tubing, leaving no real
advantage to using it as opposed to DOM tubing. At the other end of the scale,
while 4340 Cr-Mo tubing is extremely strong, I believe the required strength
can easily be accomplished for far less cost by appropriate size and thickness
selection in a mild steel DOM. Chrom-moly also has very strict welding, post-welding
heat treatment, and stress-relieving requirements. It is my opinion that it
should only be TIG or Oxy-Acetylene welded, and then only if proper stress relieving
will be done post welding. Sure, people MIG weld it all the time, and you can
safely do so - BUT - what you have in the end is a superior tube with an inferior
weld joint which reduces the overall strength of whatever you fabricated to
the weakest point (the weld in this case) and so you have a very expensive structure
that is no better overall than one made from 1020 DOM. When I recently redid
my own 3-link front and 4-link rear I used a combination of 2” x 3/8”,
2-1/4” x ¼” and 2” x 3/16” 1026 DOM tubing. In
Table 2 the values for these three tubes are highlighted in yellow for easy
comparison to our arbitrary "standard" 1-3/4" x 1/4" tube
which is highlighted
Impact
Resistance
One last consideration that relates
primarily to material type and wall thickness is the property of impact resistance.
By this I mean the link’s ability to resist small localized denting, scrapes,
and nicks. Very difficult to quantify for direct numerical comparison, nonetheless
we can state that the thicker the wall and the higher the quality of the steel
the “tougher” the tube will be and the better it will be able to
resist damage.
Table 2 gives the dimensions and
approximate weight for a wide variety of tubes that are available in ERW, DOM,
and Cr-Mo, one of which should meet your needs. Check with your supplier for
availability of a particular size and type.
Table 2 - Tube Properties
OD |
OD Decimal |
Wall |
Wall decimal |
ID |
Lbs / Ft |
Moment
of Inertia (I) |
Section
Modulus (Z) |
Stress(psi)* |
% change** |
1 1/2" |
1.500 |
1/8 |
0.125 |
1.250 |
1.836 |
0.1284 |
0.1712 |
14599 |
-56% |
1 1/2" |
1.500 |
3/16 |
0.188 |
1.125 |
2.634 |
0.1696 |
0.2261 |
11057 |
-42% |
1 1/2" |
1.500 |
1/4 |
0.250 |
1.000 |
3.338 |
0.1991 |
0.2654 |
9419 |
-32% |
1 1/2" |
1.500 |
5/16 |
0.312 |
0.875 |
3.968 |
0.2193 |
0.2925 |
8548 |
-25% |
1 1/2" |
1.500 |
3/8 |
0.375 |
0.750 |
4.506 |
0.2326 |
0.3101 |
8062 |
-20% |
1 1/2" |
1.500 |
7/16 |
0.437 |
0.625 |
4.960 |
0.2406 |
0.3208 |
7793 |
-17% |
1 1/2" |
1.500 |
1/2 |
0.500 |
0.500 |
5.340 |
0.2450 |
0.3267 |
7653 |
-16% |
1 5/8" |
1.625 |
1/8 |
0.125 |
1.375 |
2.003 |
0.1665 |
0.2050 |
12198 |
-47% |
1 5/8" |
1.625 |
3/16 |
0.188 |
1.250 |
2.885 |
0.2220 |
0.2733 |
9148 |
-30% |
1 5/8" |
1.625 |
1/4 |
0.250 |
1.125 |
3.671 |
0.2632 |
0.3239 |
7718 |
-17% |
1 5/8" |
1.625 |
5/16 |
0.312 |
1.000 |
4.386 |
0.2927 |
0.3602 |
6940 |
-7% |
1 5/8" |
1.625 |
3/8 |
0.375 |
0.875 |
5.006 |
0.3129 |
0.3852 |
6491 |
-1% |
1 5/8" |
1.625 |
7/16 |
0.437 |
0.750 |
5.553 |
0.3262 |
0.4014 |
6228 |
3% |
1 5/8" |
1.625 |
1/2 |
0.500 |
0.625 |
6.008 |
0.3342 |
0.4113 |
6078 |
6% |
1 3/4" |
1.750 |
1/8 |
0.125 |
1.500 |
2.169 |
0.2115 |
0.2417 |
10343 |
-38% |
1 3/4" |
1.750 |
3/16 |
0.188 |
1.375 |
3.136 |
0.2844 |
0.3250 |
7691 |
-16% |
1 3/4" |
1.750 |
1/4 |
0.250 |
1.250 |
4.005 |
0.3399 |
0.3885 |
6435 |
0% |
1 3/4" |
1.750 |
5/16 |
0.312 |
1.125 |
4.804 |
0.3811 |
0.4355 |
5740 |
12% |
1 3/4" |
1.750 |
3/8 |
0.375 |
1.000 |
5.507 |
0.4106 |
0.4692 |
5328 |
21% |
1 3/4" |
1.750 |
7/16 |
0.437 |
0.875 |
6.137 |
0.4308 |
0.4924 |
5077 |
27% |
1 3/4" |
1.750 |
1/2 |
0.500 |
0.750 |
6.675 |
0.4441 |
0.5075 |
4926 |
31% |
1 7/8" |
1.875 |
1/8 |
0.125 |
1.625 |
2.336 |
0.2639 |
0.2815 |
8880 |
-28% |
1 7/8" |
1.875 |
3/16 |
0.188 |
1.500 |
3.387 |
0.3576 |
0.3814 |
6555 |
-2% |
1 7/8" |
1.875 |
1/4 |
0.250 |
1.375 |
4.339 |
0.4305 |
0.4592 |
5445 |
18% |
1 7/8" |
1.875 |
5/16 |
0.312 |
1.250 |
5.222 |
0.4860 |
0.5184 |
4823 |
33% |
1 7/8" |
1.875 |
3/8 |
0.375 |
1.125 |
6.008 |
0.5271 |
0.5623 |
4446 |
45% |
1 7/8" |
1.875 |
7/16 |
0.437 |
1.000 |
6.722 |
0.5566 |
0.5937 |
4211 |
53% |
1 7/8" |
1.875 |
1/2 |
0.500 |
0.875 |
7.340 |
0.5769 |
0.6154 |
4063 |
58% |
2" |
2.000 |
1/8 |
0.125 |
1.750 |
2.503 |
0.3244 |
0.3244 |
7706 |
-16% |
2" |
2.000 |
3/16 |
0.188 |
1.625 |
3.638 |
0.4423 |
0.4423 |
5652 |
14% |
2" |
2.000 |
1/4 |
0.250 |
1.500 |
4.673 |
0.5359 |
0.5359 |
4665 |
38% |
2" |
2.000 |
5/16 |
0.312 |
1.375 |
5.639 |
0.6089 |
0.6089 |
4106 |
57% |
2" |
2.000 |
3/8 |
0.375 |
1.250 |
6.508 |
0.6644 |
0.6644 |
3763 |
71% |
2" |
2.000 |
7/16 |
0.437 |
1.125 |
7.307 |
0.7055 |
0.7055 |
3544 |
82% |
2" |
2.000 |
1/2 |
0.500 |
1.000 |
8.010 |
0.7350 |
0.7350 |
3401 |
89% |
2 1/4" |
2.250 |
1/8 |
0.125 |
2.000 |
2.837 |
0.4718 |
0.4194 |
5961 |
8% |
2 1/4" |
2.250 |
3/16 |
0.188 |
1.875 |
4.140 |
0.6502 |
0.5780 |
4326 |
49% |
2 1/4" |
2.250 |
1/4 |
0.250 |
1.750 |
5.340 |
0.7963 |
0.7078 |
3532 |
82% |
2 1/4" |
2.250 |
5/16 |
0.312 |
1.625 |
6.475 |
0.9141 |
0.8126 |
3077 |
109% |
2 1/4" |
2.250 |
3/8 |
0.375 |
1.500 |
7.509 |
1.0078 |
0.8958 |
2791 |
131% |
2 1/4" |
2.250 |
7/16 |
0.437 |
1.375 |
8.476 |
1.0807 |
0.9606 |
2603 |
147% |
2 1/4" |
2.250 |
1/2 |
0.500 |
1.250 |
9.345 |
1.1362 |
1.0099 |
2475 |
160% |
2 3/8" |
2.375 |
1/8 |
0.125 |
2.125 |
3.004 |
0.5599 |
0.4715 |
5303 |
21% |
2 3/8" |
2.375 |
3/16 |
0.188 |
2.000 |
4.391 |
0.7750 |
0.6526 |
3831 |
68% |
2 3/8" |
2.375 |
1/4 |
0.250 |
1.875 |
5.674 |
0.9534 |
0.8029 |
3114 |
107% |
2 3/8" |
2.375 |
5/16 |
0.312 |
1.750 |
6.893 |
1.0994 |
0.9259 |
2700 |
138% |
2 3/8" |
2.375 |
3/8 |
0.375 |
1.625 |
8.010 |
1.2173 |
1.0251 |
2439 |
164% |
2 3/8" |
2.375 |
7/16 |
0.437 |
1.500 |
9.061 |
1.3110 |
1.1040 |
2265 |
184% |
2 3/8" |
2.375 |
1/2 |
0.500 |
1.375 |
10.010 |
1.3839 |
1.1654 |
2145 |
200% |
2 1/2" |
2.500 |
1/8 |
0.125 |
2.250 |
3.171 |
0.6582 |
0.5266 |
4747 |
36% |
2 1/2" |
2.500 |
3/16 |
0.188 |
2.125 |
4.642 |
0.9149 |
0.7319 |
3416 |
88% |
2 1/2" |
2.500 |
1/4 |
0.250 |
2.000 |
6.008 |
1.1301 |
0.9041 |
2765 |
133% |
2 1/2" |
2.500 |
5/16 |
0.312 |
1.875 |
7.311 |
1.3084 |
1.0468 |
2388 |
169% |
2 1/2" |
2.500 |
3/8 |
0.375 |
1.750 |
8.511 |
1.4545 |
1.1636 |
2149 |
200% |
2 1/2" |
2.500 |
7/16 |
0.437 |
1.625 |
9.637 |
1.5724 |
1.2579 |
1987 |
224% |
2 1/2" |
2.500 |
1/2 |
0.500 |
1.500 |
10.680 |
1.6660 |
1.3328 |
1876 |
243% |
2 5/8" |
2.625 |
1/8 |
0.125 |
2.375 |
3.338 |
0.7675 |
0.5848 |
4275 |
51% |
2 5/8" |
2.625 |
3/16 |
0.188 |
2.250 |
4.893 |
1.0707 |
0.8158 |
3064 |
110% |
2 5/8" |
2.625 |
1/4 |
0.250 |
2.125 |
6.341 |
1.3274 |
1.0114 |
2472 |
160% |
2 5/8" |
2.625 |
5/16 |
0.312 |
2.000 |
7.729 |
1.5426 |
1.1753 |
2127 |
203% |
2 5/8" |
2.625 |
3/8 |
0.375 |
1.875 |
9.011 |
1.7209 |
1.3112 |
1907 |
237% |
2 5/8" |
2.625 |
7/16 |
0.437 |
1.750 |
10.220 |
1.8670 |
1.4225 |
1758 |
266% |
2 5/8" |
2.625 |
1/2 |
0.500 |
1.625 |
11.350 |
1.9849 |
1.5123 |
1653 |
289% |
2 3/4" |
2.750 |
1/8 |
0.125 |
2.500 |
3.504 |
0.8883 |
0.6460 |
3870 |
66% |
2 3/4" |
2.750 |
3/16 |
0.188 |
2.375 |
5.144 |
1.2434 |
0.9043 |
2765 |
133% |
2 3/4" |
2.750 |
1/4 |
0.250 |
2.250 |
6.675 |
1.5466 |
1.1248 |
2223 |
190% |
2 3/4" |
2.750 |
5/16 |
0.312 |
2.125 |
8.147 |
1.8032 |
1.3114 |
1906 |
238% |
2 3/4" |
2.750 |
3/8 |
0.375 |
2.000 |
9.512 |
2.0184 |
1.4679 |
1703 |
278% |
2 3/4" |
2.750 |
7/16 |
0.437 |
1.875 |
10.820 |
2.1968 |
1.5976 |
1565 |
311% |
2 3/4" |
2.750 |
1/2 |
0.500 |
1.750 |
12.020 |
2.3428 |
1.7039 |
1467 |
339% |
* Calculated as the
stress developed in a 48” long beam, supported at both ends and evenly
loaded in the center.
** Percent difference between the stress in this tube and the stress in an arbitrary
standard tube of 1.75” x ¼”.
Joint Selection |
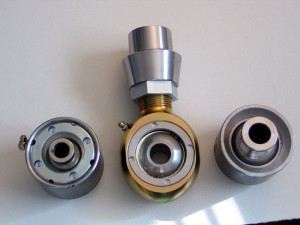 |
The selection of
the joint for the suspension link is at least as important as selection
of the tube. Having destroyed countless rubber and poly bushings I am a
firm believer in using some sort of cartridge-style joint or spherical rod
end (Heim joint). There are many good choices available on the market, all
with their advantages and disadvantages. |
In selection a joint, there are a
number of factors to consider:
- Cost – the cost of expensive
joints can add up quickly, especially since a standard 4-link front and rear
suspension uses 16 joints.
- Adjustability – if you
need adjustable-length links, you will have to choose a joint with a threaded
shank that offers this feature.
- Strength – you need to
match the strength of your tube to the strength of your joint. It is pointless
to attach a 2” x ½” Cr-Mo tube to a cheap ¾”
Heim joint.
- Size – As with all things,
as strength increases, generally so does size. Make sure your link / bracket
design and placement leave adequate room for the joints
- Rebuildability – Damage
and wear are almost a given – any good joint should offer the ability
to be rebuilt without having to fabricate a whole new link.
- Lubrication – The “sealed
vs greaseable” debate is timeless and boils down to personal choice.
Depending on the conditions of use and your preference, you may wish to use
joints that can be periodically lubricated. Some joints are “self lubricating”
meaning they use some sort of chemical-impregnated cup or liner that lubricates
the bearing but will eventually wear away – make sure these are rebuildable.
- Size of bolt hole – Something
you need to consider, especially before fabricating brackets, as many of the
largest and strongest joints use a very large bolt hole.
- Misalignment capacity –
Make sure the joint you use will work with your suspension design without
causing excessive binding that will limit suspension performance and cause
excessive wear and damage to components. Consider whether the joint offers
spacers to increase misalignment capacity.
|
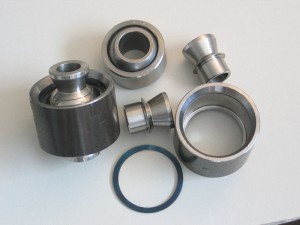 |
Poly Performance
Uniball |
|
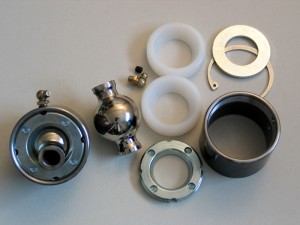 |
Large RE bearing |
|
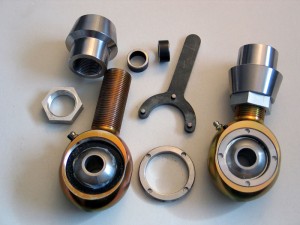 |
Evolution Heim Joint |
|
RE
(large) Bearing |
Poly
Performance |
Evolution |
Body
Material |
DOM |
DOM |
4140 |
Bearing
Material |
Chrome-plated steel |
Ball – 440C heat treated
stainless steel
Race - 17-4 PH heat treated stainless steel |
Stainless Steel |
Body
diameter (D) |
2-5/8” |
2-5/8” |
3.0” |
Body
Width (W) |
1.875” |
1.750” |
1.625” |
Bearing
width (B) |
2.625” |
1.375” |
1.750” |
Spacer
width (S) |
built in |
2 x 0.815” |
2 x 0.50” |
Total
mounted width (M) |
2.625” |
3.000” |
2.750” |
Bolt
hole (H) |
9/16” |
¾” |
¾” |
Shank
thread |
n/a |
n/a |
1.250 - 12 UNF |
Shank
length |
n/a |
n/a |
3.0” |
Tubing
Size |
Up to 2” OD |
Up to 2” OD |
1.750” ID |
Misalignment |
23° |
32° |
28° |
Approx.
Price |
$40 US |
$107 US |
$80 US (~$115 US with
spacers, tube insert, and jam nut.) |
Features |
UHMW bearing cups,
hardened, chrome-plated ball, adjustable preload, greasable, |
All metal, PTFE lined,
self-lubricating bearing, non-greasable, no preload adjustment, no special
tool required |
Stainless steel pre-load
ring with locking screw, grease nipple, composite bearing cups. Available
in left and right hand thread. Left & right hand jam nuts and tubing inserts
available. |
For a detailed article on joint selection
see my article "A
Joint for Any Occasion"
Link Design
Features
As previously mentioned, I am a fan
of the simple straight link. However, you may prefer to more highly customize
your links. Two common approaches are 1) offset mounting to the joint and 2)
links that are pre-bent or curved for clearance. If you decide to design links
with such features, there are a couple of "gotchas" to watch out for.
If you decide to gain extra clearance by joining the link more towards the top
of the joint than to the center, be aware that you will have to adjust the notch
in your tube accordingly and that you may further reduce the maximum size of
the tube you can use. Of course, if you use a threaded, adjustable joint this
will not be an option. I am not a fan of “bent links” because the
design either requires bracing which then eats up any previously gained clearance,
or leaves the link significantly weaker than if it were not bent. A curved link
shifts the neutral axis from the gravity axis (straight line between the ends
of the link) toward the center of curvature (the concave side of the link).
This shift in the position of the neutral axis causes an increase in the stress
on the concave side of the link - up to as much as 3.5 times the stress in a
straight link. What does this means in real-world terms? It means, depending
on how curved the link is, a bent-link design may require a massive 2-3/4 x
½” tube, weighing over 12 lbs/ft to equal the strength of a 1-3/4
x ¼” straight link that would weigh only 4 lbs/ft. In other words
– three times the weight and almost twice the diameter!
Building
the Links
The simplest kind of link to build
is one that uses, at both ends, joints with threaded shanks and slip-in threaded
tube adapters. In this case, you only need to cut the tube to length, insert
and weld in the threaded adapters, screw in the joints and you’re finished.
When measuring the tube, you will, of course, have to account for the length
of the tube adapter, shank of the joint, and distance from shank to bolt hole.
When doing so, do not make the mistake of counting the entire length of the
threaded shank. I will normally measure the length of the threaded shank, then
subtract the length of the threads not available for adjustment. This is equal
to the length of the minimum number of engaged threads (calculated as the length
of the adapters internal threads plus 3-4 threads) and the length of the threads
taken by the jam nut. The resulting number is the length of threads available
for adjustment, which I then divide by two, using the resulting figure for the
calculation of link length – this allows me to essentially install the
link in the middle of its adjustable range so that I can later make it shorter
or longer as required.
At the other end of the scale is
a fixed link with both joints welded directly to the tube. This approach has
the advantage of strength and simplicity, but requires extremely careful and
accurate measurement and triple-checking as there is no ability to adjust the
lengths after construction. Mismatched or inaccurate link lengths will effect
steering geometry, suspension performance, and pinion angles – so great
care is required. |
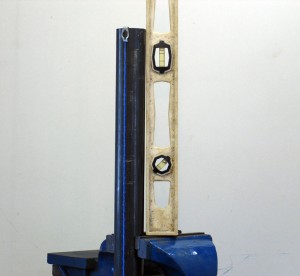 |
Figure 1 –
Using a level and plumb-line to mark tube centerline |
The other tricky part of making a
fixed link with joints welded to both ends is that you have to get both joints
at exactly 90° to the tube, and both in the same plane. If not, you will either
eat up precious misalignment just to install the link, or worse, not be able
to install it at all. Figure 1 illustrates the method I used to mark the
tube centerline for my fixed-length, lower, front links. First, clamp the tube
in a vice and use a level to make sure it is vertical both side-to-side and
front-to-back. Next, use a carpenter’s chalk line to mark a plumb centerline
on the tube. Using this centerline as a reference point should allow you to
notch the tube so that both joints will be square to the tube and in the same
plane.
Notching the tube is the final challenge
before welding up the links. There are three basic methods for notching tube:
tube notcher, chop-saw, and template. Using a tube notcher is the most obvious
method – providing you have one. The only caution is that many notcher’s
may have a difficult time getting through two inch diameter, half-inch wall
tubing. If you use a hole-saw type notcher, be particularly careful of it catching
in the cut and trying to break your wrists.
With a little patience and practice,
you can cut excellent notches in tube using a chop saw. The first step is to
mark the centerline of the tube in 2 places exactly 180° apart. Next, set the
required angle on your chop saw and chuck the tube in the saw with the blade
just touching the first centerline mark (Fig 2). Make the cut (fig 3), and the
tube should then look like fig 4. Next, rotate the tube in the saw 180° until
the blade just touches the opposite centerline mark (fig 5). Make the final
cut, and you will be left with 2 small slivers of tube and a well-formed notch
for joining to another tube (fig 6 & fig 8). To make quality, accurate cuts
you need to use a decent chop saw with a fairly rigid base and vice, and to
use a quality abrasive cutting wheel designed for cutting tube. I prefer Walter
brand cutting wheels as they are good quality, last well, and indicate on them
with a little icon whether they are suited to cutting tube. The key to success
with this method is how accurately you calculate and make the two cuts. Figure
9 illustrates the angle you are setting, and Table 3 gives some values for the
cut angle for various sizes of tube. Generally, the larger the angle, the deeper
and more narrow the notch. Figure 6 shows a notch cut at 30° and figure 7 shows
a notch cut at 45°. Because all chop saws will vary a little and even the best
are only capable of limited accuracy in angles the best results will be obtained
from using the values in the table as a starting point and then proceeding to
practice with your actual tube, keeping a 4.5” angle grinder handy to
clean up the notches. After the initial cuts, test-fit the tubes and make any
required touch-ups to the notch with the grinder (fig 8). Note that the values
in Table 3 are for joining two tubes at 90° to one another. If you want to join
the two tubes at an angle (either to offset the link from the joint, or more
likely in other tube work such as roll-cage building) you must adjust your cuts
as follows. Take the angle at which you want to joint the two tubes, and then
modify the initial cut angles by adding this value to one, and subtracting it
from the other. For example, if I wanted to join a 2” tube to a 2”
tube, the initial cut angle is 30°. If I wanted to join the tubes at a 15° angle,
I would add 15° to one cut and subtract it from the other. In this way I would
make one cut at 45° and the other at 15°. The values in the table were calculated
and kindly provided to me by Marc "Tigweld" Googer. Marc notes that
the figures given are for .120" wall tubing and that wall thickness can
dramatically affect fit. Thicker walled tube will require either an adjustemnt
to the figures shown or some post-cut cleanup with the angle grinder. The only
limitation to the chop saw method of tube notching is the angle-capacity of
the chop saw – most do not cut angles greater than 45°. NEVER ever be
tempted to bypass the chop saw’s vice and simply hold the tube at a steep
angle – no matter how strong you think you are there is a very good chance
the blade will bind in the cut, rip the tube from your hands, possibly taking
finger tips with it, and fling it across the shop with frightening force - as
usual - ask me how I know this!. If in doubt about the angle to use, it is best
to cut a little shallow (smaller angle) and finish the notch with a hand-held
angle grinder.
Table
3 - cut angle for various sizes of tube
(Data
kindly provided by Marc "Tigweld" Googer)
OD
of tube
being notched (in) |
OD
of tube
joined to (in) |
Initial cut
angle (degrees) |
2 |
2 |
30 |
1.75 |
1.75 |
28 |
1.5 |
1.5 |
26 |
1.25 |
1.25 |
22.5 |
1 |
1 |
20 |
1.75 |
2 |
25 |
1.75 |
1.25 |
45 |
1.25 |
1.75 |
20 |
1 |
2 |
12 |
|
 |
Figure 2 –
aligning first cut. |
|
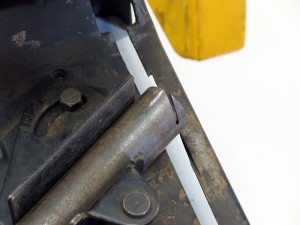 |
Figure 3 –
first cut in progress. |
|
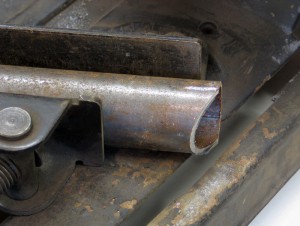 |
Figure 4 –
First cut completed. |
|
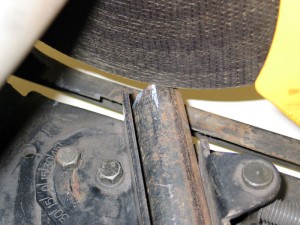 |
Figure 5 –
start of second cut |
|
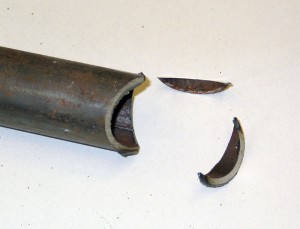 |
Figure 6 –
Completed chop saw notch cut at 30° |
|
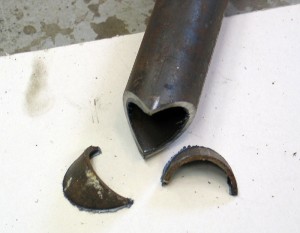 |
Figure 7 –
Chop saw notch cut at 45° |
|
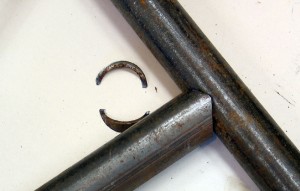 |
Fig 8 – Test
fitting the notch |
|
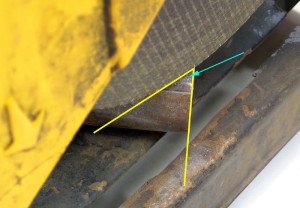 |
Fig 9 – cut
angle for chop saw notching |
The third method for notching a tube
is to use a computer program that will allow you to enter the tube dimensions
and will then calculate and print a template for your notch. You can then cut
out this template, trace it onto the tube, and use any of several methods to
cut along the lines of the notch (chop saw, 4.5” angle grinder with cutting
disc, plasma cutter, etc.) Depending on how rough your cutting was, you can
then clean up the notch with a 4.5” angle grinder to get a perfect fit.
One such program available on the internet is Winmiter. It is a shareware program
originally written for bicycle building enthusiasts. It accepts inputs of: large
tube diameter, small tube diameter, angle of joint, and centerline offset, in
metric or imperial units. It will then compute and display and/or print a simple
template. I used this method for notching the 2” x 3/8” tube for
my front lower links and it worked fairly well. Fig 10 shows the template
cut out and taped to the tube, ready to be traced. After cutting the notch with
a plasma cutter I then used a grinder to clean it up, pausing periodically to
check the fit (fig 11). |
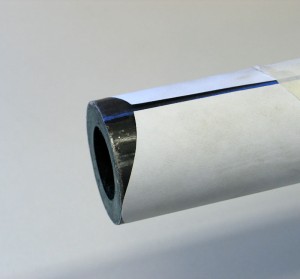 |
Fig 10 – Winmiter
template taped to 2” tube |
|
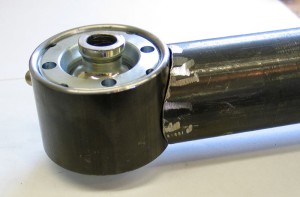 |
Figure 11 –
2” tube being test fit with RE bearing |
The final step in joining your links
to non-thread-in joints is to weld. The Evolution tube inserts come with a generous
bevel (fig 12) allowing for a good strong weld (fig 13). If welding a tube
directly to the body of a joint, make sure you have a good, clean, tight fit.
Fig 11 shows a 2” tube being test fit to a RE joint and reveals that
a little more grinder work is required on the tube to get the best fit. Patience
is the key as a tight fitting assembly will ensure a strong weld and ultimately
strong links. |
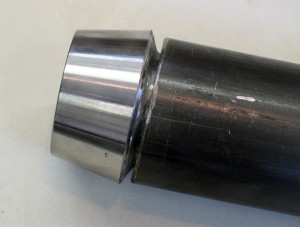 |
Figure 12 – Evolution threaded tube insert in 1.75” ID tube |
|
 |
Figure 13 – welded tube insert |
Figures 14, 15, and 16 offer a final
look at some of my completed links, built using the products and procedures
described in this article. May you experience the greatest success in your own
projects. Good luck!
|
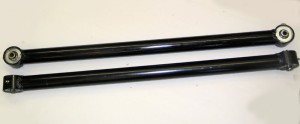 |
Figure 14 –
Fixed length lower front links using RE bearings and 2” x 3/8”
DOM |
|
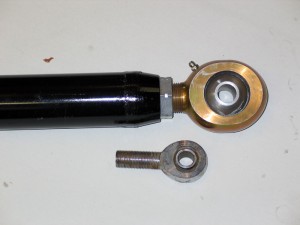 |
Figure 15 –
Completed link with Evolution Joint shown next
to standard ¾” Heim joint for scale. |
|
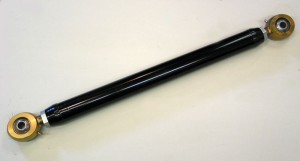 |
Figure 16 –
Adjustable top front link using Evolution Joints and 2.25 X ¼”
DOM |
Addendum:
What
do the numbers mean?
The four digit number you often
see quoted in reference to a particular type of steel (e.g. 1020 DOM)
is a standard four digit numbering system developed by the American Iron
and Steel Institute (AISI) in cooperation between with Society of Automotive
Engineers (SAE). The first two digits of the designation are the "classification"
of the steel. Mild (carbon) steels all belong to one of four classifications,
only two of which are of interest to us - the 10xx and the 15xx.
The four classifications of
carbon steel are:
10xx—nonresulfurized
carbon steel. Basic structural "low-carbon" or "mild"
steel.
11xx—resulfurized carbon steel. Free machining steels, inherently
brittle.
12xx—resulfurized and rephosphorized carbon steel.
15xx—nonresulfurized, high-manganese carbon steel. Basic carbon
steel used for low-cost forgings.
The first two digits of an
alloy steel's designation indicate the alloying elements as follows:
Designation |
Alloying Elements |
13xx |
Manganese |
40xx |
Molybdenum |
41xx |
Chromium & Molybdenum |
43xx |
Nickel, Chromium &
Molybdenum |
44xx |
Molybdenum |
46xx |
Nickel & Molybdenum |
61xx |
Chromium & Vanadium |
86xx |
Nickel, Chromium &
Molybdenum |
92xx |
Silicon |
For both mild and alloy steels,
the last two digits of the standard four digit designator indicate the
approximate carbon content of the steel in tenths of a percent. For example,
SAE 1020 contains approximately 0.20% carbon. The higher the carbon content
the higher the ultimate tensile strength of the steel — and the
lower the ductility.
Sometimes a suffix H is attached
to a AISI/SAE number to indicate that the steel has been produced to prescribed
hardenability limits. For example 1541H is a commonly used carbon steel
in the manufacture of axle shafts.
The four-digit designator not
only helps us to precisely identify the steel in question (so that we
can buy and use the right stuff), but also tells us quite a bit about
it at a glance. For example, I know that 4340 is a steel alloyed with
Nickel, Chromium and Molybdenum; and that it has a carbon content of approximately
0.40%.
If I want to know more, I can either research the exact properties of
the steel I’m considering, or I can get a general idea by using
the number and referring to a table of common alloying elements and their
effects, such as:
Element |
Effect |
Carbon |
Increases hardenability and strength |
Chromium |
Increases corrosion resistance, hardenability and wear resistance |
Manganese |
Increases hardenability and counteracts brittleness from sulphur |
Molybdenum |
Deepens hardening, raises
creep strength and hot-hardness, enhances corrosion resistance and
increases wear resistance |
Nickel |
Increases strength and
toughness |
Silicon |
Deoxidizes, helps electrical
and magnetic properties, improves hardness and oxidation resistance |
Vanadium |
Increases hardenability |
|
What
is an “Alloy Steel”?
Alloy steels are steels that
have had finite and precise amounts of alloying elements added to them
during their manufacture. Alloying Elements are chemical elements added
for improving the properties of the finished materials, such as nickel,
chromium, and molybdenum. Small, precise changes in the exact chemistry
of a steel can change its mechanical properties quite drastically. Generally,
alloying elements are added to steel to maximize some particular mechanical
property(ies). Of course, nothing in life is free, and there is always
a price to pay. The more alloyed a steel is, the narrower it's appropriate
use, as it becomes more and more specialized (narrow in focus). There
is also a trade off in the reduction of other properties: as hardness
and strength go up due to alloying with chromium and molybdenum - ease
of welding and ductility go down, and of course cost goes up - in some
cases WAY up.
Note that the hugely popular
designation "Chrom-moly" is a reference to the fact that the
steel in question has major alloying elements of Chromium and Molybdenum.
41xx and 43xx alloy steels can and frequently are both refereed to as
"Chrom-Moly Steel", though obviously the 43xx also has significant
Nickel added. |
The
Definitions
When researching, designing,
or discussing any fabrication project that uses steel, you may find the
flowing definitions of the properties of various steels useful.
Annealing - Applies normally
to softening by changing the microstructure and is a term used to describe
the heating and cooling cycle of metals in the solid state. The term annealing
usually implies relatively slow cooling in carbon and alloy steels. The
more important purposes for which steel is annealed are as follows: To
remove stresses; to induce softness; to alter ductility, toughness, or
electric, magnetic or other physical and mechanical properties; to change
the crystalline structure; and to produce a definite microstructure.
Plastic Deformation - Deformation
of a material that will remain permanent after removal of the load which
caused it.
Quenching & tempering -
procedure consisting of heating the material to the proper temperature,
holding at that temperature for a sufficient time to effect the desired
change in crystalline structure, and quenching in a suitable medium -
water, oil or air depending on the chemical composition. After quenching,
the material is reheated to a predetermined temperature below the critical
range and then cooled under suitable temperatures (tempering).
Stiffness – the ability
to resist deformation under load.
Strength - the ability to resist
an external force or load, without deforming, breaking, or rupturing.
Technically we say a material’s strength is the greatest stress
it can endure without rupturing. There are many specific kinds of strength,
from tensile, compressive, and shear to complicated combinations such
as torsional and bending.
Stress - a force or load applied,
divided by how big the part is (i.e. force per unit of cross sectional
area) measured in pounds per square inch, or PSI.
Strain - a change in shape
or dimension in response to a stress, usually expressed in percent elongation.
Toughness – The ability
of a metal to absorb energy and deform plastically before fracturing.
It is usually measured by the energy absorbed in an impact test.
Hardness – is the property
of resisting penetration. Normally, the hardness of steel varies in direct
proportion to its strength – the harder it is, the stronger it is,
and vice-versa.
Brittleness – is the
tendency of a material to fracture without changing shape. Hardness and
brittleness are closely related. The harder (and therefore stronger) a
metal is, the more brittle it is likely to be. Materials that are too
brittle will have very poor shock load resistance.
Malleability – is the
opposite of brittleness. The more malleable a material, the more readily
it can be bent or otherwise permanently distorted. As hardness was closely
related to strength, so then is malleability. Generally, the more malleable
a metal, the weaker it is.
Ductility – much like
malleability, ductility is the ability of the material to be drawn (stretched
out) into thin sections without breaking. The harder and stronger a metal
is, the less ductile, and vice versa.
Yield Strength - The point
at which a material exhibits a strain increase without increase in stress.
This is the load at which a material has exceeded its elastic limit and
becomes permanently deformed. Stress corresponding to some fixed permanent
deformation such as .1 or.2% offset from the modulus or elastic slope. |
|
References:
- Gren, Robert E., Oberg, E., Jones,
F.D., Horton, H.L., Ryffel, H. H. (Editors). Machinery’s Handbook, 24th
Edition, 1992, (Industrial Press, Inc)
|
|
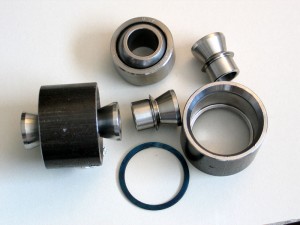 |
Sources: Evolution
Joints:
Evolution Machining & Fabrication
Inc.
#1 - 4115 64th Ave. S.E..
Calgary, Alberta T2C 2C8
Phone: (403) 236-3545 http://www.evolutionmachine.com
RE
Bearings & Poly Performance Uniballs:
Poly Performance Offroad Products
234 Tank Farm rd, Unit L & M
San Luis Obispo, CA 93401
Phone: (805) 783-2060
sales@polyperformance.com
http://www.polyperformance.com/ |
|