Much technical data was also gleaned
from the following sites:
http://www.engineersedge.com/
http://www.efunda.com/
http://www.steeltubeinstitute.org/
http://www.emjmetals.com/
http://www.usstubular.com/
I am also greatly indebted to the
following technical experts, most of them professional engineers, all of them
gentlemen. Without their
selfless sharing of technical facts and information I would never have been
able to understand all of this:
Thanks to:
Gordon, PIG, Ed Stevens, Dave Kamp
And very Special thanks to:
Robin Ansell, Goat1 and lt1yj
Table of Contents
Section 1 - Steel basics: what it
is, where it comes from, its structure, and why we use it so much
Section 2 - The concept of stress
and strain,
Section 3 - The critical definitions
- malleability, hardness, toughness, etc.
Section 4 - The steels of interest
to us - mild, carbon, alloy steel etc.
Section 5 - Steel manufacturing -
alloying, cold rolled, hot forged, etc.
Section 6 - Heat treating and hardness
|
Section 7 - Modes of Failure.
Section 8 - Dispelling myths / FAQ
- hollow vs solid, DOM vs HREW, square vs round, is pipe only for poop?
Section 9 - Equations
Section 10 - Tables
Section 11 - Glossary
Section 12 - Sources and Notes |
Section
1: Steel basics
What
is steel?
Steel is a metal. The Merriam-Webster online dictionary defines it a metal as:
any of various opaque, fusible, ductile, and typically lustrous substances
that are good conductors of electricity and heat, form cations by loss of electrons,
and yield basic oxides and hydroxides;
Yea, great – but really –
what is a metal, in terms of what we care about? Metals are materials that:
- are able to undergo a large degree
of plastic deformation (change in shape) without rupture or failure.
- can be beaten, stretched, pounded,
bent, rolled, extruded, molten, cast, and otherwise formed into useful parts.
- are elastic, meaning that, as
long as the load is not to great, they can return to original shape and form
after an external force or load is removed.
- are also generally strong –
that is, they are able to resist failure under high levels of load and stress.
Steel, in my humble opinion, is the
king of all metals, having the best of all these properties - especially considering
its weight and cost.
So, in summary, steel is
a metal that can easily be formed into useful parts, can resist high levels
of load or force without breaking, and can change shape (bend) in response to
a load and spring back to original shape.
Why
steel?
How is it that steel has such wondrous properties? The answer to this
question alone could fill several books. I will attempt to give a brief
answer, something we can refer back to when we need, in order to help our understanding.
My answer certainly won't make metallurgists of you!
As, noted, the reason steel is so
strong and yet flexible and formable is very complicated, but the answer all
boils down to it's atomic structure and the building blocks this atomic structure
leads to, that all interconnect and build on one another until we have the actual
steel.
Let me explain a bit further.
Not surprisingly, the answer lies
deep within its atomic structure. All I will say here, is that metals are made
up of atoms that have strong flexible atomic bonds, lie in very close formation
and that are arranged in a regular and repetitive fashion into crystal unit
cells of various shapes which are, in turn, built up, Lego-like, on a regular
and repetitive 3-dimensional lattice structure into crystals of metal called
“grains”. The nature of these atomic bonds, and the resulting crystal
lattice structure, is what lends metals, and particularly steel, it’s
combination of strength, hardness and malleability. In a gross
over-simplification, we can say that steel atoms bond and form crystals, small
crystals, or "grains" of metal join together to form a crystal lattice
structure, much like bricks join together to form a wall.
Continuing our brick wall analogy:
the nature of the crystal lattice structure - i.e. how regular the grains are
in shape and orientation - determines the properties (and chiefly of interest
to us, the strength) of the metal. In much the same way as the shape and
orientation of the bricks in a wall determine the properties or strength of
the wall. Compare an old-fashioned stone wall constructed from stacked
boulders and stones to a modern wall of precisely arranged rectangular concrete
blocks.
There are many factors that determine
the size, shape, and orientation of the grains and crystal lattice structure,
many of which we can manipulate. It is these factors and their manipulation
which really interests us. The factors range from the atoms themselves
i.e. the composition or "alloy" of the steel, to the shape and orientation
of the grains - affected by things like forging, heat treating, cold working
etc.
One more brick-wall analogy: The
bricks, their size, shape, and orientation to one-another determine not only
how strong a wall is - but also in what way it is strong. For example,
an old fashioned rock wall may have a great deal of strength if we bear down
on it from above - i.e. set something heavy on it and it will easily support
the load. However, lean against it sideways and it may easily topple over.
In much the same way, the different ways in which we manipulate and treat steel
can impart many different properties or "strengths" from compressive
strength to shear strength - more on this later.
Ultimately, it's all in the
atomic and inter-atomic bonds. How we forge the steel from ore, what alloying
elements we add to it, how we "work" it, and even how we machine and
weld the final product will all have an impact on the atoms/grains/crystal lattice
structure - and therefore strength and properties of the steel. Understanding
how this happens and why is chiefly the goal of this article.
As a point of trivia, there is no
such thing as a “molecule” of steel. In fact, metals, as a family
of elements, are distinguished from other elements in part because their crystalline
structure is made up of individual atoms (they are monatomic) as opposed to
molecules.
Where
does steel come from?
Steel is not a naturally occurring
substance - it is entirely man made. Steel is chiefly a combination of
two naturally occurring elements: iron and carbon (along with small amounts
of other elements - depending on the steel in question). The process by
which man makes steel, would, again, fill several volumes. Here is my
amateur synopsis:
Iron is mined from the ground in
the form if a reddish-brown rock called iron-ore. This ore is then smashed
up, strained, filtered, chemically treated etc, until ultimately it is melted
in huge blast furnaces into something called pig iron. The process uses
coke (a type of coal), which in turn imparts large amounts of carbon to the
pig iron. As a result, pig iron itself is full of impurities, brittle,
and unmachinable - practically useless. Except - it is the raw material
from which all other irons and steels are made. Pig iron is so produced
in either huge vats of molten material, or it is cast into ingots (in fact,
pig iron got it's name because the ingots or "chunks" produced were
thought to have resembled piglets).
Pig iron is then refined into either
metallic iron or steel using specialized furnaces and processes. The distinction
between the two is that metallic iron has between 2-6% carbon content, and steel
has <2% carbon content. Of course metallic iron is further refined
into, and categorized as, many different types of iron - from grey cast iron
to nodular iron; in much the same way as steel is further refined into and categorized
from low carbon steel to alloy steel. We'll explore all of these in detail
later. Metals like iron and steel, being largely composed of elemental iron,
are known as "ferrous" metals after the chemical symbol for elemental
iron - Fe.
A final word about carbon.
carbon is critically important to our whole discussion because it is
the presence of carbon that turns the element of iron that is naturally soft
and weak, into the strong, rigid materials we know as iron and steel. Precisely how this is so is beyond the scope of this article, suffice
to say:
The strength, hardness and toughness
that make the ferrous based metals useful to us are profoundly influenced by
the remarkable sensitivity of the physical and chemical properties of iron crystals
to relatively small percentages of carbon dissolved within their matrixes (actually,
the sensitivity is to the movement of dislocations within the crystal space
lattice). This sensitivity to dissolved carbon is in fact, the very basis of
ferrous metallurgy. [1]
A poor, but perhaps useful metaphor
may be the use of fibre-mat and resin in fibreglass work. The bulk raw
material of fiberglass is the fibre matting (as iron is to steel) - but by itself
the matting is of no practical use. Not until we add the resin to it to
make fibreglass (as we add carbon to iron to make steel) do we get a useful
product. In both cases, neither raw material is much use alone, but combine
them and we really have something. Similarly, though carbon may only be
present in small quantities, just as the amount of hardener added to fibreglass
resin has a profound effect on the material, so does the small amount of carbon
present in useful metallic iron and steel.
Section 2: Stress and Strain
You may have noticed that we have
already bantered around a bunch of terms that we really should define - just
so we're on exactly the same page. And there's many more terms to come.
So lets lay out some initial definitions now.
Strength - a measure of how strong something is! ha ha! Seriously, this is a very
important definition, as this entire series of articles is, in large part, just
about how strong things are. Not only that, but the truth is not nearly
as simple as my little joke above would lead you to believe.
In the broadest of terms, when we
speak of a substance or products strength, we are talking of it's ability to
resist an external force or load, without deforming, breaking or rupturing.
Technically we say a materials strength is the greatest stress it can
endure without rupturing (by rupturing - I mean the atomic bonds coming
completely apart.)
There are many specific kinds of
strength, from the "pure 3" - tensile, compressive, and shear to complicated
combinations such as torsional and bending. We will examine each of these in
detail throughout the article.
Stress. We
all know instinctively that, generally speaking, if we have 2 things made from
the same stuff, that the larger will be "stronger". In order
for us to be able to discuss the strength of material, and particularly to compare
different materials, we need a way to compare strength without constantly referring
to how big something is. That is, we need to be able to eliminate size
as a factor. We do this by employing the concept of stress. Stress
is a force or load applied, divided by how big the part is, in other
words force per unit of cross sectional area. It is common to measure the force
applied in pounds and the cross sectional area in square inches. Thus,
the unit for stress is pounds per square inch, or PSI
Using the concept of stress, we can
now compare relative strengths regardless of size. Say we have 2 steel
bars, one is 1 square inch in cross sectional area, the other 1/2 sq. in.
If they are both made from a material having a breaking strength of 10,000 psi,
one will break when 10,000 lbs is applied, the other when 5,000 lbs is applied,
despite that they are made from the same material. Conversely, if we have
2 products of unknown or difficult to determine size but we know that one is
made from a material with a yield strength of 75,000 psi and the other 100,000
psi, we know that the second is made of a stronger material (regardless of comparative
size), and we can also say that the first would have to be 25% greater in size
to be of equal strength. This logical approach can lead us to quite accurately
determine that, if the sizes are similar, the second is definitely the stronger
product.
Strain - closely allied to the concept
of stress - the concept of strain allows us to quantify or describe how
a part or material responds to an applied force or load. Quite simply: Strain is a change in shape or dimension in response to a stress.
It is usually expressed in percent elongation (%) Percent elongation is the
difference in length between the original length of a test specimen (often 2"
in length) and that same specimen after it has been ruptured by a tension load.
In other words, materials STRAIN
to resist a STRESS (much like people do to!).
Stress and strain are two separate,
useful concepts but the real power of these concepts is only realized when the
2 concepts are combined. There is a defined relationship between
stress and strain, discovered by an English bloke in 1680, that states the strain
of any material is proportional to the stress within it. It is known as Hooke’s
law and is simply stating what you already know – “the harder I
push on this, the more it will bend……”. What’s important
though, is that, up to a point, this relationship is proportional, or linear…meaning
that if I push twice as hard, it will bend twice as far. The point up
until which this is true is called the elastic limit. Realize that Hooke's
law applies not only while a load (stress) is applied, but also when it is removed.
Meaning, as long as we are within the elastic limit of the material (i.e. the
stress is less than the elastic limit of the steel) strain is always proportional
to stress, meaning if stress (load) is zero then so too is strain (distortion).
What we have just described is one of the most righteous properties of steel.
That is, it is "elastic" in nature - which is a fancy way of saying:
up to a point, we can bend it by applying a load, then if we remove the load
it will "spring" back to exactly the same shape and size it was originally.
We call this elastic deformation. Of course, we can apply a stress that
exceeds the elastic limit of the steel, and if we do, the steel changes from
elastic in nature (able to spring back) to plastic in nature - meaning the stress
applied, once it passes the elastic limit, will result in a permanent change
in shape of the metal. This we call plastic deformation.
Another quote from Mr Smith is in order:
A solid is considered to be elastic
if, after a change of shape due to an external load, the body returns to its
original size and shape when the load is relaxed. Plasticity, in the metallurgical
sense of the word, is the ability of a metal to be deformed beyond its range
of elasticity without fracture; the result is a permanent change in shape.
These two related properties are the most significant of all the characteristics
of the family of metals. Plasticity gives us the ability to form metals
into useful shapes and elasticity allows us to use metal fabrications as load-bearing
members in our structures. [2]
You can begin to see now, how with
a little knowledge, and an idea of the stress/strain diagram we can solve forever
the arguments of whether something is stronger than something else, whether
it is "too brittle" or will "bend before it breaks" etc.
Let's examine a sample, theoretical
graph of stress vs strain, called a stress/strain diagram
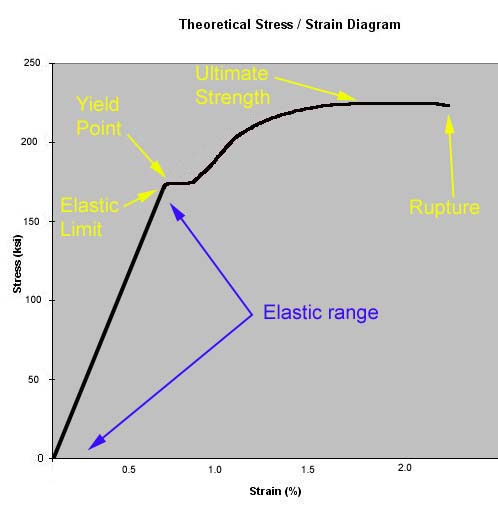
*Diagram concept adapted from "High Performance Hardware". Forbes
Aird; Berkley Pub Group, 1999 p.14
There are a few important concepts
to note here:
- This is an example only, the numbers
are not meaningful, and the slopes have been hugely exaggerated for illustrative
purposes.
- Note the straight line portion,
the "elastic range" of the metal (indicated by the blue arrows).
This is the region where stress and strain are directly proportional - hence
the straight line. Remove the stress, the strain disappears too. If this were
a real metal, any load below about 170, 000 psi can be born without permanent
shape change.
- Note the elastic limit - The
point on the stress-strain curve beyond which the material permanently deforms,
even after after the stress is removed
- Note the Yield Point - this is
the point at which a material exhibits a strain increase without increase
in stress. There is a subtle but important distinction between the yield point
and elastic limit, that we can see if we observe the horizontal line between
the elastic limit and the yield point. We can safely stress something to the
elastic limit, but once we reach the yield point, it is already too late -
even if we add no more stress, strain will continue to increase. You can illustrate
the concept by pulling on a piece of taffy or warm plastic or even play-dough.
Pull on it gently but increasingly harder, at some point stop increasing how
hard you pull and just maintain a constant pull: if you pulled hard enough
(equal or greater than the yield point) even though you stop pulling harder,
it will continue to stretch and still come apart. At the yield point a material
has exceeded its elastic limit and becomes permanently deformed.
- It is one of those "facts
of life" that the elastic limit is of great interest to us, but that
it is very difficult to accurately measure a materials exact elastic limit.
Because of this we have the concept of "yield strength". The yield
strength (not to be confused with yield point) is stress at which a material
exhibits a pre-determined, standard amount of elongation (strain). The usual
standard is 0.002" of elongation per inch of original length, or strain
of 0.2%. Ultimately, in practical use, we generally use the materials yield
strength to describe its approximate elastic limit, and can do so reasonably
safely since the 2 values are, in reality, so close that they are practically
interchangeable. We should never be designing that close to the limits anyway.
- Note that the highest point on
the curve describes the ultimate strength of a material. This is the maximum
stress a material can withstand without rupture or failure. It is calculated
by dividing the load at failure by the original cross sectional area.
- Note that one can apply a stress
higher than the yield point, up to and including the stress at the ultimate
strength, and still the material will not rupture. But because the yield point
has been exceeded, there will be a permanent deformation - illustrated by
the fact that the graph is a curve at any point past the yield point.
- Note that there is a defined
rupture point where the curve stops. This is the amount of deformation at
which the material actually rips apart or ruptures. How far to the right this
point is, is an important part of the overall picture of the materials' properties.
- Note that the total area under
the curve represents the total of all possible stress and strain combinations
where the metal has not yet ruptured. As such, it is an indication of the
materials "toughness", toughness being the ability of a metal to
absorb energy and deform plastically before fracturing
Comparative stress/strain diagrams
Now that we have a good idea of all
that the stress/strain diagram illustrates, it is extremely educational to examine
some comparative stress/strain diagrams.
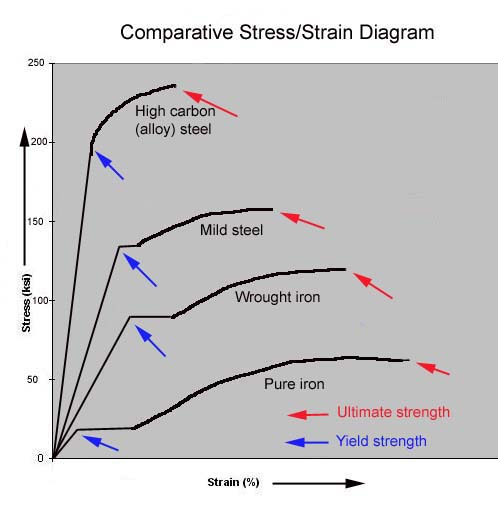
*Diagram concept adapted from "Engineer to Win". Carroll Smith; Motorbooks
International, 1985 p.41
Examining this diagram carefully,
we can learn much about the properties of different materials, and ultimate
ly that materials suitability for a given part.
Note: Again, this diagram is for
illustrative purposes, the actual scale of numbers used are not real, but are
for illustration only - the relative shape and size of the curves between the
different materials is real however. It is the concepts that are important.
A good understanding of what is really
going on here can help us understand much of the "common wisdom",
as well as the persistent myths that are out there regarding steel and iron
parts - from the "grade 8 bolts are too brittle" nonsense to other
commonly held misconceptions about cast iron and steel.
The differing yield strengths of
the different materials are indicated by the blue arrows, and the ultimate strengths
the red arrows.
Note:
- Pure iron yields under such low
stress that it is of no practical use in constructing load bearing parts.
- That the longer the curves (from
left to right) the more ductile the material - the more it can deform without
rupturing BUT keep in mind the relative yield strengths. Remember -
Once a material has "yielded", it has exceeded its elastic limit
and will never return to original shape/size - it has permanently deformed
and so in almost every case must be considered to have failed and requires
replacement.
- Notice the vast differences
in the stress a material can stand before yielding. Wrought iron may
have a long curve, and therefore be able to deform substantially before rupturing,
but yields at such a low stress that it is not a very good choice. In
contrast, high carbon steel may rupture comparatively soon after having yielded
(the curve is shorter left to right), but it doesn't yield until subjected
to such a far greater stress than other materials that it is actually much
stronger.
- As well as noting the
length of the curve left to right (elongation, or deformation) between yield
and rupture, note also the vertical distance in stress between yield and rupture.
Note that the softer, weaker materials rupture after a comparatively small
increase in stress since beginning to yield, while the stronger materials,
such as alloy steels, can tolerate a much greater increase in stress between
beginning to yield and rupturing.
These last 2 points are the root
of what I see as one of the most often misquoted and most poorly understood
concepts of material strength - the interrelationship between ductility and
strength.
Take for example the classic misconception/myth:
"Grade 5 bolts are a better choice than Grade 8 because the grade 8 are
too brittle and will snap, while the grade 5 will bend before breaking".
By examining the above stress/strain
diagram and imagining the grade 5 bolts represented by the "mild steel"
curve and the grade 8 bolt by the "alloy steel' curve (accurate enough
for our purposes) we can clearly see both the underlying "truth" in
the myth, as well as the great error that ultimately leads it to be an incorrect
statement and a very poor guide for bolt choice in all but a very few cases.
First the "truth".
We can see from the curve, that indeed, the grade 5 bolt will deform more (exhibit
greater strain) between yield point and rupture. However, the myth neglects
two critical factors that become abundantly clear when looking at a stress/strain
diagram:
- The yield point of the grade 8
is MUCH higher than the grade 5 bolt. Sure the grade 5 bolt will bend
before breaking, and proportionally more than the grade 8 - but it will have
yielded, bent, and ruptured long before the grade 8 bolt has even approached
yield strength.
- The vertical distance (stress
or load increase) between the yield strength and the ultimate strength of
the grade 8 is much greater than the grade 5 - meaning that, while the grade
8 may not bend much before breaking - it will tolerate a much greater increase
in load between beginning to yield and rupturing. In contrast - the grade
5 will begin to yield, and then it will take very little additional stress
(load) to make it bend a whole lot more, and eventually break.
And finally, one more kernel of "truth"
to the myth. The one place the grade 5 may be superior is in the area
of "impact strength" or "toughness". By impact strength
we mean the ability to withstand a sudden impact or shock load. An example might
be when a snowplow running through powder at 30 mph suddenly hits an 8"
concrete curb (ouch!) The loads imposed by such a sudden impact are exponential,
off the chart, and hard to calculate or predict accurately. Remember that
we said that the total area beneath the curve is an indication of the materials
toughness, and that toughness was the ability to absorb energy? This ability
to absorb energy is exactly what we need in the case of a severe impact shock
load, and we can see that the area beneath the "grade 5" curve is
greater than beneath the "grade 8" curve. Having said that though
- the grade 5 bolt subjected to a shock load is ONLY a better choice because
it may allow you to limp home without the plow (or whatever) separating from
the truck - the bolt will almost certainly still have passed the yield point
and has technically "failed" and therefore requires replacement.
This case study is but one example
of how we can apply a true and accurate understanding of materials, specifically
stress/strain diagrams, to either our own part fabrication or our judgement
of which part is really "strongest", "best", or "most
suitable".
Essentially, the choice of a material
for any given structural duty or load bearing part boils down to a considered
compromise or trade off between how high and steep the curve is (the yield strength)
and how long it is (how much it can deform before rupturing), and the height
between yield and ultimate strength (how much more stress it can take since
yielding before rupturing)
Ultimately, we can label a stress/strain
diagram slightly differently to help us understand the qualitative and quantitative
differences between different materials. I have chosen to do so like this:
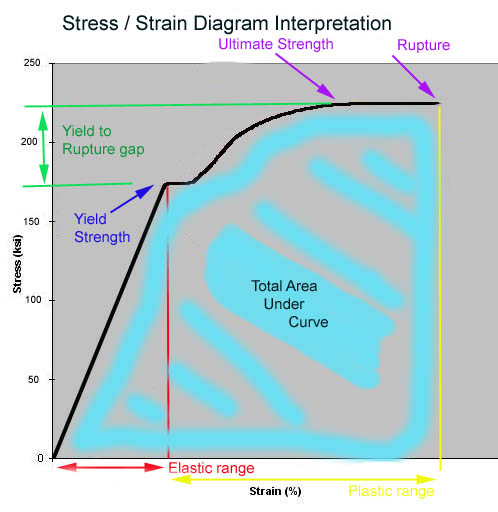
- The yield strength (blue arrow)
describes the stress at which the material begins to deform permanently -
safety factors not withstanding, it is the maximum load the part should ever
see.
- The elastic range (red arrow)
indicates how much the part can be loaded and still spring back
- The Elastic Range +Plastic Range
(red + yellow arrows), or total curve length indicates how ductile the material
is - how much it can deform without breaking
- The total area under the curve
(light blue shading) indicates how tough the material is - how much energy
it can absorb while deforming plastically and not breaking
- The yield to rupture gap (green
arrow) indicates how much more load a part can take after it begins to yield,
before it breaks.
One final point - remember
- it is the whole stress/strain curve that really describes how a material will
react under load - the size, shape, etc. - NOT just any singular value (this,
in fact shows the fallacy we indulge in when we blithely compare products by
quoting just a single property - like ultimate tensile strength or the like).
Compare, if you will, the following 2 curves for 2 different, completely hypothetical
materials. Note from the curves that, though they share very similar values
in yield strength and even similar ultimate strength, they are VERY different
materials and will react under load in very different ways - making them potentially
much more or less suitable for any given use.
Study the diagram, and once you completely
see and understand this, you are ready to proceed, young grasshopper!
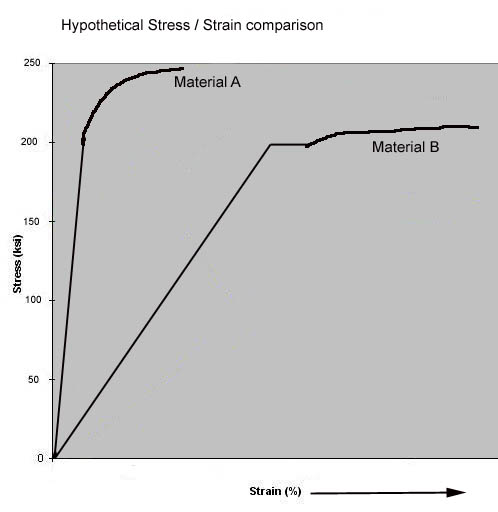
Section
3 - The Critical Definitions
Now, it would be impractical for
us to try and communicate about different materials and parts simply by comparing
stress/strain diagrams, despite the great amount of information they portray;
not to mention how complicated it is to collect the data to plot an actual graph.
As such, we have a whole vocabulary surronding metal parts that we use to describe
the properties of various steels, and the parts made from them. Here are
some of the most important definitions. Note how they can all be derived
from, illustrated by, or relate back to the stress/strain diagram.
Hardness –
is the property of resisting penetration. Normally, the hardness of steel varies
in direct proportion (i.e. as one gets bigger so does the other and vice versa)
to its strength – the harder it is, the stronger it is, and vice-versa.
Brittleness –
is the tendency of a material to fracture without changing shape. Hardness and
brittleness are closely related. The harder (and therefore stronger) a metal
is, the more brittle it is likely to be. Materials that are too brittle will
have very poor shock load resistance.
Malleability –
is the opposite of brittleness. The more malleable a material, the more readily
it can be bent or otherwise permanently distorted. As hardness was closely related
to strength, so then is malleability. Generally, the more malleable a metal,
the weaker it is.
Ductility –
much like malleability, ductility is the ability of the material to be drawn
(stretched out) into thin sections without breaking. The harder and stronger
a metal is, the less ductile, and vice versa.
Toughness –
The ability of a metal to absorb energy and deform plastically before fracturing.
It is usually measured by the energy absorbed in an impact test. The area under
the stress-strain curve in tensile testing is also a measure of toughness.
You can see how there is a trade-off
between a metal’s malleability/ductility and its hardness/strength (which
makes perfect logical sense – since malleability is the ease with which
we can form it, by applying force, and strength is its ability to resist force).
There are a whole group of people employed in a field called “physical
metallurgy” whose job it is to figure out how to use things like alloying,
heat treatment, and cold-working to skew this relationship (malleability/strength)
in our favour, so that hopefully we can develop materials that are both strong
and malleable. It will, of course, come as no surprise that their best
efforts cost the most money - aint it always the way! We'll be looking at what
they've come up with so far in a little while.
Before we begin our examination of
specific steels and treatments, there are a couple more principles we need to
get under our belts - the modulus of elasticity and the concept of stiffness.
Modulus
of elasticity and the concept of stiffness.
Intuitively we all know that load
bearing parts must be strong, must be built from material that is strong.
But there is more to it than that. We already defined strength
as the greatest stress a material can endure without rupturing. But
that's not all - for given just that definition - we could decide to build load
bearing parts out of soft materials that are strong - like copper and rubber
- they can tolerate large loads without rupturing. However, we know instinctively
they wouldn't be suitable for building bridges, buildings, crankshafts, frames
and axles - they are too flexible and while not rupturing under the load - they
would deform too much. So - what we need is a material that while
strong, will also resist deforming under load - we call this property STIFFNESS.
We need load bearing parts made from strong (so they don't break) and stiff
(so they can bear the load without excessive deformation) materials.
How do we determine what materials
are suitably "stiff" as well as being strong? The problem is
complicated by the fact that how stiff something is, is a function of not only
the material, but also the shape. For example, take a piece of paper - not very
stiff is it? Now roll it into a tube and press it together lengthwise
- pretty stiff eh? In much the same way as we use the concept of stress to isolate
strength due to material from strength due to size; so we need a way to isolate
stiffness due to structure (shape) and stiffness due to material. Another
English guy figured it our for us. In 1800 English physicist Thomas Young discovered
that he could rewrite Hooke's law to read "for any material, stress
divided by strain is equal to a constant". What this deceptively
simple statement hides is the very fabric of all structural design engineering
- namely that elastic materials, such as steel, all have a unique "constant
of elasticity" that describes the materials elasticity - it's ability to
spring back into shape after a stress is removed. This constant of elasticity
is a measure of how stiff the material is - the larger the constant, the larger
the stress than can be applied without exceeding the elastic limits of the material,
and the stiffer the material.
This "constant"
is unique and constant for each material, and is known as the Young's modulus
or the "modulus of elasticity" of the material. In
order to be able to compare materials, in much the same way as there is s standard
way to measure yield strength (stress required to produce 0.2% elongation),
there is a standard way to calculate Young's modulus. Young's modulus
is defined (and calculated) as the the stress required to double the length
of a test specimen. Obviously this is a theoretical value, useful only
for comparing materials stiffness, as no structural material on earth can actually
be doubled in length without rupturing. The modulus of elasticity
for all steels is about 30, 000, 000 psi !!!!
Stop! Read that again!
Yes, that's right - the modulus of elasticity is the same for ALL steels.
This means they are all comparably stiff, they will ALL resist bending or twisting
about the same amount - from cheap pipe to expensive cr-mo tubing. The
difference between them is what happens when they bend - in other words, the
stress/strain curves are different. The better, more expensive steels, due to
their much higher yield points and greater elastic ranges, will be able to easily
shrug off the load, wheras the lesser material may yield (take a permanent set,
or bend) or actually rupture. This is very important, and hugely misunderstood
concept, so I'll repeat it. All steels will bend or twist the
same amount under the same load - the difference is in how they handle this
loading - good steel will "spring back", poorer steel will bend permanently
or break.
Mathematical proof of this comes
from the equation used to determine how much a tube will deflect under a given
load. The equation is:
P*L / (E*I)
where:
P = the load (force) placed on the
tube (lbs)
L = the length from where the tube is supported to where the load is applied
(in)
E = modulus of elasticity (same for all steels)
I = Moment of Inertia.
In comparing 2 tubes, the only factor
in this equation that can change is the Moment of Inertia, I
The formula for calculating I for
any tube is:
I = (0.049*OD^4) - (0.049*ID^4)
Where:
OD = the outside diameter of the
tube
ID = the inside diameter of the tube
Note that the equation does not take
into account anywhere the type of steel the tube is made from. The factors
that effect how much the tube will deflect, or bend, are just the OD and ID
of the tube (or OD and wall thickness if you prefer, it amounts to the same
thing); with OD being the much more powerful determining factor.
Now, you might reasonalby ask - why
build anything of expensive steels then? Where are the equations to deal with
that? Remember, the tube will deflect the same amount, but whether it
survives that deflection is where we get into the difference between steels,
using the concept of yield strength.
How much load the tube can handle
before yielding (changing shape permanently) is calculated as:
Ld = 2*I/OD*Fy/L
Where:
I = I = Moment of Inertia
OD = the outside diameter of the tube
L = the length from where the tube is supported to where the load is applied
(in)
Fy = the yield strength of the steel in question.
This last factor, Fy, is where the
different steels will have hugely different values - from 30,000 psi for A-53
welded pipe to 240,000 psi for quenched and tempered 4340 Cr-Mo tubing.
I should point out that these equations
are shown simply for the purpose of understanding and illustrating the concepts
discussed: DO NOT USE THEM for calculations, as they may not
include critical elements such as design factor, impact loads, safety margins,
and fatigue factors! (that's what professional Engineers are for :-)
Mr Smith summarizes quite nicely:
"We do not build structures
from materials with low moduli of elasticity [non-stiff, flexible] simply
because such structures would sag under any reasonable load...We do not make
structures from weak materials simply because such structures would break under
load. Together the two properties of stiffness and strength define the
physical properties of a solid material. For instance:
- Steel is strong and stiff
- Copper is strong and flexible
- Fibreglass is weak and stiff
- Lead is weak and flexible" [3]
And finally, before moving on to
the next section, we shall now cover some of the other more commonly encountered
and more important definitions. Other definitions are covered in the glossary:
Alloy
The mixture of any element with a pure metal. However, there are several
elements regularly occurring in plain carbon steel as manufactured, such
as carbon, manganese, silicon, phosphorous, sulphur, oxygen, nitrogen
and hydrogen. Plain carbon steel is therefore an alloy of iron and carbon
and these other elements are incidental to its manufacture. Steel does
not become alloy steel until these elements are increased beyond their
regular composition for a specific purpose, or until other metals are
added in significant amounts for a specific purpose.
Alloying Elements
Chemical elements added for improving the properties of the finished materials.
Some alloying elements are: nickel, chromium, manganese, molybdenum, vanadium,
silicon, copper.
Alloy Steel
Steel is considered to be alloy steel when the maximum of the range given
for the content of alloying elements exceeds one or more of the following
limits: Manganese 1.650/0, silicon,.60%, copper,.600/0, or in which a
definite range or a definite minimum quantity of any of the following
elements is specified or required within the limits of the recognized
field of constructional alloy. Steels: Aluminium, chromium up to 3.9~,
cobalt, columbium, molybdenum, nickel, titanium, tungsten, vanadium, zirconium,
or any other alloying element added to obtain a desired alloying effect.
Carbon Steel
Steel is classified as carbon steel when no minimum content is specified
or required for aluminium, boron, chromium, cobalt, columbium, molybdenum,
nickel, titanium, tungsten, vanadium, or zirconium, or any other element
added to obtain a desired alloy effect; when the specified minimum for
copper does not exceed .40% or when the maximum content specified for
manganese does not exceed 1.650/0; silicon .600/0; copper .60%.
Cold Finishing
The cold finishing of steel, generally used for bars and shafting, may
be defined as the process of reducing their cross sectional area, without
heating, by one of five methods: Cold rolling, Cold drawing and grinding,
Turning and grinding, Cold drawing, or Turning and polishing.
Cold Rolling (Cold Finishing)
A forming process in which metal is rolled or drawn through dies, usually
at room temperature. This produces a product with certain advantages over
hot rolled steel, such as tighter tolerances, increased properties, improved
finish and straightness.
Ductility
The ability of a material to be plastically deformed without fracturing
Elastic Limit
The greatest stress which a material is capable of developing without
a permanent deformation remaining upon complete release of the stress.
Endurance Limit
Also known as fatigue limit, a limiting stress, below which metal will
withstand without fracture an indefinitely large number of cycles of stress.
If the term is used without qualification, the cycles of stress are usually
such as to produce complete reversal of flexural stress. Above this limit
failure occurs by the generation and growth of cracks until fracture results
in the remaining section.
Fatigue
The phenomenon of the progressive fracture of a metal by means of a crack
which spreads under repeated cycles of stress.
Fatigue Resistance
The ability of a metal to withstand repeated and varying loads.
Ferrous
Metals or alloys that contain appreciable amounts of iron.
Forging
A hot working operation generally involving plastic deformation of metal
at high temperatures into desired shapes with compressive force.
Fracture Toughness
The ability of a material at a given temperature to resist further crack
propagation, once a crack has started.
Hardness
The ability of a metal to resist penetration, defined in terms of the
measurement (Brinell, Rockwell,Scleroscope, Vickers, Knoop etc.)
Hardenability
This relates to the ability of steel to harden deeply upon quenching and
takes into consideration the size of the part, the method of quenching
and the analysis and grain size of the steel. Carbon steels are considered
as shallow hardening and various alloy and tool steel grades are considered
deep hardening or through hardening.
Hardening
Increasing the hardness by suitable heat treatment, usually involving
heating and cooling. When applicable, the following more specific terms
should be used: age hardening, case hardening, flame hardening, induction
hardening, precipitation hardening, and quench hardening.
Heat Treatment
An operation or combination of operations involving the heating and cooling
of a metal in the solid state for the purpose of obtaining certain desirable
conditions or change in properties or metallurgical structure. Heat treating
operations include annealing, normalizing, quenching and tempering, etc.
Hot Rolled
Hot rolled products are those products that are rolled to finish at temperatures
above the recrystallation temperature.
Impact Toughness
The ability of a material to resist fracture under an impact.
Mechanical Properties
The properties of a material that reveal its elastic and inelastic behaviour
where force is applied, thereby indicating its suitability for mechanical
applications; for example, modulus of elasticity, tensile strength, elongation,
hardness and fatigue limit.
Modulus of Elasticity
Measure of stiffness. The ratio within the limit of elasticity of the
stress to corresponding strain. The stress in pounds per square inch is
divided by the elongation in fractions of an inch for each inch of the
original gauge length of the specimen. The modulus of elasticity for cold
rolled steel is 29,500,000 psi and for other steels varies between 28,600,000
and 30,300,000 psi.
Plastic Deformation
Deformation of a material that will remain permanent after removal of
the load which caused it.
Quenching
A process of rapid cooling from an elevated temperature by contact with
liquids, gases or solids.In the heat treating of steel, the step of cooling
metals rapidly in order to obtain martensite by immersing or quickly cooling
the steel in a quenching medium. The quenching media may be water, brine,
oil, special solutions, salts or metals; and the intensity of the quench
is determined by the temperature, volume and velocity of the media. In
the case of air hardening tool steels the quenching medium is air at room
temperatures.
Residual Stress
Macroscopic stresses that are set up within a metal as the result of non
uniform plastic deformation or thermal gradients. Stresses of this nature
are caused by cold working or by drastic gradients of temperature from
quenching or welding.
Rockwell Hardness
A method of measuring the hardness of materials (resistance to penetration).
Rockwell measures the hardness by pressing an indentor into the surface
of the steel with a specific load, then measuring how far the indentor
was able to penetrate. There are a number of Rockwell tests the most common
is Rockwell B.
Rolling
A term applied to the operation of shaping and reducing metal in thickness
by pressing it between rolls which compress, shape and lengthen it following
the roll pattern. Steel is either hot rolled or cold rolled depending
upon the product being manufactured,
Scale
A complex iron oxide formed on the steel surface during the hot rolling
operation or formed on steel parts which are heat treated in the presence
of oxygen.
Steel
A solid solution of iron and carbon. An iron-base alloy, malleable
in same temperature range as initially cast, and containing carbon in
amounts greater than .05% and less than about 2.00%. Other alloying elements
may be present in significant quantities, but all steels contain at least
small amounts of manganese and silicon.
Strain
Deformation produced on a body by an outside force.
Stress Relieving
A process of reducing residual stresses in material by heating to a suitable
temperature and holding for a sufficient time. this treatment may be applied
to relieve stresses inducted by casting, quenching, normalizing, machining,
cold working or welding.
Temper
The state of or condition of a metal as to its hardness or toughness produced
by either thermal or heat treatment and quench or cold working or a combination
of same in order to bring the metal to its specified consistency. A condition
produced in a metal or alloy by mechanical or thermal treatment and having
characteristic structure and mechanical properties.
Tensile Strength
The maximum load in pounds per square inch that the sample will carry
before breaking under a slowly applied gradually increasing load during
a tensile test. The ratio of maximum load to the original cross-sectional
area.
Toughness
The ability of a metal to absorb energy and deform plastically before
fracturing. It is usually measured by the energy absorbed in a notch impact
test such as the Charpy or Izod Impact Test. The area under the stress-strain
curve in tensile testing is also a measure of toughness.
Ultimate Strength
See tensile strength.
Work hardening
An increase in resistance to deformation (hardness and strength) caused
by cold working.
Yield Point
The yield point is the load per unit area at which a marked increase in
deformation of the specimen occurs without increase of load during a tensile
test.
Yield Strength
The point at which a material exhibits a strain increase without increase
in stress. This is the load at which a material has exceeded its elastic
limit and becomes permanently deformed. Stress corresponding to
some fixed permanent deformation such as .1 or.2% offset from the modulus
or elastic slope.
Young's Modulus
Same as modulus of elasticity. |
Section
4 - The Steels of interest to us.
OK - hopefully we now have a good
comprehensive understanding of what the different properties of materials are
- from elastic range and yield strength to ductility and ultimate strength.
Now what we need to do is develop
and understanding of how and why some materials have these differing properties,
followed by looking at the actual and relative properties of different irons
and steels we will encounter, and finally which we should choose (or demand
our suppliers and manufacturers choose) and why.
There are really three groups of
metals that are of greatest interest and use to us. They are all ferrous metals, meaning they are iron based
and are magnetic. The groups are:
- cast irons
- carbon steels
- alloy steels
We will now examine each in a bit
of detail.
Cast Irons
Ahhh - yes, the much maligned, hugely
misunderstood cast iron. Let me get this off my chest right now. The term
CAST IRON does not refer to a specific material with properties that we can
discuss. It is a GENERIC TERM for a whole group of ferrous metals that are made
up of iron, silicon, and carbon. The name has 2 parts - CAST referring
to the fact that these metals can be readily poured into moulds (cast) when
molten, to make parts, and IRON for the chief element that makes them up. It
is sometimes (though rarely) necessary, and therefore just barely acceptable,
to use the term "cast iron" when referring to the material from which
something is made - but ONLY if we do not know the more specific type of cast
iron. It is NEVER acceptable (though vast numbers of derelicts and miscreants
are guilty of it!) to shorten this further and refer to any material by calling
it 'cast' and using the word cast as a noun. In our world, "cast"
is a verb, and is the method of making a part by pouring molten metal into a
mould.
There, I feel better, don't you?
Now, there are several different
types of cast irons that we should know about, and within each type there are
often several different "grades." The different types of cast iron
are distinguished by the form which the carbon takes - be it carbides, graphite,
flakes, nodules, etc. The different types are:
Gray Iron
Composed of iron and silicon and carbon, with it's carbon content
in the form of very thin interconnected flakes of graphite Gray iron possesses
excellent castability and machinability so that complex parts can be readily
cast and economically finish machined. The material has modest tensile strength
values, good wear resistance, and good resistance to galling. It is economical
to produce, cast and finish. Some examples of its use include: machine tool
bases, ways and housings, disc brake rotors, cylinder blocks and heads.
White Iron
Having it's carbon content in the form of granules of iron carbide
(due to low silicon content and rapid cooling when cast); white iron is very
hard and brittle and virtually unmachinable. It is therefore of little
practical use to us, despite having high compressive strength and good resistance
to wear and abrasion. It is, however, often the starting point for malleable
iron.
Malleable Iron
Malleable Iron has most of its carbon content in the form of irregularly
shaped lumps or nodules of graphite mixed in the matrix (lattice) of iron.
These nodules of graphite are not connected to one another though. Malleable
iron is created by careful and precise heat treatment of solid white iron castings.
The result is a cast iron that is extremely tough (toughest of all cast irons)
and that can have (depending on the exact heat treatment) tensile strength and/or
ductility similar to a mild carbon steel. It is not as easy to cast or
machine as gray iron and therefore is usually only used to cast relatively simple
parts. It is, however, often used for: hand tools (e.g. C-clamp, pipe
wrench), brackets, hangars, axle housings, drive yokes, connecting rods, brake
callipers, etc.
Nodular (Ductile) Iron
Named "Nodular Iron" because all of it's carbon content appears as
tiny spherical nodules of graphite, and with carbon content of up to 10%, nodular
iron combines the best properties of gray iron and malleable irons. It
has both excellent castability as well as very good machinability while being
the most ductile of all cast irons and having very high tensile strength (for
a castable metal). With carefully controlled changes in chemical composition
(it can be alloyed with other elements such as nickel, molybdenum, vanadium,
etc - much the same as steel) and/or heat treatment it can be used to
manufacture very strong, stiff, tough components. The trucking and
transportation industries have been quick to appreciate nodular castings as
lighter and stronger replacements for complex steel weldments and for their
ability to produce complex structural shapes - both cored and solid - that are
strong, light, and cheap. Examples include such critical components as
crankshafts, gears (including ring and pinion sets), and front suspension steering
knuckles. [4]
One of the most popular examples
of nodular iron applicable to us must be the famous Ford 9 inch rear axle with
the highly sought after nodular housing. Note also that some popular Dana
axles (center sections) are cast from malleable iron (e.g. Dana 30) and some
from Nodular Iron (e.g. Dana 44, 60)
Carbon
Steels
It stands to reason that we cannot
possibly describe or compare something unless we have a common language and
a way to ensure we're talking about the same thing. In other words, a way to
make sure we are comparing 'apples to apples". This is, in fact,
one of the areas most full of error that I encounter on the web - people are
not comparing "apples to apples". Hopefully, after reading this
section, we will all be able to do so more accurately.
Steel Designations.
Numbering systems currently in use
today for steel have been developed over the years by various groups, including:
trade associations, engineering societies, standards organizations, and private
industry groups. Some examples are those developed by the American iron
and Steel Institute (AISI), Society of Automotive Engineers (SAE), American
Society for Testing and Materials (ASTM), American National Standards Institute
(ANSI), Steel Founders Society of America, American Society of Mechanical Engineers
(ASME), and the American Welding Society (AWS). You can see how it would
be easy to fall into the trap of comparing apples to oranges! Not to worry,
for our use, it's pretty easy as we generally stick to SAE/AISI designators.
If you have or come across a steel with a different designator, there are many
good trade publications that contain tables showing equivalent designations.
All carbon steels, the types we are
interested in, (at least in North America) are designated using a standard four
digit numbering system developed in cooperation between the American Iron and
Steel Institute (AISI) and the Society of Automotive Engineers (SAE).
For example, we are often used to seeing different steels referred to as 1020
or 4130 or 4340. The numbers are not arbitrary, they have specific meaning,
and can tell us a lot about the steel in question. The first 2 digits of the
designation are the "classification" of the steel. Carbon steels all
belong to one of four (4) classifications, only two of which are any use to
us - the 10xx and the 15xx. The four classifications of carbon steel
are:
10xx—nonresulfurized carbon
steel. Basic structural "low-carbon" or "mild" steel.
11xx—resulfurized carbon steel. Free machining steels, inherently brittle.
12xx—resulfurized and rephosphorized carbon steel.
15xx—nonresulfurized, high-manganese carbon steel. Basic carbon steel
used for low-cost forgings.
The last two digits of the standard
four digit designator indicate the approximate carbon content of the steel in
tenths of a percent. For example, SAE 1020 contains approximately 0.20% carbon
(actually from 0.17% to 0.23%).
Recall that the higher the carbon
content the higher the ultimate tensile strength—and the lower the ductility.
Sometimes a suffix H is attached
to a AISI/SAE number to indicate that the steel has been produced to prescribed
hardenability limits. For example 1541H is a commonly used carbon steel in the
manufacture of axle shafts.
There are a great many different
specific types of carbon steel. The following information, taken from Carroll
Smith's "Engineer to Win" and from the 24th Edition of the Machinery's
Handbook (not the most modern, but the one I happen to own!) covers all or most
of the types that are likely ever to be used by us to make parts from or used
by manufacturers we might buy from.
SAE 1010-1015
This is the most common of the low carbon or mild steels. It is generally available
as hot-rolled or cold-rolled sheet and it is used to form ERW tube in wall thicknesses
below 0.065". Both formability and weldability are excellent. Like all
of the low-carbon steels, 1010-1015 does not respond to heat treatment. Its
strength levels are moderate and it was never intended to be used as a primary
structure—lawn furniture, trailer frames and tooling only!
SAE 1018-1020
This is a very popular grade of low-carbon structural steel. It is available
as hot-rolled or cold-finished bar, as ERW tube in wall thicknesses of 0.063"
and up, as cold-drawn-seamless and DOM tube. It welds and forms very well and,
while it does not respond to heat treatment, it can be case hardened by carburizing.
I use it for just about everything other than suspension links— usually
as DOM round tube or as cold-rolled sheet.
SAE 1025
This is the best of the low carbon steels. To the best of my knowledge it is
now available only as seamless round tube—and that rarely. Before 4130
was developed, 1025 was the standard aircraft structural tubing. We don't use
it simply because it is difficult to find and, if a tube fabrication deserves
something better than 1020, it deserves to be made from 4130 and heat treated.[5]
And here's what the 24th edition
of the Machinery's Handbook has to say on the matter:
Carbon Steels,-- SAE steels 1006,
1008, 1010, 1015: These steels are the lowest carbon steels of the plain
carbon type, and are selected where cold formability is the primary requisite
of the user. They are produced both as rimmed and killed steels.
Rimmed steel is used for sheet, strip, rod, and wire where excellent surface
finish or good drawing qualities are required, such a body and fender stock,
hoods, lamps, oil pans, and other deep drawn and formed products. This
steel is also used for cold heading wire for tacks, and rivets and low carbon
wire products. Killed steel (usually aluminium killed or special killed) is
used for difficult stampings, or where non-aging properties are needed.
Killed steels (usually silicon killed) should be used in preference to rimmed
steel for forging or heat treating applications.
These steels have relatively
low tensile values and should not be selected where much strength is desired.
Within the carbon range of the group, strength and hardness will rise with increases
in carbon and/or with cold work, but such increases in strength are at the sacrifice
of ductility or the ability to withstand cold deformation. Where cold
rolled strip is used the proper temper designation should be specified to obtain
the desired properties.
With less than 0.15 carbon, the
steels are susceptible to serious grain growth, causing brittleness, which may
occur as the result of a combination of critical strain (from cold work) followed
by heating to certain elevated temperatures. If cold worked parts formed
from these steels are to be later heated to temperatures in excess of 1100 degrees
F., the user should exercise care to avoid or reduce cold working. When
this condition develops it can be overcome by heating the parts to a temperature
will in excess of the upper critical point, or at least 1750 degrees F.
Steels in this group, being nearly
pure iron or ferritic in structure, do not machine freely and should be avoided
for cut screws and operations requiring broaching or smooth finish on turning.
The machinability of bar, rod and wire products is improved by cold drawing.
Steels in this group are readily welded.
SAE 1016, 1017, 1018, 1019, 1020,
1021, 1022, 1023, 1024, 1025, 1026, 1027, 1030: Steels in this group, due to
the carbon range covered, have increased strength and hardness, and reduced
cold formability compared to the lowest carbon group. For heat treating
purposes they are known as carburizing or case hardening grades. When
uniform response to heat treatment is required, or for forgings, killed steel
is preferred; for other uses, semi-killed or rimmed steel may be indicated,
depending on the combination of properties desired. Rimmed steels can
ordinarily be supplied up to 0.25 carbon.
Selection of one of these steels
for carburizing applications depends on the nature of the part, the properties
desired, and the processing practice preferred. Increases in carbon give
greater core hardiness with a given quench, or permit the use of thicker sections.
Increases in manganese improve the hardenability of both the core and case;
in carbon steels this is the only change in composition that will increase case
hardenability. The higher manganese variants also machine much better.
For carburizing applications SAE 1016, 1018, and 1019 are widely use for
thin sections or water quenched parts. SAE 1022 and 1024 are used for
heavier sections or where oil quenching is desired, and SAE 1024 is sometimes
used for such parts as transmission and rear axle gears. SAE 1027 is used
for parts given a light case to obtain satisfactory core properties without
drastic quenching. SAE 1025 and 1030, while not usually regarded as carburizing
types, are sometimes used in this manner for larger sections or where greater
core hardness is needed.
For cold formed or headed parts
the lowest manganese grades (SAE 1017, 1020, and 1025) offer the best formability
at their carbon level. SAE 1020 is used for fan blades and some frame
members, and SAE 1020 and 1025 are widely used for low strength bolts.
The next higher manganese types (SAE 1018, 1021 and 1026) provide increased
strength.
All of these steels may be readily
welded or brazed by the common commercial methods. SAE 1020 is frequently
used for welded tubing. These steels are used for numerous forged parts,
the lower carbon grades where high strength is not essential. Forgings from
the lower carbon steels usually machine better in the as forged condition without
annealing, or after normalizing. [6]
Some sample uses of 10xx and 15xx
steels, taken from the Machinery's Handbook:
Steel |
Use |
1020 |
Camshafts, Fan Blades, Welded
Tubing, Wrist Pins |
1030 |
Brake Levers, Gear Shift Levers,
Key Stock, Seamless Tubing |
1035 |
Bolts and Screws |
1040 |
Axles, Brake Levers, Camshafts,
Connecting Rods, Carbon Steel Forgings, Studs |
1045 |
Axle Shafts, Crankshafts, Carbon
Steel Forgings, Ring Gears, Spline Shafts |
1060 |
Clutch Disks, Clutch Springs,
Lock Washers, Snap Rings, Valve Springs, Thrust Washers |
1070 |
Clutch Disks, Plow Beams |
1080 |
Agricultural Steel, Plow Discs,
Plow Shares |
1085 |
Clutch Disks, Leaf Springs,
Mower Knives, Bumper bars |
1095 |
Harrow Discs, Harrow Rake Teeth,
Coil Springs |
Adapted from: "Machinery's Handbook"
24th Edition. Erik Oberg, Franklin D. Jones, Holbrook L. Horton, Henry H. Ryffel,
Robert E. Green; Industrial Press Inc., 1992 p.382-4
Alloy Steels
Alloy steels are
steels that have had finite and precise amounts of alloying elements added to
them during their manufacture. Alloying
Elements are chemical elements added for improving the properties of the finished
materials. Some alloying elements are: nickel, chromium, manganese, molybdenum,
vanadium, silicon, copper. Small, precise changes in the exact chemistry
of the steel can change the mechanical properties quite drastically. Generally,
alloying elements are added to steel to maximize some particular mechanical
property(ies). Of course, nothing in life is free, and there is always
a price to pay. The more alloyed a steel is, the narrower it's appropriate
use, as it becomes more and more specialized (narrow in focus) There is
also a trade off in the reduction of other properties: as hardness and strength
go up due to alloying with chromium and molybdenum - ease of welding and ductility
go down, and of course cost goes up - in some cases WAY up.
Steel is considered to be alloy
steel when the maximum of the range given for the content of alloying elements
exceeds one or more defined limits.
Common alloying elements and their
effects are:
Element |
Effect |
Aluminium |
Deoxidizes and restricts grain
growth |
Boron |
Increases hardenability |
Carbon |
Increases hardenability and
strength |
Chromium |
Increases corrosion resistance,
hardenability and wear resistance |
Lead |
Increases machinability |
Manganese |
Increases hardenability and
counteracts brittleness from sulphur |
Molybdenum |
Deepens hardening, raises creep
strength and hot-hardness, enhances corrosion resistance and increases wear
resistance |
Nickel |
Increases strength and toughness |
Phosphorus |
Increases strength, machinability,
and corrosion resistance |
Silicon |
Deoxidizes, helps electrical
and magnetic properties, improves hardness and oxidation resistance |
Titanium |
Forms carbides, reduces hardness
in stainless steels |
Tungsten |
Increases wear resistance and
raises hot strength and hot-hardness |
Vanadium |
Increases hardenability |
Alloy steels are also designated
using a standard four digit numbering system, very similar to that used for
the carbon steels. However, the first two digits indicate the major alloying
element or elements, whereas the last two digits again indicate the approximate
carbon content of the steel in tenths of a percent. For example, SAE 4340 contains
approximately 0.40% carbon. The first two digits of an alloy steel's designation
indicate the alloying elements and their percentages as follows:
13xx - Manganese-1.75 %
40xx - Molybdenum-0.20% or 0.25%
41xx - Chromium-0.50%, 0.80% OR 0.95% PLUS Molybdenum 0.25%
43xx - Nickel-1.83% PLUS Chromium 0.50% or 0.80% PLUS Molybdenum 0.25%
44xx - Molybdenum-0.53 %
46xx - Nickel-0.85% or 1.83% PLUS Molybdenum 0.20% or 0.25%
61xx - Chromium-0.60% or 0.95% PLUS Vanadium 0.13% or 0.15%
86xx - Nickel-0.55 % PLUS Chromium 0.50% PLUS Molybdenum 0.20%
87xx - Nickel-0.55% PLUS Chromium 0.50% PLUS Molybdenum 0.25%
88xx - Nickel-0.55% PLUS Chromium 0.50% PLUS Molybdenum 0.35%
92xx - Silicon-2.00%
Note that the hugely popular designation
"Chrom-moly" steel has nothing to do with the shiny stuff on bumpers
and hubcaps, but is in fact a reference to the fact that the steel in question
has major alloying elements of Chromium and Molybdenum. That's why I prefer
to write the abbreviation as Chrom-Moly, without the "e" on chrome.
It is also popularly abbreviated as Cr-Mo, Cro-Mo, etc. Note that 41xx and 43xx
alloy steels can and frequently ARE both refereed to as "Chrom-Moly Steel",
though obviously the 43xx also has significant Nickel added.
Some characteristically enlightening,
if rather opinionated, insight from my hero on the most common/popular alloy
steels follows:
SAE 4130
Best known of the family of CHROME-MOLY steels, 4130 is often considered, in
racing circles, to be the ideal steel for all high-strength/high-stress applications.
IT IS NOT! In thin sections (that is, in tube or sheet form) its unique combination
of excellent tensile strength, toughness and response to mild heat treatment
combined with its good formability in the annealed condition and its outstanding
welding characteristics make it virtually unbeatable for fabrications subject
to high stress levels. It is critical that all welds be stress relieved. I prefer
the use of OXWELD 32 CMS welding rod with 4130 for the simple reason that it
both normalizes and heat treats well in conjunction with 4130. Many welders
prefer to use a stainless rod, but the high nickel content of stainless welding
rods means that the weldment will not respond well to heat treatment. Since
I believe that not heat treating 4130 fabrications is DUMB (if you don't heat
treat you end up with an expensive part with the same strength as 1020—and
brittle weld areas). Smith's law says to use the heat-treatable rod for EVERYTHING.
I heat treat 4130 fabrications to Rock-well C Scale 26 to 30 and no higher.
This results in an ultimate tensile strength of about 130,000 psi with sufficient
ductility that I do not have to worry about brittle parts. The other side of
the 4130 coin, often unknown to (or at least unappreciated by) the racer, is
that it possesses poor deep-heat-treating characteristics and has an inborn
dislike of varying cross-sections. These characteristics make 4130 a poor choice
for machined or forged parts—it doesn't forge very well anyway. It also
doesn't machine very well, at least in the normalized condition—too gummy.
Those people who make hubs, steering knuckles and the like from 4130 are kidding
themselves—and their customers. It doesn't make very good shafts, either,
as in drive shaft, or axle, or torsion bar.
SAE 4140
This is a deep hardening chrome-moly steel with excellent impact resistance,
fatigue strength and general all-around toughness. It is commonly used for small-aircraft
forgings. I use it in bar form for all of the little gub-bins and small parts
that we are always machining. It doesn't weld as well as 4130 but it does weld
satisfactorily. Welded to 4130 tube or sheet, with Oxweld 32 rod, a 4140 machined
component can be heat treated to the same spec as 4130.
SAE 4340
This is the nickel-chrome-moly deep-hardening steel that we SHOULD use, in its
vacuum-melted configuration, for our hub forgings, drive shafts, axles and the
like. Its tensile strength, toughness, fatigue resistance, excellent deep-heat-treating
characteristics and very high tolerance of stress reversals (which is just another
way of saying that it has excellent fatigue resistance) make it just about unbeatable.
It is also weldable (with care and a lot of pre-and post-heat) and eminently
forgeable. In use it should be heat treated to the 180,000—200,000 psi
range, maximum—although it can be taken to 220,000 psi without significant
loss of toughness. The hardness range between Rockwell C Scale 46 and 48 should
be avoided with this steel as it becomes brittle in this range.
SAE 4340 MODIFIED (300M)
This is, as you would expect, very similar to 4340... The addition of a trace
of vanadium and an increase in the silicon level (while they have no notable
effect on the hardness, strengths, or ductility of the resultant alloy) work
miracles in the toughness and resistance to fatigue, producing a steel which,
in the 270,000 to 300,000 psi range, is the toughest, most impact resistant
and most fatigue resistant of the usually available steels. Unfortunately, even
in the normalized condition, it is a bear to machine. Reducing the hardness
by reducing the level of heat treatment or by tempering has the curious effect
of reducing the tensile strength WITHOUT increasing the ductility or toughness.
The most common use of this outstanding steel, also known as 300M, is for military
and commercial aircraft landing gear. We use it for hubs, for drive shafts,
axles and torsion bars—when we can afford it (or when we cannot afford
NOT to use it). At its normal, heat-treated hardness level of Rockwell C 52/56
it is hard enough that we can and do run roller bearings directly on its surface.
While the material is great, the heat treating is tricky. There is a very real
danger of surface decarburization which can only be avoided by copper plating
prior to heat treat. The ONLY heat treat specification for 300M is MIL H 6875,
but there are tricks to every trade. MIL H 6875 calls out a two-hour quench
at 575 degrees F. Doubling the quench time to four hours will notably increase
the ductility and fatigue resistance of the finished product. Another trick
is to absolutely forbid the heat treat shop to perform Rockwell or Brinell hardness
tests on the actual part, supply a "test coupon" of the same material
and cross-section wired to each part and insist that the coupon be heat treated
along with the part and that all hardness tests be done on the test coupon.
This is a good idea with ALL parts heat treated much above Rockwell C 40.
THE HIGH SILICON, NICKEL CHROME
STEELS
These are usually known by trade names such as Hi-Tuff and Stress Proof. They
contain up to about 3 % silicon and are, as the names suggest, tough as hell.
They are popular for stock car and off-road racing axles—and the alloys
are very suitable for these applications. They are not as good as 4340 M or
even 4340, but they are also a damned sight cheaper and, especially where the
minimum weights imposed are high, the fact that a part with the same strength
and fatigue resistance can be made lighter by using a better steel may be a
lot less significant than the cost difference. However, these steels are tough
only because of the high silicon content, which is mainly in the form of longitudinal
fibers or strings of silicon. This limits the efficient (and safe) use of the
alloys to parts with minimal section changes and virtually no transverse machining
(we don't want to cut the longitudinal strings that make the stuff tough to
start with, do we?). They also don't like being bent very much because that
may rupture the silicon strings. Mind you, I have made a lot of street car antiroll
bars from Stress Proof with excellent results and pretty severe bends—but
in this case the bends are almost, by definition, in lightly stressed areas.[7]
Mechanical
Properties
The following tables
illustrate mechanical properties of various different types of steels of varying
types - from hot rolled 1020 to cold finished 4340 chrom-moly alloy steel.
They are taken from a variety of sources[8]. In addition to the actual
specific numbers / data they contain, I believe they clearly illustrate some
key concepts:
|
|
|
Ultimate Strength |
|
Modulus Of Elasticity |
|
|
|
Material |
Type |
Condition / Treatment |
Tension (psi), T |
Compression % of T |
Shear % of T |
Yield Point (psi) |
In Tension, E (millions of psi) |
In Shear, % of E |
% Elongation |
Reduction of Area %) |
Impact Strength (Izod) ft-lb |
|
|
|
|
|
|
|
|
|
|
|
|
Gray Iron |
Class 20 |
Class 20 |
20,000 |
360-440 % |
160% |
|
11.6 |
40% |
|
|
|
|
Class 40 |
Class 40 |
40,000 |
310-340% |
140% |
|
17 |
40% |
|
|
|
|
Class 60 |
Class 60 |
60,000 |
280% |
100% |
|
19.9 |
40% |
|
|
|
Malleable Iron |
|
|
40-100,000 |
|
|
30-80,000 |
25 |
43% |
|
|
|
Nodular (ductile) Iron |
|
|
60-120,000 |
|
|
40-90,000 |
23 |
|
|
|
|
|
|
|
|
|
|
|
|
|
|
|
|
Cast Steel |
Carbon |
|
60-100,000 |
100% |
75% |
30-70,000 |
30 |
38% |
|
|
|
|
Low Alloy |
|
70-200,000 |
100% |
75% |
45-170,000 |
30 |
38% |
|
|
|
|
|
|
|
|
|
|
|
|
|
|
|
Magnesium |
|
|
37-55,000 |
|
19-27,000 |
26-44,000 |
6.5 |
|
|
|
|
|
|
|
|
|
|
|
|
|
|
|
|
Carbon Filament |
|
|
280,000 |
|
|
|
110 |
|
|
|
|
|
|
|
|
|
|
|
|
|
|
|
|
Aluminium |
6061-T6 |
|
48,000 |
|
34,000 |
40,000 |
10.5 |
|
|
|
|
|
2024-T3 |
|
65,000 |
|
34,000 |
59,000 |
10.5 |
|
|
|
|
|
7075-T6 |
|
83,000 |
|
48,000 |
73,000 |
10.5 |
|
|
|
|
|
|
|
|
|
|
|
|
|
|
|
|
Titanium |
|
|
50-135,000 |
|
|
40-120,000 |
15-16.5 |
|
|
|
|
|
|
|
|
|
|
|
|
|
|
|
|
Steel |
ASTM A-53 pipe |
Grade A |
48,000 |
100% |
75% |
30,000 |
30 |
38% |
|
|
|
|
Grade B |
60,000 |
100% |
75% |
35,000 |
30 |
38% |
|
|
|
|
|
|
|
|
|
|
|
|
|
|
|
|
1020 |
Cold Drawn Bar |
82,000 |
100% |
75% |
70,000 |
30 |
38% |
20% |
65% |
|
|
1020 |
Hot Rolled Bar |
69,000 |
100% |
75% |
40,000 |
30 |
38% |
38% |
52% |
|
|
1020 |
Normalized (1600°F) |
64,000 |
100% |
75% |
50,250 |
30 |
38% |
36% |
68% |
86.8 |
|
1020 |
Annealed (1600°F) |
57,000 |
100% |
75% |
42,750 |
30 |
38% |
37% |
66% |
91 |
|
1030 |
Quenched & Tempered (400°F) |
123,000 |
100% |
75% |
94,000 |
30 |
38% |
17% |
47% |
|
|
1030 |
Quenched & Tempered (800°F) |
106,000 |
100% |
75% |
84,000 |
30 |
38% |
23% |
60% |
|
|
1030 |
Quenched & Tempered (1200°F) |
85,000 |
100% |
75% |
64,000 |
30 |
38% |
32% |
70% |
|
|
|
|
|
|
|
|
|
|
|
|
|
|
1025 (low carbon) |
|
60-103,000 |
100% |
75% |
40-90,000 |
30 |
38% |
|
|
|
|
|
|
|
|
|
|
|
|
|
|
|
|
1045 (medium carbon) |
|
80-182,000 |
100% |
75% |
50-162,000 |
30 |
38% |
|
|
|
|
|
|
|
|
|
|
|
|
|
|
|
|
1095 (high carbon) |
|
90-213,000 |
100% |
75% |
20-150,000 |
30 |
38% |
|
|
|
|
1095 (high carbon) |
As-Rolled |
140,000 |
100% |
75% |
83,000 |
30 |
38% |
9% |
18% |
3 |
|
1095 (high carbon) |
Normalized (1650°F) |
147,000 |
100% |
75% |
72,500 |
30 |
38% |
10% |
>14% |
4 |
|
1095 (high carbon) |
Annealed (1450°F) |
95,250 |
100% |
75% |
55,000 |
30 |
38% |
13% |
21% |
2 |
|
1095 |
Quenched & Tempered (400°F) |
216,000 |
100% |
75% |
152,000 |
30 |
38% |
10% |
31% |
|
|
1095 |
Quenched & Tempered (800°F) |
199,000 |
100% |
75% |
139,000 |
30 |
38% |
13% |
45% |
|
|
1095 |
Quenched & Tempered (1200°F) |
122,000 |
100% |
75% |
85,000 |
30 |
38% |
20% |
47% |
|
|
|
|
|
|
|
|
|
|
|
|
|
|
4130 |
RC-30 |
136000 (81-179,000) |
100% |
75% |
(46-161,000) |
30 |
38% |
|
|
|
|
4130 |
Normalized (1600°F) |
97,000 |
100% |
75% |
63,250 |
30 |
38% |
26% |
60% |
63.7 |
|
4130 |
Annealed (1585°F) |
81,250 |
100% |
75% |
52,250 |
30 |
38% |
28% |
56% |
45.5 |
|
4130 |
Hot Rolled & Annealed Bar |
86,000 |
100% |
75% |
56,000 |
30 |
38% |
29% |
57% |
|
|
4130 |
Hot worked & Annealed Tube |
85,000 |
100% |
75% |
65,000 |
30 |
38% |
20% |
|
|
|
4130 |
Cold Drawn & Normalized Bar |
98,000 |
100% |
75% |
87,000 |
30 |
38% |
21% |
52% |
|
|
4130 |
Cold Worked & Normalized |
95,000 |
100% |
75% |
>75,000 |
30 |
38% |
15% |
|
|
|
4130 |
Water quenched @ 1550°F Tempered at 1000 1000°F |
146,000 |
100% |
75% |
133,000 |
30 |
38% |
17% |
50% |
|
|
|
|
|
|
|
|
|
|
|
|
|
|
4340 |
RC-44 |
208000 (109-220,000) |
100% |
75% |
(68-200,000) |
30 |
38% |
|
|
|
|
4340 |
Normalized (1600°F) |
185,500 |
100% |
75% |
125,000 |
30 |
38% |
12% |
36% |
11.7 |
|
4340 |
Annealed (1490°F) |
108,000 |
100% |
75% |
68,500 |
30 |
38% |
22% |
50% |
37.7 |
|
4340 |
Hot Rolled & Annealed Bar |
101,000 |
100% |
75% |
69,000 |
30 |
38% |
21% |
45% |
|
|
4340 |
Cold Drawn & Normalized Bar |
111,000 |
100% |
75% |
74,000 |
30 |
38% |
18% |
42% |
|
|
4340 |
Oil quenched @ 1550°F Tempered at 1000°F Bar |
182,000 |
100% |
75% |
162,000 |
30 |
38% |
15% |
40% |
|
|
4340 |
Quenched & Tempered (400°F) |
272,000 |
100% |
75% |
243,000 |
30 |
38% |
10% |
38% |
|
|
4340 |
Quenched & Tempered (800°F) |
213,000 |
100% |
75% |
198,000 |
30 |
38% |
10% |
44% |
|
|
4340 |
Quenched & Tempered (1200°F) |
140,000 |
100% |
75% |
124,000 |
30 |
38% |
19% |
60% |
|
|
|
|
|
|
|
|
|
|
|
|
|
|
300M (4340M) |
RC-52 |
270,000 |
100% |
75% |
|
30 |
38% |
|
|
|
|
|
|
|
|
|
|
|
|
|
|
|
|
8630 |
Normalized (1600°F) |
94,250 |
100% |
75% |
62,250 |
30 |
38% |
24% |
54% |
69.8 |
|
8630 |
Annealed (1550°F) |
81,750 |
100% |
75% |
54,000 |
30 |
38% |
29% |
59% |
70.2 |
|
8630 |
Quenched & Tempered (400°F) |
238,000 |
100% |
75% |
218,000 |
30 |
38% |
9% |
38% |
|
|
8630 |
Quenched & Tempered (800°F) |
185,000 |
100% |
75% |
170,000 |
30 |
38% |
13% |
47% |
|
|
8630 |
Quenched & Tempered (1200°F) |
112,000 |
100% |
75% |
100,000 |
30 |
38% |
<
23% |
63% |
|
- Note the various
discrepancies - not all sources agree precisely on "the numbers".
This is due to a variety of reasons - from differing test or calculation methods
to the inerrant difficulty and imprecise repeatability of methods used to
gather the data. The important point is - use the numbers for comparisons
and as a guide. Actual design calculations should best me made using
certified data from the specific supplier of the exact product to be used
(i.e. the steel producer themselves) or a recognized standards organization
such as the ASTM. Not only that - but this point clearly illustrates
the folly of "designing to the limit" and demonstrates why engineers
are trained to use "design factors" (used to be called safety factors
in the past) of anywhere from 2 to 10 or more when making calculations.
- Note the general
differences between the types of steel - from the mild, low carbon steels
(e.g. 1020) to the high carbon, alloy steels (e.g. 4340 etc)
- Note also the
(sometimes dramatically) different properties between different types (conditions)
of the same steel - for example, between the hot rolled, normalized, annealed,
and various tempered variants of the same steel.
- Note that, even
without a stress/strain diagram we can tell something about a steel by looking
at the difference between yield and ultimate tensile strengths. For
example - the tensile strength of normalized 1020 is 64,000 psi or 27% greater
than its 50,250 psi yield strength; whereas the tensile strength of normalized
4340 is 185,500 psi or 48% greater than its 125,500 psi yield strength!
Section
5 - Steel Production
How Steel
is made into the useful products we need.
Recall that steel is produced from
pig iron in a specialized furnace of a steel mill. This steel is produced
in one of three special forms, known as slabs, blooms, or billets - each of
which has an industry defined standard shape and size and which will be made
into different useful products. Slabs eventually become steel plate, sheet
metal or tubing. Blooms become something called "structural shapes"
which we know as angle-iron, I-beams, etc. The last product is a billet,
which is used to make solid steel bars and wire. Note that this is the correct
use of the term "billet" - though we commonly misuse the term as either
a noun meaning "any solid piece of metal from which we usually machine
a part" or as an adjective meaning "a part machined from a single
solid piece", as in "Look at my billet steering arms."
Whichever the particular shape that
is started with or the finished product that is desired, the essential process
is the same. The raw steel shape is turned into a useful steel product
by one or more of various mechanical means - the raw steel is either pressed,
rolled, formed, stamped, forged, or extruded into the final product. Each of
these methods can be conducted at temperatures close to room temperatures (cold
working) or at much higher temperatures, up to where the steel is nearly molten
(hot working), or some combination thereof (for example, a particular steel
product could be hot forged and then cold-finished. Carroll Smith explains
the process further:
"In the process, the physical
characteristics of the metal are improved by breaking up the "as cast"
crystal structure and "refinement" of the grain size...The yield strengths
of almost all metals decrease notably with increasing temperature, so that a
given amount of deformation can be achieved at much lower stress levels if the
material is hot worked rather than cold worked. ..Almost all of the energy expended
in the hot working of metals is dissipated as heat, leaving the metal's crystal
structure largely unaffected and the metal ductile. On the other hand, while
most of the energy expended in the cold working of a metal is also dissipated
in the form of heat, some part of this energy remains within the crystal structure
of the metal itself as "strain energy" in the form of various distortions
of and dislocations in the crystal space lattice. Therefore, cold working, by
decreasing the grain size and increasing the number of dislocations in the crystal
lattice of the metal being worked, can increase the strength and hardness of
the finished product—sometimes to a notable extent—at some cost
in ductility...As you would expect, the different mill forming processes result
in steel mill products of varying qualities and properties:"
TUBE AND PIPE
Seamed tubing and pipe are roll formed from strips of sheet or plate and then
welded. Seamless tubing (and pipe, which is merely tubing with thick walls intended
primarily for the conveyance of liquids), on the other hand is pierced by a
pointed mandrel while being fed by angled rollers and then either hot or cold
finished.
STRUCTURAL SHAPES
Structural shapes—angles, zees, I-beams and the like— are hot rolled
through progressive grooved rollers.
STEEL PLATE and SHEET
Steel sheet and strip are produced by progressively reducing a slab to the desired
final thickness through hot-rolling mills. The better grades of steel sheet
are hot rolled only to an approximation of final thickness and then cold rolled
to final dimensions. Annealing and/or other thermal treatments before, during
and after rolling are carefully controlled to produce a specified quality of
finished sheet. Plate (sheet more than 1/4" thick) is produced in the same
way.
BAR AND ROD STOCK-WIRE
Bar stock, rod, angles, I-beams and other shapes are also rolled to specified
dimensions through progressive hot shaped rollers. Again, the higher grades
are hot rolled only to approximate size and are cold drawn through hardened
dies to their final dimensions. Hot-rolled round bar stock is also extruded,
under unthinkable pressure, into wire. Special "tube rounds" are hot
rolled and then used in the production of seamless pipe and tube. [9]
What's the difference to us, between
hot and cold?
Depending on the exact product (tube,
pipe, flat bar, plate steel, etc) the type of steel (mild, high carbon, alloy
etc) and the manufacturer - MOST steel products we might use are available as
either hot rolled, cold rolled, or hot rolled and cold finished. The difference
is:
- Cold rolled or cold finished products
are stronger - sometimes significantly so (up to 100% stronger (greater yield
strength) - because of the improvement in the crystal lattice structure from
improved grain size, shape, and orientation)
- Cold rolled or finished products
are straighter, have a much smoother and uniform surface finish, and are made
to much closer, more consistant dimensions
- Hot rolled products are more malleable
and therefore easier to form
- Hot rolled products are supplied
covered with scale, and are not as uniform in dimension as cold rolled
Steel Tubing
It is impossible to go into details
about every type and shape and grade of steel product available or that we might
be interested in. There are far too many, and availability will vary greatly
depending on location and manufacturer/supplier.
That said, one of the most often
used, most often asked about, and most often misunderstood products we use is
the venerable round steel tubing.
Round steel tube is commonly available
in a number of industry standard sizes. For an idea of the common industry
sizes (inside diameter (ID), outside diameter (OD), and wall thickness) browse
the supply catalogue of your local supplier. My local supplier is Loucon Steel, and they have an excellent 70-page catalogue that lists all the commonly available dimensions for round, square, rectangular, plate, channel, I-beam, and sheet steel.
Note that round steel mechanical
tubing is NORMALLY ordered and supplied based on a specified OD and wall thickness.
The ID is the result of these former 2 specs. There are however some exceptions
to this - most notably in true seamless tubing.
Here are some Flash™ graphics
of the different steel tube forming processes that I snagged from the excellent Steel Tube Institute of North America
website.
Contnuous
(butt welded) pipe process.
The continuous process produces a full range of pipe sizes from only a few different
widths of skelp. The coils of skelp, or strip, are fed into the mill and their
ends welded together to provide a continuous flow. The strip passes through
a pre-heater and into a furnace. The heated strip is shaped into an arc of about
270° in a forming stand before passing into the welding stand. There a nozzle
applies oxygen to the edges to further heat them as they are pressed and welded
together. The pipe's OD and wall thickness are reduced in a stretch-reducing
mill. Pipe is then cut to length, reduced to the required size in a sizing mill
and water-cooled before being straightened. It is then ready for finishing
Typical
Electric Resistance Welded tube process
Steel strip is unwound from coils and side-trimmed to control width and condition
the edges for welding. The strip then passes through a series of contoured rolls
which progressively cold-form it into a circular shape. The edges are forced
together under pressure and welded by heating the steel to temperatures between
2200° F and 2600° F using copper contacts or coil induction. Weld flash
is removed from the the inside and outside surfaces of the newly-formed pipe,
and the weld zone is heat treated to ensure homogeneity between the base metal
and weld. The weld is subjected to in-line nondestructive testing, and the tube
then passes through a series of sizing rolls to attain its precise finished
diameter. It is then straightened and cut to the desired finished length.
DOM
tube being constructed, starting as ERW and then being drawn over a mandrel.
The manufacturing process for DOM tubing begins with coils of steel, which are
slit to the proper width for the desired tube size. The strip is cold formed
and passed through an electric resistance welder which joins the edges together,
under pressure, to complete the tubular shape. After testing the weld's integrity,
the tubing is cut to length for further processing
Seamless
tube construction
The production process for seamless tube begins by heating a steel billet to
about 2250° F. The red-hot billet is rotated and drawn by rolls over a piercing
rod, or mandrel. The action of the rolls causes the metal to flow over and about
the mandrel to create a hollow tube shell. After reheating, the shell is moved
forward over a support bar and is hot-rolled in several reducing/sizing stands
to the desired wall thickness and diameter. The tube, which has grown significantly
in length during the piercing and sizing processes, is then cut into sections
and conveyed across a cooling bed to cool slowly in the air. It then receives
whatever finishing processes are needed to meet customer requirements.
Steel tubing is usually supplied
in one of the following forms:
Seamless Tube.
This is expensive and specialized stuff. It IS NOT the commonly
used (and misreferenced) DOM tubing, as DOM tubing does indeed have a seam (albeit,
almost invisible - more details below). True seamless tubing is uncommon
in motorsports and automotive use. It is seamless because it is manufactured by
a process know as "extrusion" where a solid bar of steel is
pierced down the center with a die, at unthinkable pressures, to form a tube.
The process looks similar to how hollow pasta (macaroni etc) is made.
There are 2 sub-types of seamless tube:
Cold Drawn Seamless (CDS)
Tube is normally drawn to O.D. and I.D. dimensions and produced to
standard dimensional tolerances (this differs from most other types of tubing
except DOM) . It is normally made from SAE 1018 and is considered good quality.
Hot Finished Seamless (HFS) Tube is lower in cost than cold
drawn and most applicable where precise dimensions and surface quality are
of secondary importance. It is manufactured to O.D. and wall dimensions from
SAE 1026 steel and is scaly, less dependable and not as strong as cold drawn
tube.
Electric Resistance Welded
(ERW) Tube
ERW is the most economical and readily available type of mechanical tuning.
It is produced by taking a flat bar of steel and rolling it into a tube shape
(picture rolling up a newspaper - but without any overlap) and then welding
the seam - by, you guessed it - electric resistance - hence the name.
Electric resistance welding is somewhat like a long, continuous spot weld.
It's often computer controlled and extremely consistent. ERW is normally
SAE 1010 (for wall thickness < 16 ga) or SAE 1020. ERW tube comes in 2 flavours:
Hot Rolled ERW (HREW)
HREW is rolled into a tube at elevated temperatures, usually way above room
temperature. This produces a tubing that is more malleable and therefore
easier to form but that is also not as strong, is supplied covered with scale,
and not as uniform in dimension as cold rolled. It is also quite a bit
cheaper than cold rolled.
Cold Rolled ERW (CREW)
CREW is manufactured by a process in which a steel bar is rolled into a tube
and the seam welded, usually at room temperature. Compared to hot rolled,
CREW is stronger - (greater yield strength) - because of the improvement in
the crystal lattice structure from improved grain size, shape, and orientation
imparted by being worked at cold (room) temperatures), straighter, has a much
smoother and more uniform surface finish, and is made to much tighter, more
consistent dimensions. It is the best economical choice for tube work,
and because of the better surface finish and tighter dimensional tolerances
it is much nicer to work with than HREW.
Drawn Over Mandrel (DOM)
Strong and well-finished DOM is an electric resistance welded tube tested for
soundness of weld and drawn through a die and over a mandrel. This process imparts
significantly improved mechanical properties to the tube, due to the cold working
process. It is considered a high quality tube, and is normally constructed
from SAE 1020 or 1026 steel. Note that, technically DOM refers to the
process by which the tube is finished after having started as an ERW tube.
Technically, DOM is not a type of steel tube, but rather a process. As
so often happen though - in common use the term has become accepted to mean
a specific type of tubing rather than a process. In this case, when people say
"DOM" they normally mean an ERW tube drawn over a mandrel at (close
to) room temperature and made from SAE 1020 steel. It is normally drawn to O.D.
and I.D. dimensions. Here is what the Steel Tube Institute of North America
has to say about DOM:
The DOM Manufacturing
Process
The manufacturing process for
DOM tubing begins with coils of steel, which are slit to the proper width
for the desired tube size. The strip is cold formed and passed through an
electric resistance welder which joins the edges together, under pressure,
to complete the tubular shape. After testing the weld's integrity, the tubing
is cut to length for further processing.
The cold-drawing process creates
a uniform, precision product with substantially improved tolerances, surface
finish and tensile strength, increased hardness and good machinability. In
this process, the tube is cleaned and annealed, and one end of each length
is squeezed to a point so it can be gripped by the drawing mechanism. The
tube is then drawn through one or more dies and over mandrels. This reduces
the diameter of the tube and thins its walls to the required dimensions in
a controlled fashion to provide the qualities desired in the finished product.
Metallurgically, drawing improves the tube's concentricity, tensile strength,
hardness and machinability. Close dimensional accuracy is achieved through
tight control of both outside and inside diameters.[10]
Alloy Steel Tubing
Is not really a different type of tubing, as it will be manufactured
by one of the above described methods, usually by extrusion, but from alloy
steel instead of mild steel. It is generally available in either the normalized
or the annealed condition. Commonly referred to as chrom-moly tube - it
has very strict welding process and post-welding heat treatment and stress relieving
requirements. It is my opinion that it can (should) only be TIG or Oxy-Acetylene
welded, and then only if proper stress relieving will be done post welding.
Sure people MIG weld it all the time, and you can safely do so - BUT - what
you have in the end is a superior tube with an inferior weld joint which reduces
the overall strength of whatever you fabricated to the weakest link (the weld
in this case) and so you have a very expensive structure that is no better overall
than one made from 1020 DOM.
Exact chemical content, heat treatment,
physical properties, production method and therefore mechanical properties will
vary from one supplier to the next, even for seemingly similarly named products
- the wise fabricator double-checks all assumptions carefully before building
anything. Different suppliers will also have available different products.
For example, Ryerson, one of North America's largest suppliers list in
their catalogue of steel tubing between 1" and 2' OD, the following types
(not all available in all sizes):
CDS, HFS, DOM, ERW, and a proprietary
product they call "Ry-Star 512 Extra".
Many suppliers will have such special
proprietary products - you will have to check with your supplier for its proprietary
product properties and specs.
One thing that has to be watched
out for is that the industry bends a lot of carbon steel tubing to make lots
of things and so most carbon steel tubing is available in the annealed condition—woe
to him who does not detect it before he builds the part. I have a very good
friend who once got an entire roll cage cut, bent, fitted and tacked before
he realized that his merry men were working with annealed boiler tube. The other
thing that we don't want is "free machining tubing." I currently use
round carbon steel DOM mechanical tubing for most things other than suspension
links (there I use E4130N and stress relieve and heat treat after welding).
For roll cages I use either 4130 or DOM 1020. I do not want to know about hot-finished
tubing because I do not want to clean it. I am old enough to remember the days
when English ERW tubing was liable to split along the weld seam. As a matter
of principle (or, possibly, stubbornness) I do not use ERW or butt welded tube
on the race car; although, since it is a lot cheaper, I use it all over the
trailer and the shop.[11]
My personal mantra on the subject
of steel tubing choice for custom fabrication projects is:
"You can't go wrong
with 1020 DOM!"
Heat
Treating
Heat treating and hardness - Two
terns you hear A LOT, and so you should, for they are a critical part of the
puzzle. In fact, when determining a materials suitability for any given
task or part, heat treating itself is probably THE MOST SIGNIFICANT factor.
It goes hand-in-hand with the type of material. In fact, very often, the more
exotic and expensive alloys steels are "stronger" or "better"
because they can be heat treated and hardened more thoroughly or deeper.
In other words, chrom-moly steel is not just a product with wondrous properties
- it's also a steel with certain alloying elements added to it that allows it
to be hardened , and therefore made much stronger and more wear resistant, than
other steels.
The trouble is - the topic of Heat
Treating is HUGE, and quite complicated.....it involves physics, chemistry,
math - all the fun Saturday night subjects :-) There is no possible way
I can even scratch the surface in an article of this scope - but I can drop
a little knowledge in the bucket of your collective minds, so that at least
you will have a passing idea when you see or hear the terms, so that you may
at least be able to ask intelligent questions, and so that you will have a place
from which to start more detailed research if you need to.
Let's start with the definitions
of the often seen, and often (erroneously) interchanged terms Hardness and Heat
Treating.
Heat Treatment
An operation or combination of operations involving the heating and cooling
of a metal in the solid state for the purpose of obtaining certain desirable
conditions or change in properties or metallurgical structure. Heat treating
operations include annealing, normalizing, quenching and tempering, etc.
Hardness
The ability of a metal to resist penetration, defined in terms of the
measurement (Brinell, Rockwell,Scleroscope, Vickers, Knoop etc.) Normally,
the hardness of steel varies in direct proportion to its strength –
the harder it is, the stronger it is, and vice-versa.
Hardenability
This relates to the ability of steel to harden deeply upon quenching and
takes into consideration the size of the part, the method of quenching
and the analysis and grain size of the steel. Carbon steels are considered
as shallow hardening and various alloy and tool steel grades are considered
deep hardening or through hardening.
Hardening
Increasing the hardness by suitable heat treatment, usually involving
heating and cooling. When applicable, the following more specific terms
should be used: age hardening, case hardening, flame hardening, induction
hardening, precipitation hardening, and quench hardening. |
Now, recall from the beginning of
the article that we said:
"You can see how there is a
trade-off between a metal’s malleability/ductility and its hardness/strength
(which makes perfect logical sense – since malleability is the ease with
which we can form it, by applying force, and strength is its ability to resist
force). There are a whole group of people employed in a field called “physical
metallurgy” whose job it is to figure out how to use things like alloying,
heat treatment, and cold-working to skew this relationship (malleability/strength)
in our favour, so that hopefully we can develop materials that are both strong
and malleable."
Heat treating is the bread and butter
of the physical metallurgist, it's probably the most important aspect of optimizing
a steels properties for the job you want it to do, and it's effects can be enormous
(for better or worse.)
So, we harden steel parts to make
them "stronger", to make them better able to resist penetration and
carry the loads imposed on them. We do so by heating them to very specific
temperatures, holding them at those temperatures for very specific amounts of
time (called "soaking") and then cooling them at very specific rates,
sometimes quickly, sometimes in steps, and sometimes very slowly. Thus, the
hardening of a steel is an operation achieved through heat treatment.
There are other reasons for heat
treating as well, for example; to relieve stress. Stress relieving is
process used to reduce internal residual stresses in a metal object by heating
the object to a suitable temperature and holding for a proper time at that temperature.
This treatment may be applied to relieve stresses induced by casting, quenching,
normalizing, machining, cold working, or welding.
So, I can't possible tell you how
to heat treat steel here, but I can tell you a few important facts to keep in
mind.
- Different methods of heat treating
or hardening achieve different results. For example, an axle shaft that is
"induction hardened" has a hard outer layer and a softer, more malleable
inner core; compared to a shaft that is "through hardened" which
will be hard all the way through. This in turn leads to the shafts having
different properties.
- Different heat treating methods
work more, or less, effectively with different steels and alloy steels. For
example, you cannot "through harden" 1541 steel axle shafts, and
although you CAN induction harden 4340 cr-mo alloy steel, to do so without
ALSO through hardening it would be a great waste, as the beauty (and strength)
of 4340 lies in it's ability to accept a deep through hardening. In many cases
there is a narrow range of acceptable matching alloys and heat treating methods
- matching them to get the best properties possible in the part is an exact
science.
- Heat treating is generally expensive,
time consuming, and complicated. It produces much better parts, and
you have to pay for it. The very best treatments are achieved through
multiple steps - for example: an axle shaft that is through hardened and then
induction hardened. Very few companies do this, and those that do produce
a superior product - and will charge you for it.
- Heat treating, even if you know
what you're doing can be difficult and temperamental. Done incorrectly
or under poor control it can ruin expensive parts or produce inferior parts.
To illustrate the effect of hardening,
look at this table, taken from "Engineer To Win". Note, for example,
the difference between 4340 at Rockwell C 22 and 4340 at Rockwell C 44!
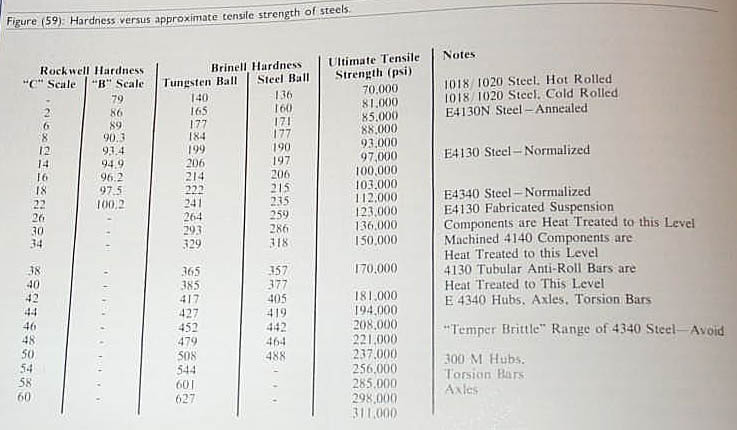
I will leave the topic here by repeating
the golden rule of heat treatment, and the providing a table of some more heat
treatment terms:
"Heat treatment is the
key to a steel parts strength and suitability - but it must be: matched carefully
to the alloy, precisely selected for the desired results (properties achieved),
and controlled carefully by an expert"
AIR HARDENING STEEL -An
alloy steel which does not require quenching from a high temperature to
harden but which is hardened by simply cooling in air from above its critical
temperature range.
ANNEALING - Applies normally
to softening by changing the microstructure and is a term used to describe
the heating and cooling cycle of metals in the solid state. The term annealing
usually implies relatively slow cooling in carbon and alloy steels. The
more important purposes for which steel is annealed are as follows: To
remove stresses; to induce softness; to alter ductility, toughness, or
electric, magnetic or other physical and mechanical properties; to change
the crystalline structure; and to produce a definite microstructure.
AUSTEMPERING - This is a method
of hardening steel by quenching from the austenitizing temperature into
a heat extracting medium (usually salt) which is maintained at some constant
temperature level between 400” and 800” and holding the steel
in this medium until austenite is transformed to bainite. The austempering
process is limited to sections less than `/2” diameter. The advantages
of this method of interrupted quenching are increased ductility and toughness
at the resulting hardness of RC 45-55.
AUSTENITE - The solid solution
of iron and carbon which is attained by heating to high temperatures above
the upper critical temperature. This temperature or temperature range
is called the austenitizing temperature and must be attained to obtain
the proper microstructure and full hardness of steel in heat treating.
The austenitizing temperature varies for the different grades of carbon,
alloy and tool steels.
BAINITE - A decomposition or
transformation product of austenite which is a type of microconstituent
or structure in steel. This term is used by metallurgists to describe
a particular structure of steel when the steel is polished, etched and
examined with a microscope.
BRINELL HARDNESS - A hardness
number determined by applying a 3000 kilogram load to the surface of the
material to be tested through a hardened steel ball of 10mm. The diameter
of the depression is measured and the hardness is the ratio of load to
spherical area of the impression. Tables of numbers have been prepared,
and the hardness is read from the table from the diameter of the depression.
CARBURIZING - Adding carbon
to the surface of steel by heating the metal below its melting point in
contact with carbonaceous solids, liquids, or gases.
CASE HARDENING - A heat treatment
or a combination of heat treatments of surface hardening involving a change
in the composition of the outer layer of an iron-base alloy in which the
surface is made substantially harder by inward diffusion of a gas or liquid
followed by appropriate thermal treatment. Typical hardening processes
are carburizing, cyaniding, carbo-nitriding and nitriding.
CYANIDING - Surface hardening
by carbon and nitrogen absorption of a steel article or a portion of it
by heating at a suitable temperature in contact with cyanide salt, followed
by quenching.
DECARBURIZATION - When steel
is subjected to high temperatures, such as are used in hot rolling, forging,
and heat treating in a media containing air, oxygen, or hydrogen there
is a loss of carbon at the surface which is known as decarburization.
This resultant loss of carbon or chemistry change at the surface of the
steel part reduces the strength of the part by reducing the size of the
section and produces a softer surface hardness than the core of the part.
FLAME HARDENING - A heat treat
method used to harden the surface of some parts where only a small portion
of the surface is hardened and where the part might distort in a regular
carburizing or heat treating operation. The operation consists of heating
the surface to be hardened by an acetylene torch to the proper quenching
temperature followed immediately by a water quench and proper tempering.
Generally wrought or cast steels with carbon contents of .30 to .40%,
low alloy steels, and ductile and malleable cast irons are suitable for
flame hardening.
HARDENABILITY- This relates
to the ability of steel to harden deeply upon quenching, and takes into
consideration the size of the part and the method of quenching. The test
used to determine the hardenability of any grade of steel is the Jominy
Test.
HARDENING - The heating and
quenching of certain iron-base alloys from a temperature above the critical
temperature range for the purpose of producing a hardness superior to
that obtained when the alloy is not quenched. This term is usually restricted
to the formation of martensite.
HARDNESS - The ability of a
metal to resist penetration. The principle methods of determining hardness
of steel are the Rockwell, Brinell and Scleroscope Tests.
HEAT TREATMENT - An operation
or combination of operations involving the heating and cooling of a metal
or an alloy in the solid state for the purpose of obtaining certain desirable
conditions or properties.
MARTEMPERING OR MARQUENCHING
- This is a method of hardening steel by quenching from the austenitizing
temperature into some heat extracting medium, usually salt, which is maintained
at some constant temperature level above the point at which martensite
starts to form (usually about 450” F.), holding the steel in this
medium until the temperature is uniform throughout, cooling in air for
the formation of martensite and tempering by the conventional method.
The advantages of this method of interrupted quenching are a minimum of
distortion and residual strains. The size of the part can be considerably
larger than for austempering. MARTENSITE - A microconstituent or structure
in quenched steel which has the maximum hardness of ally of the other
steel structures resulting from the transformation of austenite.
NITRIDING - See case hardening.
NORMALIZING - Heating steels
to approximately 100 F above the critical temperature range followed by
cooling to below that range in still air at ordinary temperatures. This
heat treat operation is used to erase previous heat treating results in
carbon steels to .40% carbon, low alloy steels, and to produce a uniform
grain structure in forged and cold worked steel parts.
OIL HARDENING - A process of
hardening a ferrous alloy of suitable composition (generally alloys) by
heating within or above the transformation range and quenching in oil.
PEARLITE - Another microscopic
structure of steel which is produced by slow cooling or air cooling low
to medium carbon and low alloy steels from the austenitic state.
QUENCHING AND TEMPERING - In
this operation the procedure consists of heating the material to the proper
austenitizing temperature, holding at that temperature for a sufficient
time to effect the desired change in crystalline structure, and quenching
in a suitable medium - water, oil or air depending on the chemical composition.
After quenching, the material is reheated to a predetermined temperature
below the critical range and then cooled under suitable temperatures (tempering).
SCLEROSCOPE OR SHORE HARDNESS
- A hardness test performed on a Shore Scleroscope Hardness Tester. The
hardness is determined by the rebound of a diamond pointed hammer (or
tip) when it strikes the surface of a specimen. The hammer is enclosed
in a glass tube and the height of the rebound is read either against a
graduated scale inscribed on the tube, or on a dial, depending on the
model used. This type of hardness testing is generally used on large parts
which cannot be tested by either using a Rockwell or Brinell machine.
SUB-CRITICAL ANNEALING - Also
Stress Relief Annealing. A heat treating operation used to relieve or
dissipate stresses in weldments, heavily machined parts, castings and
forgings. The parts are heated to 1150” F., uniformly heated through,
and are either air cooled from temperature or slow cooled from temperature
depending on the type of part and subsequent finishing or heat treating
operations.
TEMPERING - Also termed drawing.
Reheating hardened, usually quenched, steel to some temperature below
the lower critical temperature followed by any desired rate of cooling
after the steel has been thoroughly soaked at temperature. Usual tempering
temperatures are 300” to 1100” F.
WATER HARDENING - High carbon
grades of tool steel, straight carbon steels and low alloy steels that
are hardened by quenching in water during the heat treating operation.
|
Section
7 - Modes of
Failure
There are only 3 ways that steel
parts can break. That is, there are only 3 ways that the atomic bonds of the
steel's crystal lattice structure can be broken. They are: tension, compression,
and shear. Tension is the action of pulling. Steel parts can be
pulled apart - for example, if you grasped 2 ends of a steel bar and pulled
lengthwise until it is pulled apart like taffy - it would have failed in tension.
Compression is the action of being pressed on. We don't generally see steel
ATV parts failing in compression, but it can still affect us. A more obvious
example of compression failure might be a concrete block that is loaded with
weight until it crumbles into dust. Shear is
the action of slicing or cutting through something. Take 2 pieces of steel
plate and bolt them together through a hole drilled in each. Now, slide the
2 pieces away from each other in opposite directions and if the bolt fails by
getting sliced in half, it has failed in shear.
UTS or Ultimate Tensile Strengths
for different materials or components are readily published, as they are comparatively
easy to determine by testing. A sample is placed into a machine and pulled until
it comes apart, the force required is recorded. Compressive strengths
are not commonly published, but they are available. Shear strengths for
steel products are generally regarded to lie in the range of 60-80% of the UTS
of the material.
There may seem to be other modes
by which a part can fail, but on examination these are really just some combination
of the above 3 modes of failure. For example, bending is really just a part
that is experiencing tension on one side and compression on the other. Torsional
loading is really a combination of tension, compression, and shear all at once
(and is therefore fairly complicated to calculate) |